Nine Elms, Battersea Growth & SuDS (2018)
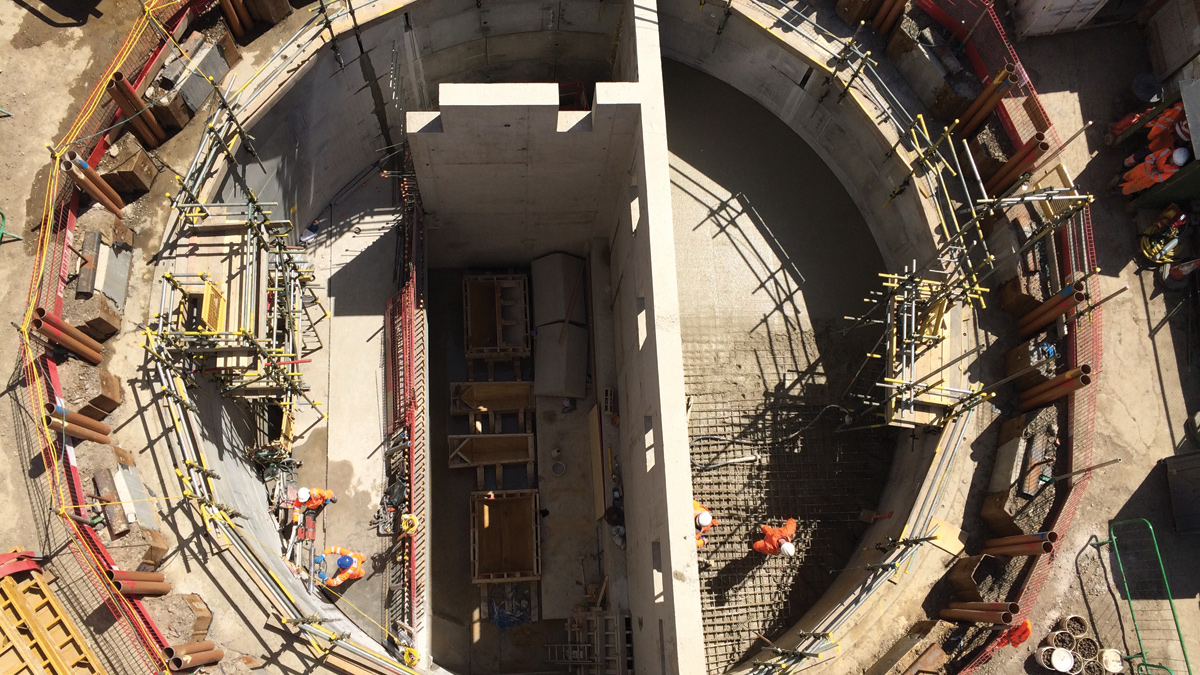
Main pumping station shaft including inlet chamber, wet well, junction box and valve chambers - Courtesy of eight2O
The Nine Elms redevelopment area within Battersea includes 21,000 new dwellings, office, leisure and retail space creating 8000 new jobs including the new US Embassy, a relocated New Covent Garden Market site and the Northern Line extension. An integrated water management study completed by Thames Water (TW) in partnership with the Greater London Authority, ARUP and the Nine Elms Partnership (Lambeth and Wandsworth councils) considered the existing and future situation here. Hence further to a detailed hydraulic modelling exercise of the existing sewer system for TW the choice was clear; either build new sewers to cope with the additional demand or pursue surface water run-off removal from the combined sewer network incorporating a SuDS (sustainable urban drainage system) solution to create foul sewer capacity too.
Project background
As part of the redevelopment, a new public open space was planned creating the Linear Park, a 20m wide paved boulevard and landscaped recreation area stretching through the entire development. All utilities were to be located beneath this area, with a further constraint being the designated 4.5m wide service corridor coordinated by AECOM.
TW decided to deliver an innovative £16.5m surface water removal and SuDS project which would become the UK’s largest sustainable urban drainage system including over 13 hectares of surface water run-off area removed. This would be achieved by extending out the existing surface water network to serve the development and allowing for future growth, relocating/upsizing an existing surface water pumping station and the reuse of an existing rising main including an outfall to River Thames. The surface water removal would create the capacity to connect in all new foul sewers from the new development; a successful outcome for both TW and the developers.
The types of SuDS facilities provided would include roof gardens, open ditches with filtering vegetation, swales, streams, ponds, open water features, underground attenuation crates, soft and hard landscaping including hidden ACO-type drains, rainwater gardens.
Thames Water’s eight2O Alliance team was responsible for the design and construction of the project with Stantec UK as the designer and Costain as the main contractor.
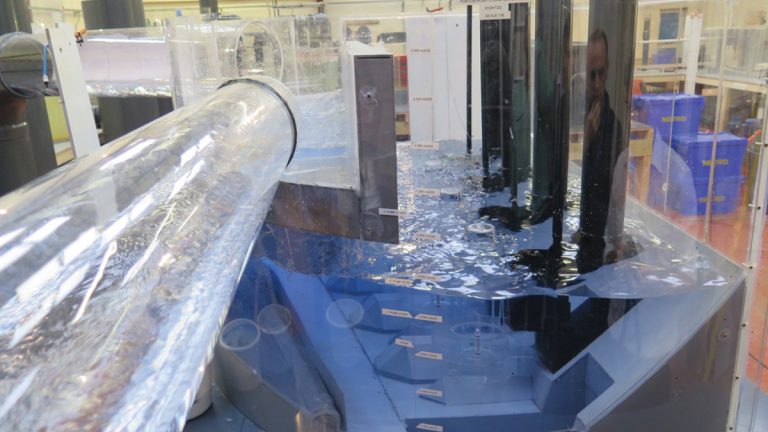
Scale model of main PS at Hydrotec – Courtesy of eight2O
Catchment background
The development site was previously an industrial estate including depots for Royal Mail, DHL and Yodel and prior to this, part of the site was an old gasworks and railway sidings bringing with it land contamination issues. Online records indicate that the gasworks was operational between 1853 and 1970, and some of the gas holders were only demolished in 2015 for the new development.
Hydraulic modelling of existing network and solution
To understand the existing catchment Stantec verified the existing hydraulic model of the catchment including flow and manhole surveys.
The proposed solution was then verified within the model:
- New Ponton Road Pumping Station and small lift station at Old Heathwall Sewer.
- New gravity surface water sewer.
- Details of individual developments connections including flow controls.
- Carrying out design storm simulations to check pump selection, pipe capacities and storage volumes, as well as checking top water levels to ensure no detriment or flooding.
The breakdown of the area and finishes draining into the new surface water sewer system are shown in the table (below) and includes the 13ha removed from the existing combined network:
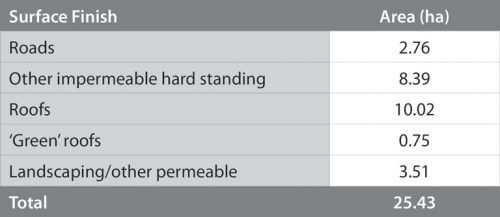
Breakdown of the area and finishes
The new surface water network and relocated/enlarged Ponton Road Pumping Station is designed for a 1 in 30-year rainfall event and maximum incoming flow currently equates to 667 l/s from the eastern leg and 976 l/s from the western leg with a maximum pumped flow of 1,100 l/s made up of duty (600 l/s)/assist (900 l/s)/further assist (1,100 l/s), which is the existing rising main capacity increased slightly from previous pump rate of circa 900 l/s.
When incoming flow exceeds the maximum pump rate, the oversized pipes fill until the storm subsides. The new surface water sewer and pumping station is designed to accommodate future development flows too, including the temporary flower market site/entrance site to the west (future flows unknown) and the Vauxhall gyratory in the east (estimated at 530 l/s).
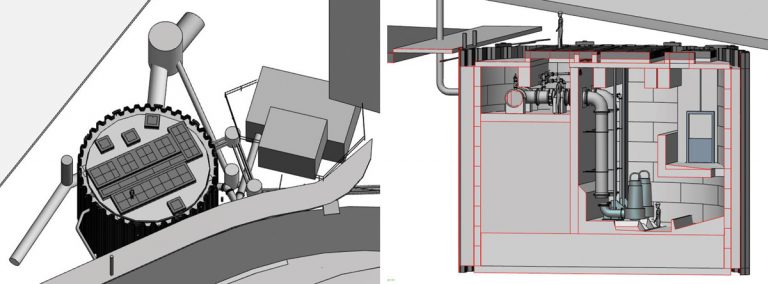
3D CAD drawing of main pumping station – Courtesy of eight2O
Proposed solution overview
Thames Water did not control the route of the pipeline, which travels through several active construction sites controlled by various developers. As a result, the team has had to work constantly around obstacles out of their control dealing with third parties to coordinate and help avoid construction clashes.
The new DN2100 pipeline runs 270m from the western boundary across a former Royal Mail depot (and prior to that an old gas works) which had site-wide remediation of contaminated ground completed down to 3m below ground level.
The new surface water sewer is around 5m deep here so breached the extent of remediated ground, and as a result the site team had to work carefully to avoid recontamination and meant dealing with both contaminated groundwater and disposal of 2,600m3 of excavated hazardous waste material from the total of 12,500m3 excavated here.
This contamination also impacted pipeline selection and led to wider learning in relation to hydrocarbon soil contamination and HDPE pipe selection/PCC pipes with gasket type seals too including expert analysis.
Between the former Royal Mail depot and the main pumping station site, the pipeline crossed the entrance of a live Royal Mail depot serving Westminster and Ponton Road, the main access and egress road for the entire development with 800 vehicle movements a day. Therefore it was not an option to use open cut trenching for this length so a 140m micro-tunnelled drive using a DN1200 pipe jacked section was completed to limit disruption along with 65m of open cut DN1200 either side of this.
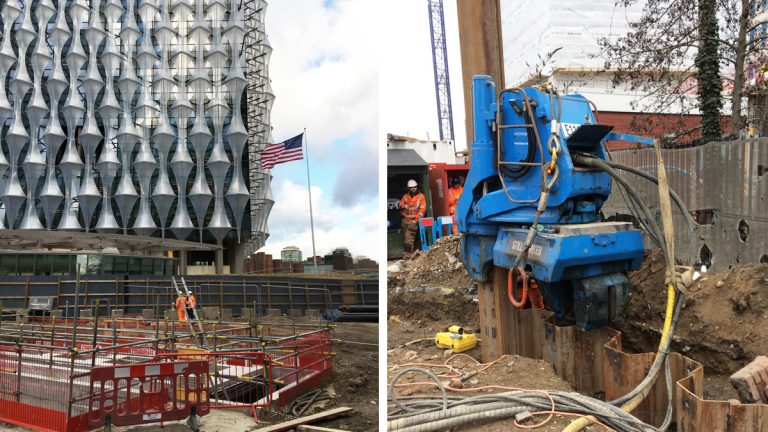
(left) Main PS awaiting cover installation and (right) Silent piling rig used for the main shaft – Courtesy of eight2O
The new DN12500 pumping station site is located centrally in terms of the new drainage network, sited between a new apartment block (which initiated the relocation of the existing pumping station) and the main entrance to new US Embassy. Collaboration was vital and while key allies put the finishing touches to their super secure HQ next door, TW’s eight2O Alliance was building the new surface water sewer network and pumping station in its shadow.
The new DN1800/2400 sewer then runs for 194m across the front of three apartment blocks, which led to a permanent sheet pile wall being installed to enable scaffolding to be erected and sewer to be laid at the same time. The final 190m section of DN1800/2100 follows the boundary of the former Covent Garden Flower Market site and crossed an underground reinforced concrete service tunnel linking the two market sites, which needed careful negotiation and planning and finishes at the Wandsworth Road.
Finally the team decided not to upsize or duplicate the existing rising main here to avoid unnecessary disruption as it had already been diverted around the new US embassy recently.
To succeed along this route required close cooperation and teamwork between all parties led by TW’s Developer Services team for planning and eight2O for design and delivery.
From the beginning this project has been marked by great cooperation and compromise by all parties and very complicated and lengthy land negotiations, but over time the trust of everyone involved was earned to deliver this scheme successfully.
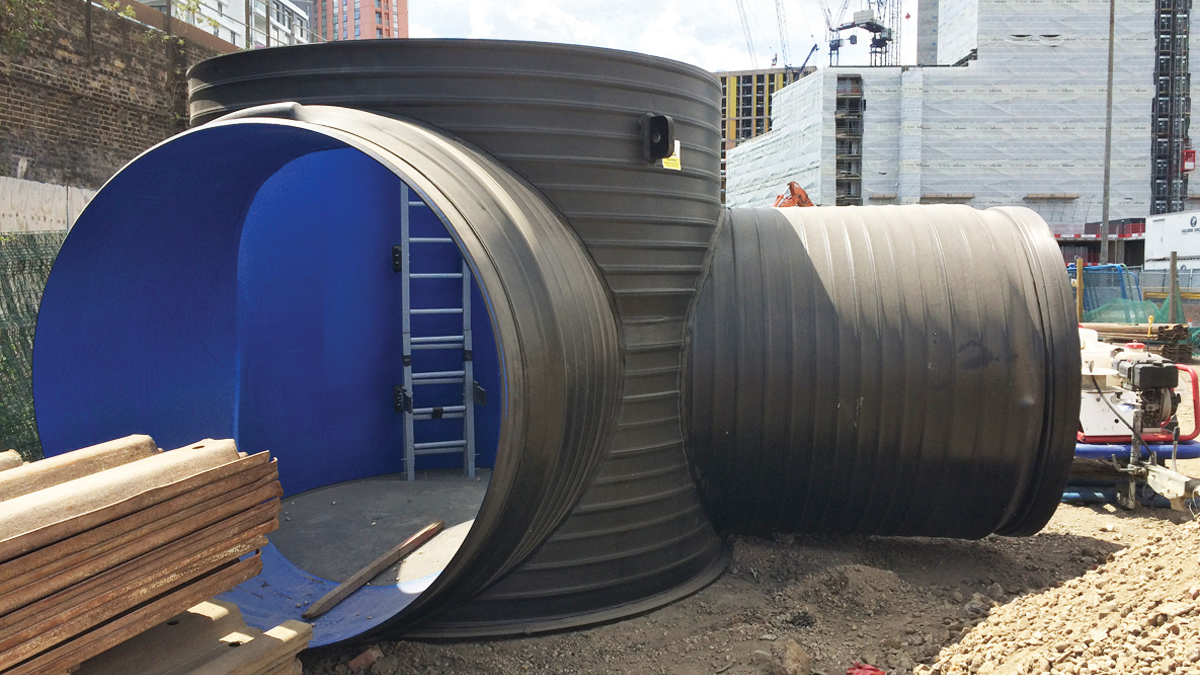
Bespoke change in direction access chambers – Courtesy of eight2O
Detailed design and construction
The completed project incorporates a new 900m long gravity sewer incorporating circa 3,000m3 of storage volume using DN1200 to DN2400 pipes with bespoke change in direction access chambers supplied by Polypipe and constructed by Davey Civils Ltd.
Additionally, the project required a DN1200 micro-tunnelled jacking pipe section and DN12500 pumping station shaft, which incorporates the inlet chamber, junction box and valve chamber to save space on a very tight footprint site, supplied by FP McCann and installed by Joseph Gallagher Ltd.
The project also includes an innovative reuse of an old section of the DN1200 Heathwall sewer which runs beneath the railway line from the south and will serve the redeveloped market site. The design involved diverting a small amount of foul flow still draining to it, then reusing the pipeline as an outlet for all new surface water sewers on the site. Due to level difference a DN3600 lift pumping station to drain siphon created was required.
Ground investigation
Made ground, alluvium, river terrace deposits, and London clay are typical ground conditions across the site. Based on the invert levels, the sewer will be predominantly founded in alluvium or river terrace deposits resulting in a small net reduction in vertical stress at foundation level and as such, no settlement or bearing capacity issues.
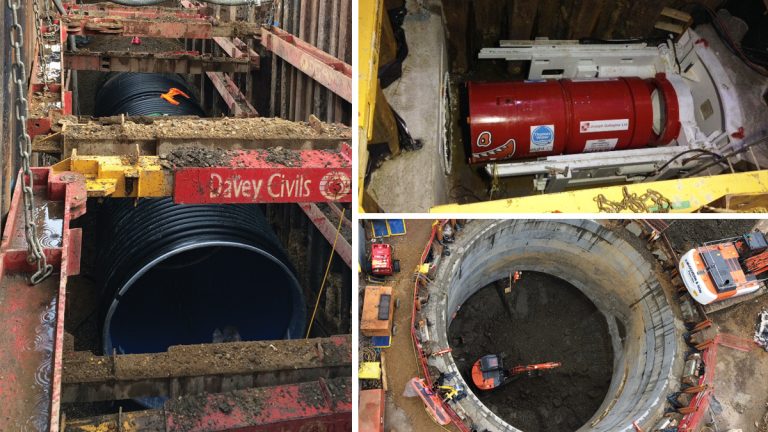
(left) DN2400 Ridgistorm XL pipeline excavation, (top right) tunnelling machine ready to go at Battersea and (bottom right) main PS shaft constructed using under pinning – Courtesy of eight2O
Consideration was given to the effects of groundwater with the water table 2.1m-4.8m below ground here, and sample testing results indicating high levels of petroleum hydrocarbon contaminants at the old gasworks site which led to a stringent discharge license from the Environment Agency and meant the installation of a temporary treatment plant at site prior to discharge to a foul sewer. All buried concrete was therefore designed to DS-1/AC-1 for shallower pipework but then DS-2AC-2/DS-3/AC-3 for deeper sections founded in London Clay.
Also, flotation of the proposed pipeline and chambers meant further liaison with Polypipe for HDPE pipework to ensure this was resolved.
The section of microtunnelling/pipe jacking of a DN1200 PCC pipe at around 6m depth predominantly in river terrace deposits was ideal and the DN12500 pumping station constructed as an underpinned shaft to 11m depth founded in the London Clay provided adequate support.
Design challenges and supplier liaison
Innovative pumping station design on small land footprint led to building a scale model build by Hydrotec and testing the inlet chamber and wet well to assist in designing incoming flow paths and benching to avoid poor pump performance and cavitation issues.
Early engagement with the supply chain meant that standard product and off-site construction solutions could be embedded within the design too and included the following suppliers:
- HDPE large diameter pipes and bespoke chambers: Weholite® and Polypipe
- Pumps: Xylem Water Solutions
- MCC Panel: Boulting Group
- GRP Kiosk for small lift PS: Kingsley Plastics
- Access covers: EJ
- Penstocks (to isolate PS DN1200 and DN1800): VAG Penstocks
- PCC shaft and bespoke cover slabs: FP McCann
- Valves: AVK
Thames Water Operations liaison
- Discussions with the TW Operations team was regular and the need to keep the existing Ponton Road Pumping Station live during construction was both a limitation and invaluable in terms of constructing all new assets off line with no over-pumping required.
- TW standards for key assets required two independent mains electrical supplies together with the facility for connection of a mobile generator.
- The team agreed a unique shaft design due to limited footprint here including technical waivers to standards for layout and valve types to save space. All maintenance is planned from ground level and man access only required for planned less routine maintenance via solo-lift access chambers.
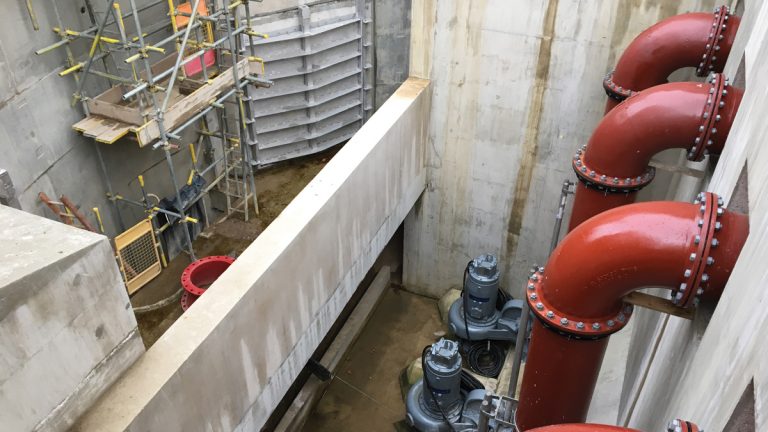
DN1800 penstock inlet and main pumping station wet well – Courtesy of eight2O
Also due to restriction on use of a kiosk, fencing or lifting gantry within the Linear Park as a compromise the MCC panel and incoming power supplies are housed in a dedicated room provided by the developer in the ground floor of an adjacent building. With a new reinforced section of footway designed to be hidden beneath the proposed granite set finish to act as a lay-by for the mobile crane to sit on during pump removal.
Outcomes
The project aligns with Thames Water’s Outcomes and Objectives including the following:
- Delivered 13 hectares of the 20-hectare surface water run-off removal target for the entire AMP6.
- 80% use of standard products: HDPE & PCC pipes/chambers/shaft and pumps from Xylem Water Solutions.
- 20% TOTEX reduction: Net reduction in pumping and treatment costs downstream.
- 50% offsite construction: Bespoke HDPE access chambers, PCC pipes/chamber rings and cover slabs, MCC control panel and specialist infill type access covers.
Results/lessons learnt
At the time of writing (May 2018) the project has been constructed successfully with just commissioning still outstanding. However, the main PS is now live so that the existing PS can be demolished and decommissioned to enable the developers to progress.
- The only work remaining is the mechanical and electrical fit out of the smaller lift pumping station while awaiting disconnection of foul sewer flow from the soon to be surface water line within the old Heathwall sewer.
- Ground investigation and route/materials of pipeline through contaminated land has been a learning curve for the team.
- Early liaison and collaboration with all landowners and affected third parties was essential. However, having restrictions all around led to innovative thinking being the norm here rather than the exception.
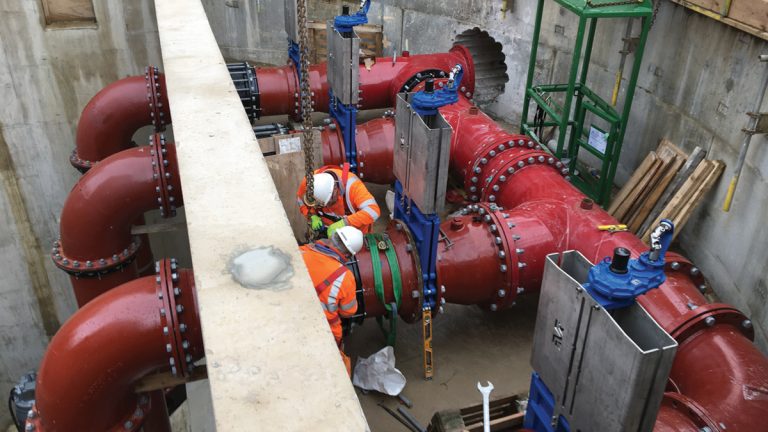
Wall between wet well and valve chamber – Courtesy of eight2O
Conclusion/summary
The collaborative working between the key stakeholders including TW, Nine Elms Partnership, Ballymore, Bellway Homes, Royal Mail Group, New Covent Garden Market, eight2O (Stantec and Costain), Wandsworth Council, CH2M, Camlins Landscape Architects, ARUP and AECOM has been a huge success.
It has enabled the successful construction of a new surface water sewer network linked to a wide range of developers SuDS solutions within a tight utility corridor bringing with it customer, community and environmental benefits.
The small footprint on which to site the relocated pumping station and early supplier engagement led to some very innovative designs including a multi-funtional pumping station shaft, HDPE bespoke change-in-direction access chambers, infill solo-lift access covers and very limited above-ground features (an MCC room within an adjacent building and a hidden lay-by for TW Operations vehicles).
TW Operations as final user, has been involved and consulted throughout the project and whilst compromise was required, they are happy with the new improved asset provided here.