Tideway Central – Overview (2018)
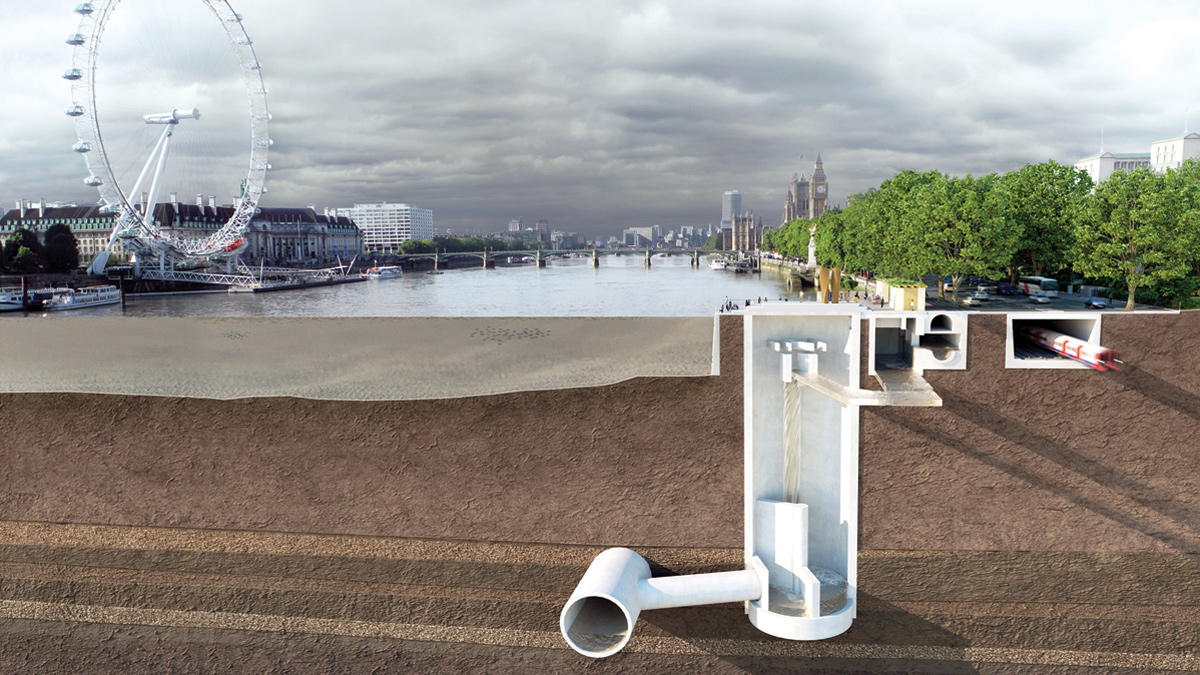
Visualisation showing cross section through the Thames Tideway Tunnel Central Victoria CSO site - Courtesy of Tideway
Thames Tideway Tunnel is the largest water infrastructure project currently under construction in the UK and will modernise London’s major sewerage system, the backbone of which dates back to Victorian times. Although the sewers built in the mid-19th century are still in excellent structural condition, their hydraulic capacity was designed by Sir Joseph Bazalgette for a population and associated development of 4 million people. Continued development and population growth has resulted in the capacities of the sewer system being exceeded, so that when it rains there are combined sewer overflows (CSO) to the tidal Thames performing as planned by Bazalgette. To reduce river pollution, risk to users of the river and meet bespoke dissolved oxygen standards to protect marine wildlife, discharges from these combined sewer overflows (CSOs) must be reduced. The Environment Agency has determined that building the Tideway Tunnel in combination with the already completed Lee Tunnel and improvements at five sewage treatment works would suitably control discharges, enabling compliance with the European Union’s Urban Waste Water Treatment Directive.
Project structure and programme
The Thames Tideway Tunnel closely follows the route of the river, intercepting targeted CSOs that currently discharge 18Mm3 of untreated sewage a year. Once complete, it will connect to the Lee Tunnel and then sewage will be pumped to treatment at Beckton STW by the Tideway Pumping Station.
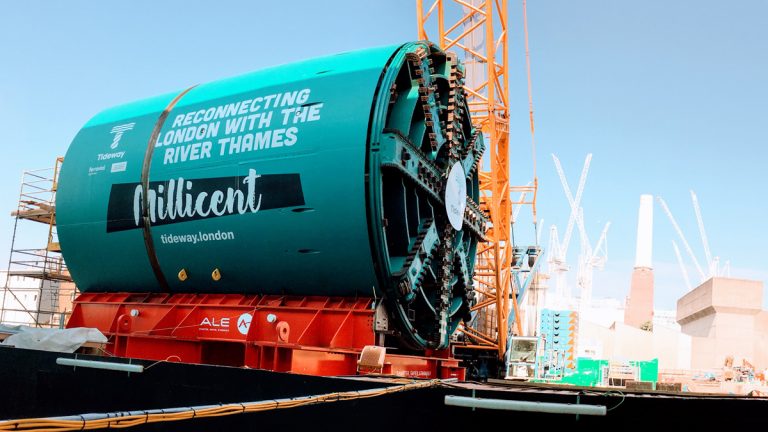
Tunnel boring machine arriving at Kirtling Street shaft site outside Battersea Power Station – Courtesy of AECOM
Due to the size and complexity of the project, a new wastewater utility was formed; Bazalgette Tunnel Limited (trading as Tideway). Tideway will construct, own and maintain the Tideway Tunnel. However, Thames Water will remain the overall operator of the sewerage system, including the tunnels. Tideway has split the project into three detailed design, consenting and construction contracts – West, Central and East – which roughly correspond to three distinct geological zones encountered by the main tunnel. There is also a fourth overarching systems integrator contract providing the project’s monitoring and control system. Jacobs Engineering is the overall programme manager for Tideway.
The three main civil works contracts were awarded in September 2015. The programme is for all contracts to be sufficiently completed to allow commissioning by 2022 with handover and CSO control by early 2024. Following handover, there is an 18 to 36-month system acceptance period at the end of which Thames Water will take over maintenance responsibilities for the near-ground interception structures and assets.
Tideway will retain responsibilities for the deep shafts, drop tubes and tunnel structures for the duration of the project’s 120 year design life. Thames Water will operate the system.
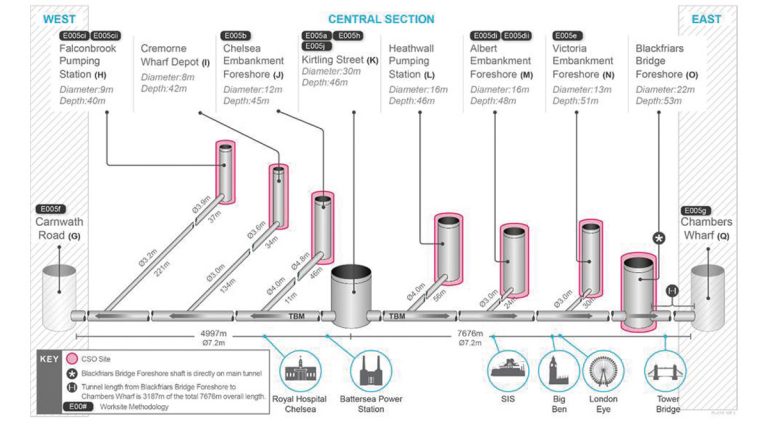
Tideway Tunnel Central Contract
Key elements of the Central Contract
This article covers the Central Contract, which with a tender value of £750 million is the largest of the three area contracts. A joint venture of Ferrovial Agroman UK and Laing O’Rourke Construction (FLO JV) is the main contractor and has appointed AECOM as main designer for the permanent works to provide the detailed hydraulic, civil/structural, MEICA and architecture design and to support the consenting process. Jacobs Engineering Group provides programme management, contract administration and CDM principal designer services to Tideway.
Spanning 12.6km and directly intercepting nine CSOs, the Central section of the tunnel extends from Hammersmith & Fulham in west London to Southwark in east London, passing close to many of the Capital’s key landmarks such as Tower Bridge, Victoria Embankment, Royal Hospital Chelsea, Battersea Power Station and the Houses of Parliament. The tunnel runs through seven London boroughs, passes beneath 20 sensitive road, rail and pedestrian bridges and close to 30 tunnels including tube and cable tunnels, 138 buildings, as well as numerous listed river walls, in-river structures and major utilities.
Main tunnelling activity is focused around the Kirtling Street site adjacent to Battersea Power Station, where two tunnel boring machines (TBM) will drive out of the shaft; one for a distance of 5km to meet the West contractor at Carnwath Road in Hammersmith and Fulham adjacent to Wandsworth Bridge, and one driving 7.6km easterly under Tower Bridge to meet the East contractor at Chambers Wharf in Southwark.
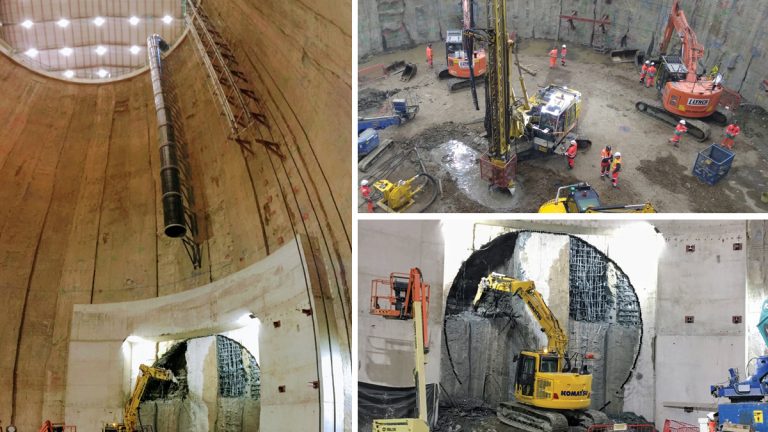
(left) Construction of the sprayed concrete lining TBM launch adit at the base of Kirtling Street shaft, (top right) jet grouting trial at the Kirtling Street shaft site in advance of the jet grouting operation at Blackfriars and (bottom right) breaking out the main tunnel portal at the Kirtling Street drive shaft – Courtesy of AECOM & FLO JV
In addition to the main TBM launch shaft, there are a further seven worksites with deep shafts which contain vortex drop structures to convey intercepted storm flows from the existing sewers to the Thames Tideway Tunnel. Alongside these there are associated interception chambers, valve chambers, air treatment structures and connection tunnels and culverts constructed in a mixture of diaphragm wall, secant piled, sprayed concrete lining (SCL), precast concrete and in situ concrete.
Key drivers and design challenges
Geology: While the West Contract section of the main tunnel is predominantly in London Clay and the East Contract section is in Chalk, the Central section covers a range of ground conditions, with sands and gravels forming major constituents. The geology transitions from West to East through the London Clay, into the complex Lambeth Group, where clay, sand and gravel strata are interlayered with the inclusion of numerous hard layers of mudstone, limestone, sandstone and calcrete. As the tunnel progresses further East it enters for a short duration into the Thanet Sands, where sandy and silty deposits are encountered together with cobbles of the Bullhead Beds, before giving way to the Chalk and flints. The interfaces or transitions between geological layers are particularly challenging.
A large programme of ground investigations was carried out before the main works contract was let, including two phases of overwater exploratory holes bored from jack-up barges within the main channel and foreshore of the River Thames and four phases of land-based exploratory holes drilled close to each of the proposed shaft sites. This has been augmented with additional ground investigations carried out by FLO to add to already available information. Investigations have focused at the sites of CSOs and main construction shafts, together with their sub-river connections to the main tunnel. Elsewhere, investigations have been undertaken at intervals along the length of the tunnel alignment, governed by geological features such as folds and faults and accessibility considerations.
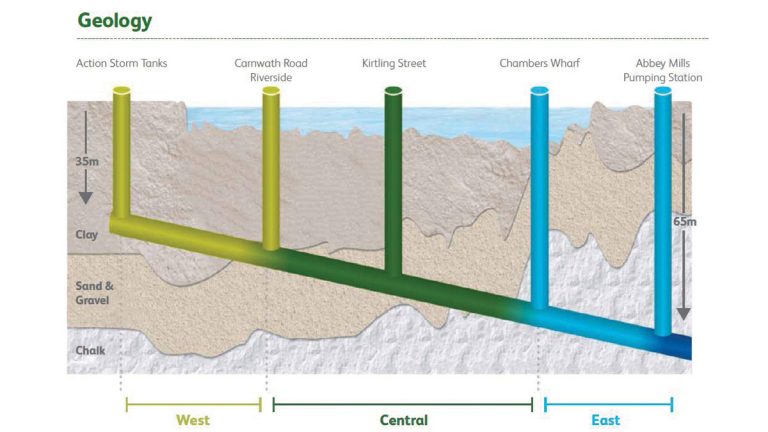
Project-wide overview of Tideway Tunnel geology – Courtesy of Tideway
The bases of the shafts and connection tunnels are situated mainly in the Lambeth Group and Thanet Sands 15-35m below the piezometric water level of the lower aquifer, so dewatering will be needed to ensure they can be constructed safely without the risk of groundwater inflow and ground instability at the base of the excavation.
Main tunnel: To enable the construction of the main tunnel through the variable ground conditions, two earth pressure balance TBMs with an external diameter of 8.8m will be launched from a 30m diameter, 60m deep (to formation level) shaft at Kirtling Street, which was constructed using the diaphragm wall technique. The TBMs, supplied by French company NFM Technologies, each have an approximately 780 tonne cutting head and tunnelling shield with a 100m long production train behind them housing the handling and assembly plant for the precast concrete segmental primary tunnel lining, spoil conveyors, control centre and ventilation equipment.
Due to noise and construction hours of operation constraints, the drive shaft is housed inside a large acoustic shed. This will enable continuous operation of the TBMs with materials stored then removed from site via barges on the river. The precast segments used for the tunnel lining will also be transported to site via the river from a casting yard at Thamesport on the Isle of Grain in Kent.
Hydraulic modelling: Hydraulic modelling of the complex Tideway Tunnel system was undertaken as part of the reference design, both in the form of numerical modelling and physical modelling. Design flows into each of the CSO drop shafts range from a smallest value of 18m3/s at Cremorne Wharf to a largest value of 51m3/s at Blackfriars. To prevent adverse transient conditions in the tunnel or the system becoming overwhelmed and surcharging uncontrollably during severe storm events each interception site has automated penstock controls in place to limit flows into the main tunnel under extreme storm events. When the tunnel system reaches set levels any residual combined sewage flows will revert into the River Thames. Overall the whole CSO scheme will reduce discharges from over 50 to four or less in a typical year, with CSO volumes reduced by more than 90%.
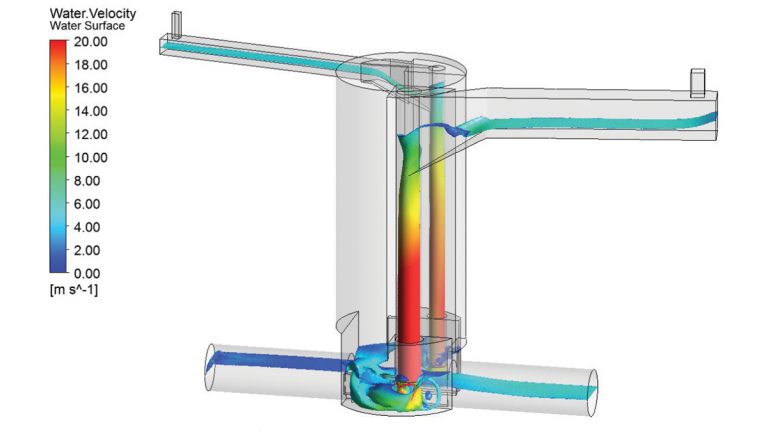
CFD modelling of combined sewer overflow drop shaft at Blackfriars – Courtesy of AECOM
Under the contract FLO is required to demonstrate that it meets the enumerated requirements of the hydraulic specification. Key concerns are that the final design does not in any way diminish the hydraulic performance of the system, particularly the interception chambers and vortex generators; that transient hydraulic movements and air flows due to differential filling of the tunnel are accommodated; that abrasion and corrosion due to sewage flows can be controlled for the 120 year design life and that entrained air entering the system is effectively limited by de-aeration structures built into the CSO drop shafts. AECOM has built upon the reference design materials and, as required by the works information, undertaken Computational Fluid Dynamics modelling for each worksite to demonstrate hydraulic compliance and has commissioned physical hydraulic scale models of the Falconbrook Pumping Station and Cremorne Wharf worksites.
Third party consents and damage risk assessments: With the Central section of the Tideway Tunnel running beneath or close to so many key London landmarks and infrastructure assets, third party consents have been a major challenge for the project. The development consent conditions require FLO (with AECOM, Arcadis, Robert West, OTB Engineering and WSP) to carry out a phased approach to impact assessment, with initial green field settlement assessments undertaken to determine structures likely to be affected and then more detailed Phase 2 and Phase 3 assessments carried out to determine which structures require monitoring and which require mitigation measures, such as diversion or strengthening of utilities.
Overall, 25 detailed assessments have been carried out on bridges, 69 on utilities and non-listed buildings, 38 on tunnels, including London Underground and utility tunnels, 36 on in-river structures such as piers and eight on listed buildings. In addition, detailed existing river wall assessments have been carried out at each work site.
Blackfriars CSO drop shaft and Fleet Culvert: Blackfriars is the most challenging of the CSO drop shafts sites on the Central contract and the project. The shaft will be 53m deep and 22m in diameter, constructed within a cofferdam within the Thames, adjacent to the north bank. Once complete it will receive 51m3/s of flow from the existing interceptor and storm relief sewers which will be conveyed through two vortex drop structures to the bottom of the drop shaft, which is directly on the line of the main tunnel.
The shaft is in a high profile location adjacent to Blackfriars Bridge, the main line railway and in close proximity to two medium pressure gas mains, the District and Circle Line, Waterloo and City Line, listed river wall and other listed buildings. Prior to the start of the cofferdam construction an existing Thames Clipper pontoon pier had to be dismantled and removed and a new pier installed east of Blackfriars Bridge.
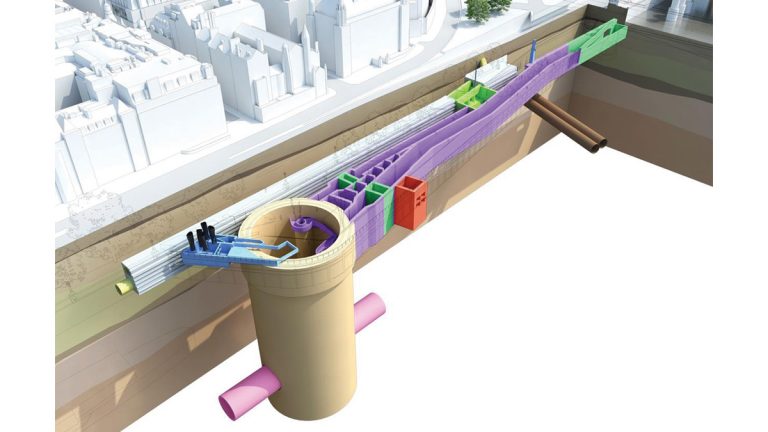
Proposed CSO shaft and Fleet Culvert at Blackfriars – Courtesy of Tideway
The original intention was to build the primary lining of the shaft as a reinforced concrete diaphragm wall and receive the TBM into this. However, due to a number of programming, logistical and consenting issues, the diaphragm wall shaft would not have been completed by the time the TBM was due to pass through the bottom of the shaft. The shaft primary lining design has therefore been changed to comprise temporary piles and a reinforced concrete header section at the top of the shaft and a sprayed concrete lining section at the bottom of the shaft. This construction allows the shaft to be constructed once the main tunnel TBM has passed through. To enable the TBM to safely stop for maintenance beneath the site as planned, a jet grouted safe haven will be created on the tunnel alignment, which will be broken out to create the shaft base once the TBM has left the shaft site and the SCL operation commences.
Jet grouting will also be used in combination with dewatering to stabilise the ground and minimise the risk of large groundwater inflows during the excavation of the shaft. Experience of jet grouting the Lambeth Granular and Thanet Sands within Central London is limited, although similar soils have been grouted in projects overseas. Due to this industry wide lack of experience at grouting in these strata and at these depths in the UK, it was necessary to conduct a trial test and a detailed assessment of the grouting parameters at the Kirtling Street shaft site. The main challenges to overcome during construction will be the control of the drill deviation, taking into account the more than 50m depth of the treatment and the target column diameter of 2.6m.
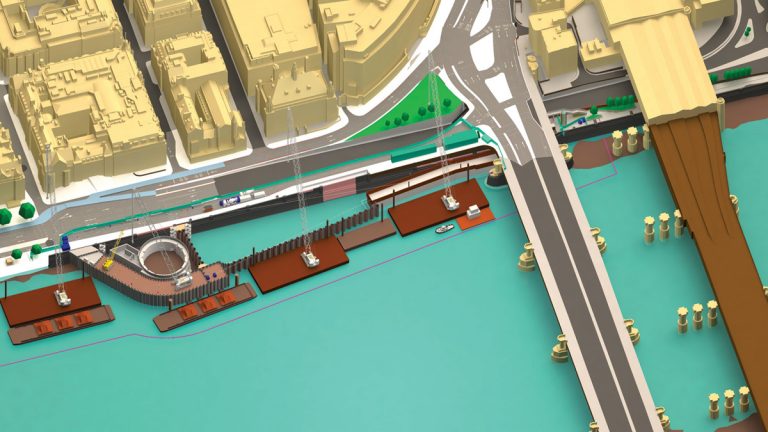
Visualisation of the temporary cofferdam and working arrangements at the Blackfriars site – Courtesy of FLO JV
Equally challenging is the construction of the Fleet culvert. This culvert section forms the eastern half of the of the foreshore structure and will intercept and convey overflows from the Fleet Sewer overflow located under Blackfriars road bridge. The culvert will span over the Waterloo and City line and convey flows to the drop shaft approximately 200m west of the Fleet interception. Whilst still under early stages of design development the proposal is to construct this by precasting a 100m long culvert section within the upstream cofferdam. The cofferdam would be flooded allowing the culvert section to be floated into position.
This operation would need to be timed during a dry weather period when there would be a low risk of overflows from the Fleet CSO and under specific tidal conditions. Maintaining the bed formation under the culvert is critical.
As wells as the civil and marine engineering challenges, the works will interface with the existing infrastructure, river bed and river navigation and will require close liaison and approvals from key stakeholders including the City of London, London Underground, Thames Water and Port of London Authority.
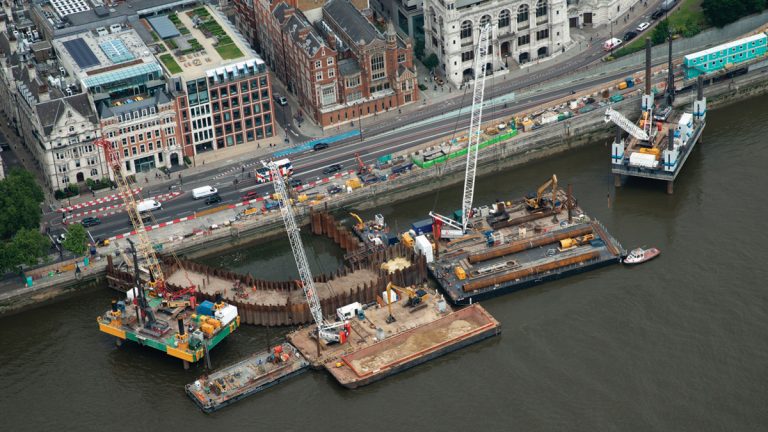
Marine works at the Blackfriars site – Courtesy of Tideway
Falconbrook Pumping Station Interception Chamber: The western-most worksite of the Central Contract is one of the most complex in terms of interfaces with existing Thames Water assets. The Falconbrook interception structure will receive 22m3/s of flow from three major existing storm sewers which are currently pumped to river during storms by the existing pumping station. An 18m deep reinforced concrete chamber will have to be built around the Low Level Relief Sewer Number 1 while keeping this live, necessitating the installation of robust temporary works to carry the flows during the construction phase. The chamber will be constructed within a temporary secant pile box with complex propping to minimise the risk of damage to adjacent critical Thames Water assets which are less than a metre away from the excavation. The site contains the historic foundations and basement of an old pumping station as well as the infrastructure of the newer pumping station, which was constructed in the 1960s. During the site investigation contaminated groundwater and historic sheet piles have been found at the site of the interception chamber, necessitating a review of the design to accommodate these additional constraints.
Innovative design solutions
BIM modelling of the TBM: BIM and virtual reality (VR) models of the TBM and worksites have been produced to enable a better understanding of the workspace constraints and train staff before they enter into the live tunnelling environment. FLO JV has worked with visualisation specialists Hobs 3D to develop a cost-effective, interactive and accessible training and site induction process. Using software from the gaming industry and stereoscopic display, Hobs 3D has created an interactive group VR experience that gives users a high-fidelity induction into the hazardous environment. Original CAD data was taken from Revit files and then optimised to match the requirements of real-time visualisation. Using a simple tablet interface, communicating over a closed Wi-Fi network, the instructor can guide users through the virtual work space. Tideway estimates the system, which has been part funded by government agency Innovate UK, could potentially see a 20% reduction in training time, a 10% reduction in accidents and near-misses and most significantly increases employee understanding of on-site hazards and risks.
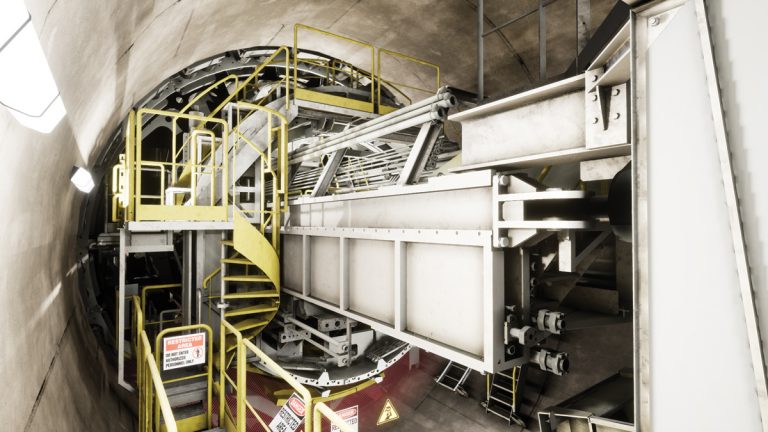
Visualisation from the virtual reality model of the TBM, showing working conditions within the main tunnel – Courtesy of Hobs 3D
Abrasion protection and CSO drop shaft design: The Tideway Tunnel and associated structures have a design life of 120 years and have to be protected from abrasion caused by high flow velocities during that period, together with impacts from items which may be washed down or thrown into the sewers such as timber sleepers or in the extreme even engine blocks. To avoid physical testing of concrete for abrasion resistance, specialist durability consultant OtB Concrete developed an innovative method of assessment based on previous physical testing research.
This determined the flow velocity and exposure time required to cause significant abrasion. AECOM then used CFD analysis to pinpoint abrasion hotspots on the tunnels and structures where limited additional concrete cover or stainless steel plate protection could be provided, rather than having to take a blanket approach. The scale and design life of the large vortex drop structures dictated that these will all have to be stainless steel lined. The design of these structures was coordinated across all three main works contracts to provide a standardised and efficient design.
Value engineering delivered
Main tunnel: The works information includes a requirement for a reinforced concrete secondary lining. FLO, in collaboration with the other main works contractors, identified an opportunity to develop an alternative precast segmental concrete secondary lining which in combination with the precast primary lining would still meet the performance requirements of the tunnel lining system, potentially reducing cost, improving construction schedule, reducing both environmental impacts and likely rework for the main tunnel compared with the in situ option.
The precast concrete secondary lining initiative is being supported by Tideway with the East and Central contractors currently proceeding with the development and trial of a lining erector machine to verify the solution.
AECOM worked with FLO to change the concept design from load sharing between the primary and secondary linings to designing a primary segmental concrete lining that will take 100% of the hydrostatic and ground loads. In addition, connection tunnel junctions with the main tunnel have been developed by AECOM and sub-consultant COWI to allow propping on the outside of the tunnel instead of the inside to enable connections to be made whilst minimising the impact on main tunnel production, saving months of programme time.
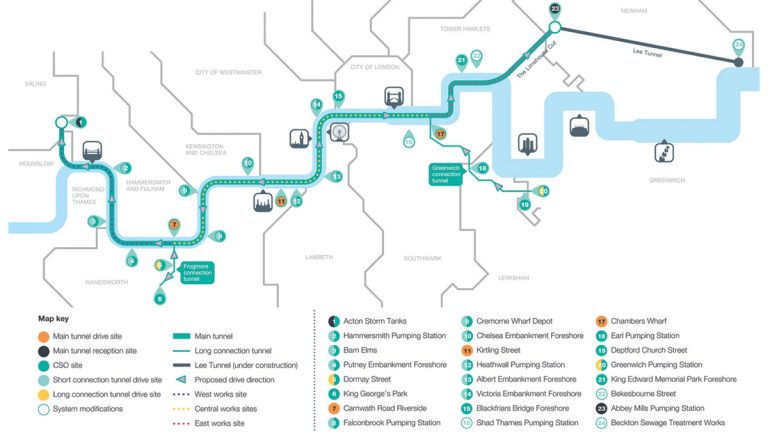
Thames Tideway Tunnel Route – West, Central & East Sections
Storm pump exercising: The original works information design required the provision of a new storm pump exercising system at Falconbrook Pumping Station to be regularly used to ensure that the storm pumping station can operate when called upon due to the infrequent need for storm pumping because of the interception into the Tideway Tunnel upstream of Falconbrook PS. This would have required a significant water supply requirements and would have taken Thames Water operatives two shifts to complete each time the exercising was carried out. FLO, working with Tideway and Thames Water, proposed an alternative system that would enable existing pumps to pump against closed valves for a short period of time, resulting in a lower capital cost solution requiring less water usage, less time and fewer operational staff.
Health and safety
Tideway has adopted an immersive behavioural health and safety approach including ‘EPIC’ live role play training on realistic film-style sets depicting a site, client office, HSE office and accident victim’s home. This and other initiatives within the project have brought a strong H&S culture throughout the Central contract. In relation to design, regular inter-disciplinary Designer’s Risk Register workshops are held with FLO and Tideway and AECOM has developed an innovative risk scoring system which highlights significant ‘Black Swan’ risks that are low probability but high consequence, so that these can be given the focus they deserve.
Collaborative multi-disciplinary review sessions including Thames Water, Tideway, FLO, AECOM and key sub-consultants and suppliers are regularly held to ensure the design is developed to eliminate or reduce risks where possible and with the needs of the end user in mind. Design for Manufacturing and Assembly techniques are also being used to increase off-site production and increase safety during the construction phase for shaft roof slabs, river walls and some elements of the interception chambers.
Architecture
Delivering a legacy of attractive public realm spaces in central London has been one of the key aims of Tideway. As a number of the CSO shaft and interception chamber sites are being constructed on new foreshore structures created in the tidal Thames it has been a challenge to ensure these will look attractive and an integral part of the Thames whilst also remaining useable workspaces for the maintenance of the structures. AECOM, working with architect Hawkins\Brown, landscape architect Gillespies and lighting specialist Studio Dekka, has been responsible for further developing the architectural designs from the Design Principles agreed by Tideway with local authorities and other stakeholders as part of the Development Consent Order Planning process.
Tideway has also commissioned artists to integrate public art into the designs. Integration of the above ground architecture has been achieved through BIM modelling and regular Progressive Design Assurance meetings to ensure that the functional requirements for Tideway and Thames Water are maintained while achieving the functional and aesthetic aims of the public spaces. Independent peer reviews of the architectural designs have also been carried out at the most sensitive sites through the Design Council Cabe Design Review process.
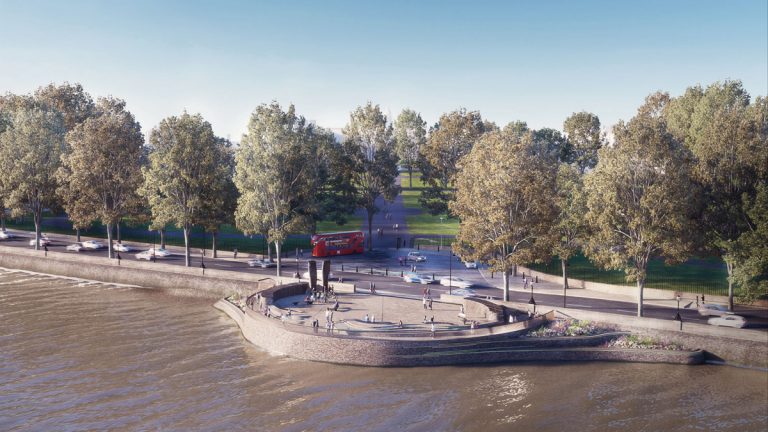
Architectural design of the Chelsea Embankment Foreshore site, adjacent to the Royal Hospital Chelsea – Courtesy of HawkinsBrown
Conclusion
The Thames Tideway Tunnel Central Contract is a highly challenging project which involves construction of major shafts, tunnels and marine works in some of London’s most sensitive locations, passing close to major landmarks and key transport infrastructure. Once complete the project will deliver significant benefit in cleaning up the River Thames by intercepting and controlling combined sewer overflows that currently discharge untreated into the river and it will also leave a legacy of new public realm space for the public to enjoy for years to come.
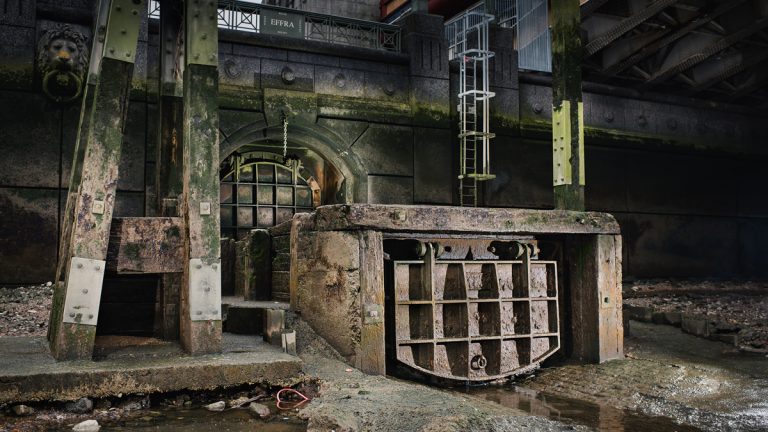
Existing CSO on River Thames – Courtesy of AECOM
The technical, logistical and operational difficulties of the project have required an innovative approach to the design and proposed construction of the works. Particular challenges include the number of interfaces and transitions in geology that the TBMs will have to negotiate as well as the number of third party interfaces involved. At the highly constrained Blackfriars shaft site an agile design approach is being employed to meet the programme for the TBM’s arrival together with innovative methods to construct the works within the marine environment, including the precasting and floating into position of the 100m long Fleet culvert. At the time of writing the detailed design is well progressed and enabling and marine works are progressing across the project’s worksites. The main TBM launch shaft in Battersea has been constructed to full depth and the TBMs are in the process of being assembled, ready for launch towards the end of 2018. Commissioning is planned for 2022 with Handover and CSO control planned for 2024.