Perth (Bertha Park) WwTW (2024)
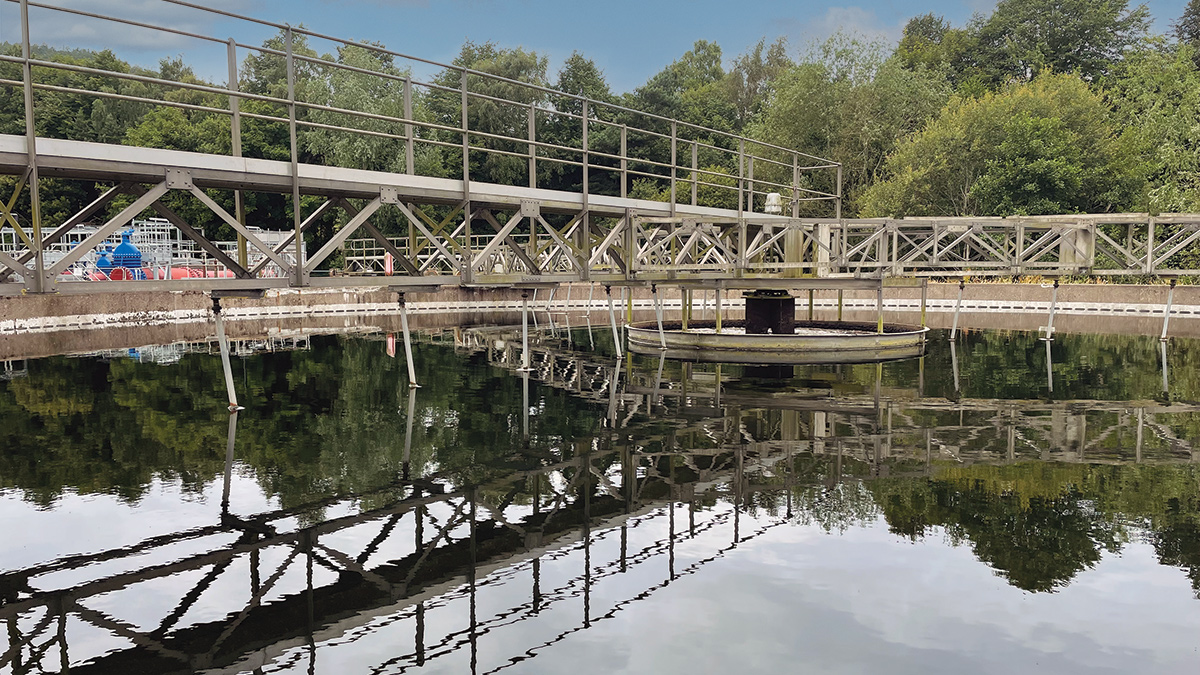
Perth WwTW - Courtesy of ESD
Perth Sewage Treatment Centre (STC) is located to the south-east of Perth city centre, on the banks of the River Tay. The facility treats the wastewater requirements for Perth and its surrounding areas. Perth STC was first constructed in the early 1970s. It was built to help with the growing population and industrial sector within the Perth area. Over the years, the treatment centre has undergone various upgrades and expansions to meet increasing demand and to incorporate advances in treatment technologies. The latest upgrade project is referred to as Perth (Bertha Park) WwTW.
Background & project drivers
The driver behind the latest upgrades and growth to Perth STC stems from a greenfield development project called Bertha Park which will see the construction of more than 3,000 new homes and employment land within the Perth & Kinross Council area. This new development will see the works population equivalent (PE) rise from c.70,000 to c.105,000.
In parallel with the Perth (Bertha Park) WwTW project, the Perth IFAS project is being undertaken by a separate delivery team. This will see the installation of integrated fixed-film activated sludge (IFAS) media into the activated sludge lanes. This project aims to add an IFAS stage to the two combined activated sludge (CAS) lanes at Perth WwTW, converting the final two-thirds of each lane.
The work involves new civil construction, installation of pipework, valves, instrumentation and control systems. New fine bubble diffusers and additional blowers will be installed to meet air requirements, and IFAS media will be added to support growth until 2033.
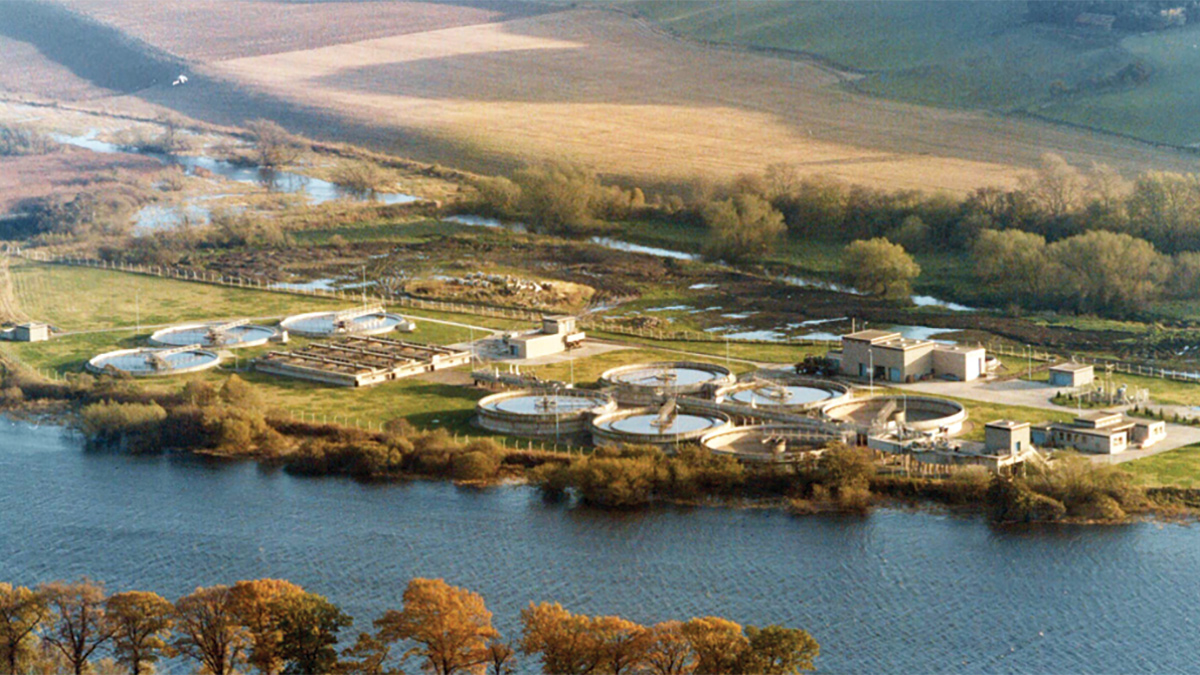
Perth WwTW photographed from Kinnoull Hill Tower in 1971 – Courtesy of Scottish Water
Existing works
Perth WwTW treats sewage from Perth and the surrounding areas. Influent sewage gravitates to the WwTW. Sewage exceeding 570 l/s is diverted to storm storage, while flows under 570 l/s are screened and go through grit removal prior to passing through four primary settlement tanks (PSTs). Flows over 1,100 l/s are spilled at an inlet overflow.
Primary settled sewage then enters a selector tank and is split between two activated sludge plants; the fine bubble diffused air (FBDA) plant, and the surface aeration plant. Mixed liquor from these plants goes to three final settlement tanks before discharge into the River Tay.
Return activated sludge (RAS) is recycled back to the selector tank, and surplus activated sludge (SAS) is co-settled in the primary settlement tanks. Co-settled primary sludge is stored in a sludge storage tank, which also receives imported sludge. The sludge is processed by Veolia who dewater it and transport the sludge cake off-site for disposal.
Overview of scope and process
This screenshot below from ESD’s 3D model highlights the key areas being upgraded within the scope Bertha Park. The blue area highlights the inlet works and PST upgrades, yellow shows the aeration upgrades, red covers the new sludge dewatering area, purple details the new sludge reception No. 2 area, and the orange area is the FSTs and distribution chamber.
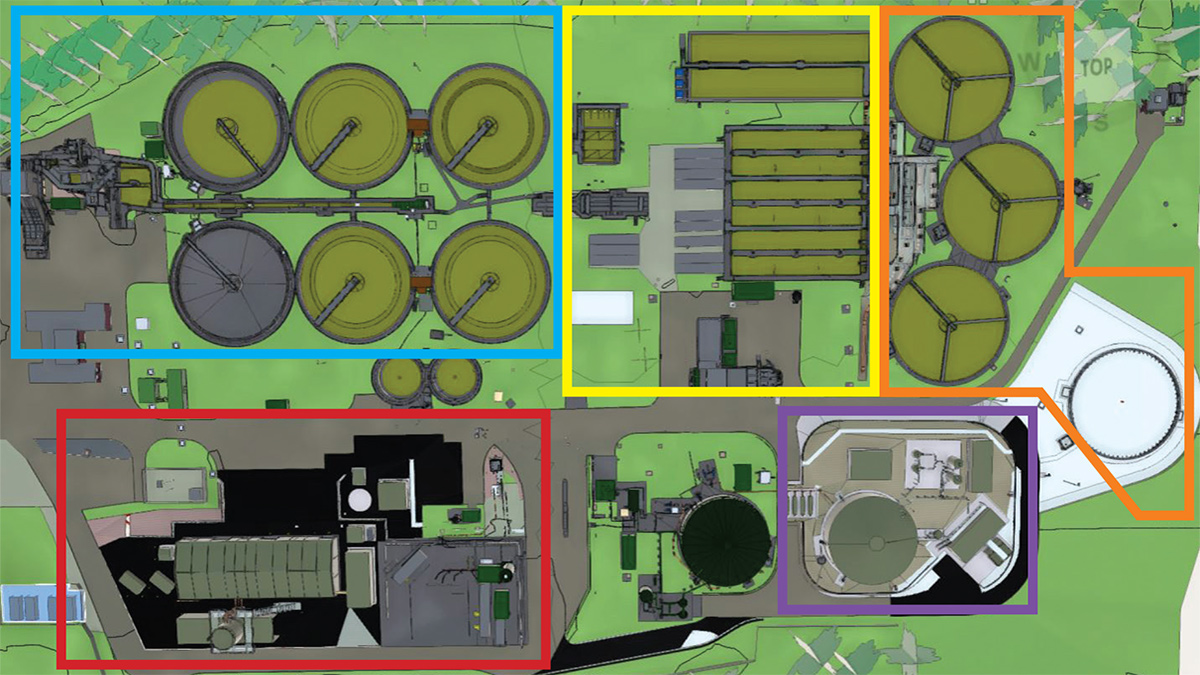
MView model showing birds-eye view of proposed design for Perth (Bertha Park) WwTW – Courtesy of ESD JV
Inlet works (blue)
The inlet works are undergoing extensive repairs and upgrades to numerous areas. Inlet screens 1 and 2 will be replaced with new screens, compactors and launder channels, and a new vehicle turning area will be constructed for skip replacement.
Three new actuators are being installed for the inlet and outlet penstocks associated with screens 1 and 2, and all nine penstocks, including handwheels and frames at the inlet channel and screens, will be refurbished through shot blasting, lubrication and painting. Handrailing and toe boards for the inlet works, storm tanks and PST will be replaced, and two storm tank inlet valves will be actuated.
A new motor control centre (MCC) is also being installed to aid with the upgrades of the inlet works.
Aeration works (yellow)
The IFAS project was completed in June 2024. ESD’s scope is as follows:
- Divert the existing inlet pipe to a new selector tank. The selector tank will allow for future aeration grid installation.
- Decommission and remove the existing SSSO structure.
- Provide a five-way split to five aeration lanes.
In aeration lanes 1, 2 and 3, nine inlet penstocks (three per lane), three outlet penstocks (one per lane), and two cross-connection penstocks will be replaced. Adjustable outlet weirs will be replaced with fixed weir boxes and scum boards.
Six 11kW surface aerators will be upgraded to 15kW, and the MCC5 surface aeration cone feeder compartments will be updated to handle the increased motor kW. Cabling for the upgraded aerators will also be enhanced and electromagnetic current (EMC) filters will be installed within the MCC starter compartments to comply with specifications.
Final settlement tanks 1-3 (existing), distribution chamber and FST4 (new) and modifications to distribution pipework (orange)
In this area, work is also being carried out on the existing final settlement tanks (FSTs). FSTs 1, 2 and 3 will be upgraded with new v-notch weirs, replacement of existing drain-down penstocks, sludge plug valves, drain-down valves, and hydrostatic bellmouths.
Additionally, a fourth FST will be constructed, featuring a new scraper bridge, actuated hydraulic bellmouth, penstock and valves, as well as a connection to the final effluent (FE) outfall chamber.
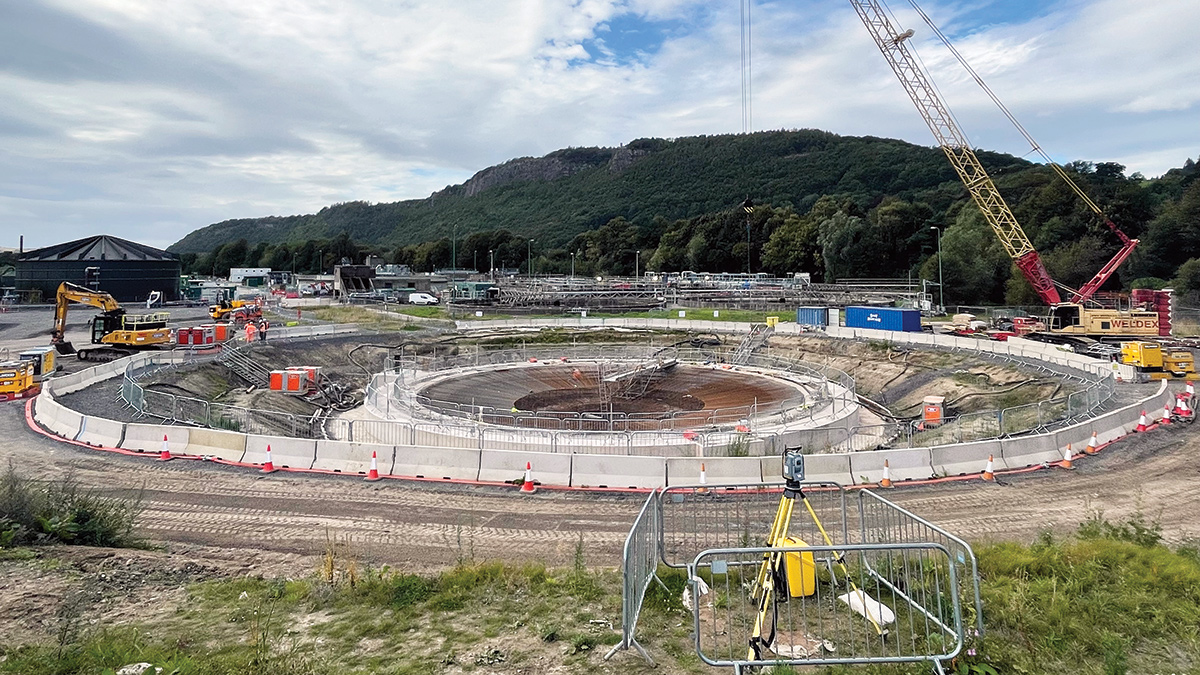
FST4 under construction – Courtesy of ESD
A new distribution system will also be installed. This includes adjustable weirs and flow meters on each outlet to the FSTs. The construction will be staged, incorporating tie-ins to both existing and new pipelines, ultimately ensuring equal distribution among the four FSTs upon completion.
Sludge reception No.2 (purple)
A new sludge reception facility will be constructed. This will be a replica of the existing sludge reception No.1 on site. It will include a screen with grit removal, an enclosed screenings skip, an imported sludge pumping station, a 2205m3 glass coated steel (GCS) sludge tank with mixers and decant valves, new sludge transfer pumps, an odour control system, two tanker delivery points, a road extension for drive-through access and drainage returned to the head of the works.
Sludge dewatering (red)
A new sludge dewatering system will be installed and will operate Monday to Friday, along with polymer makeup and dosing. A sludge cake transfer and trailer loading system will be housed in an enclosed building with odour control and automated doors. A liquor return pumping station with variable speed drive pumps will be installed.
Overall site
There will be a total of four new panels installed (three MCCs and one LVSB) which will support the new works areas detailed above and will be integrated with the existing works.
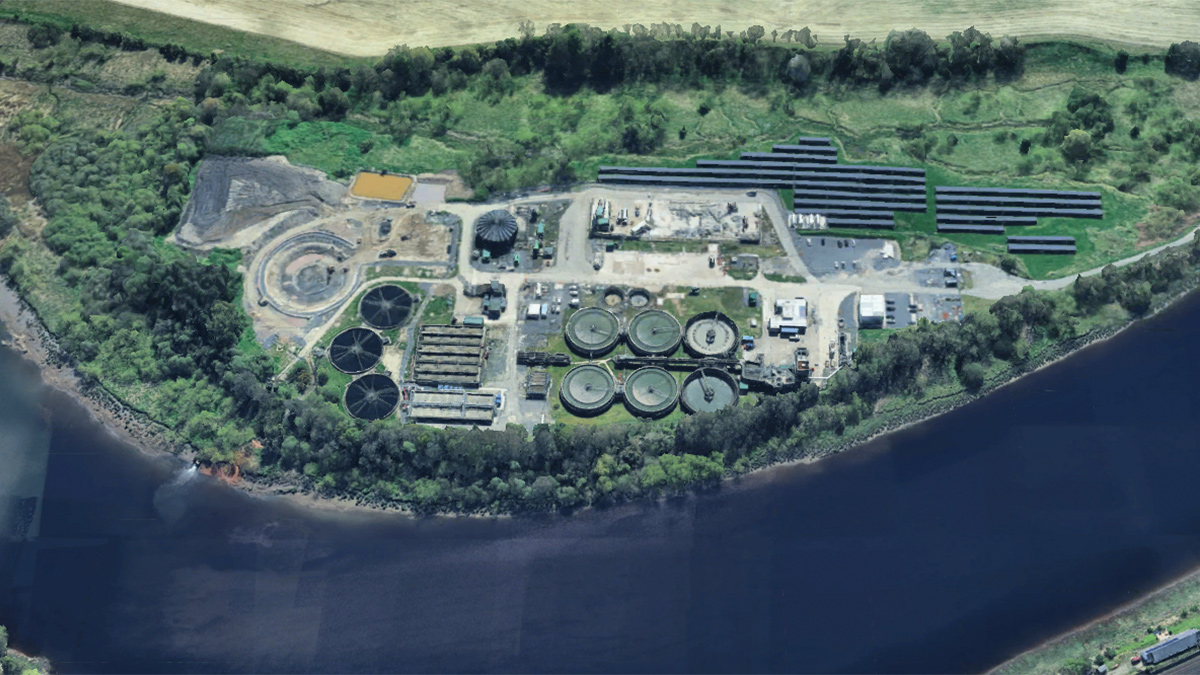
Google Earth image of Perth (Bertha Park) WwTW (2024) – Credit: Google Earth
Perth (Bertha Park) WwTW: Supply chain – key participants
- Client: Scottish Water
- Principal designer & contractor: ESD
- Asbestos surveys & removal: Enviraz
- Material & site testing: Dunelm Geotechnical & Environmental Ltd
- Piling: Van Elle
- Demolition: Central Demolition Ltd
- FST4 design & precast concrete for FST4 & distribution chamber: Shay Murtagh Precast
- FST4 mechanical: Colloide
- MCC/systems integration: BGen Ltd
- Inlet screens: Huber Technology
- Mechanical installation (sludge diversion): Dustacco Engineering Ltd
- Electrical installation: Falcon Engineering
- Electrical & handrailing installation: Reactive Electrical & Mechanical Engineering Services Ltd
- Sludge dewatering plant: Kent Stainless Ltd
- Odour control plant: ERG (Air Pollution Control) Ltd
- Sludge tanks: Reliant
- Sludge screen: CDE Group
- Ductile iron pipework: Saint Gobain PAM UK
- Well-pointing for FST 4: SLD Pumps & Power
- Plant hire & surveying equipment: GAP
Challenges faced
Due to the proximity of the River Tay, the site’s water table is tidal, posing a significant risk to the construction of the new final settlement tank. To address this, well-pointing has been implemented by SLD Pumps & Power to temporarily lower the water table in the area, allowing for the construction of FST4. This process impacts the settlement of existing structures and assets, necessitating continuous monitoring to prevent significant movement or damage. This challenge will also arise in other areas of the site during deep excavations.
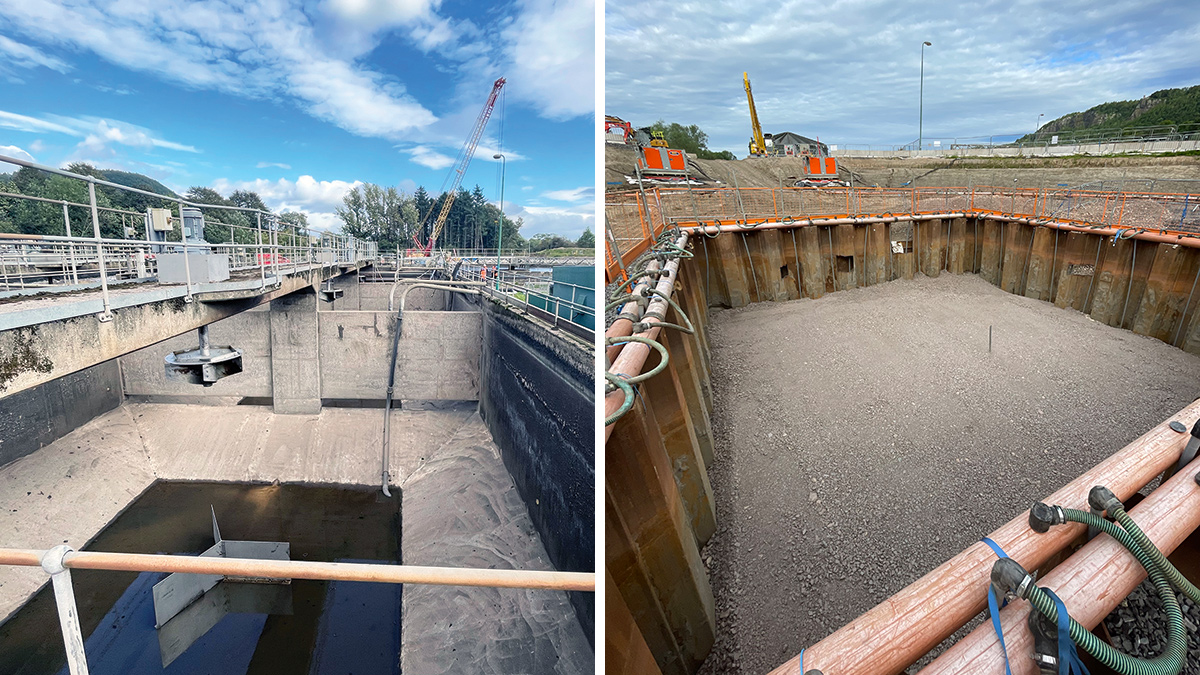
(left) Aeration lanes and (right) well-pointing to aid the construction of FST4 – Courtesy of ESD
Dewatering is being managed under GBR15 controls, which is valid for six months. However, since this period is likely to extend, a complex license has subsequently been applied for from SEPA to ensure ongoing compliance.
The presence of multiple principal contractors on site requires meticulous health & safety customer data management (CDM). Regular communication is crucial to ensure both contractors can work safely without interfering with each other.
Some access delays have occurred due to commissioning issues with the separate IFAS project, but ESD is working collaboratively with the client to mitigate any delays where possible.
Additionally, areas of the site have been contaminated with asbestos-containing materials and invasive species. The project team promptly notified the relevant authorities and sought guidance on appropriate remediation measures.
MView
The ESD design was developed using Revit, a 3D modelling package, which was shared in MView, a cloud-based BIM management and collaboration product.
The 3D model has been an integral part of the project lifecycle from the early stages to developing detailed design in collaboration with stakeholders within Scottish Water. It has also helped create smoother discussions between the site team and the design team during the construction phase.
The 3D model provides much detail and clarity not only to the new works but also the existing works including underground pipes and services. It allows for a much more in-depth discussion to be had around installation and construction of new pipework which reduces the risk of errors, delays and miscommunication.
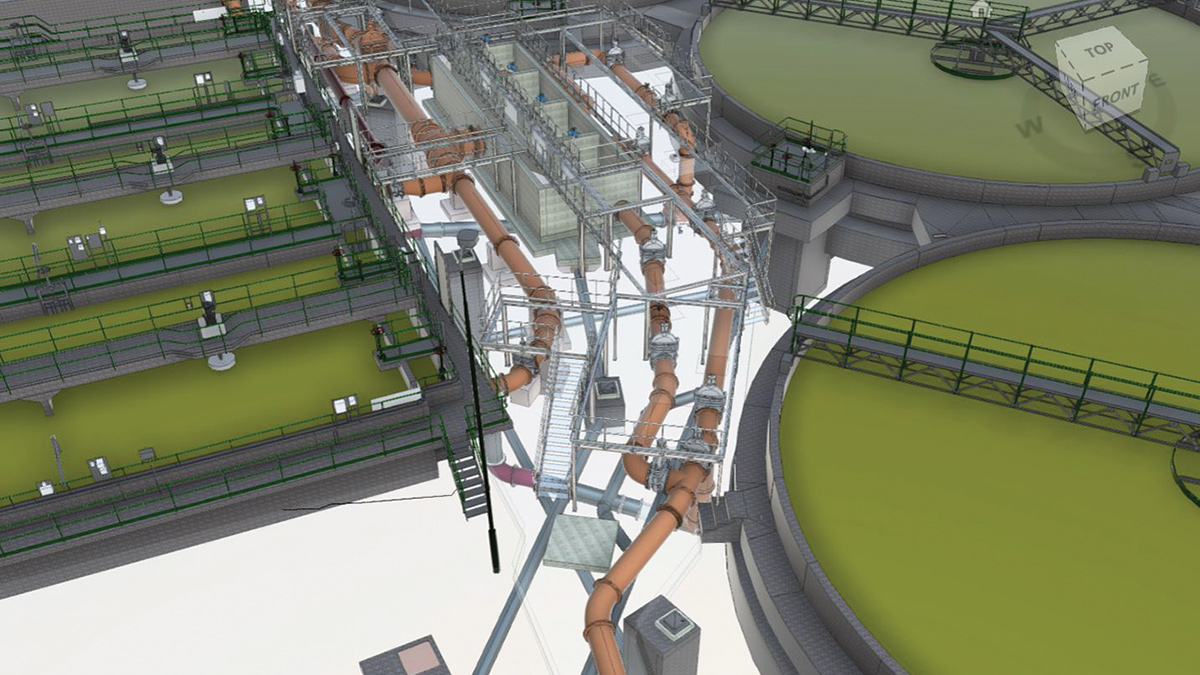
MView close up of existing FSTs deep tie-ins – Courtesy of ESD
Current status
Despite its challenges, the project is progressing well. Since the start of work in mid-2023, ESD has demolished two sizeable, abandoned structures and rerouted the basement pumps to a new buffer tank and valve arrangement. The formwork, reinforcement and concrete work for FST4 are set to begin shortly.
Additionally, work has commenced on capital maintenance mechanical packages. We are preparing to intensify construction with a challenging programme focused on delivering the aforementioned areas.
ESD will continue installing large-diameter pipework to the FST distribution chamber, including any necessary tie-ins. These efforts will also include improving and replacing elements of the aeration lanes and initiating work on the sludge reception area and sludge dewatering building.
The Perth (Bertha Park) WwTW project management team is utilising Fieldview to record progress on site and to carry out daily, weekly or specified check sheets related to safety, health, environment and quality. This is a positive step forward.
The wider project team is actively engaging the supply chain through the procurement process for various workstreams and activities planned through to the anticipated project completion in August 2026.
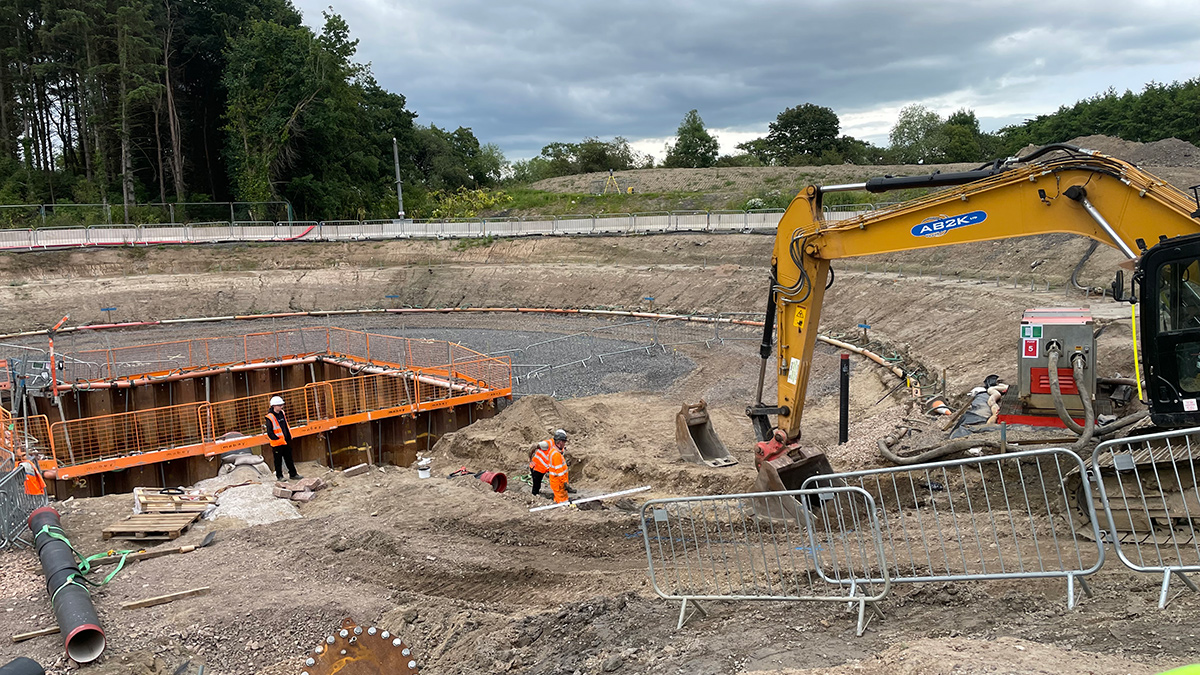
FST4 under construction - Courtesy of ESD