Evergreen Water Solutions
Volute Disc Press – Nigg WwTW (2017)
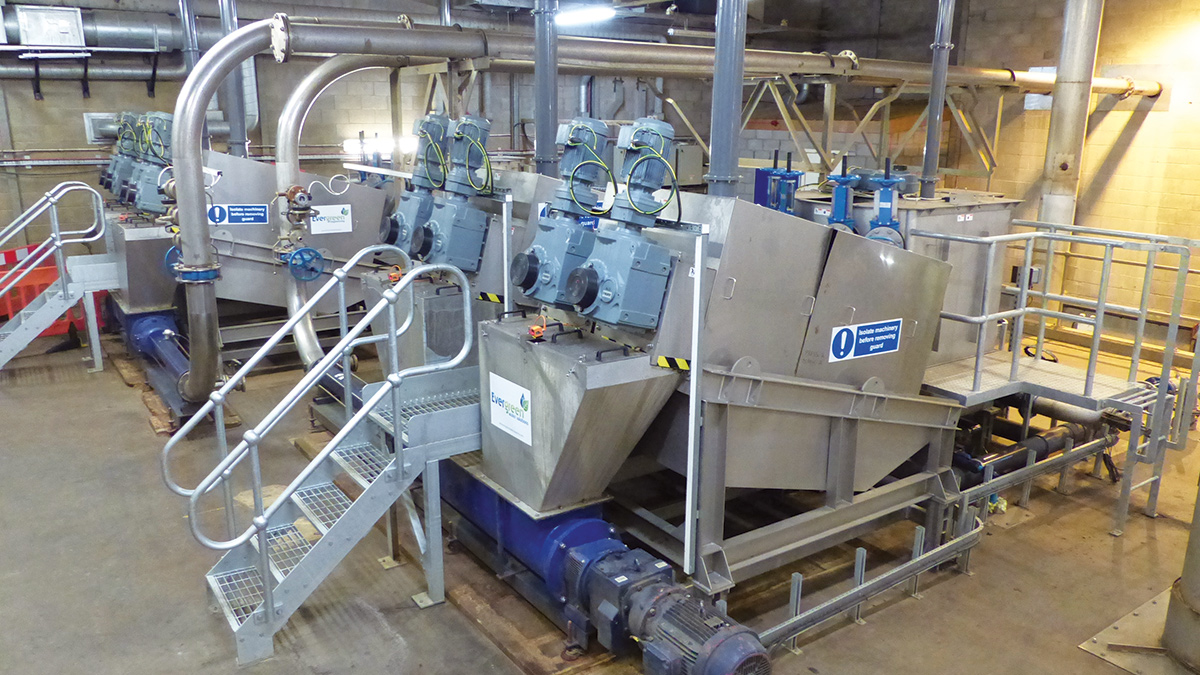
Kelda Water Services Grampian (KWS Grampian) has a 28 year design, build, finance and operate contract with Scottish Water to operate and maintain four wastewater treatment plants serving the north east of Scotland; two sites in Aberdeen (Nigg and Persley) and two sites to the north (Peterhead and Fraserburgh). In addition to treating wastewater, KWS Grampian operate sludge treatment facilities able to receive imported sludge and liquid wastes. Nigg WwTW located to the south east of the City of Aberdeen on the shore of Nigg Bay serves a PE of 250,000. The works was built to provide full treatment to a flow of 1600 l/s and achieve the requirements of the Urban Waste Water Treatment Directive (BOD: 25mg/l and COD: 125mg/l).
Nigg WwTW treatment process
A pumping station lifts the flow up from the preliminary treatment stages whence it gravitates through the primary and secondary treatment stages prior to discharge into the North Sea. Due to the compact nature of the site primary treatment is provided by lamella settlement. Lamella settlement uses inclined plates or tubes to provide high settling area in a small plan area; flow travels up these plates or tubes with the solids ‘falling’ onto the inclined surface and falling into the hopper below. These solids are subsequently removed from the hopper and at Nigg WwTW pumped to the sludge treatment centre (STC).
Secondary treatment is provided by a two-stage biological aerated flooded filter (BAFF). The BAFF utilises a down-flow plastic open-structured media, followed by an up-flow through a bed of granular clay media of 3 to 6mm in diameter. This media is regularly backwashed with the resulting dirty water pumped to the lamella stage for treatment.
In addition to the sludge generated on-site, the Nigg STC receives sludge (in either cake or liquid form) from the surrounding area of an additional 200,000 people. After reception and blending, sludges are dewatered and thickened, with the assistance of polymer addition, and pre-treated by thermal hydrolysis before entering 2 (No.) anaerobic digesters with a combined heat and power system. Digested sludge is then dewatered, assisted by further polymer addition, with the resulting product applied to land.
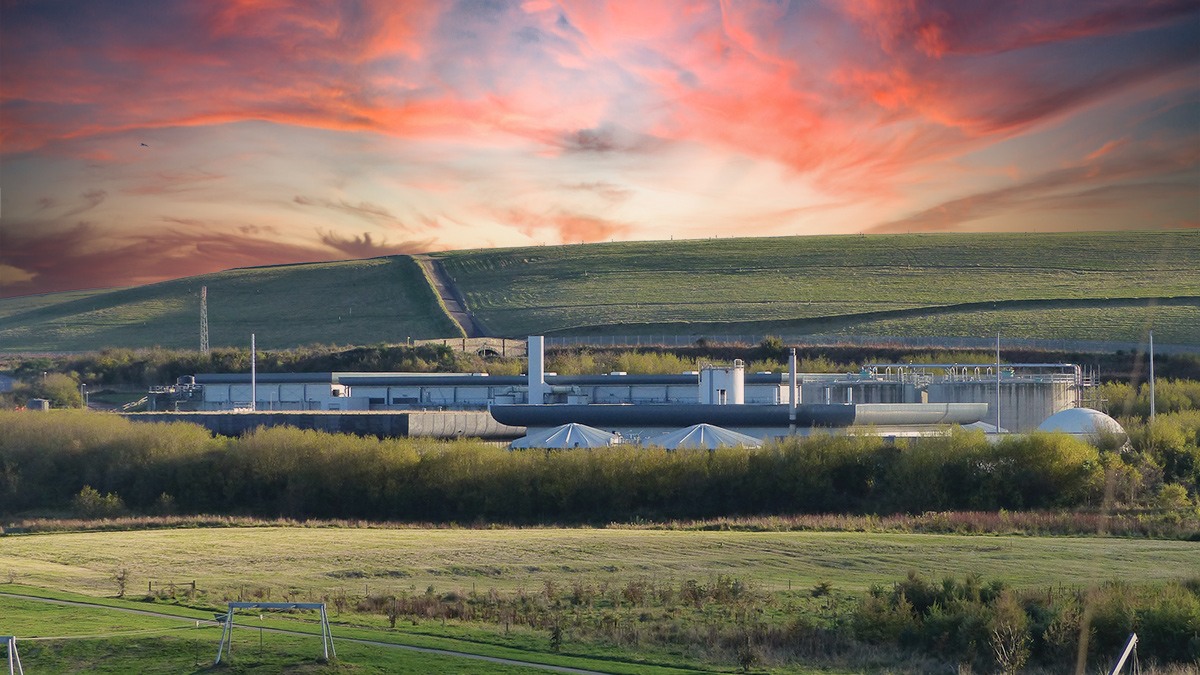
Nigg WwTW and the STC – Courtesy of Evergreen Water Solutions
As built, the dewatering and thickening stages deployed 7 (No.) belt presses, but by 2014 these were requiring intensive maintenance and considered to be at the end of their asset life and thus in need of replacement. Consequently, KWS Grampian commenced an evaluation of options which included the Amcon Volute disc press.
The evaluation concluded through a highly structured business case which considered odour generation potential, health and safety, the ability to cope with rags and the total and whole-life cost, that the belt presses used to dewater and thicken the sludges fed to the thermal hydrolysis process should be replaced by Volute technology; calculations, based on pilot-scale trials in Aberdeen, clearly demonstrated that the whole life cost of the Volute technology was around two-thirds that of any competition.
Based on this appraisal KWS Grampian placed an order for the provision of a 2 (No.) Amcon Europe ES354 Volute disc press units to replace five belt presses. These were to represent the first ever full-scale installation in the UK.
The Volute process
The Volute ES Series thickening and dewatering press was introduced by Amcon, a Japanese company in 1992. To date, there are over 3,000 dewatering machines sold in around 50 countries. It is a cost effective, energy efficient, versatile, robust and revolutionary dewatering and thickening technology. Evergreen Water Solutions Ltd introduced the Volute in to the UK municipal market in 2011.
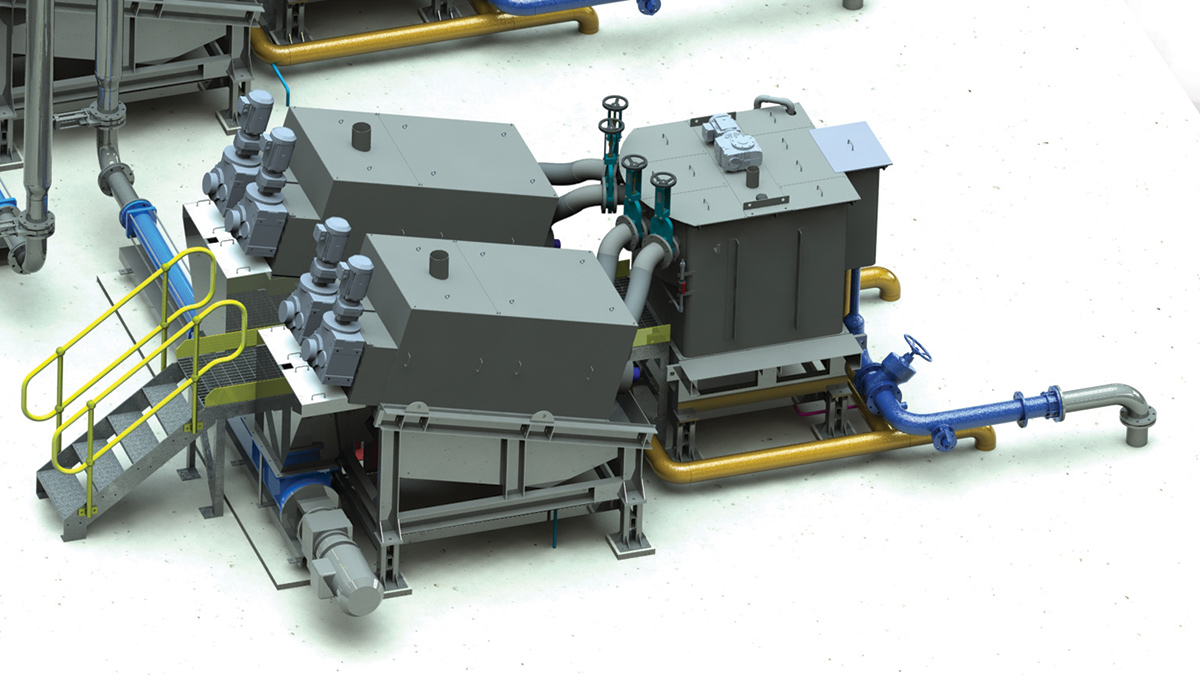
3D CAD Image of the planned installation at Nigg – Courtesy of Evergreen Water Solutions
Volute is a relatively simple process utilising an integrated flocculation tank, a special spiral tapered screw sitting inside a disc drum of alternate fixed and moveable stainless steel rings.
Performance is enhanced by the addition of polymer to the liquid sludge and the action of the screw transports sludge up the inside of the disc drum rings which induce a squeezing and shearing action on the sludge resulting in the release of liquid. This filtrate is then allowed to gravitate out between the fixed and moving rings and collected in a filtrate pan for discharge to the head of the works. Once the thickened sludge reaches the top of the disc screw press it is further dewatered by a permanent end plate where more pressure is applied to the sludge to improve dewatering.
The dry sludge cake is allowed to fall down a chute where it can be collected and forwarded for further treatment.
Volute achieves three process steps in a single process stage; flocculation, thickening and dewatering. The low power required to operate the Volute disc screw makes it 90% more energy efficient than a typical centrifuge and as its washwater requirement is minimal (just a spray-bar system for odour control) consumption of water is significantly less than that of a belt press.
Volute also operates with very little noise (63dB), little vibration, is self-cleaning and resistant to clogging, which means very little maintenance is required (typically 12,000 hours operation between services) all of which results in a very low whole life operating cost.
Design and construction
The order placed with Evergreen Water Solutions Ltd was for the design, manufacture, testing, inspection, delivery, commissioning, training and handover of 2 (No.) Amcon Europe ES354 Volute dewatering presses. This included the provision of mixing and flocculation tanks and any necessary modifications to both the feed and reject pipework and the cake discharge arrangement to suit the existing cake pumps. Evergreen Water Solutions Ltd was also responsible for ensuring that their PLC system was compatible with that of KWS Grampian and providing a control philosophy for maintaining the required dry solids concentration of the sludge cake product as part of the PLC control.
As it was absolutely essential that such a major asset should have minimal downtime during the install, Evergreen Water Solutions Ltd collaborated, and worked very closely, with the client throughout the project, with just two weeks allowed for the mechanical installation by Evergreen, two weeks for the electrical installation by KWS Grampian and one week for commissioning.
During the ten week lead time for delivery of the units, 3D plans were produced, the units manufactured and FAT tested in the Czech Republic and subsequently delivered to the STC at Nigg.
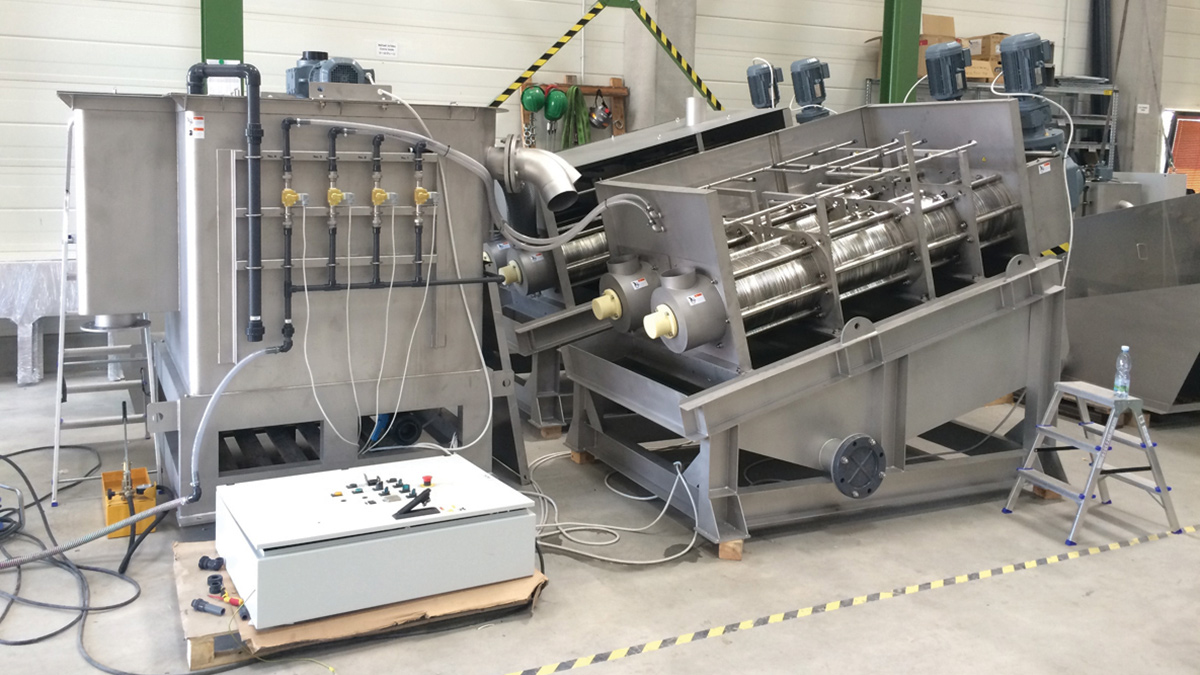
The pristine and Nigg bound Volute unit undergoing FAT testing in the Czech Republic – Courtesy of Evergreen Water Solutions
This identified that the Volute units needed to be raised up 700mm on stainless steel stands to ensure that the existing positive displacement cake pumps feeding the sludge to the THP would not need modification.
During this lead in period KWS Grampian was responsible for removal and disposal of the existing belt presses from the STC building, and this was completed in August 2015. KWS Grampian also assisted with the off-loading of the Volute equipment when it arrived on site and hired in a centrifuge to provide sludge thickening and dewatering, to keep the thermal hydrolysis plant (THP) operational during the project.
Installation of the Volute equipment, into the area previously occupied by the belt presses commenced in September 2015. This included modifications to existing pipework e.g. sludge feed pipework, filtrate drain, washwater, and the improvements to the polymer dosing system (provision of Solitax probes) and was complete by mid-October 2015.
The washwater requirement, to supply the integrated spray bars, was for the provision of 15l/s every 15 minutes per drum (the two Volute units present a total of eight (No.) disc drums), equivalent to 0.5m3/hour. Access platforms and walkways were also provided and installed during this period for inspection of the disc drums and flocculation tanks.
KWS Grampian subsequently undertook the electrical cabling, made all the electrical connections and installed some additional sensors to improve control and set-up interfaces between the PLCs and SCADA to allow control and the exchange of data between the LCP and the main motor control centre (MCC).
This allowed Evergreen Water Solutions Ltd to undertake electrical testing and subsequent commissioning, which was completed in December 2015. However, although the units were in use from this time and feeding the THP some subsequent on-site electrical issues had to be resolved and the polymer dosing system set up to suit the requirements of the Volute. These were soon resolved and the process considered to be fully functional during March 2016, allowing full training of KWS Grampian staff to ensue.
Approximately 95% of the Volute plant and equipment was constructed off-site.
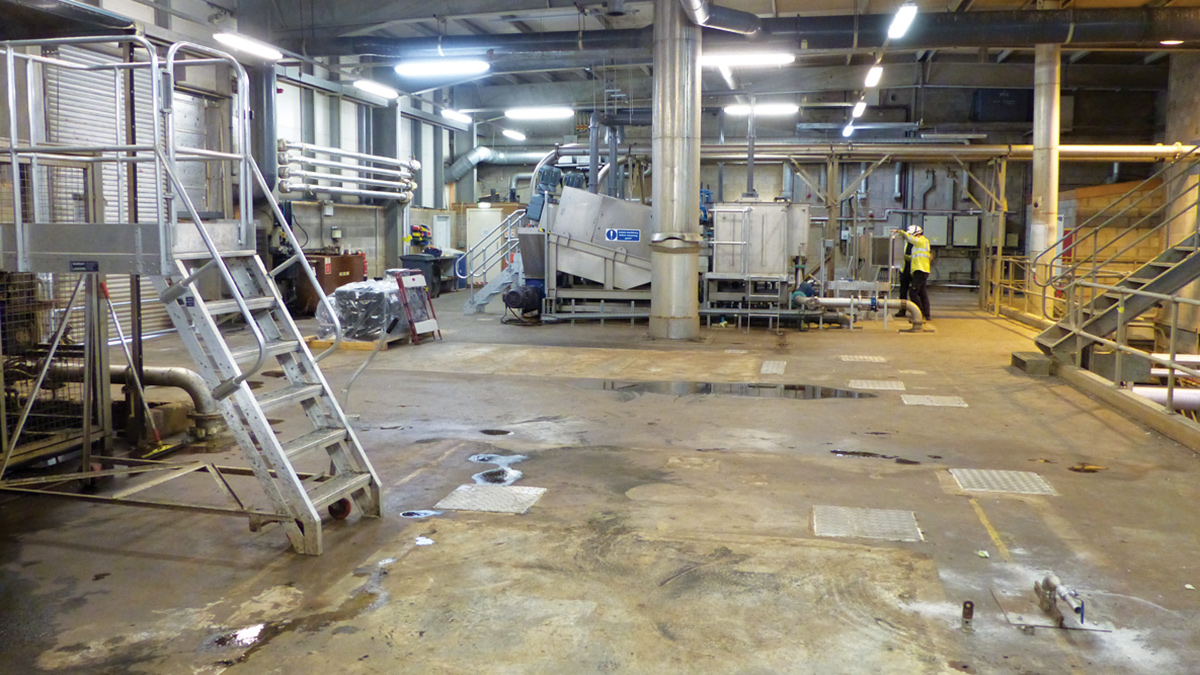
What a comparison! Looking across the area where the belt presses stood towards the Volute machines – Courtesy of KWS Grampian
Progress to date
Since introduction to service at the Nigg STC, the twin Volute machine has exceeded the Kelda Water Services Management and operations team expectations for being reliable and robust process, achieving high utilisation and delivering a consistently dry sludge cake.
Although feed quality can be quite variable (in the range 2.1 to 3.3% dry solids) the Volute units have demonstrated an ability to produce a sludge cake with a dry solids content in excess of 30%. However, this is not ideal and so the target is to actually achieve a cake of around 25% dry solids which can be fed directly to the thermal hydrolysis unit.
This is being achieved consistently with very little variation (+/- 2%) and is one of the attractions of Volute; its operation can easily be ‘tuned’ to deliver the desired quality of product.
The 2 (No.) Volute units operate at a range of 35-70m3/hour (duty/standby or duty/assist). The Nigg Sludge Treatment Centre treats the equivalent of 300,000m3 and 400,000m3 of sludge per annum, equivalent to the processing of between 8,000 and 10,000T of dry solids. As expected solids capture is excellent at around 98%, which usually results in a filtrate containing around 600mg/l of suspended solids.
Over the first year or so of operation KWS Grampian embarked on a programme of optimisation and this has resulted in a further reduction in operating cost as their good work has allowed a polymer dose around 3kg per tonne of dry solids to be utilised.
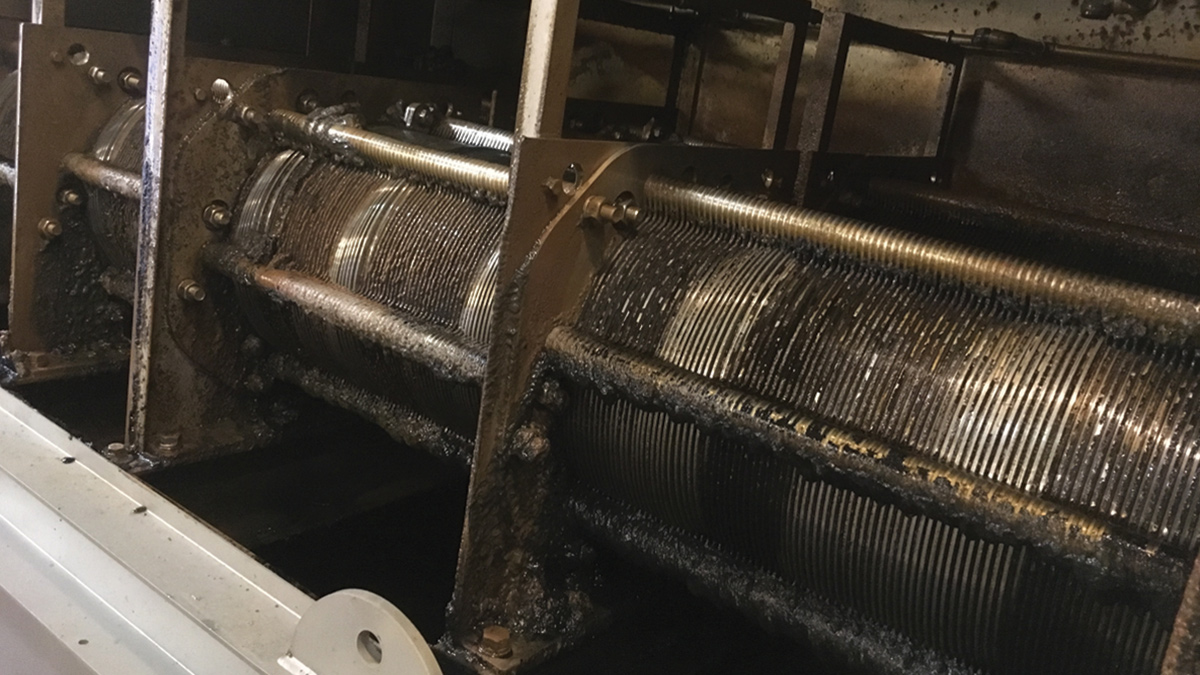
The disc press in action, showing the rings of a Volute drum – Courtesy of KWS Grampian
Conclusion
With 95% of the build off-site, the Volute installation for KWS Grampian at Nigg WwTW has proved very successful and is consistently delivering the target dry solids sludge cake they require on site, 24 hours operation a day 7 days a week, suitable for feeding directly into the a thermal hydrolysis process at 16.5%.
By utilising a polymer dose of just 3kg per tonne of dry solids, using much less energy than a centrifuge and much less water than a belt press, operating costs are low.
Having become the first user of Volute technology in the UK KWS Grampian is now treating their sludge for a significantly lower cost than previously. As a result of this success Evergreen Water Solutions Ltd has subsequently been invited to provide Volute technology at the KWS Grampian Persley site and this is expected to occur in 2017.
This paper was prepared by Robert Mannion, Managing Director, and Geoff Cooper-Smith, Lead Process Engineer, both with Evergreen Water Solutions Ltd.
For more information: Evergreen Water Solutions Ltd: +44 (0)1455 639760 | www.evergreenengineering.co.uk
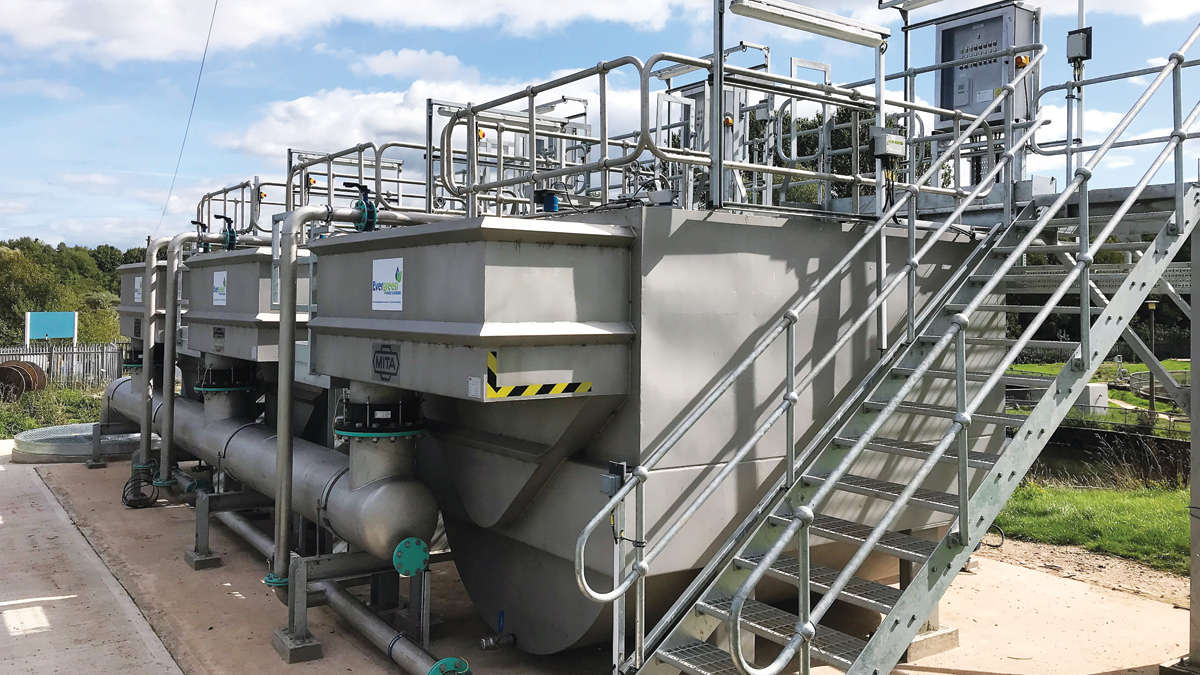
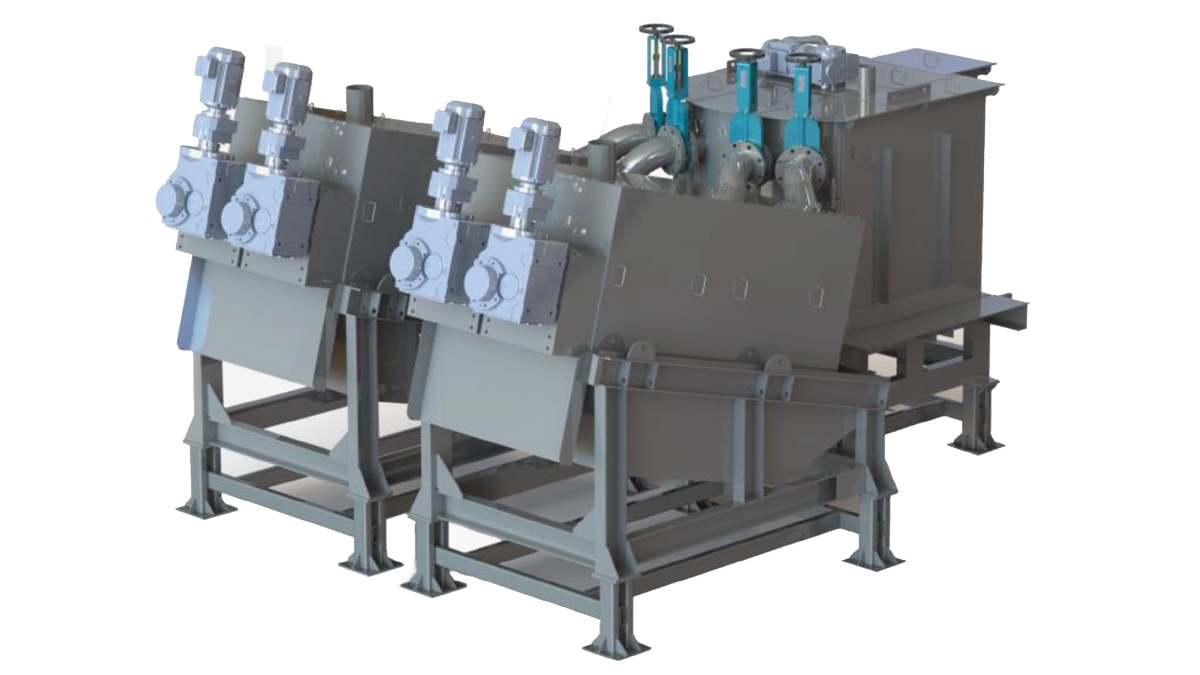
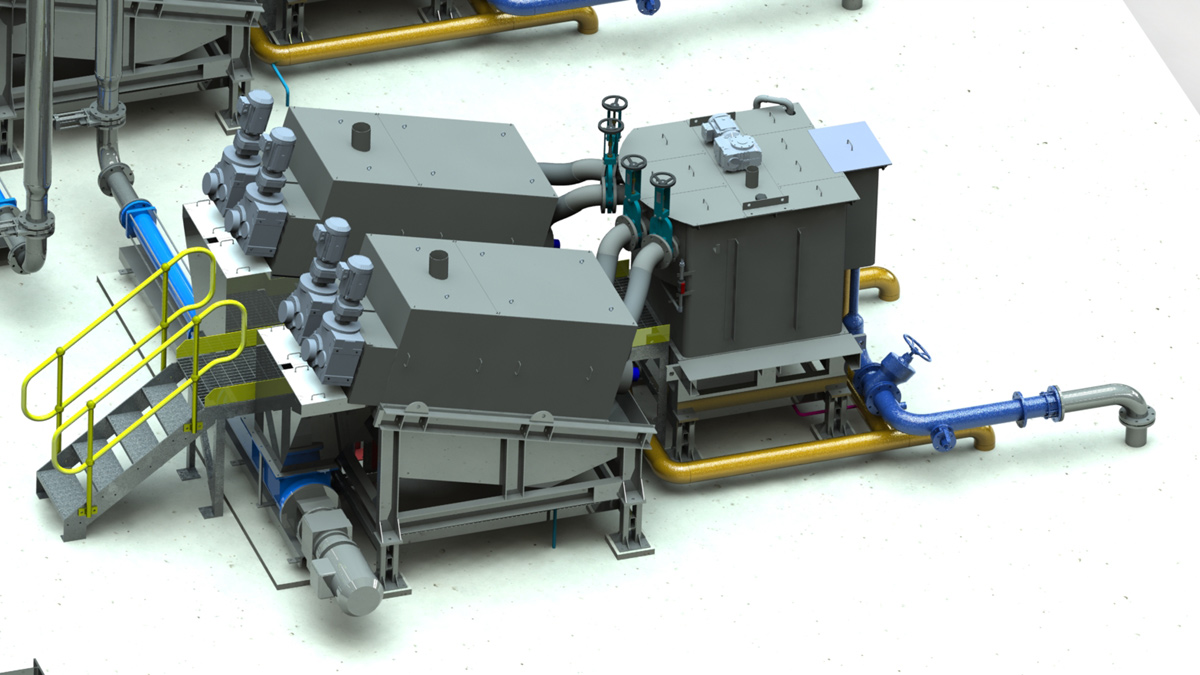
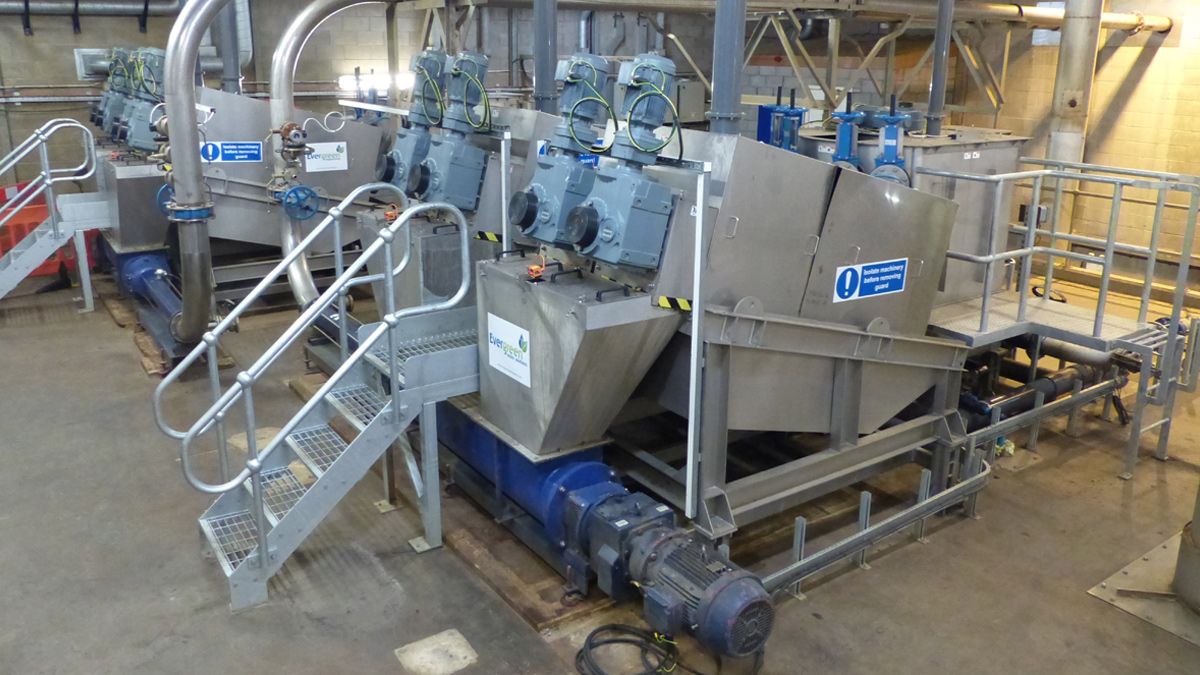
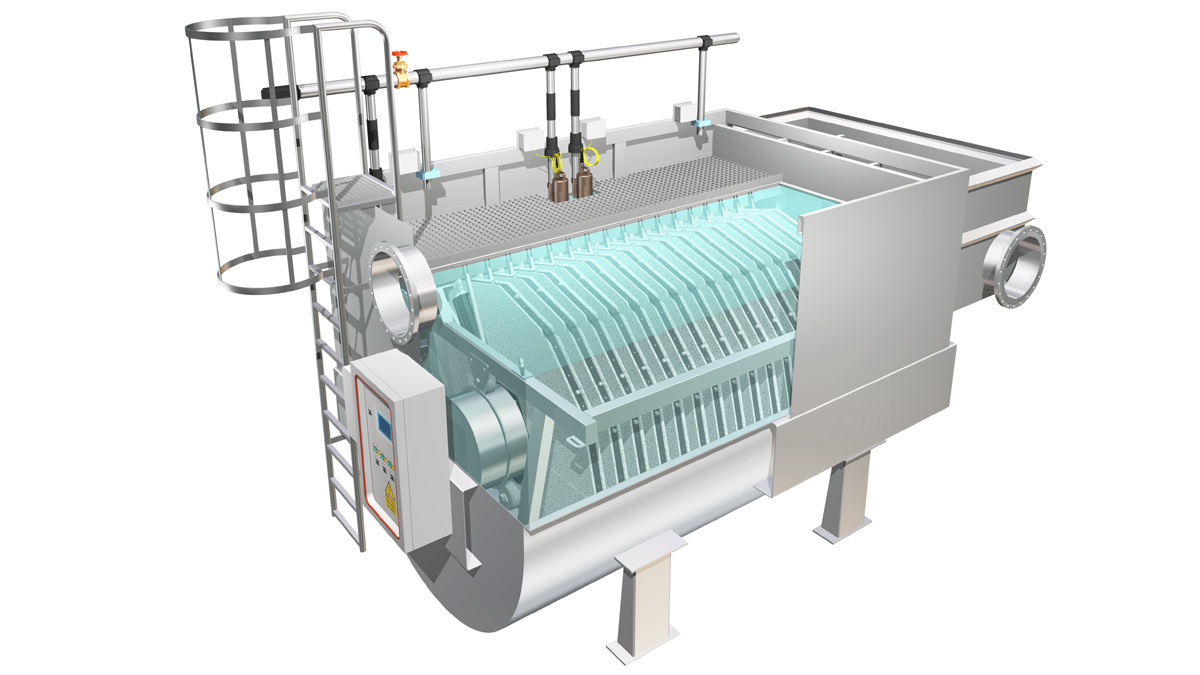
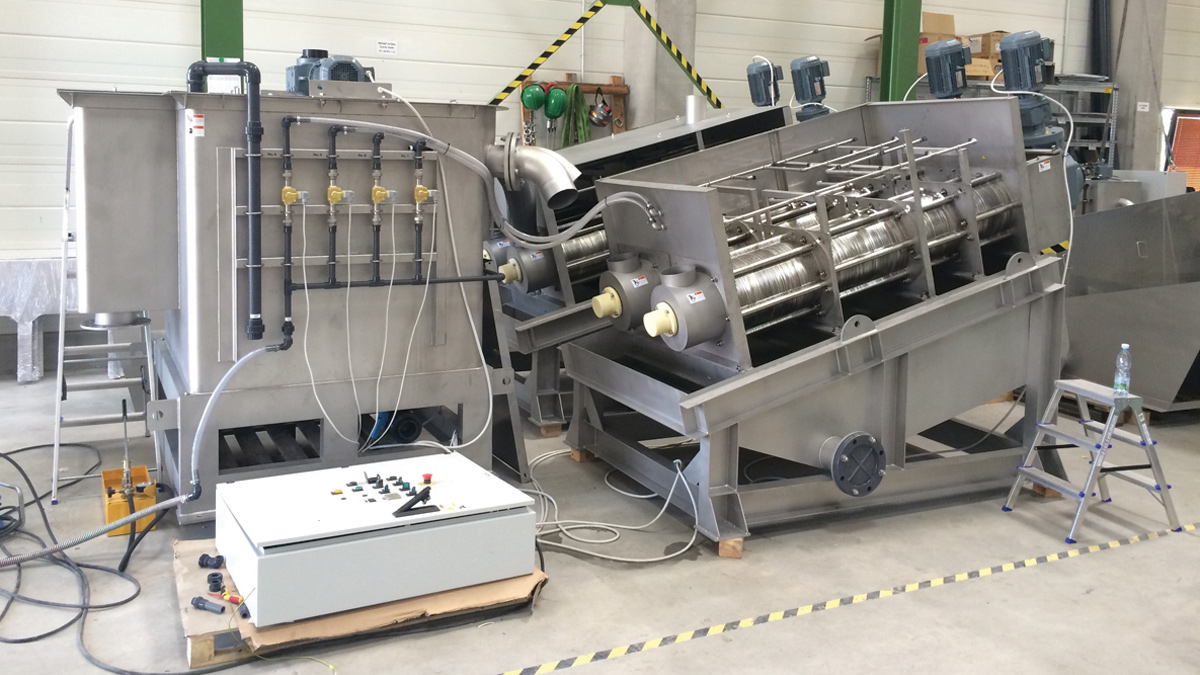
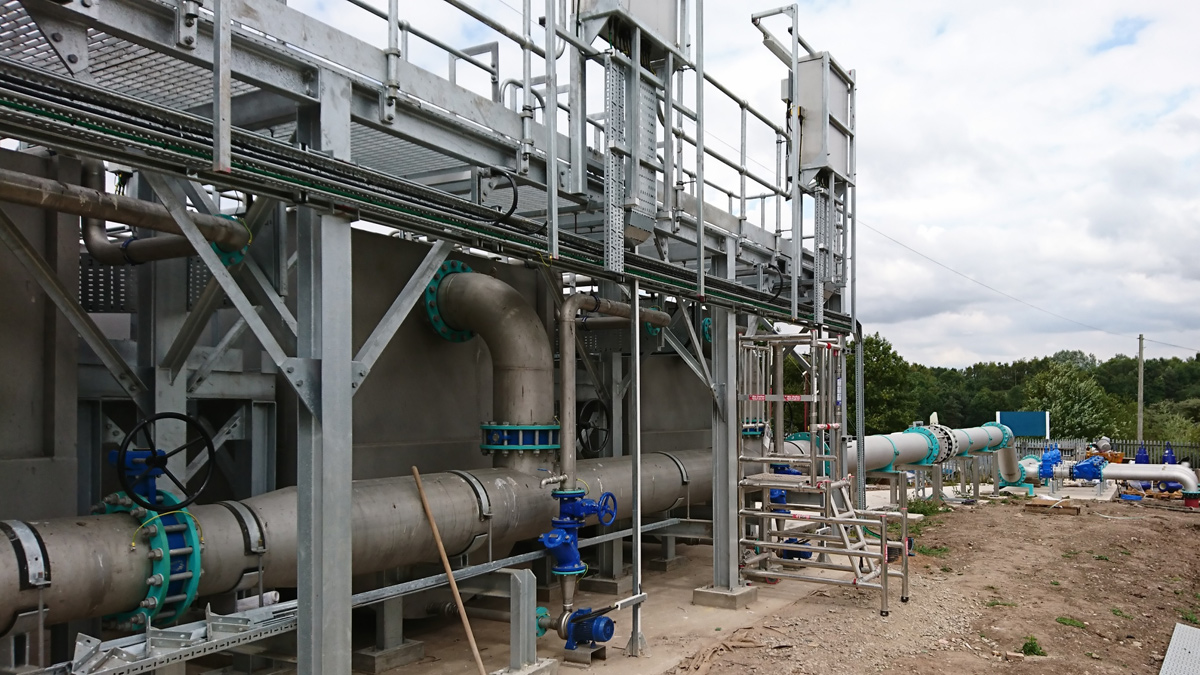

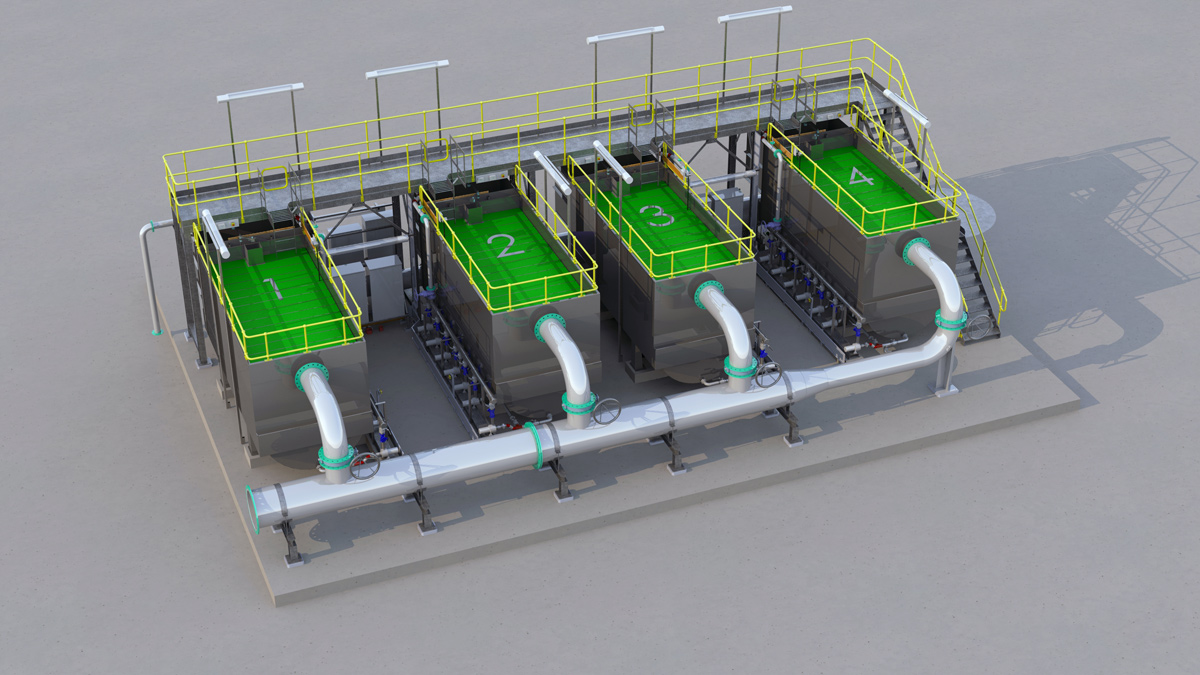
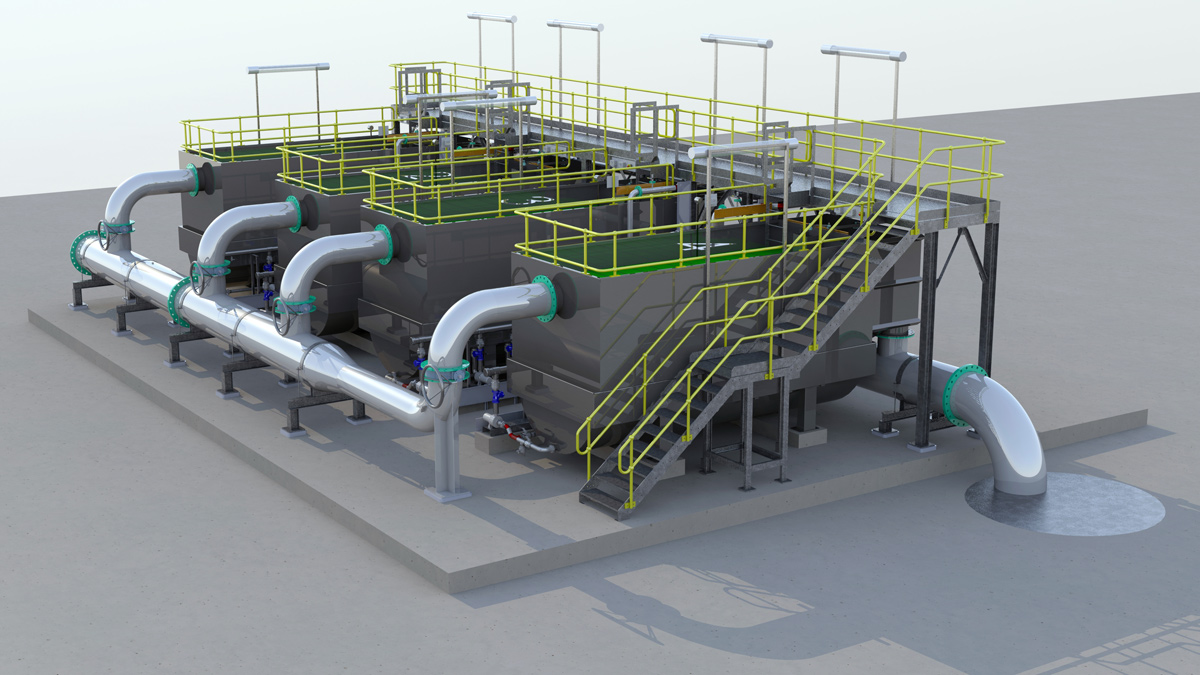
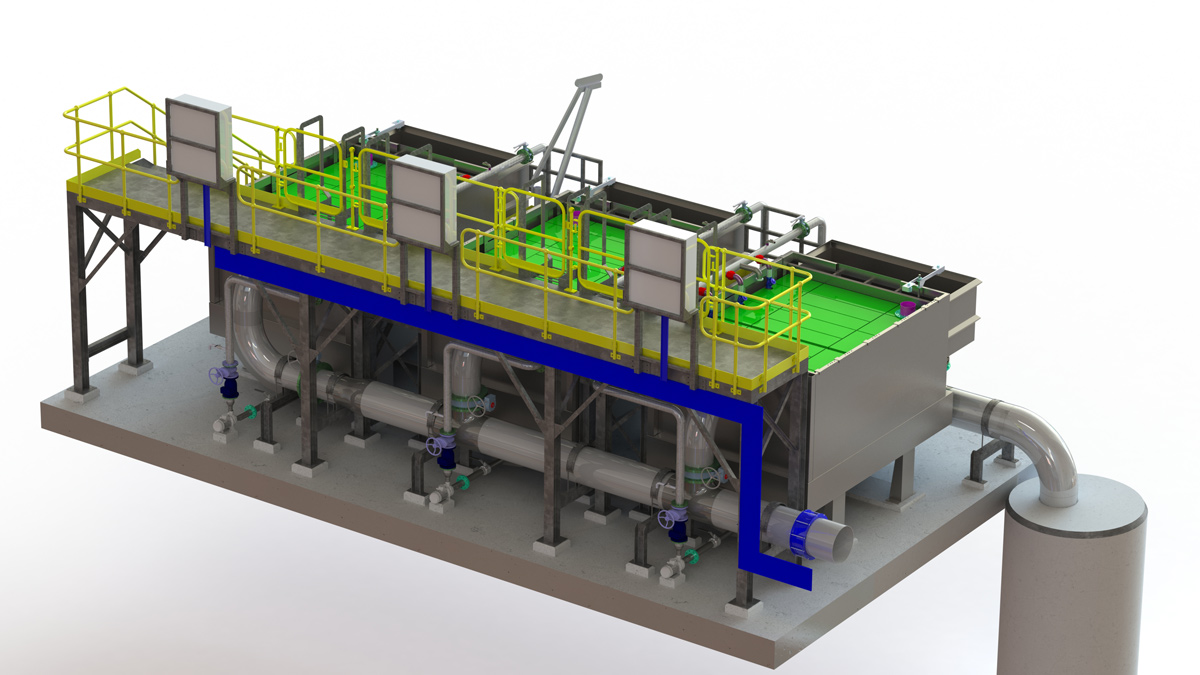
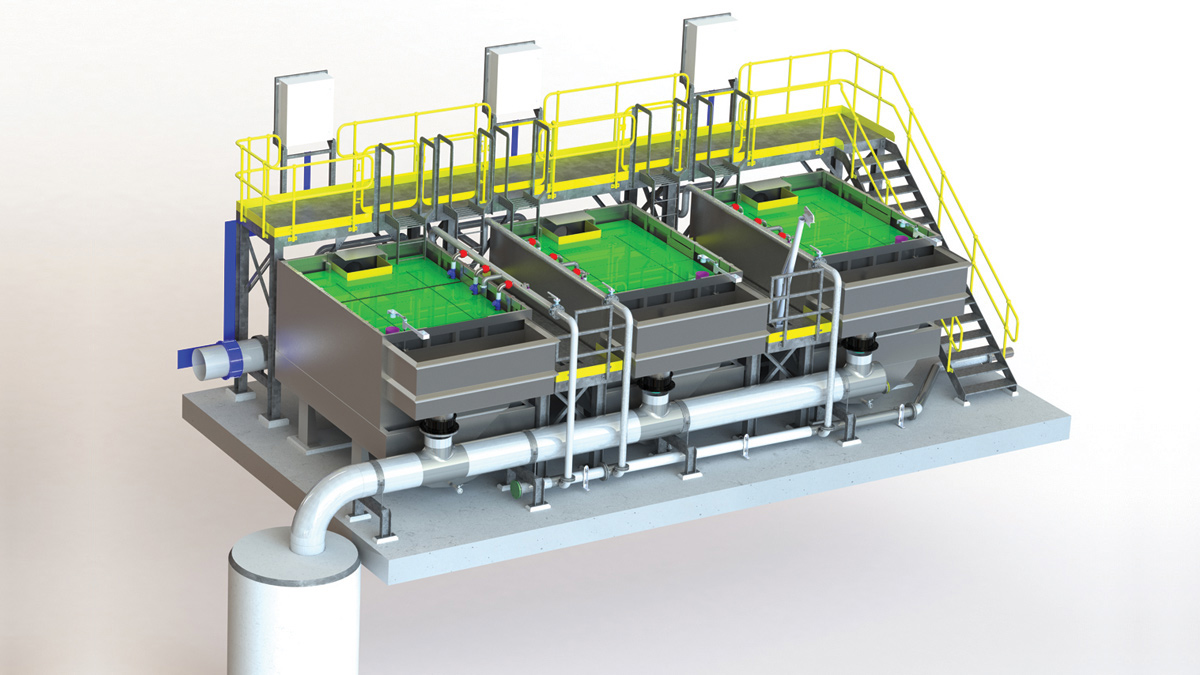
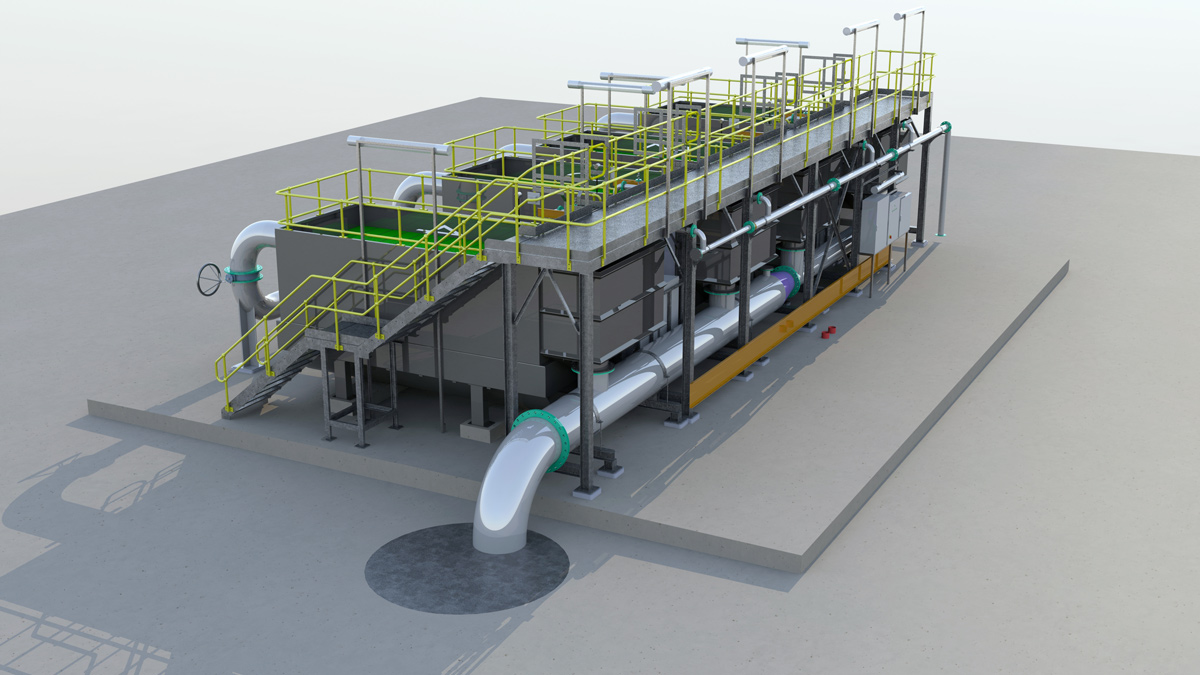
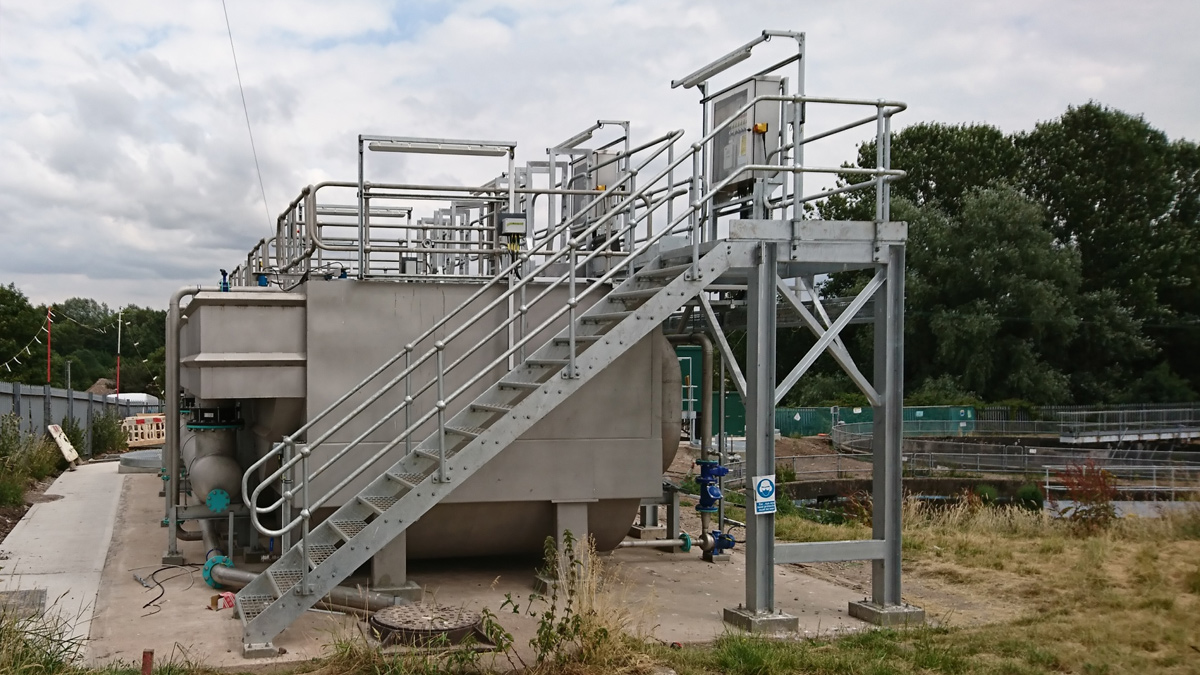