Springwell Service Reservoir (2024)
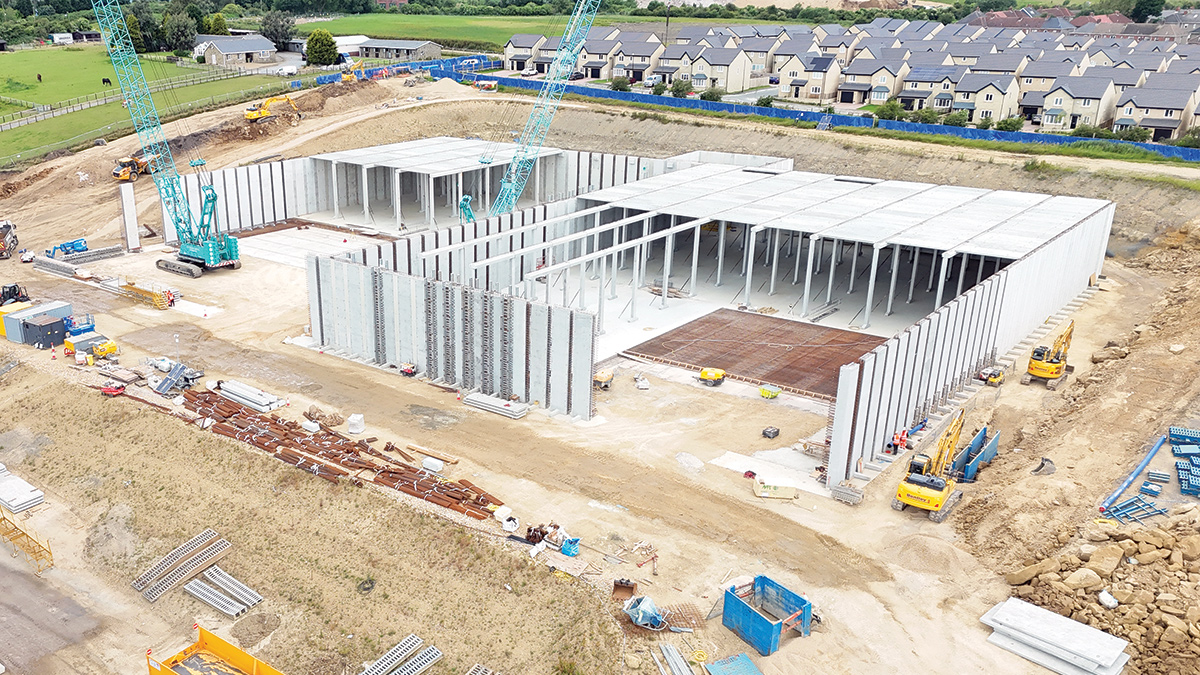
Springwell Service Reservoir construction progress (June 2024) - Courtesy of Mott MacDonald Bentley
Northumbrian Water are constructing a new 43 ML service reservoir at Springwell Village near Washington, Tyne and Wear, along with associated pipework and connections to the Derwent and Carr Hill mains. The project will supply water to the village and support the wider Wearside and South Tyneside areas, improving water storage and benefitting around 50,000 properties in South Tyneside, and supporting resilience for a further 200,000 properties in South Tyneside and Wearside. Mott MacDonald Bentley was appointed as principal designer and contractor for the £26m project which started on site in June 2023 and is due for completion by March 2025.
Project details
The twin cell reservoir is 100m by 75m x 9m tall with a storage capacity of 43 ML. The construction of the reservoir is semi-precast, utilising precast wall panels with an in situ concrete base, in situ infills between the walls, precast columns and roof planks and an in situ screed placed over the top of them. The site is comprised of a sloping grassland field with a fall of 1 in 10 from north to south.

Springwell Service Reservoir 3D model – Courtesy of MMB
Planning & environment
The new service reservoir and pipework was subject to planning and full statutory Environmental Impact Assessment. Environmental assessment and planning submission was undertaken by others during the definition design stage. Environmental constraints and any required mitigation were passed to MMB for consenting and implementation. This included the discharge of numerous planning conditions from local Councils, applications for: protected species licences (including great crested newt); prior consent under Section 61 of the Control of Pollution Act, and Scheduled Monument Consent from Historic England for tunnelling work under the Bowes Railway.
Landscaping upon completion of works will implement a non-statutory biodiversity net gain on the reservoir site through planting other neutral grassland using a locally sourced seed mix on the reservoir banks and surrounding land, the reinstatement/gapping up and planting of new species rich hedgerow, and the planting of new native trees within the site. A retention basin will be constructed within the site boundary to manage runoff.
Design strategy
Once appointed, MMB began to consult with the pre-construction designers at WSP and the client to further develop and detail design the structure and pipe network. MMB worked with FLI Precast at an early stage of the development to engage with them to design a semi-precast solution for the main structure, utilising lessons learned, and knowledge gained by both organisations from constructing multiple service reservoirs in this manner.

Springwell Reservoir base construction – Courtesy of MMB
From the beginning of their appointment, MMB has engaged with all stakeholders to develop solutions through collaborative working and to ensure that water quality standards are met throughout the construction process. MMB has particularly engaged with WSP and NWG, who have had an on-site presence throughout the works and have been able to identify opportunities within the design for cost and carbon effective design amendments, with shorter approval windows due to the collaborative nature of the design.
One opportunity highlighted by the design team was the proposal to remove the reservoir underdrainage from the scope. By studying available guidance, in particular the UK Water Industry Research Limited, Treated Water Storage Assets: Good Practice for Operation and Management, Version 2 report.
Underdrainage is more prevalent on structures that are not considered monolithic. Due to the construction sequencing and the type of jointing techniques considered, with no movement joints along with the required fall and depth of the drainage system due to project constraints, reservoir fall direction, the lack of presence of groundwater and subsequent uplift concerns, the underdrainage system would not have been beneficial to the structure. This was presented at an early stage to the Qualified Civil Engineer appointed to oversee the structural design and was deemed surplus to requirement and omitted.
The use of BIM360 as a shared working environment allowed the client, their consultants, MMB and their subcontractors to collaboratively work on drawings, showing real time changes to the design in 3D and allowing quicker design discussions, with the aim to shorten the design program and keep the site program on target. This worked particularly well when MMB re-designed the valve house layout and sizing using virtual reality.

Springwell valve house – Courtesy of MMB
It was noted on receipt of the outline design that the valve house was not sufficiently designed for operation and maintenance of the assets housed within it. Therefore, MMB had to increase the size of the building itself, change pipework arrangements to ensure adequate access to assets. To make this process as efficient as possible the 3D model was used in a VR headset to aid meetings and acceptances with the client. This was better than using 2D drawings as the team could all see in real space what the proposals were, and pick up any issues to be addressed.
Due to constraints regarding planning consents, works on the project began in earnest in May 2023, whilst the detail design of the reservoir was still ongoing, leading to a truly ‘design and build’ approach on the scheme. This approach sharpened attention on the project’s critical path and detail design works proceeded with construction programme in mind.
Significant design works were conducted in relation to the geotechnical operation, which required approximately 55,000m3 of sandstone and superficial materials to be excavated. The excavated materials will be reprocessed at a local quarry to become the embankment backfills, reducing waste.
Geotechnical & earthworks
One of the initial challenges with the construction of the scheme was the variance in geotechnical properties of the founding material. Covering approximately 80% of the reservoir footprint is an area of sandstone, and the remaining 20% an area of superficial materials, comprising weathered sandstone and granular glacial till to the south side of the reservoir.
Due to this variance, there was a significant risk of differential settlement of the base, which was highlighted during the definition phase. Initial settlement calculations led to large differential settlements which would have created intolerable stresses within the structure, so a ground improvement solution was sought. The solution adopted was to use a large temporary berm of material, comprising of the excavated material for the reservoir, to surcharge the softer material to the south. This berm of material (measuring approximately 8m tall, generating greater bearing pressures than the final structure would when filled to maximum capacity) was constructed, along with monitoring points using settlement gauges within this material, to drive out the anticipated settlement.

Springwell settlement bund – Courtesy of MMB
The monitoring results were analysed showing that the settlement was achieved quickly, with a significant tail off from any additional settlement recorded. The trendline of the settlement indicated granular properties over more cohesive, which confirmed that rebound of the material was unlikely. The berm was removed and then an assessment of rebound of the material was made. Initial programmed time for this berm was significantly longer than eventually needed and due to the close monitoring of this settlement it resulted in some programmed time savings to the works.
Precast construction & value added
The use of the precast walls reduced the scale of wall reinforcement fixing reducing both a risk of the reinforcement cages moving during the temporary construction phases and the time duration of works at height for setting the reinforcement and pouring operations, making construction safer. The reduction in concrete pours reduced the number of deliveries to site and the number of concreting operatives at any one point.
Off-site production of the walls aided in finish control of the concrete and allowed for higher accuracy of the placement of pipe wall couplers and setting in submarine door frames with less likelihood of cracking around these openings.
Precast wall panels installation is quicker than traditional wall pour construction, which has aided the construction programme, however this has led to a significant number (231) of wall infill pours required. As these locations are a potential area for leakage, good curing and placing procedures were required. The infill pours are tall and thin (approximately 8.5m tall and nominally 500mm to 1m wide) and significant care was given for the placement using tremie pipes and rate of concrete pour, with considerable care on concrete delivery times taken. Bar spacing within the infill was designed with a view of construction procedures, ensuring adequate bar spacing for effective concrete compaction via vibratory pokers.

(left) Wall panels and (right) wall infills – Courtesy of MMB
SMR Projects Ltd supplied a Xypex additive for the concrete mix, which reacts with water and forms crystalline structures closing small voids/cracks that may occur from various thermal effects. Controlled permeability formwork was used to densify the surface of the concrete by limiting evaporation of water from the concrete surface. This increases resistance to soft water attack which is prevalent in this area of England. An impermeable sheet was also used over the infill following striking of the formwork for the curing process to prevent the concrete from drying out too quickly, again to reduce early cracking of the concrete surface creating a higher quality product.
From an operational perspective, using submarine doors to access the reservoir cells through the valve house allowed MMB to design out a requirement for access directly through the reservoir roof, thus reducing the number of openings in the roof helping to prevent contamination ingress to the reservoir via additional roof hatches and reducing fall from height risks associated with such access.
A further saving was made during design by ensuring that the valve house was capable of housing the electrical and signal board components needed for monitoring of flows and operation of valves. This removed the need for an external electrical control building that was considered in the planning application.
Early planning & stakeholder engagement
The Springwell Project, located near a new housing estate close to the village, has led the team to focus on early engagement with local stakeholders to minimise disruption, including road closures, bus and footpath diversions, construction traffic, and the impact on local businesses, as well as noise and dust concerns. To ensure the community feels informed and involved, MMB have participated in meetings and workshops with residents to provide project updates, get local input and answer questions.
The approach to community engagement has also included regular drop-in sessions, quarterly information events, newsletters, and site tours to keep residents up to date throughout the project. These initiatives have helped build a strong, positive relationship with the community, reflecting MMB’s commitment to minimising disruption and improving the local environment.
There has been significant emphasis on supporting education, particularly in STEM. By partnering with Newcastle College, we’ve organised site visits and provided two students with work experience, while local primary schools have been engaged through activities such as site safety aiming to spark interest in engineering and construction. Beyond education, MMB have collaborated with local organisations and the project’s subcontractors have also contributed to the community by installing a reading area at Springwell Village Primary School, demonstrating how MMB have harnessed resources and partnerships to deliver meaningful improvements.

Springwell Reservoir under construction – Courtesy of MMB
Springwell Reservoir: Supply chain – key participants
- Client: Northumbrian Water
- Main designer & contractor: MMB
- Client’s designer: WSP
- Earthworks: Thompsons of Prudhoe
- Excavations: Cheetham Hill Construction Ltd
- Soils material testing: Dunelm Geotechnical & Environment
- FRC: Cidon Group
- Precast design & install: FLI Precast Solutions Ltd
- Precast roof panels design & supply: Stresslite Precast
- Xypex concrete waterproofing chemical additives: SMR Projects Ltd (UK Xypex Distributor)
- Pipeline cleaning & dechlorination: Pipeline Testing Consultants Ltd
- Tunnelling works: Active Tunnelling Ltd
- Directional drilling: Ken Rodney Construction
- Underpressure connections: Power Technologies Services Ltd
- Connections to NWL network: EJ Peak Technology
- Pipe welding: Serimax Ltd
- Pipework & fittings: UTS Engineering Ltd
- Pipework & fittings: Electrosteel Castings (UK) Ltd
- Pipework & fittings: George Green (Keighley) Ltd
- Pipe brackets: Deritend Group Ltd
- Metalwork: JHT Fabrications
- Fencing: Middleton Forge Ltd
Conclusions
The reservoir is part of a broader package of works to improve the resilience of Northumbrian Water’s clean water network and the reservoir aspect of the scheme is approximately 70% complete at the time of writing (August 2024).

Springwell Reservoir columns and roof – Courtesy of MMB
Through MMB’s commitment to protecting the environment and social engagement the project has limited disruption where possible and aimed to build a stronger connection with the local community.
Direct engagement with the client during the enabling works and beyond has expedited the programme of works, allowing longer lead items to be procured earlier and aid in achieving this challenging programme.
The use of a large berm of excavated material during the enabling works for the scheme has induced settlement within the ground prior to the structure installation, thus reducing stresses on the structure and allowing a more efficient design to be made.
Engaging with the precast concrete panel designer at early stages of the construction programme allowed construction efficiencies to be achieved with respect to structural arrangements and thickness, reducing embedded carbon for the structure. Through the team’s collective experiences of building modern service reservoirs, MMB have endeavoured to create a structure which should be less prone to leakage. Further works and testing are ongoing to realise this so far successful project.

Site visit (July 2024) - Courtesy of MMB