Nereda in Ireland (2017)
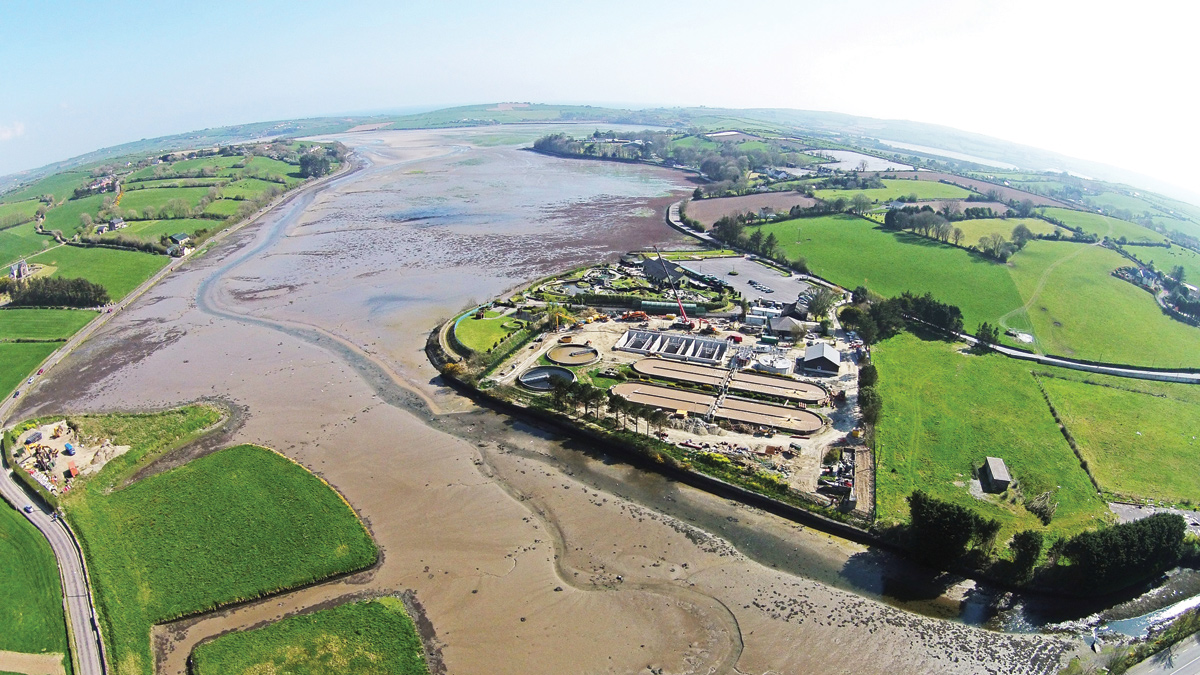
Clonakilty WwTP, the first Nereda® plant in Ireland, under construction in January 2015 Courtesy of EPS Group & Mark Cliffe Aerial Photography
Nereda® is an innovative, sustainable and cost-effective biological wastewater treatment technology that purifies water using the unique features of aerobic granular biomass; purifying bacteria that create compact granules with superb settling properties. The technology was originally discovered by the Delft University of Technology in the Netherlands, and developed in a unique public-private partnership between the University, the Dutch Foundation for Applied Water Research (STOWA), the Dutch Water Boards and Royal HaskoningDHV. After 20 years of research and development this innovative biological solution is now proving itself to be a leap forward in wastewater treatment technology. EPS Water Group was one of the first Nereda® licensees and has been instrumental in the construction and operation of full-scale plants.
About the technology
What makes the Nereda® process so different is the aerobic granular biomass. In a conventional activated sludge treatment process, flocs of sludge are suspended in the water. It takes time for these flocs to settle in the treated wastewater, and a secondary settling tank or clarifier is needed. Nereda® granules settle much faster, and can do so in the same tank in which the treatment process takes place.
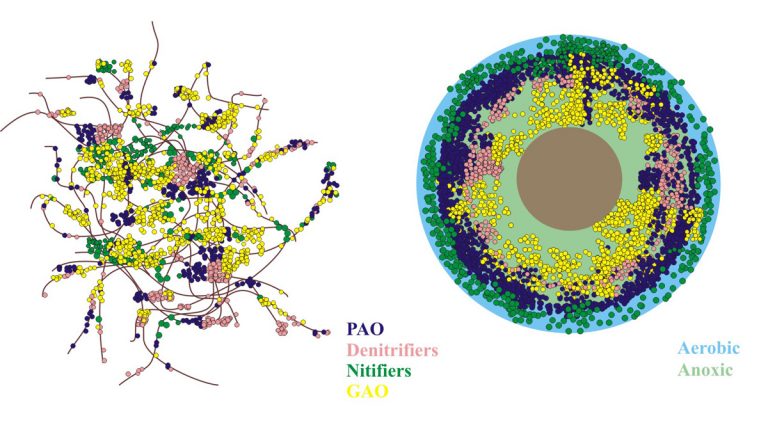
Comparative structural properties of activated sludge (left) and Nereda® granular biomass (right) – Courtesy of Royal HaskoningDHV
Owing to their composition, the granules have an aerobic outer shell which is rich in oxygen and an anoxic/anaerobic core that is low in oxygen. This means that different treatment conditions can be found in a single granule. In a normal treatment plant, the high-oxygen and low-oxygen processes take place in different parts of the overall process.
Nereda® is being used internationally for the sustainable and cost-effective treatment of industrial and domestic wastewater. The technology is proven and suitable for even the largest applications. The performance of Nereda® plants is outstanding and exceeds those of traditional activated sludge plants. The robustness and stability of the treatment process under strongly varying influent load conditions and influent pH fluctuations is remarkable. Furthermore, even in cold conditions, extensive nitrogen removal can be established at high biological sludge loads.
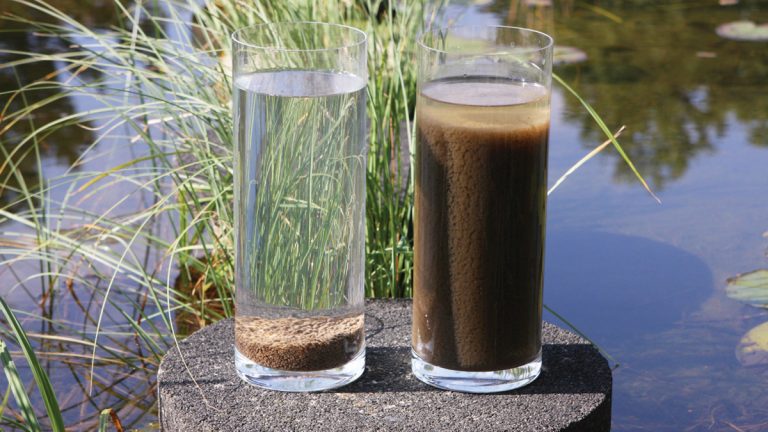
Comparative settling properties of Nereda® granular biomass (left) and activated sludge (right) – Courtesy of Royal HaskoningDHV
Key Success Factors for Nereda® granular activated sludge
- Reduced footprint and land uptake.
- Reduced carbon and whole lifecycle (TOTEX) costs.
- Reduced civil costs.
- Reduced power consumption.
- Reduced requirement for chemical dosing.
- Reduced sludge production.
- Step change technology utilisation to meet demands for reduced space constraints, stricter environmental regulation and discharge limits.
Nereda® in Ireland
The demographic and geographical spread of wastewater treatment facilities, coupled with the very often variable loads and stringent environmental compliance requirements, has made SBR the technology of choice for a majority of small-to-medium sized works in the Irish market. However, in recent years, stricter environmental requirements from Europe coupled with targets for carbon reduction have driven a different approach.
Following a comprehensive review by EPS of new and emerging global technologies, Nereda® was identified as an ideal technology to treat municipal wastewater and meet success criteria in Ireland. In 2013, EPS became the sole Irish license holder to Royal HaskoningDHV for this new Nereda® technology.
Introducing the technology was straightforward as Irish Water quickly became receptive to Nereda® and immediately recognised the benefits that it would bring to their investment programme and associated targets. Three case studies follow detailing EPS’s Nereda® installations at Clonakilty, Carrigtwohill and Cork Lower Harbour.
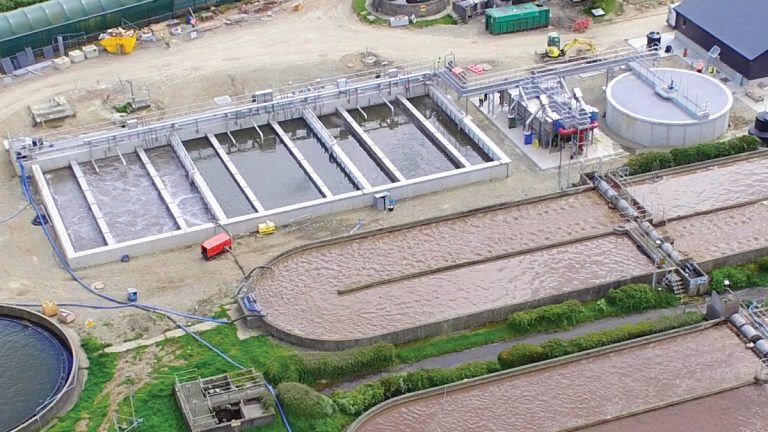
Clonakilty WwTP with 20,500PE Nereda® reactors under testing, alongside oxidation ditches – Courtesy of EPS Group & Mark Cliffe Aerial Photography
Clonakilty WwTP
Clonakilty WwTP was the first full-scale Nereda® plant built in Ireland or the UK. Located on the southern coast, Clonakilty is a bustling seaside town heavily reliant on tourism with a reputation for fine food, festivals, blue flag beaches, and other features of natural and cultural heritage. The 2014 County Development Plan designated Clonakilty as a ‘Strategic Employment Centre’ for West Cork, but the over-loaded capacity of the WwTP serving the town was a large impediment to growth in the region. Clonakilty presented a new and challenging environment for the use of the Nereda® technology.
EPS had already been awarded the contract for the design, build and operate of this plant before Nereda® became an option. EPS chose to present the Nereda® option to the client in the form of a value-engineered proposal and this was accepted as having the best outcome potential after a lengthy due diligence period.
Clonakilty WwTP was originally constructed in 1987 very close to the town centre using an area of reclaimed land on the sea front and immediately adjacent to the Model Railway Village, a popular tourist attraction. Flows from the predominantly combined sewer network were treated through a conventional extended aeration process. The original design population equivalent for the plant was 5,333 person equivalent (PE) but 20 years later was regularly receiving loads of up to 20,000 PE in the summer months.
As well as restricting growth in the town, the overloaded process gave rise to very severe odours which were impacting on local residents, tourism and trade (well known informally as the ‘Clon Pong’). Also, the treated effluent discharges to Clonakilty Bay which is designated as a proposed Natural Heritage Area, a candidate Special Area of Conservation, a Special Protection Area and provides designated bathing waters.
Particular challenges included high industrial loads from local dairy and poultry processing industries, the saline environment, the environmental designations of Clonakilty Bay, the strategic importance of tourism and water quality for the local economy, footprint size limitations, and significant planning restrictions on the site. A design horizon of 2030 was chosen for the required new plant, with design parameters of 20,500 PE, a BOD load of 1,230kg/day and a peak hydraulic load of 14,388m3/day.
EPS began works on site in October 2014 and were set a very challenging 8-month programme to take live flows to the new Nereda® plant by May 2015. The main treatment tanks were 3 (No.) rectangular small-to-medium sized reactors that were required to be mostly buried due to the planning consents in place.
The project also included a new inlet works and new sludge thickening and dewatering systems as well as new MCC and SCADA works. The plant went live on schedule on the 11 May 2015 and coped very well and maintained compliance despite some initial over-loading and pH shock loads.
The real benefits of Nereda® were realised through this project in the form of the excellent effluent quality as well as the volume of remaining future development land now available to the client. The main benefit to the local community however was the nuisance removal with the odour issues so prevalent and problematic before the upgrade disappearing almost completely.
This was recognised by the adjacent tourist attraction who graciously hosted a community day for the neighbouring treatment plant to allow local stakeholders recognise the positive impact of the plant to the town.
Carrigtwohill WwTP: Maximising the benefits of Nereda®
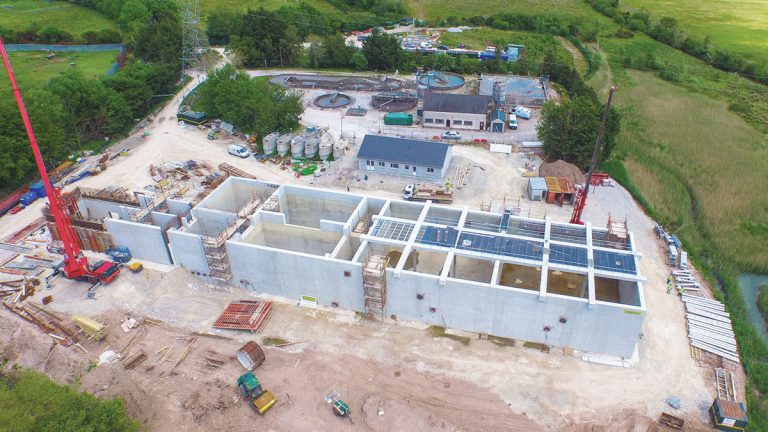
Carrigtwohill WwTP Nereda® reactor block under construction during summer 2015 – Courtesy of EPS-Sorensen JV and Joshua Sorensen Aerial Photography
The Clonakilty plant provided EPS with a higher degree of confidence in the new technology and the roll out continued to Carrigtwohill WwTP where Nereda® was offered as the basis of the successful EPS tender proposal.
The Nereda®-based tender was evaluated by the client on a whole life cost basis against other competitive bids using conventional process solutions. The Nereda® process emerged as the most economically viable solution for Irish Water.
Carrigtwohill is a fast-growing commuter town located east of Cork City with a high degree of bio-medical and other industrial activity. The over-loaded capacity of the WwTP serving the town was a large impediment to expansion for industry and was contributing to the pollution of Cork Harbour Area.
Carrigtwohill WwTP was originally constructed to cater for 5,000 PE and was expanded in 1990 to increase the treatment capacity to 7,500 PE. The plant receives imported sludges from several smaller wastewater treatment plants in East Cork as well as local landfill leachate. The volume of industrial expansion in the Carrigtwohill area is reflected in the fact that despite the high degree of importation, approximately 50% of the influent to this wastewater treatment plant is from an industrial source.
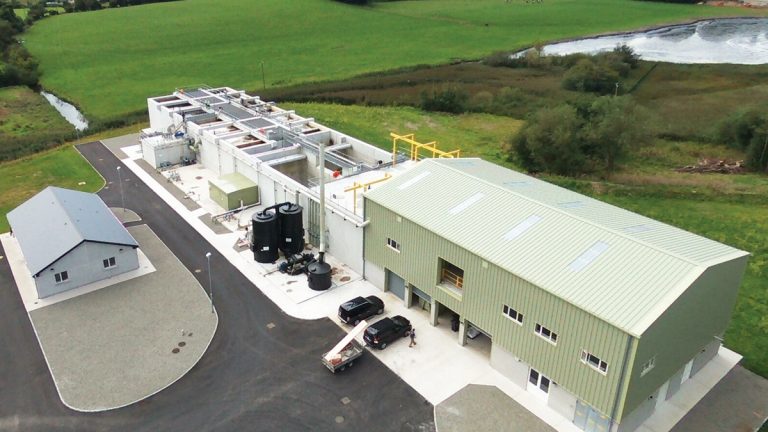
Carrigtwohill WwTP: Combined inlet works and sludge handling building in the foreground, and storm tanks and Nereda® reactors beyond – Courtesy EPS-Sorensen JV and Joshua Sorensen Aerial Photography
The contract provided for design, build and (20-year) operate under Phase 1 for a PE of 30,000 with provision for the future expansion under Phase 2 & 3 to an ultimate PE of 60,000. The modular layout chosen for the Nereda® plant design future-proofs the site as it offers a ready-made, cost-effective solution for future expansion.
The minimal footprint of the Nereda® solution was also very important to this project due to the site location within a flood zone. To maximise this benefit, a common wall construction method was selected for the entire plant. This has optimised civil costs, particularly in terms of earthworks and pre-construction ground improvement works.
The new plant consisted of a new inlet works sized for future flows with screenings removal to 2mm as well as extensive grit and FOG removal. The biological process consisted of an importation reception tanks, an Influent buffer tank and 2 (No.) medium-sized Nereda® reactors. Also included were new sludge thickening and dewatering systems as well as new MCC and SCADA works and a new administration building including laboratory facilities.
Ground improvement commenced in September 2014 with the first base pour in December 2014 and the first Nereda® cell fit out beginning in late May 2015. The plant received live flows in January 2016. Carrigtwohill WWTP successfully completed process proof testing on the 1st May 2016 and is giving excellent results on all KPIs at present. EPS also continues to operate this plant on behalf of the client for the foreseeable future.
Cork Lower Harbour WwTP
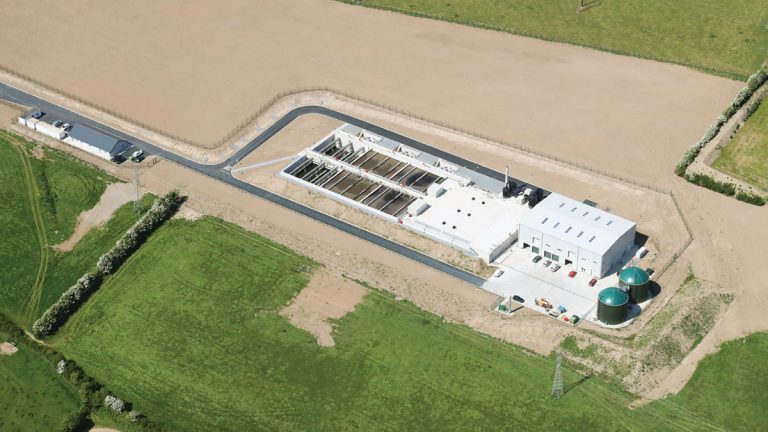
Completed in December 2016, Cork Lower Harbour WwTP is currently the largest operational Nereda® plant in the UK or Ireland – Courtesy of EPS-Sisk JV and Barrow Coakley Photography
The Clonakilty and Carrigtwohill schemes were able to provide assurance that the Nereda® technology was an effective process option and could realise the promised benefits. With this comfort, EPS began to utilise in house DfMA techniques being simultaneously developed within the organisation using BIM design software and a new emphasis on off-site construction. These systems had been previously successfully used by EPS in industrial applications such as the new Guinness brewhouse development, a new dairy wastewater plant in Ireland, and on some particularly challenging municipal projects such as Frankley Water Treatment Works in Birmingham; delivered via the MEPS joint venture in collaboration with MWH Treatment.
Cork Lower Harbour WwTP was part of the €105m Cork Lower Harbour Main Drainage Project. EPS set out on this project to use these DfMA techniques to minimise programme durations on site, to improve site safety and to guarantee build quality for the final product. Cork’s Lower Harbour is the second-largest natural harbour in the world. It has a rich maritime history and a proud industrial tradition. It supports employment, fosters tourism and provides many opportunities for water-based activities, as well as supporting a diverse range of coastal ecological habitats.
The Cork Lower Harbour Main Drainage Project was required to significantly enhance the water quality in Cork Harbour, which had fallen below minimum requirements under the Water Framework Directive. The Phase 1 contract provided a PE of 65,000 with provision for the future expansion under Phase 2 to a Population Equivalent of 80,000. The contract for the design, build and operation was awarded to an EPS/Sisk JV in July 2015. The JV relied heavily on off-site BIM manufacturing techniques to achieve the challenging targets.
The plant consists of preliminary treatment facilities similar to Carrigtwohill, sized for an incoming flow of 988 l/s. Flows to treatment of 508 l/s are treated in 3 (No.) Nereda® reactors using a similar common wall construction method as used previously. The sludge thickening and dewatering systems were supplemented by 2 (No.) 600m3 anaerobic digesters to allow for waste to energy recovery on site and minimise sludge disposal volumes from the plant.
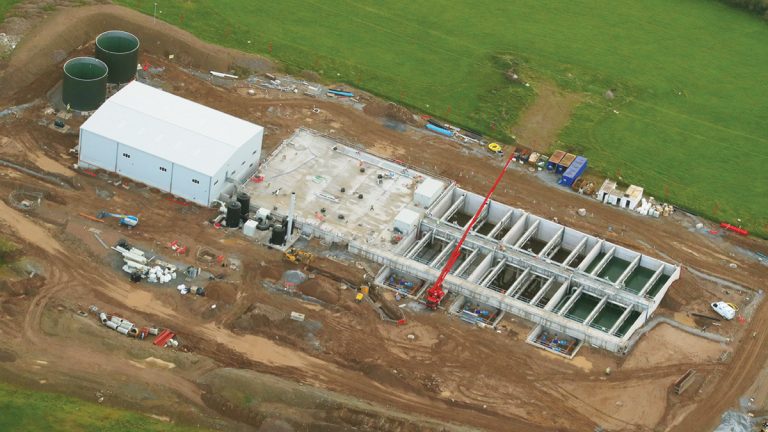
Cork Lower Harbour WwTP under construction during summer 2016 – Courtesy of EPS-Sisk JV and Barrow Coakley Photography
Following an intensive 15-month construction period, live flows were received to the new treatment plant on 16 December 2016. The process proving test period was completed in late March 2017, ahead of schedule, and to the satisfaction of the client and all other stakeholders involved. The quality of the treated effluent from this plant has been consistently excellent to date.
The utilisation of off-site manufacturing techniques on this project enabled EPS to accelerate the reactor fit-out time by an impressive factor of 4 (versus the previous two plants) while ensuring best possible quality. In the last reactor, substantial completion of the fit-out was achieved in just 4 weeks. The 215,000 man hours on site were completed without a single accident largely due to the reduction of required site works, and the almost complete elimination of working at height and hot works. The ability to deliver pre-assembled modules, with safety features already in place, and the use of full synchronisation videos of the assembly prior to commencement, were key factors in achieving this statistic.
DfMA and Nereda®: Where next?
The Cork Lower Harbour plant illustrates EPS’s conviction that off-site manufacturing is the future of all sectors of the construction industry, including the delivery of water projects.
The EPS commitment to off-site is reflected in the organisation’s new 4,000m2 DfMA Centre of Excellence recently constructed within its head office complex, and its MEPS joint venture with MWH Treatment for delivering DfMA solutions. The new workshop, incorporating new BIM technologies and collaboration centres, has been active from May 2017 to complement existing facilities and capabilities across Ireland and the United Kingdom.
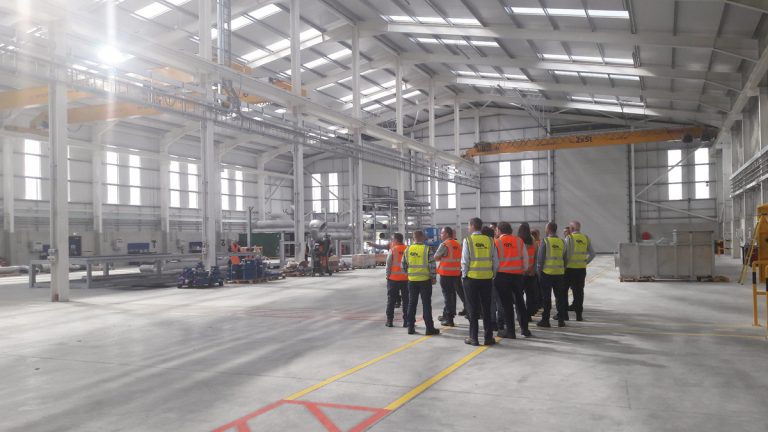
UK water company delegation visiting the new EPS DfMA Centre of Excellence – Courtesy of EPS Group
Nereda® has become an important part of the global water industry toolkit for biological wastewater treatment, with its treatment performance fully proven and its economic viability established and improving all the time. By sharing its unique learning from the Irish projects and collaborating closely with RHDHV, EPS are de-risking Nereda® delivery and accelerating uptake of the technology in the UK market. EPS have recently undertaken successful pilot trials for Scottish Water and Anglian Water, and have provided Nereda® pilot plants for trials in Ireland and the USA. New full-scale projects are underway for Scottish Water and Anglian Water, and further schemes are in development with many other water companies including United Utilities and Severn Trent Water.