Newthorpe STW (2024)
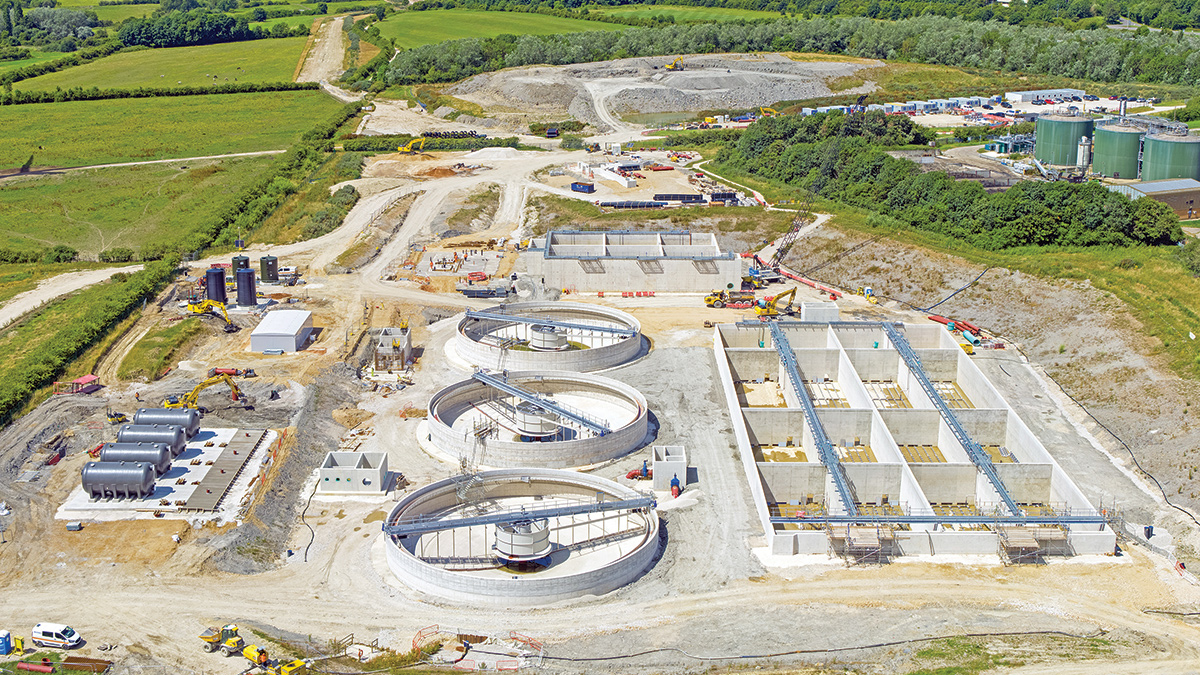
Newthorpe site overview (June 2024) - Courtesy of Mott MacDonald Bentley
Newthorpe Sewage Treatment Works, in the Erewash Valley in Nottinghamshire, is undergoing a major expansion. The new works will duplicate its current capacity, from 324 l/s and 41,000 population equivalent (PE) to 649 l/s and 100,000 PE, to receive the flows of the Heanor Milnhay STW catchment area. A 2.5 km dual-rising main will connect both sites. Heanor Milnhay STW, a dual-stream site in Derbyshire currently treating 258 l/s (41,000 PE), has reached its maximum capacity and its geographical location makes it impossible to cope with the projected population growth. The process will be decommissioned, and the site will be re-purposed to hold a storm storage capacity that exceeds the current storm storage capacity by more than three times. The client, Severn Trent, and Mott MacDonald Bentley, principal designer and contractor, are the main stakeholders of this project.
Project objectives
The main project objectives align with the current social and economic environment. With the expansion of the works, Severn Trent is aiming to:
- Improve the effluent quality, especially phosphorus content. The new site will reduce the phosphorus concentration in the effluent from 2 mg/l to less than 0.2 mg/l.
- Reduce the running costs and maintenance costs of the plant by merging two sewage treatment works and using a less-intensive chemical usage treatment process.
- Reduce the non-treated sewage spillage by increasing the stormwater storage capacity at Heanor from 2,200m3 to 7,000m3. Additionally, all the storm flows will be preliminary treated by physical screening and settlement.

Newthorpe STW: (left) site compound and storage, (top) existing site, and (bottom) the new expansion (August 2024) – Courtesy of MMB
Process description: Preliminary & primary treatment
Once the expansion is completed, Newthorpe flows and Heanor flows will have separate preliminary and primary treatment streams, before combining in the secondary treatment stage.
Flows from the Newthorpe catchment will arrive at the existing inlet works. This area will stay as per the current arrangement and only the mechanical equipment will be upgraded. The flows are lifted using Archimedes screw pumps to a raised inlet works structure.
This structure holds the fine screens, which are designed to capture at least 80% of all the solids above 6mm. After the screens, a detritor will settle all grit and inorganics such as sand; removing them from the process stream to avoid damage to the mechanical equipment.
The wastewater from the catchment then flows to the primary treatment area, where the first physical separation of particles using gravity to settle the fines at the bottom of the two existing primary settlement tanks is carried out.
The effluent from the primary settlement tanks, that is currently connected to a secondary treatment consisting of trickling filters and hummus tanks, will now be diverted to the new works’ expansion.
Flows from the Heanor catchment area that arrive at Heanor will be pumped 2.5km to a newly build inlet works at Newthorpe. Similar to the existing inlet works, the new inlet works will feature 2D 6mm screens provided by Longwood Engineering Company Ltd and a 4.5m detritor provided by Tuke & Bell Ltd.

Heanor flows inlet works (August 2024) – Courtesy of MMB
After the detritor, the flows merge, without having been settled, with the Newthorpe flows. Keeping the Heanor flows unsettled is key to provide the right load for the process to work.
Process description: Secondary treatment
The main biological treatment happens in this secondary stage, where the aim is to reduce to the consented levels certain parameters such as Phosphorus, ammonia, iron and suspended solids. The process selected for Newthorpe is an enhanced bio phosphorus removal process in a modified University of Cape Town (UCT) configuration.
The first stage in the process is the anaerobic zone, where the polyphosphate-accumulating organisms (PAOs) thrive in an environment with no oxygen nor nitrogen introduced. In this stage, the PAOs accumulate volatile fat acids which will help them being biologically competitive in the aerobic phase of the treatment.
The next stage is the anoxic zone, where recirculated active sludge (RAS) from the secondary settlement process is introduced.

Enhanced Bio Phosphorus Removal UCT configuration – Courtesy of MMB
This RAS recirculates the bacteria through the system as well as introduces nitrogen oxides which have been created in the aerobic section by the oxidation of ammonia (NH4). In this anoxic zone, the nitrogen oxides are transformed into nitrogen gas which escapes to the atmosphere.
The third stage of the process is the aerobic zone in which air is introduced. Under these conditions, three main processes concur:
- The nitrification process, where ammonia is transformed into nitrogen oxides which then are degraded to N2 in the anoxic zone as previously mentioned.
- To carry out this process, the bacteria need energy which they obtain from the organics load in the sewage.
- The PAOs previously mentioned consume the VFAs accumulated in the anaerobic zone to accumulate phosphorus. The phosphorus accumulated at this stage is larger than the phosphorus released in the anaerobic stage, hence producing enhanced bio-phosphorus removal.
The final stage of the secondary treatment is the secondary sedimentation on the final settlement tanks, where the rich-P sludge is removed from the system and either recirculated to the anoxic zone; or thickened and wasted to produce other products such as gas and cake on sludge digestion processes.
Process description: Tertiary treatment
The final stage of the process aims to further reduce the P levels in the effluent by capturing non-organic phosphorus.
Ferric sulphate is dosed upstream of the tertiary solids removal unit to cluster the particles into larger floccules that are then removed by a physical filtration system. The system selected in Newthorpe is FilterClear (mixed media filtration), designed and manufactured by Bluewater Bio Ltd. Once commissioned it will be the largest FilterClear system in wastewater treatment.

Installation of the tertiary solids removal units (August 2024) – Courtesy of Mott MacDonald Bentley
Delivering innovation
MMB and Severn Trent will be working together during the commissioning of the plant to understand the emissions of greenhouse gases in sewage treatment works and how to optimise the plan to reduce them. Instrumentation to measure NO and N2O will be installed on the ASP.
Nitrous oxide is produced during the biological removal of ammonia in nitrifying ASPs. Monitoring nitrous oxide emissions (along with nitrite) during commissioning at Newthorpe will not only provide STW with a baseline process emissions factor (EF) for the site but also with valuable insights into the mechanisms resulting in nitrous oxide production.
Newthorpe STW: Supply chain – key participants
- Client: Severn Trent
- Principal designer & contractor: Mott MacDonald Bentley
- CFD analysis, planning, mining studies: Mott MacDonald
- CFA piling: Van Elle
- ASP FRC: Bell Formwork Services Ltd
- Inlet works FRC: TCL Structures UK Ltd
- Design/build of FRC final settlement tanks: Tank Consult Ltd
- Rising main HDD: Johnston Trenchless Solutions (JTS)
- Mechanical installation: Alpha Plus Ltd
- Electrical installation: Main Electrical
- Inlet screens: Longwood Engineering Company Ltd
- Grit removal plant: Tuke & Bell Ltd
- Scraper bridges: EPS Water
- Glass-coated steel tanks: Goodwin Tanks
- MCCs: CEMA Ltd
- Aeration diffusers for ASP: Xylem Water Solutions
- Polymer dosing: Richard Alan Engineering
- Alkalinity dosing: Lintott Control Systems
- Ferric dosing: Colloide
- Mixers, blowers & submersible pumps: Sulzer Pumps Wastewater Ltd
- Progressive cavity pumps: NOV
- Booster pumps: Grundfos
- Tertiary solids removal: Bluewater Bio Ltd
- Gravity belt thickeners: Alfa Laval
- Kiosks: Morgan Marine
- Steel buildings: LGSF
- Valves: AVK UK Ltd
- Penstocks: Waterfront Fluid Controls Ltd
- Lifting equipment: T Allen Engineering Services Ltd
- Steelwork & storm distribution chamber: GT Fabrications
- Steelwork: GWH Fabrications Ltd
- Steelwork & GRP platforms: APT Marine Engineering Ltd
- FE monitoring: Servitech International
- Fencing: Town & Country Fencing (Midlands) Ltd

Heanor site overview (September 2024) – Courtesy of MMB
Progress: Heanor STW
At Heanor, the main structure, which is the new transfer and storm pumping station structure, is currently in its final stages.
- The design of the structure was a challenging process where the proximity of nearby structures and the groundwater were the main constraints. The final structure consists of a wall of secant piles by Van Elle, which has been incorporated into the permanent structure. This secant pile provided a cut-off for groundwater that was key to delivering the pumping station installation safely.
- The blind tank, which is a 1,700m3 glass-coated steel tank provided by Goodwin Tanks Ltd, has been completed in September 2024. The slab and all drainage pipework are now completed.
- A steel storm distribution chamber fabricated by GT Fabrications is being manufactured and will be installed in October 2024.
- Finally, the MCC has been installed and powered in September 2024.
The site will be operational in its final configuration by December 2024 to meet the regulatory requirements.
Progress: Rising main
The 2.5km 450mm dual rising main connecting Heanor STW to Newthorpe STW is now completed by with only the pressure testing and its final connection to Newthorpe STW pending. The rising main will be ready to transfer flows in October 2024, to aid with the EBPR maturation process ahead of the regulatory commitment.
The route of the rising main crossed several historical mine sites. MMB’s geotechnical team conducted an investigation to understand the status and position of the mine entries and any other mine-related features along the route. Additionally, a watching brief was in place to quickly identify any non-natural ground features.
Thanks to this effort all the risks were mitigated, and the rising main was safely constructed by Johnston Trenchless Solutions.

Rising main site just outside Newthorpe (August 2024) – Courtesy of MMB
Progress: Newthorpe STW
At Newthorpe, all major civil structures are completed, and on the site, a major operation of backfilling, electrical and mechanical installation is currently ongoing.
- Inlet works: The new Heanor flows inlet works structure was built by TCL Structures UK Ltd, with the new 2D 6mm screens being provided by Longwood Engineering Company Ltd and a 4.5m detritor being supplied by Tuke & Bell Ltd.
- Final settlement tanks: The three 33m FSTs built by Tank Consult Ltd with full scraper bridges provided by EPS Water are now complete.
- Activated sludge plant: The four-lane ASP built by Bell Formwork & Civil Engineering Services Ltd is also complete. The aeration grid and pipework supplied by Xylem Water Solutions, the blowers and the mixers from Sulzer Pumps Wastewater Ltd, and the tank steelwork from GT Fabrications has all been installed.
- Chemical dosing: The four tanks of the chemical dosing area are now installed. The ferric dosing system was provided by Colloide while the alkalinity dosing system is provided by Lintott Control Systems Ltd.
- Site buildings: The Newthorpe site is changing rapidly and at the end of September 2024, the building that will house the Alfa Laval gravity belt thickeners and the Richard Alan Engineering polymer dosing plant, has been erected by LGSF.
- Tertiary treatment plant: The four Bluewater Bio Ltd FilterClear tertiary solid removal vessels are now installed on site. All ancillaries such as pipework and service tanks are currently being installed and the TSR plant will be ready to start commissioning in November 2024.
- Motor control centre: The MCC that will be controlling the expanded works was provided by CEMA Group and is housed in a kiosk manufactured and installed by Morgan Marine. All the electrical installation on site is being carried out by Main Electrical.

Sodium hydroxide (left) and ferric sulphate (right) dosing systems
(August 2024) – Courtesy of MMB
An award-winning project
In 2024, the Newthorpe STW expansion project has been awarded two Green Apple Awards in the categories of Building & Construction and Sustainable Water Management. The project also won the first Ground Engineering Awards for MMB for the UK Project with a Geotechnical Value of between £500k and £1m.
Conclusion
Newthorpe STW and Heanor Milnhay STW have been merged in one of the major AMP7 Severn Trent projects, with Mott MacDonald Bentley as principal designer and contractor. The expansion to Newthorpe STW will be one of the largest enhanced bio-phosphorus treatment sites in the region covering a population equivalent of 100,000 and will achieve a tightened permit of 0.2 mg/l, whilst minimising the use of chemicals to remove phosphorus.
The project is currently on track to achieve the biological maturation of the EBPR by its regulatory date in December 2024.

The project has won the first Ground Engineering Awards for MMB for the UK Project with a Geotechnical Value of between £500k and £1m