Lower Gornal STW (2024)

Completed construction (June 2024) - Courtesy of Mott MacDonald Bentley
As part of the AMP7 programme of work, Severn Trent raised schemes at both Lower Gornal and Roundhill STWs, with the aim of meeting reduced phosphorus and ammonia permits. Roundhill STW had tightening consents of 0.25 mg/l (down from 1 mg/l) for phosphorus and 4 mg/l (down from 5 mg/l) for ammonia, whilst Lower Gornal STW’s consents were tightening to 0.3 mg/l phosphorus (from 2 mg/l) and 1.5 mg/l ammonia (from 10 mg/l). The proposed solution from Severn Trent’s outline design was to close the site at Lower Gornal and replace it with a terminal pumping station which would transfer all non-storm flows to Roundhill STW; the full flow to treatment at Lower Gornal is 253 l/s.
Early contractor involvement
Mott MacDonald Bentley (MMB), had previously been asked to price the scheme, but an agreement on target cost was not met. Challenges with the variance to the original affordability targets set by Severn Trent were the principal issue, and led to Severn Trent wishing to take a different approach to reduce costs associated with the works.
Severn Trent invited a team of operational, design and commercial staff from MMB to complete an early contractor involvement (ECI) for the scheme with a view to improving on the unfavourable cost position.
After a collaborative challenge between MMB and Severn Trent, MMB was able to review scheme drivers with a view to what could be done to keep Lower Gornal open and avoid a costly and disruptive pipeline installation to Roundhill.
MMB had completed similar schemes to Lower Gornal in the past at Trescott STW and Little Aston STW, so was able to quickly produce a proposal incorporating a new moving bed biofilm reactor (MBBR) and tertiary solids removal (TSR) plant to meet the tightened consents.
Retaining the works at Lower Gornal also mitigated the significant operational expenditure of running a new transfer pipeline and associated pumping equipment, maximising output from the existing assets.
The ECI has been considered very successful by all parties involved. With the removal of the requirement to transfer flows from Lower Gornal to Roundhill and the subsequent reduction in scope requirements for the scheme at Roundhill itself, Severn Trent saved more than £20m from the original cost build-up, bringing the delivery of the two schemes as close as possible to the original affordability target.

Demolition of biofilter bank – Courtesy of MMB
Demolition
The new scheme at Lower Gornal required the demolition of an existing bank of four biofilters to allow space for the construction of the new assets. This was the only solution for the new plant due to historic mining activity surrounding the site making any other locations unfeasible. The existing biofilters where demolished by specialist sub-contractor Bagnall Construction Ltd to base slab level. Building the new plant on top of the old bases reduced the risk of differential settlement in a historic mining area.
Lower Gornal STW: Supply chain – key participants
- Main designer & contractor: Mott MacDonald Bentley
- Topographical survey: 40Seven
- Ground investigation: Dunelm Geotechnical & Environmental Ltd
- Demolition of biofilters: Bagnall Construction Ltd
- Demolition of PAC dosing: Ron Hull Group
- Formwork reinforced concrete works: TCL Structures UK
- Recirculation shaft & augerbore: Active Tunnelling Ltd
- Mechanical installation & fabrication: Franklyn Yates Engineering Ltd
- Electrical installation: Installation Maintenance & Controls Ltd (IMAC)
- Tertiary ammonia removal plant: FLI Water
- Blowers: Aerzen Machines
- Tertiary solids removal plant: Eliquo Hydrok Ltd
- Ferric & alkalinty dosing: Colloide Engineering Systems
- Motor control center: BGEN Ltd
- Biofilter drives: Drive Systems Ltd
- TSR backwash & washwater tanks: Balmoral Tanks Ltd
- MCC kiosk: Morgan Marine
- Lifting equipment: T Allen Engineering Services Ltd
- Access metalwork: Ant Access International
- Trace heating & lagging: Waste Water Manufacturing
- Landscaping: Holt’s Tree Care Ltd
- Surfacing: Tarmac
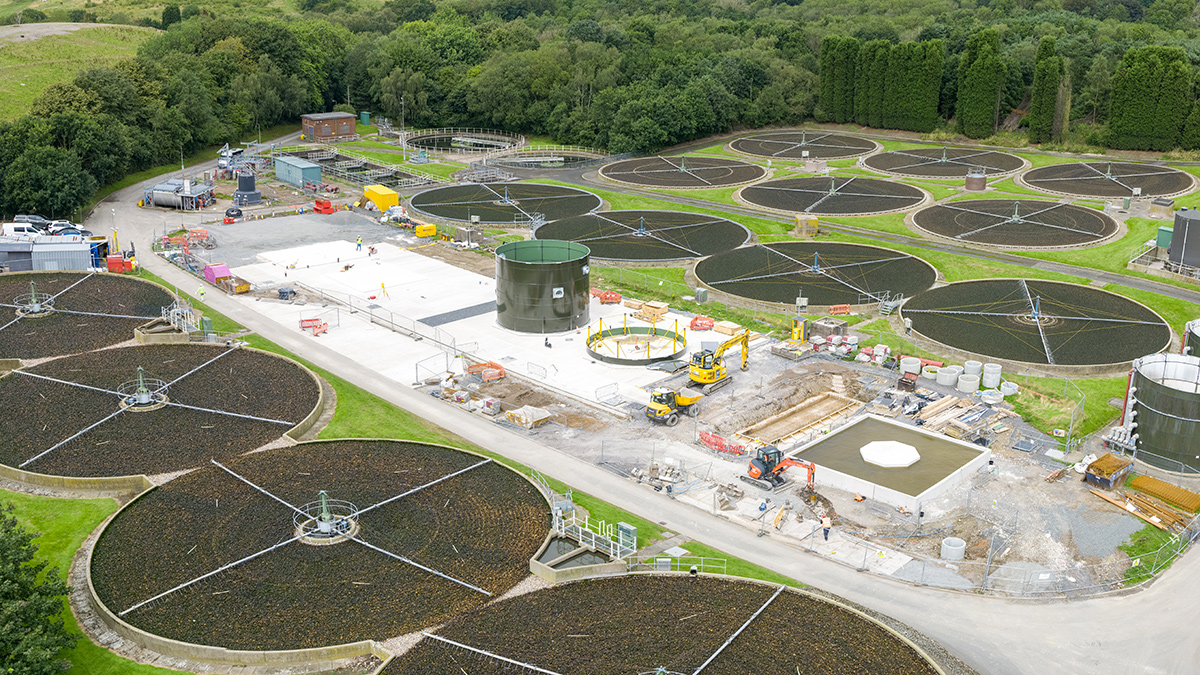
Construction progress (August 2023) – Courtesy of MMB
Chemical dosing
The process design incorporated ferric dosing into the primary settlement tanks’ (PST) inlet channel followed by an alkalinity dose. Both the 60m3 alkalinity and ferric rigs were provided by Colloide Engineering Systems. A crude dose is applied prior to entering the PSTs and is mixed by the turbulence of the main channel flow. The ferric sulphate reacts with the phosphate in the effluent to create an iron-phosphate sludge, which is settled out in the PSTs.
A tertiary dose is applied upstream of the TSR plant for the purposes of removing any residual phosphate in the effluent. The iron phosphate sludge from this plant is returned upstream of the PSTs and is co-settled with the crude-dosed flow.
A sodium hydroxide dosing plant has been provided in place of a decommissioned PAC dosing plant. Sodium hydroxide is dosed upstream of the PST distribution chamber (but downstream of the crude ferric dose) to correct the pH of the effluent entering the main treatment works.
By correcting the pH of the effluent through the main treatment works, the nitrification of the biofilters, and the MBBR plant is maintained at an optimal level, as well as ensuring that the tertiary ferric sulphate dose is effective.
Moving bed biofilm reactor (MBBR)
The flow is initially distributed equally over four existing primary settlement tanks before dosing, then travelling through the existing biofilters, onto six existing humus tanks, then through the MBBR and TSR.

MBBR tanks completed (June 2024) – Courtesy of MMB
The MBBR plant was provided by FLI Water comprises two MBBR tanks, which operate in a lead/lag configuration. Flow is pumped to the MBBR plant from the tertiary feed pumping station, and passes into either MBBR Tank 1, or MBBR Tank 2; dependant on which tank is selected as the lead. Every day the tanks rotate the lead. This will be inhibited if the flow to the plant is too high (hydraulic safety), or if the ammonia monitored in between the MBBR tanks is too high (to protect the permit, if there is too much ammonia contained within the tank that would become the lag tank).
Each tank is filled with a plastic media which provides a surface for ammonia-reducing bacteria to grow upon. Flow is aerated by duty/standby blowers; which provides mixing for the media and aeration to each tank, thereby removing ammonia from the effluent.
Flow passes through the lead MBBR tank into the lag MBBR tank, before entering the TSR plant provided by Eliquo Hydrok Ltd. The flowrate and the orthophosphate concentration are measured at the inlet.
Tertiary solids removal (TSR)
Ferric sulphate is dosed in a static mixer at the inlet of the TSR plant and dosed flow enters the two flocculation tanks where it is mixed by four mixers. When mixed, the ferric sulphate binds with the phosphate in the flow forming an iron-phosphate sludge suspended in the flow.
This flocculated flow passes to three Mecana cloth filters, which operate in parallel. Flow must pass through the cloths in order to continue forward. The cloths block the passage of the iron phosphate sludge, retaining it within the Mecana tanks. As the cloths become blinded with sludge, the level within the respective tank will rise, and when the level is high, a backwash sequence will be initiated. Sludge retained within the TSR Sludge backwash buffer tank is returned to upstream of the PST’s at a constant rate.
Flow existing the TSR plant flows through a buffer tank, which retains a volume of water to be used as washwater. Excess flow will overflow this tank, and flow to the normal final effluent (FE) route, and then to the watercourse.
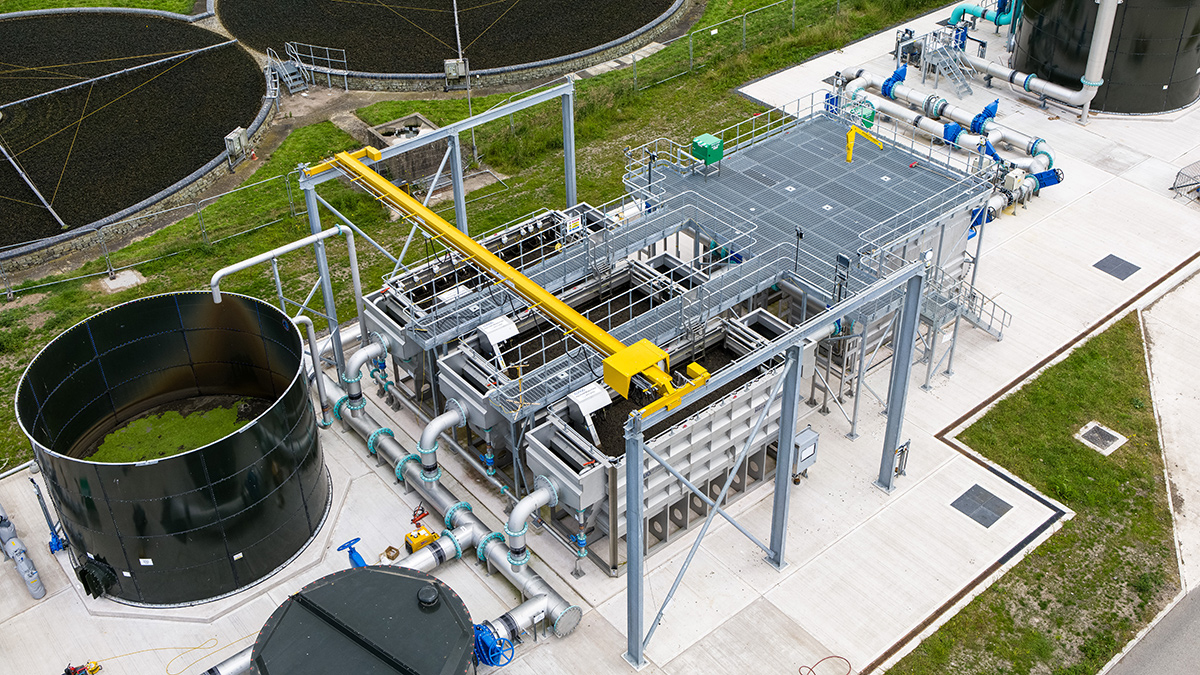
TSR plant (June 2024) – Courtesy of MMB
Pumping stations
A new enhanced recirculation pumping station has been provided, which replaces the existing recirculation system. The TSR feed pumping station is hydraulically linked to the new enhanced recirculation pumping station, which is hydraulically prioritised.
This was installed using a top-down construction method by Active Tunnelling to a depth of 6.5m below ground level and a 28m augerbore was completed from the new shaft to make the connection into the existing TSR pumping station inlet pipework.
The augerbore method of construction allowed the new pipe to pass under existing live services, this prevented having to excavate around existing services and avoid any works shutdowns.
Site network
Recirculation flow is returned to a point upstream of the PST distribution chamber as the flow is circulated through the PSTs, as well as the biofilters, this dilutes the strength of the ammonia concentration in the PSTs. This more constant flow allows for a more consistent load of ammonia to the MBBR, making the MBBR more resilient to variations in ammonia load, and reducing the magnitude of load spikes to the MBBR Plant.
The site washwater network has been re-fed from a new washwater pumping station and new hosereel points have been provided to the new tertiary treatment plant. This effluent is taken from the outlet of the TSR Plant, entering a buffer tank which provides washwater at all times, allowing for a cleaner, and more reliable washwater network on the site.

Recirculation pumping station (June 2024) – Courtesy of MMB
Collaborative working
Weekly on-site collaborative planning sessions with the design and site team, including subcontractors and the client has driven pace in the design and construction programme. This has ensured client buy in throughout the programme eliminating any blockers to progress. All works have been completed without any interruption to the day-to-day running of the plant and the existing permit has never been put at risk. The pace of delivery has meant the scheme has been completed early.
A procurement-led programme and effective liaison with the supply chain meant that all long-lead items for the scheme were delivered ahead of schedule. MMB took a novel approach to the procurement of control panels, working closely with BGEN Ltd to negotiate information provision cut off points in the contract. This alleviated all the issues that COVID caused with the procurement of control panel chips and ensured timely delivery.
MMB employed the carbon hierarchy approach throughout the scheme. This culminated in the reuse of an existing civil bund for the new alkalinity rig. The most noteworthy carbon saving was delivered by reusing 2000m3 of biofilter media, as engineered fill during the demolition works. This was graded and reused to provide the foundations for the new structures using the CLAIR:E process for sustainable land reuse.
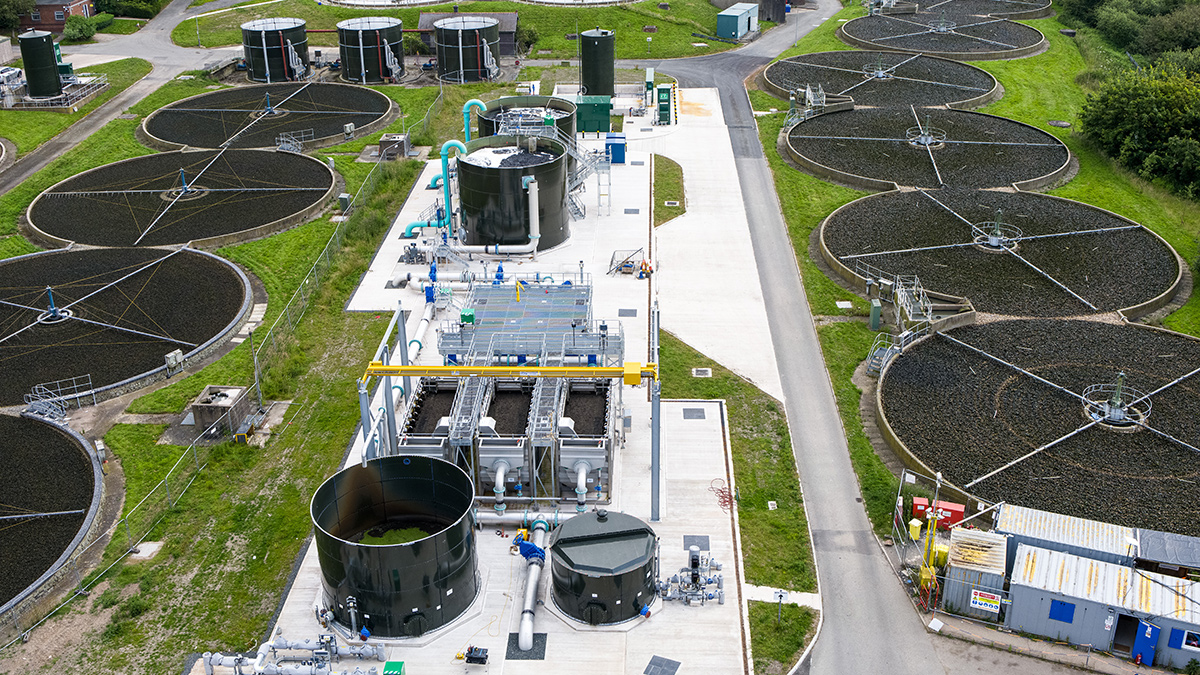
Completed plant (June 2024) – Courtesy of MMB
Project status
At the time of writing, September 2024, Lower Gornal is undergoing 28-day process performance testing and is currently comfortably meeting the contractual permit. The scheme is due for completion three months ahead of schedule and below the agreed target price. It has demonstrated what can be achieved with true collaboration between client and contractor. The scheme demonstrates MMB’s expertise in design and construction of MBBR and TSR plants.