Bürkert Fluid Control Systems
We were established in 1946 by Christian Bürkert, with our headquarters in Ingelfingen, Germany. We boast 5 factories in Germany, France, the US and China and sales subsidiaries in 30 countries, with over 3200 employees across the world. In addition to 5 Systemhaus’, which work on bespoke and customised solutions in close partnership with our customers.
We manufacture over 670 product types, in up to 20 million variants. These include water quality monitors, process control valves, pneumatics, flow sensors, micro valves and pumps, flow meters and controllers. Essentially, we can produce the full fluid control and measurement loop for whatever fluid or gas you are working with, whether this be measuring, controlling, mixing, levelling, dosing and analysing. We also focus on process automation with intelligent communication modules which can be integrated into a process or plant and our online water quality monitoring devices for continuous control.
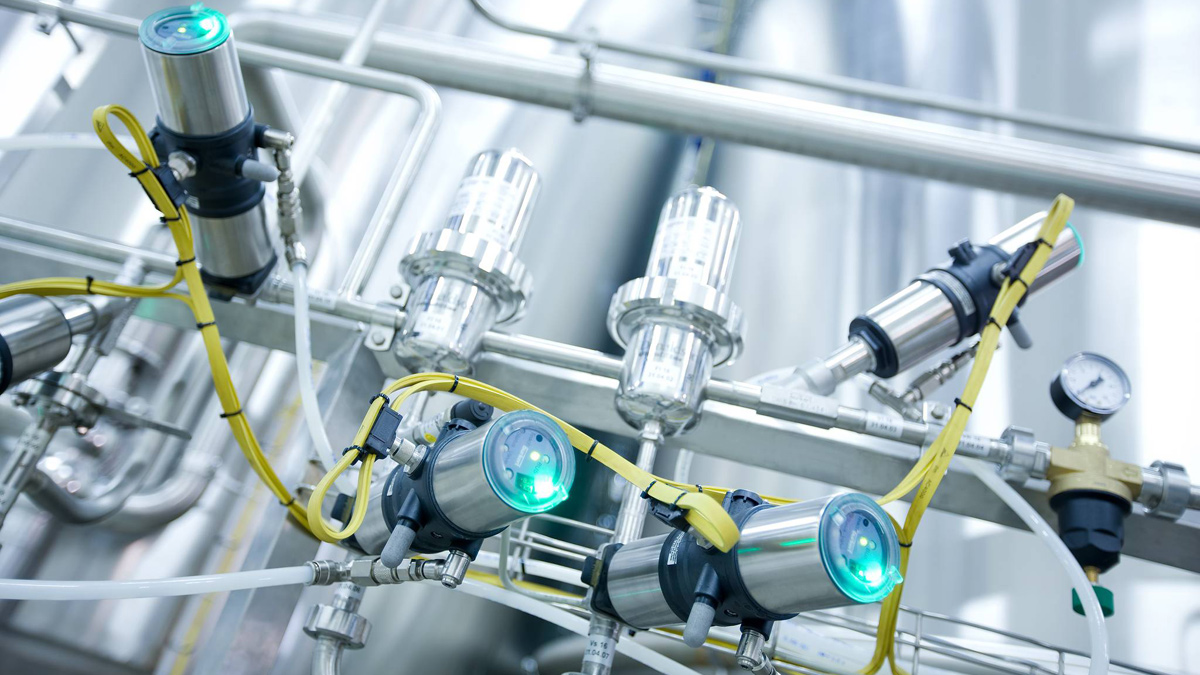
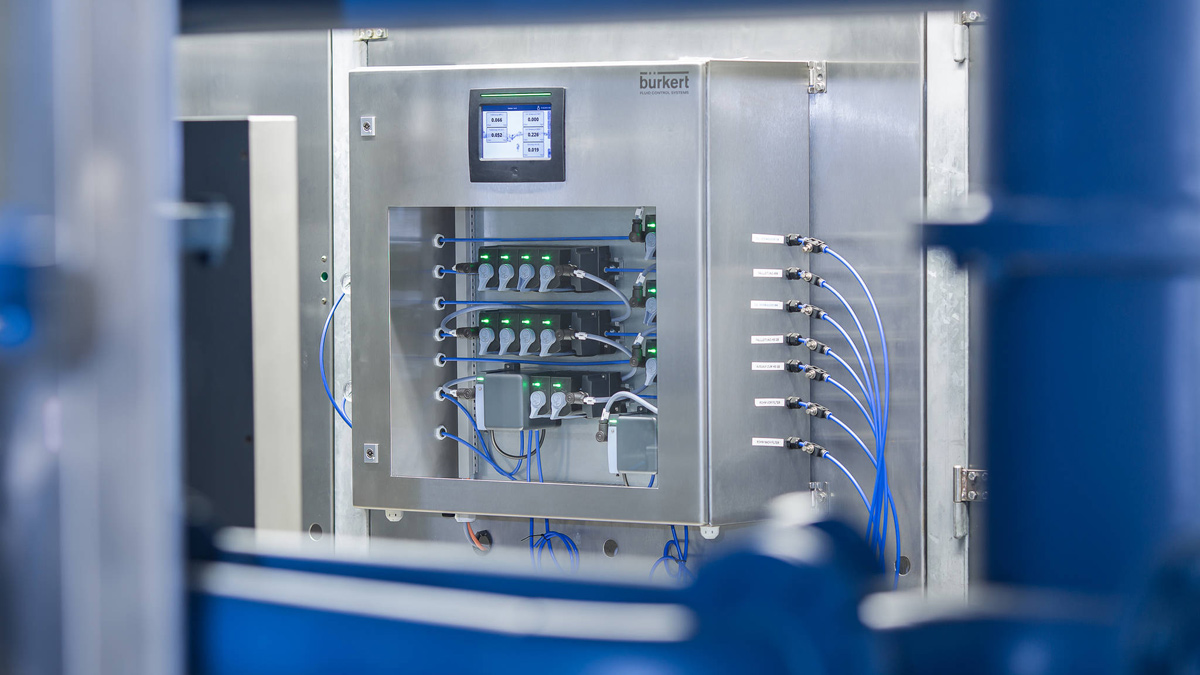
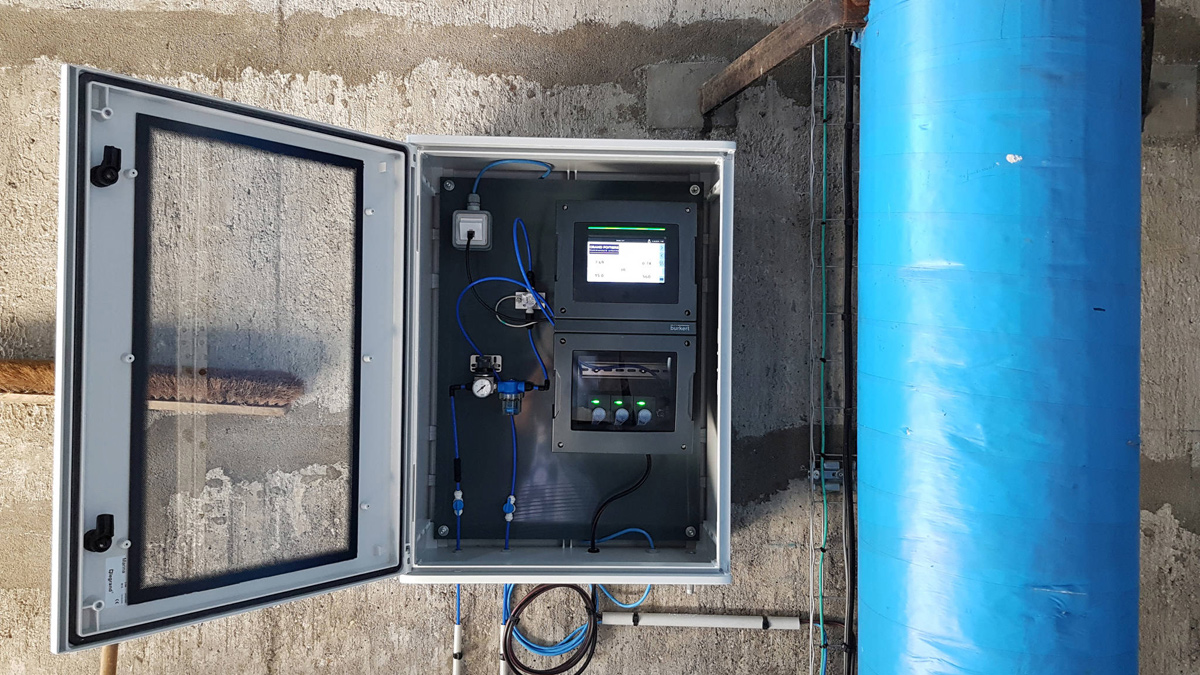
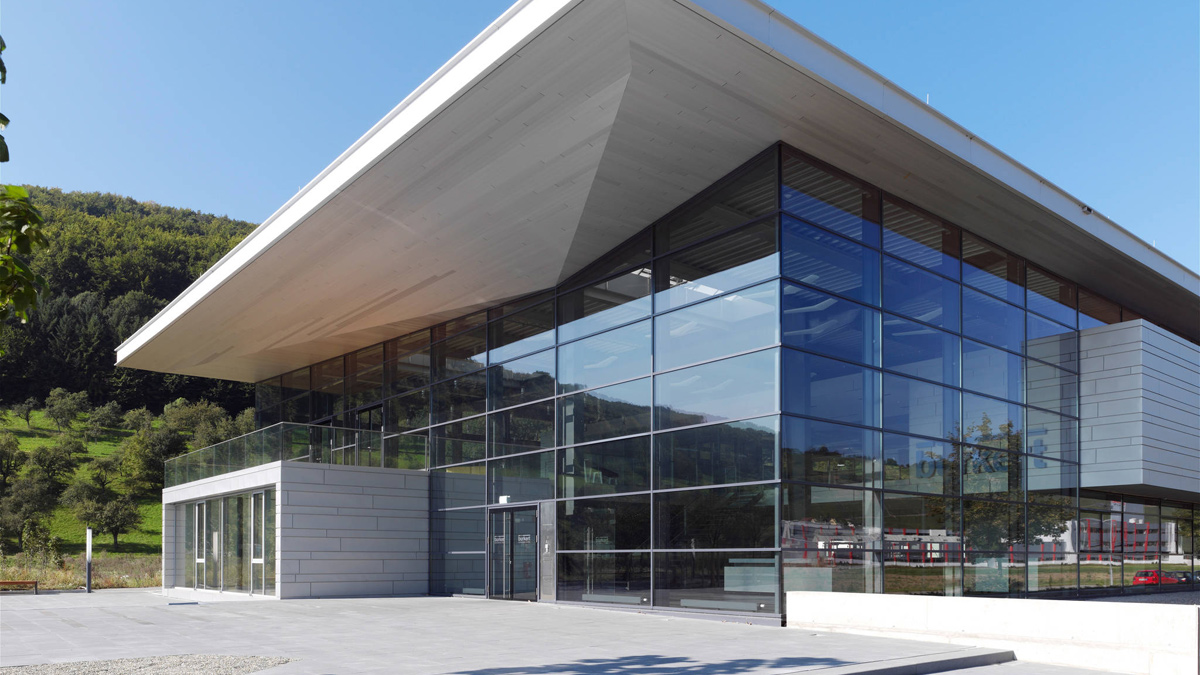
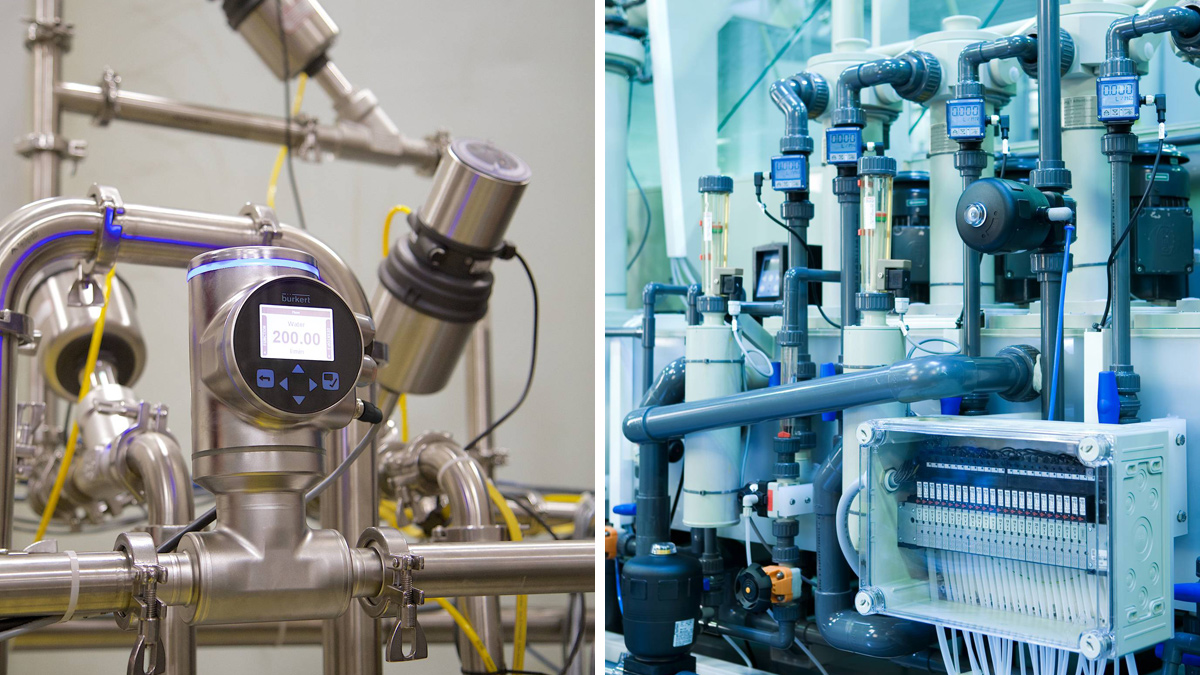
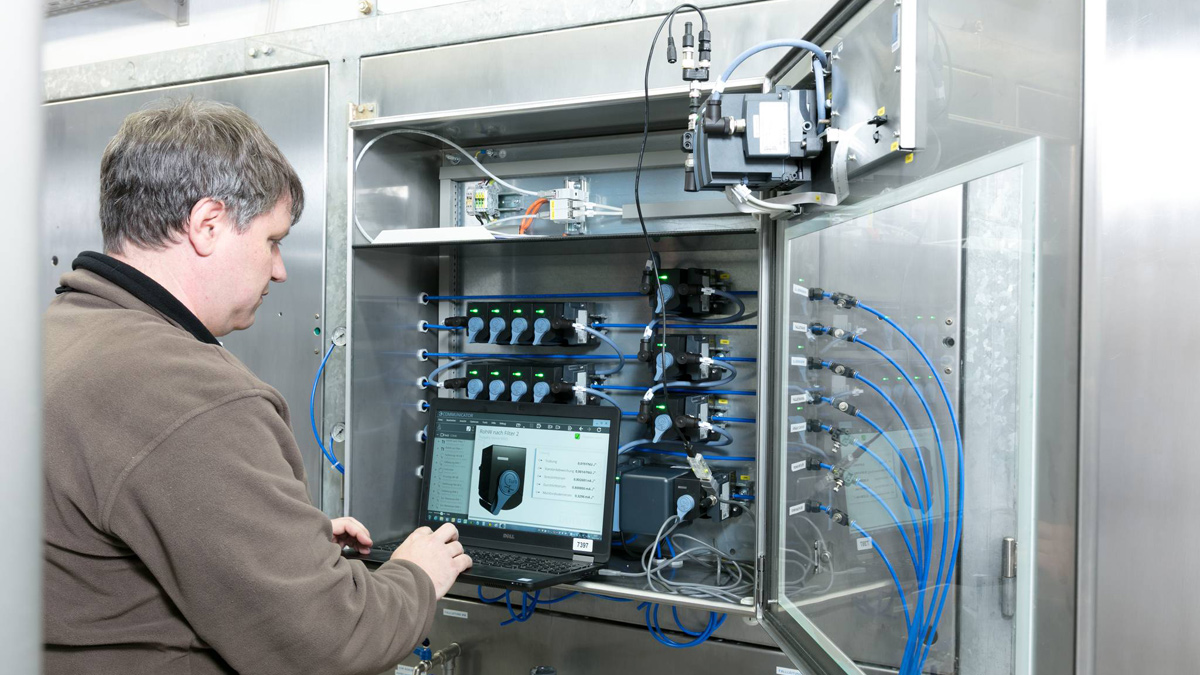
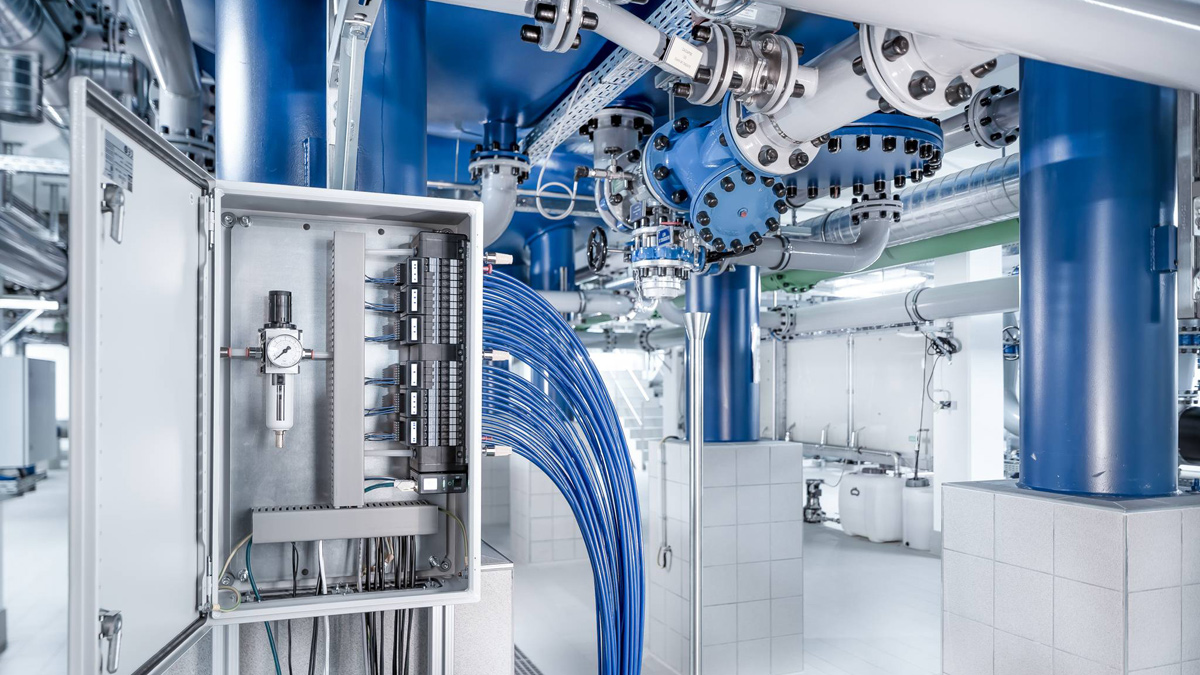
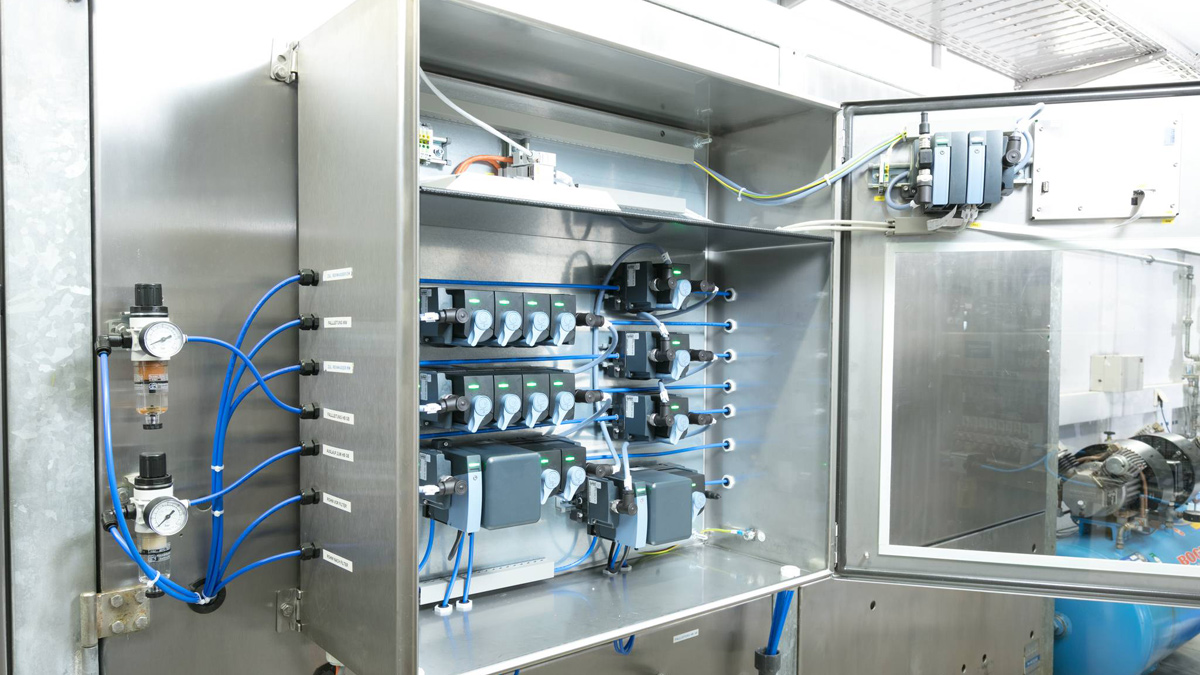