Tideway Central – Chelsea Embankment Foreshore (2020)
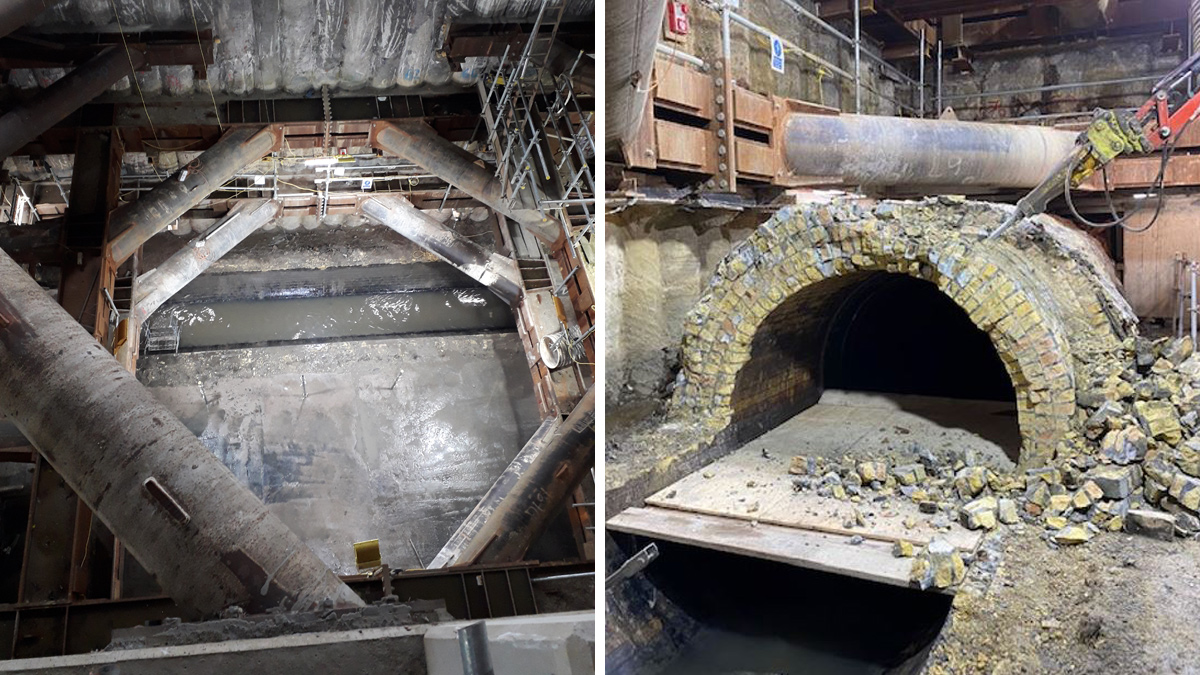
Leakage liner and sewer brick removal - Courtesy of FLO JV
The Chelsea Embankment Foreshore (CHEEF) site is one of the eight main sites in the Central Section of the Thames Tideway Tunnel. The site is located within the Royal Borough of Kensington and Chelsea and will allow for the diversion to the main tunnel of approximately 280,000m3 of sewage that currently discharges into the river. The permanent works at CHEEF will connect the current Ranelagh Combined Sewer Overflow (CSO) and Low Level No.1 (LL1) Sewer with the Thames Tideway Tunnel. This work has been contracted to a joint venture between Ferrovial Agroman and Laing O’Rourke (FLO JV).
Outline of works
During storms, when large amounts of rain get into the sewers, flows may arrive more quickly than they can be collected and processed. CSOs prevent the sewerage system becoming overloaded and potentially backing up during these storm events by discharging into the river. The Ranelagh CSO will discharge into the new CSO shaft which will then flow into the main tunnel. An overflow weir chamber will be constructed to capture storm flows in LL1 sewer which will then also be diverted to the CSO shaft via the connection culvert.
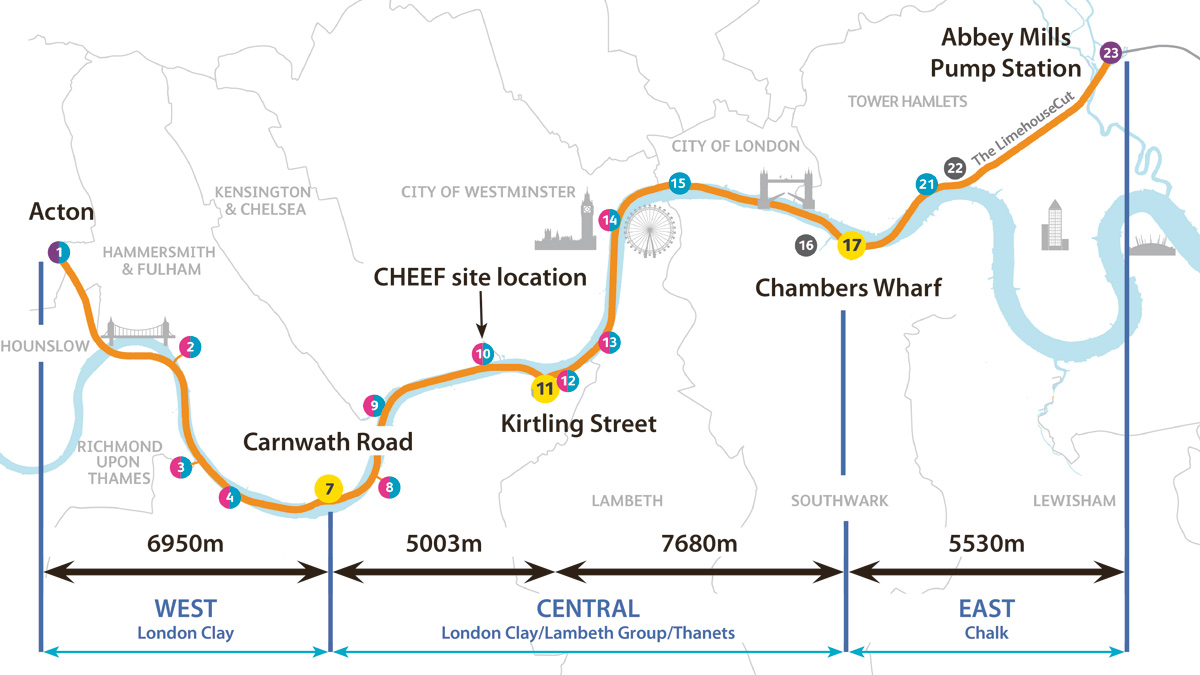
CHEEF location and Thames Tideway Tunnel overview – Courtesy FLO JV
The purpose of this report is to describe the techniques employed to enable the LL1 Sewer to remain operational while the overflow weir chamber is being constructed. The report will also discuss the data analysis methods and monitoring techniques that were required to be carried out to ensure that works could progress safely. The chamber is constructed using secant piles and is excavated to a depth of 22m supported by temporary steel props.
LL1 sewer is required to remain operational throughout the course of the construction of the chamber. To allow this, a temporary leakage liner was designed to strengthen the sewer to allow for excavation to the sewer elevation and a flume was designed to provide a conduit for the LL1 flows when excavating the rest of the chamber.
Temporary leakage liner
Prior to commencing the excavation works, a temporary leakage liner was installed in LL1 Sewer. The leakage liner was installed to prevent rupture during storm events and to protect LL1 from predicted ground settlement. Excavating the chamber to sewer level would remove the overburden pressure on the sewer and therefore the sewer would require strengthening to resist internal pressures.
The leakage liner comprised an 18m long structural cage which was fixed to the intrados of the sewer. 3mm thick steel plates were then fixed to the cage before a rubber liner was secured to this by a series of adjustable inner steel restraint bands.
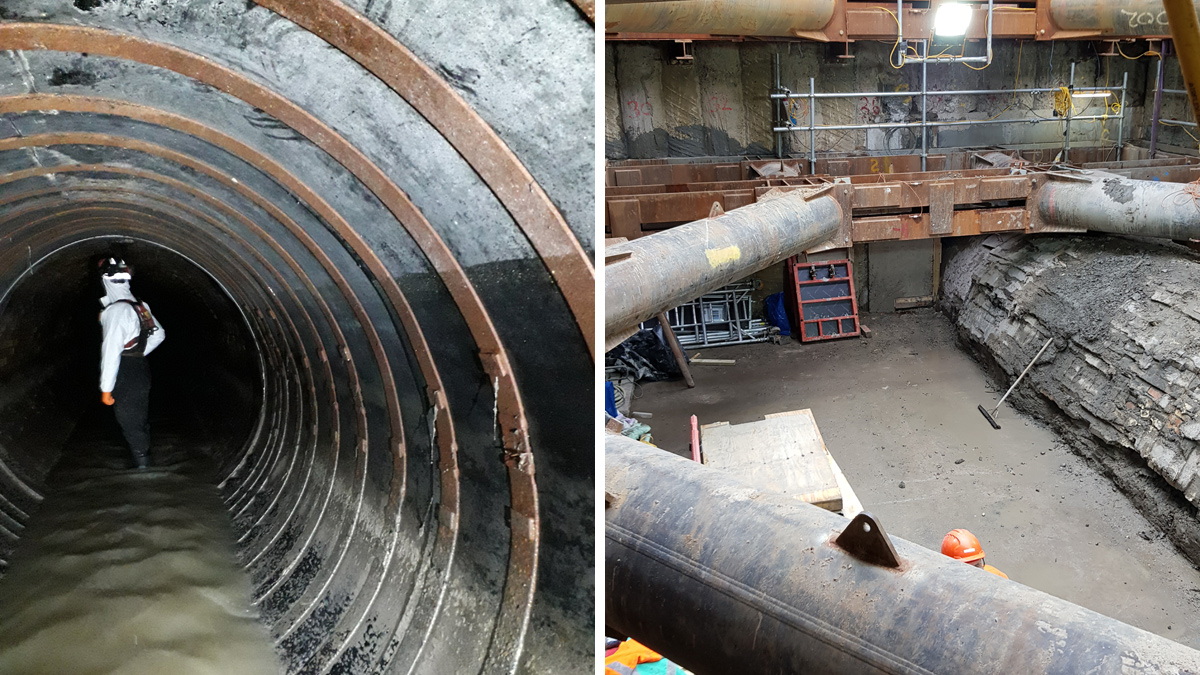
(left) Inspection of leakage liner in LL1 sewer and (right) LL1 sewer exposed prior to brick removal – Courtesy of FLO JV
Leakage liner design issues
The leakage liner had originally been designed to withstand a head of water of 4.056m above the invert level. This figure had been considered based on hydraulic modelling of the flows inside LL1 sewer. However, after installation, there were further discussions with all stakeholders, and it was deemed that the liner should have been designed to consider a 1 in 30 year storm event; which correlates to a head of water of 9.3m above the invert level which exceeded the capacity of the leakage liner. It was not possible to strengthen the liner from inside the sewer; therefore, an observational method was used to monitor the flows so as to continue the excavation works.
Observational method – sewer level monitoring
Thames Water supplied monitoring data of LL1 Sewer over a period of 12 months which gave the head of water readings in the sewer at 2-minute intervals. As there was no clear pattern to the data sets, historical rainfall records were gathered and analysed in 10-minute, 1 hour and daily intervals. The two data sets were then compared which showed a correlation between the maximum flows in the sewer and the maximum 1-hour rainfall per day. The results showed that there was little increase on the head of water in the sewer given a full day of consistent rain as the network could cope with the gradual demand. A high 1-hour rainfall such as a storm event, however, would result in sudden increased demand on the network and result in an increase in the head of water level. The correlation trendline that was calculated from the data analysis is shown in the graph below.
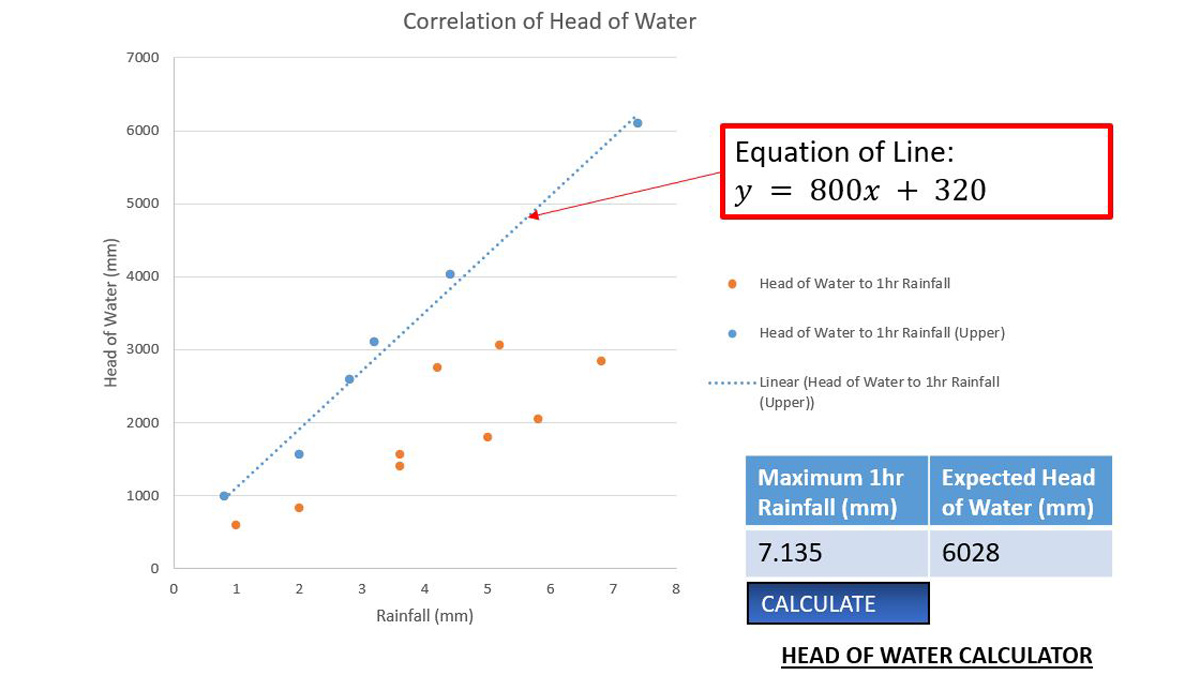
Correlation of rainfall and head of water data – Courtesy of FLO JV
After calculating the maximum allowable 1-hour rainfall of 7.135mm, which corresponded to an expected 6.028m head of water, a 2 week lookahead of hourly rainfall was set up to ensure that this value would not be breached. A Go/No-Go system was developed where the weather forecast and current conditions dictated whether the works could continue which allowed excavation to commence. If rainfall was predicted to exceed 7.135mm per hour, sand would be placed in the excavation as a temporary overburden to provide sufficient ballast to ensure that the sewer remained structurally sound in the case of a 1 in 30 year storm event.
The innovative data analysis approach satisfied both FLO JV and Thames Water that the progress of works could continue based on this observational method. The forecasting of the 1-hour rainfall was key in enabling the completion of this section of works.
Sewer brick removal
After excavating and exposing the crown of the sewer, the excavation could continue to the springer (centreline) of the sewer. At this point, a penetration was cut in the leakage liner and bricks which meant that there was no risk of rupture as the liner was then redundant as the flows could freely enter the chamber. Once the bricks had been completely removed, the flume could then be installed.
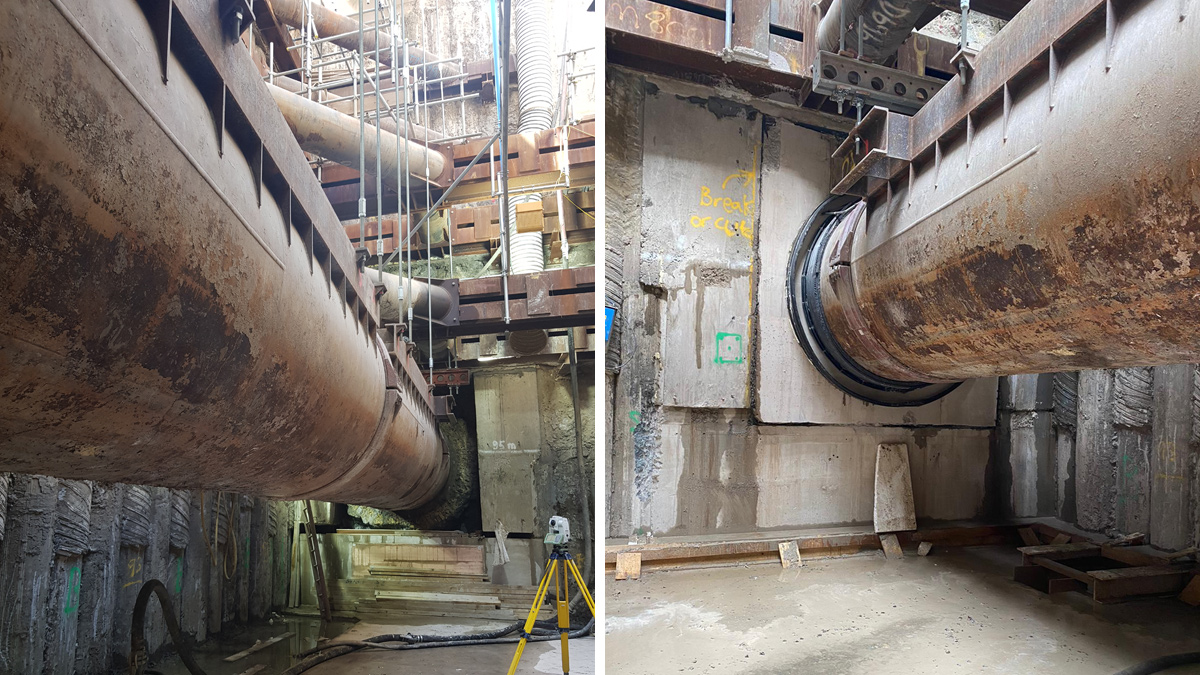
(left) Flume installation complete and excavation continuing and (right) RC collar poured between chamber and flume – Courtesy of FLO JV
The leakage liner, sewer removal and flume installation works were carried out with inflatable lampe stoppers in place upstream in the sewer which reduce flows downstream. The reduced flows in LL1 allow works to be carried out and ensure the safety of the operatives. The lampe stoppers are made of rubber and are inflated in the sewer.
Prior to each shift and throughout the works there was close communication with Thames Water who granted consent to proceed with works and ensure the sewer network could cope with the diversion and the additional flows elsewhere in the system.
Flume installation
The steel flume is designed to be installed inside the sewer, extending 6.5m either side further than the excavation itself. The flume comprises of four separate steel circular sections which are connected by Victaulic couplers at the 3 (No.) joint positions. The coupler clamps together to ensure connectivity between sections before a Trelleborg seal is installed inside each joint to provide secondary leakage protection.
Support beams spanning the excavation on the capping beam support tie rods which connect to the central sections of the flume suspending the sections to allow for excavation. In designing the flume sections, consideration had to be given to ensure that their weight could counteract the surge forces in the sewer and the stresses on the section as a result of the head of water pressure.
To install the flume sections, the separate sections were lifted between the props and located on rails so that they could be moved into position using tirfors.
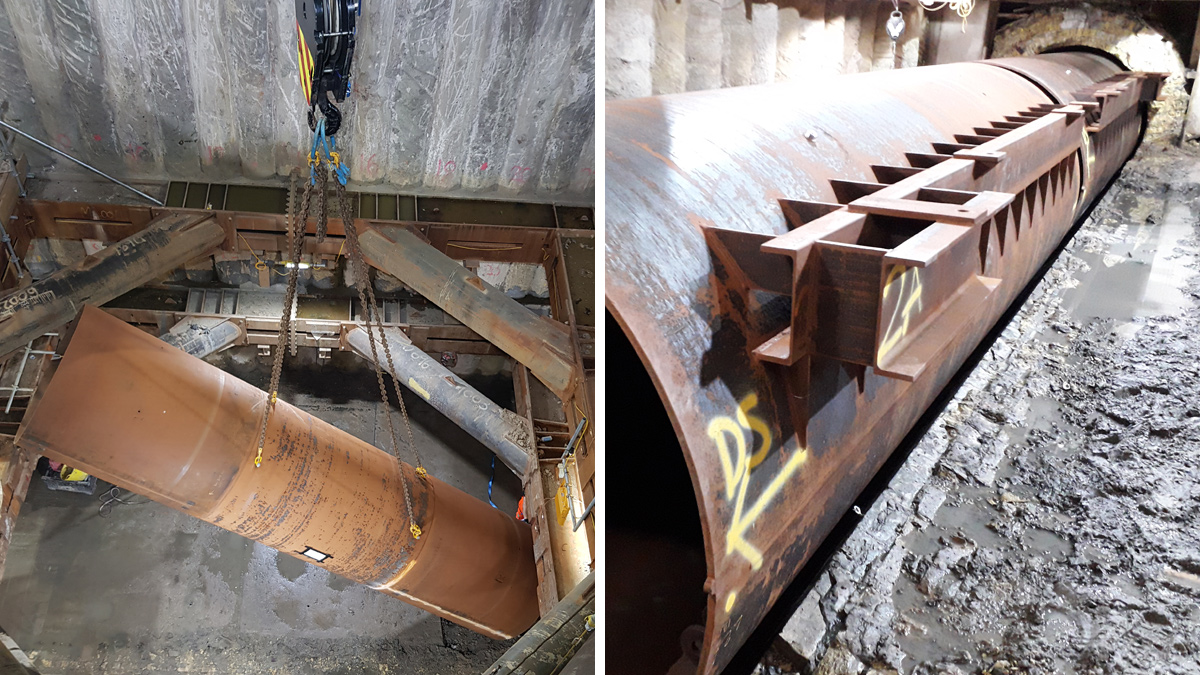
Lifting and moving flume sections into position – Courtesy of FLO JV
Once all sections were in position, the Victaulic couplers were installed between the sections to create one conduit. Once the grout seals were installed at either end of the external flumes this created a watertight seal and meant that there were no flows which could enter inside LL1. The support beams were then landed and the tie rods dropped into position. At this stage, a clash was detected between the rod position and the temporary steel flumes due to an offset in the actual sewer position compared to the design. The temporary works design allowed the rods to bypass the props.
With the tie rods in position, the sway bracing could be installed to the south secant piles. Once the tie rods were tensioned and immediately prior to excavation, baseline readings were recorded for the shape accel array (SAA) monitoring system. The SAA system measures deflections in the flume as a result of the construction process and is installed across the length of the flume. To control the risk of joints opening, an inspection and monitoring regime was developed with the designers and the monitoring team. Trigger levels were agreed to understand any actions that would be required to carry out as a result of significant movement between the couplers. With the baseline confirmed, the excavation could then commence to dig beneath the flume which would be fully supported and transferring all flows in LL1 through the overflow weir chamber.
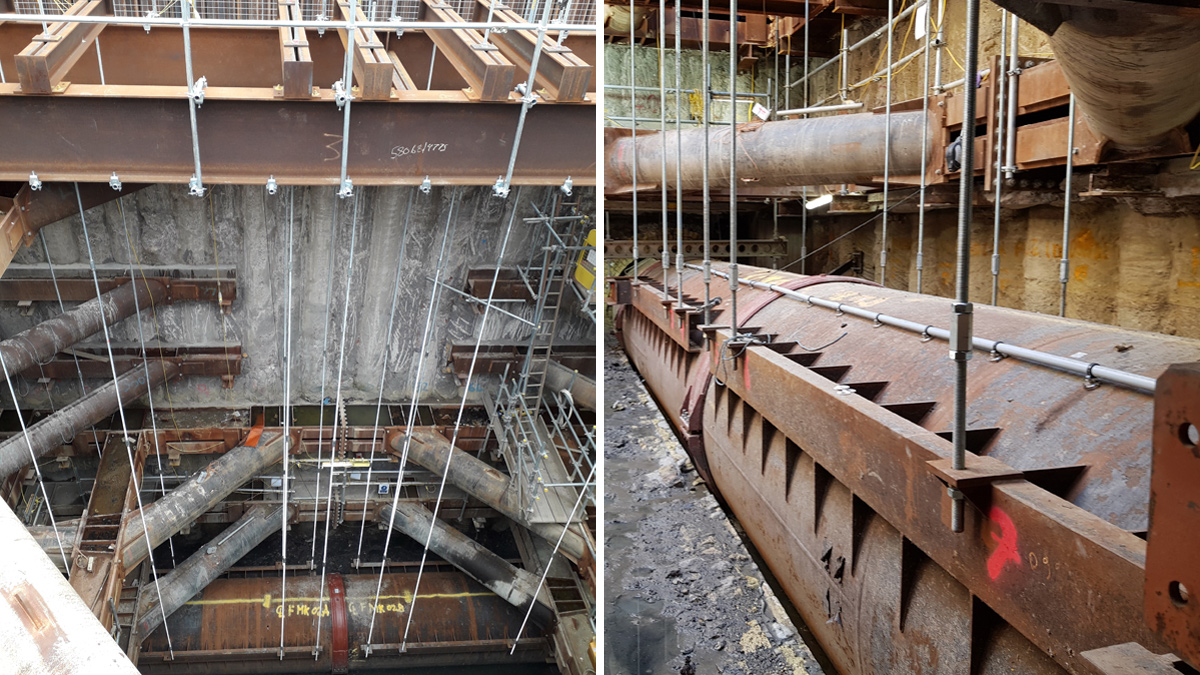
Flume supported by tie rods and bridge deck and (right) tie rods in position to tension – Courtesy of FLO JV
Chelsea Embankment Foreshore – Thames Tideway Tunnel Central Section: Supply chain – key participants
- Main contractor: FLO JV
- Sub-contractor: McAllister Group
- Temporary works consultant: Robert Walpole & Partners
- Permanent works consultant: AECOM
Summary
The design and installation of the temporary flume allows for the excavation and permanent works construction to be carried out in the overflow weir chamber while LL1 Sewer remains operational with no impact to the network. It was important that there was no structural damage to the LL1 Sewer as a result of the excavation and installation of the flume.
Throughout the design and installation there was a requirement for FLO JV to work with Thames Water, who issued consent for the works, to provide a design that ensured the risk of damage to the asset was mitigated. The installation of the flume was successful and has allowed the further excavation and permanent works to be carried out. At the end of the project, once the chamber has been fully constructed, the flume will then be removed which will mean that flows will then run through the excavation, discharging during storm events to the main tunnel, thus reducing pollution to the river.