Paisley Tunnel Project (2019)
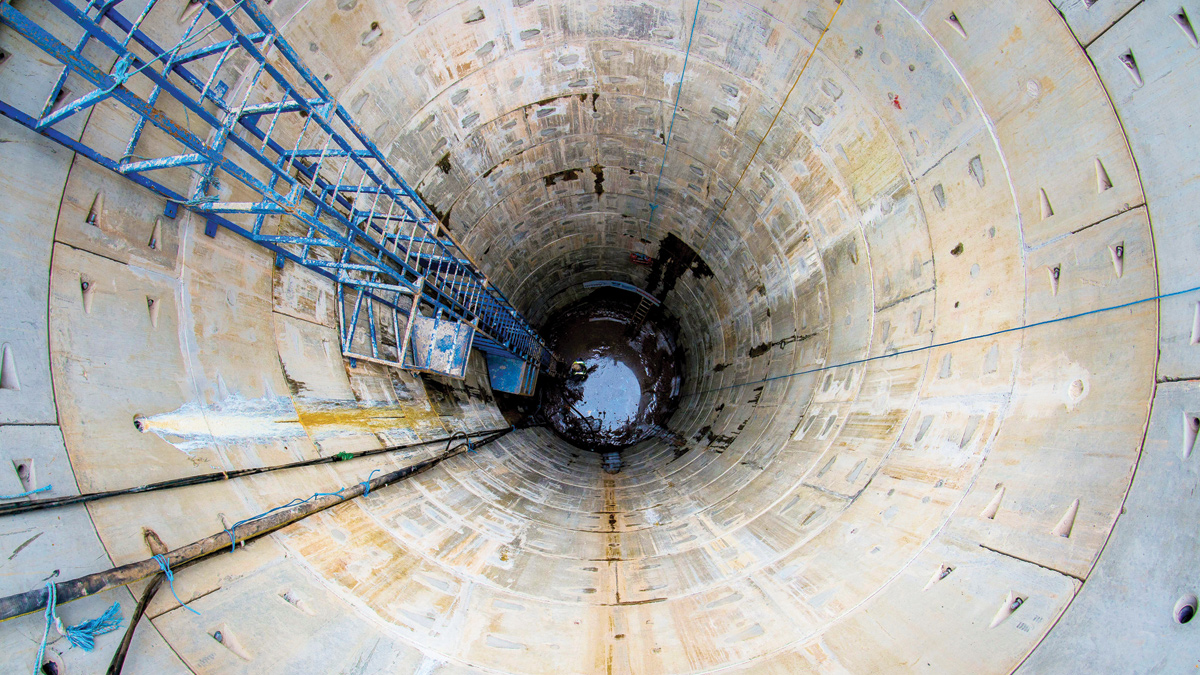
Shaft for the tunnel - Courtesy of Scottish Water
Scottish Water’s £17m Paisley Environmental Project, which started in October 2016, is the largest of its kind that Scottish Water has ever made in Renfrewshire. The project is part of the company’s £250m, six-year programme of work, launched in 2013, to improve river water quality and the natural environment and tackle flooding across the Greater Glasgow area. The Paisley Environmental Project has improved the water quality and natural environment in two local watercourses; the Espedair Burn and White Cart Water, and in turn, the River Clyde. The project comprised the construction of a mile-long wastewater tunnel under the streets of Paisley and the installation of combined sewer overflows (CSOs) in the town centre.
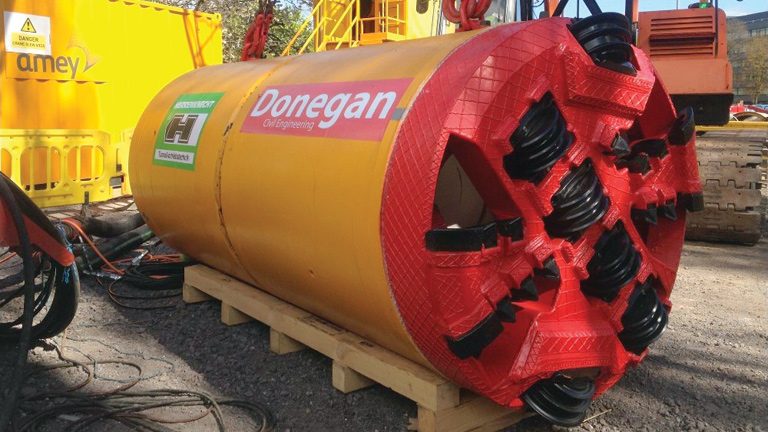
Tunnel boring machine – Courtesy of Scottish Water
Project summary
The new infrastructure will fundamentally alter the performance of the drainage catchment in Paisley and retain more of the storm flows in the sewer network, which ultimately go to the Laighpark WwTW, meaning storm spills to the White Cart Water and Espedair Burn have been substantially reduced.
Working for Scottish Water, main contractor Amey and main sub-contractor, VJ Donegan Civil Engineering Ltd have constructed the large diameter interceptor sewer. Starting in a car park close to the town centre the tunnel crossed below busy dual carriageways before going beneath the railway line near Canal Street Station, under Saucelhill Park and through residential areas.
By intercepting the overflows from nine existing CSOs, the new sewer will completely remove future spills into the Espedair Burn up to a 1:5 year storm. It will then transfer these flows downstream to new large, powered screen CSOs being installed on the opposite side of the White Cart Water from Paisley Abbey and at Causeyside Street opposite Dunn Square.
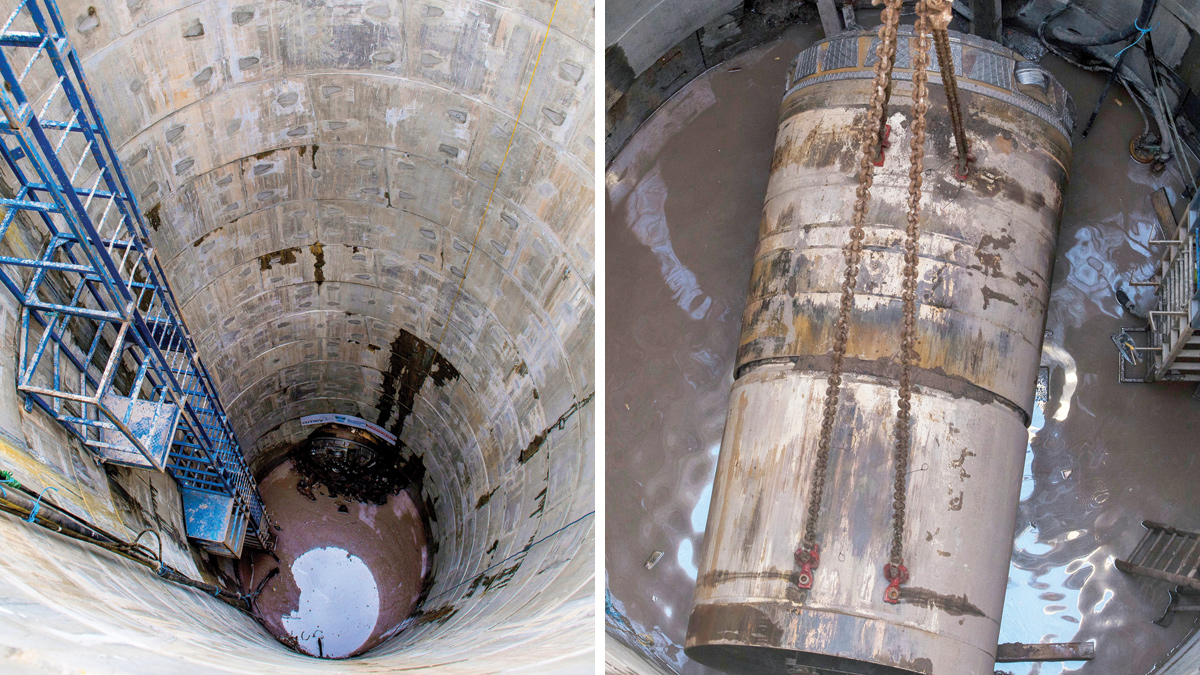
(left) Shaft and tunnel breakthrough and (right) removing the TBM – Courtesy of Scottish Water
The Paisley Tunnel Project comprises:
- 1.6km transfer sewer.
- 200m of 1000mm diameter tunnel.
- 1000m of 1200mm diameter tunnel.
- 300m of 1500mm diameter tunnel.
- 100m of open cut works ranging from 375mm-1500mm diameter.
- 14 (No.) shafts ranging from 4.0m-7.5m diameter.
- New combined sewer overflow at Bridge Street.
- New combined sewer overflow at Causeyside Street.
The tunnels
The route of the sewer tunnel was chosen to minimise disruption to local residents, road users and businesses. It has a diameter of up to 1.5m and was installed at depths of between 4m and 27m. A total of 14 shafts were installed along the sewer route.
The tunnel was constructed using the ‘closed face’ method, with pipe-jacking used to install the pipes behind a remotely-controlled and guided microtunnel boring machine (MTBM). The remote control operation takes places from a control centre above the launch shaft.
Pipe-jacking
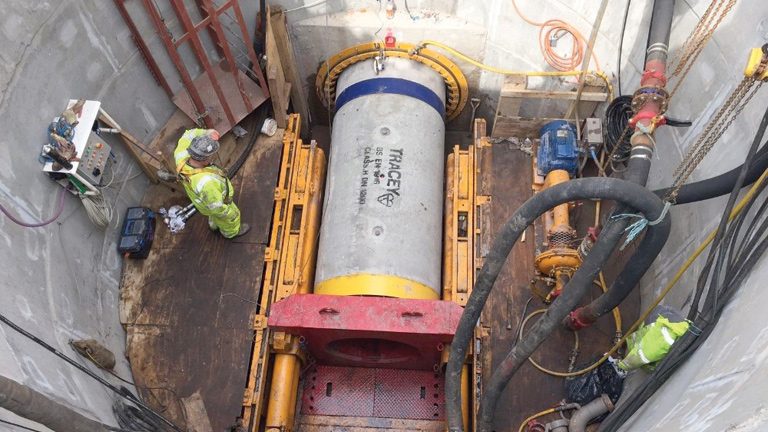
Pipe jacking in progress – Courtesy of Scottish Water
The pipe-jacking operation balanced groundwater and earth pressures, and once the MTBM had removed the soil, individual sections of concrete pipe were installed sequentially and jacked into position to the rear of the machine. This method is be much more efficient and less disruptive than using the open cut method of excavating, given the depths of the pipe and the urban location.
Other trenchless methods used in the project included directional drilling and hand dug timber headings. These methods were utilsed when a TBM or open cut were unsuitable due to the length or depth of the drive or where existing buried services had to be crossed.
Herrenknecht slurry TBM
Three Herrenknecht AVN slurry machines were utilised on the project. These were: 1500mm diameter TBM for 1 drive, 1200mm TBM diameter for 11 drives and a 1000mm diameter for 1 drive.
The tunnels were predominately bored through rock (sandstones and mudstones) with only some areas of boulder clay. A mixed ground cutting head was used on all the drives with the exception of the 1500mm drive where a rock head was used.
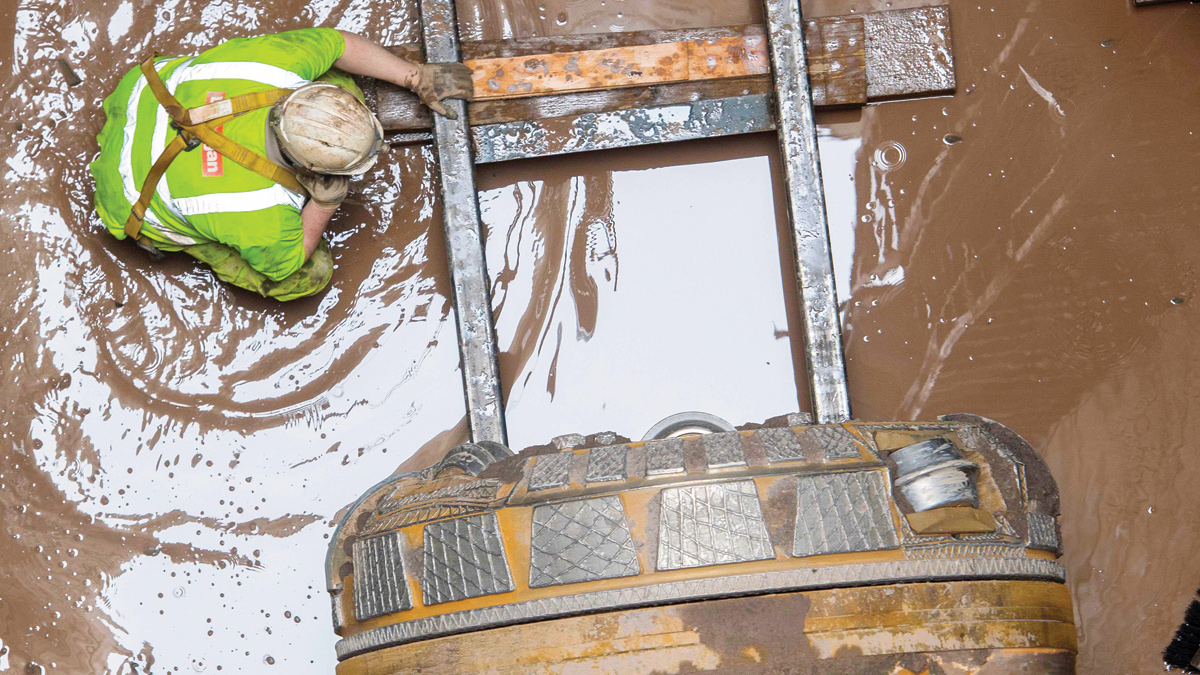
TBM breakthrough – Courtesy of Scottish Water
Above ground site set up and shaft construction
Most of the shafts where constructed using segmental concrete shaft rings with some shafts formed within steel sheet piled cofferdams.
During tunneling works the drive shafts sites housed the main pipe jacking stations and slurry treatment plants. The limited space available at these locations to house all of this equipment was one of the main challenges on this project.
MTBM launches
The launch chamber for the first Herrnenknecht machine, named Abbey, was constructed in Bridge Street car park Bladda Lane. The MTBM was lowered into the shaft in April 2017 in two sections. Once assembled, the machine was 7m long, 1200mm in diameter and weighed 12 tonnes.
Powered by an external hydraulic power pack, the MTBM operated at about 8 linear metres per day, removing about 45 to 50 tonnes of earth per day; mainly mudstone and siltstone.
Tanya, the second machine, was launched from close to Espedair street, has a diameter of 1.5m and weighs 23 tonnes and tunnelled 270m at depths of 27m beneath Saucelhill Park, removing 5000 tonnes of rock before terminating adjacent to the Canal Street station. This drive commenced in January 2019 and was completed in March 2019 taking 9 weeks in total.
The third Herrenknecht machine, the smallest at only 1000mm diameter, completed one tunnel starting within Espedair Street and tunneling 94m along Barterholm road in just 13 days.
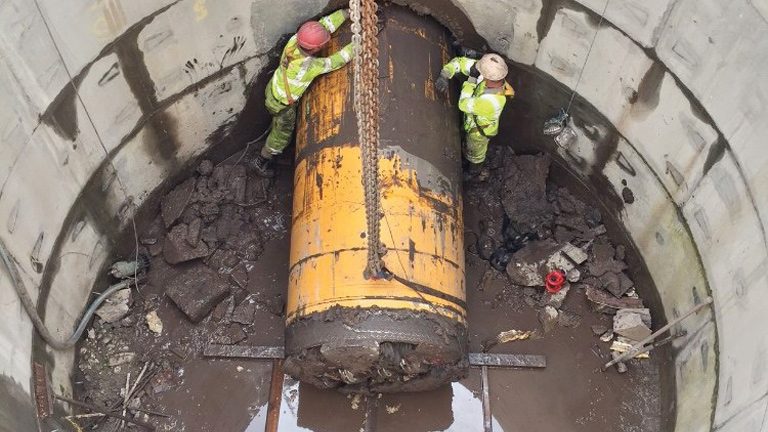
Tunnel breakthrough and extraction of TBM – Courtesy of Scottish Waterr
Paisley Tunnel Project: Supply chain
- Principal design/build contractor: Amey Plc
- Tunnelling contractor: VJ Donegan Civil Engineering Ltd
- Tunnel boring machines: Herrenknecht
- Shaft installation: Northern Tunnelling
- Open cut & precast CSOs: ASG Civil Engineering
- Open cut & CSOs: Bonnars
- 6mm powered screen: Eliquo Hydrok Ltd
- Powered screen commissioning: IDSystems UK
- Precast jacking pipes & shaft segments: Tracey Concrete
- Standard concrete rings & biscuits: Keyline
- Standard concrete rings & biscuits: FP McCann
Progress
Work started on site in October 2016 and the tunneling work commenced in April 2017.
The two new CSOs for the project were both completed by March 2018 and were put into operation at this stage along with the bottom section of the tunneled sewer. Precast concrete CSO chambers were utilised on these elements of the project.
This methodology significantly reduced the construction timescale and minimised the amount of work that was required within the below ground excavations.
The final tunnel was completed in March 2019 with all flows diverted to the new sewers by June 2019. At the time of writing (July 2019) only some minor reinstatement works remain to be completed.

TBM extraction – Courtesy of Scottish Water
Multiple stakeholders
While the project was designed to minimise disruption to residents, businesses and visitors, a scheme of this size in the centre of the town comes with challenges.
The project required interaction with multiple stakeholders including customers, land owners, utility providers, Renfrewshire Council, Network Rail, SEPA and road users.
With work in very close proximity to residential and business customers Scottish Water and Amey kept these stakeholders informed during drop in meetings, regular newsletters and face to face conversations. The project also had close relations with the local school. A name the tunnel machine completion was held with the school, the project team provided relevant teaching to the pupils and volunteering work was undertaken by the project team in the school grounds.
Carefully advanced planning was required at each shaft location to ensure that land access was achieved, utility diversions were completed in advance of the main works and all other affected stakeholders were fully informed.
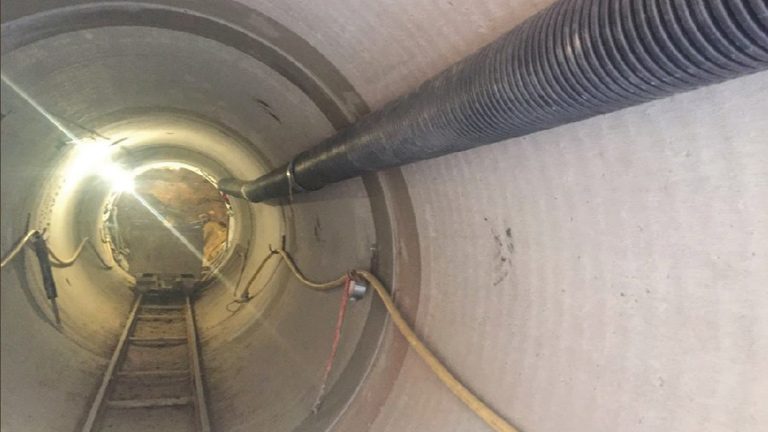
Paisley Espedair Tunnel – Courtesy of Scottish Water
Conclusion
The improvement work in Paisley is part of Scottish Water’s £250m investment in the Greater Glasgow area’s wastewater network, the biggest in more than a century, It will improve river water quality and the natural environment of the River Clyde and its tributaries, enable the area to grow and develop, alleviate sewer flooding and deal with the effects of increased rainfall and climate change.
This major civil engineering project was completed in a busy town centre and residential areas with relatively little disruption to the people of Paisley. This was done by using trenchless techniques, timing of the works and close liaison with the multiple stakeholders affected. The environmental benefits of the project have now been realised and will continue for generations to come.