Cotswold Valves
Covering a wide range of sectors including oil, gas, industrial, water, waste water, sewage, chemical and power generation, the business provides consultancy services including product design, specification, selection, valve sizing, actuation, flow and pressure management, installation and the supply and retrofit of a full range of spares and replacement products.
The Group’s Site Services division specialises in “On-Site” product support. We can undertake both new installations and carry out retrofit of valves and actuators to existing works. Where necessary we can act in a support capacity on client led installations
The Flow Control Group incorporates fabrication and machining capabilities and can, in addition to the production of valves and penstocks, design and manufacture mounting kits, pedestals, drive bushes, spindles and other ancillary equipment.
Our manufacturing facilities supply bespoke products in accordance with ISO 9001:2015 quality management systems. The business also operates to ISO 14001:2015 and ISO 45000:2018 standards operating to the highest Health & Safety and Environmental standards.
Utilising our in-house actuation facility, we can assist with actuator selection, and can fit, set and test actuators prior to delivery. We can also fit actuators on site where necessary.
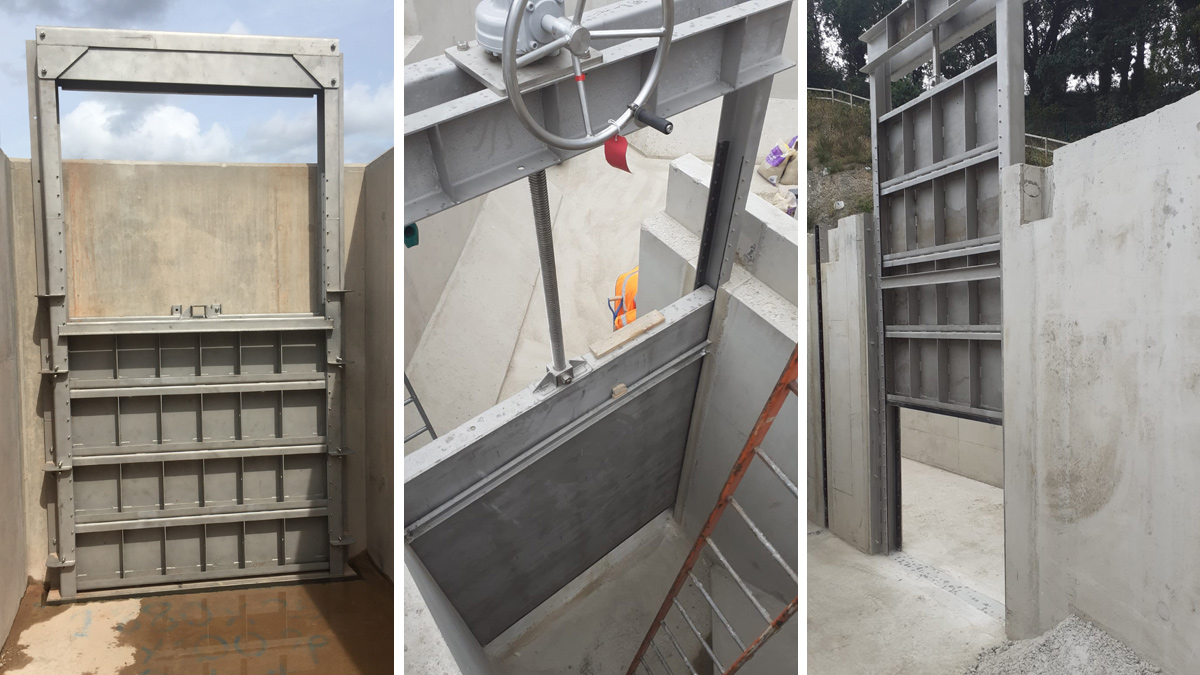