Pipex px
Advanced Thermoplastic Solutions
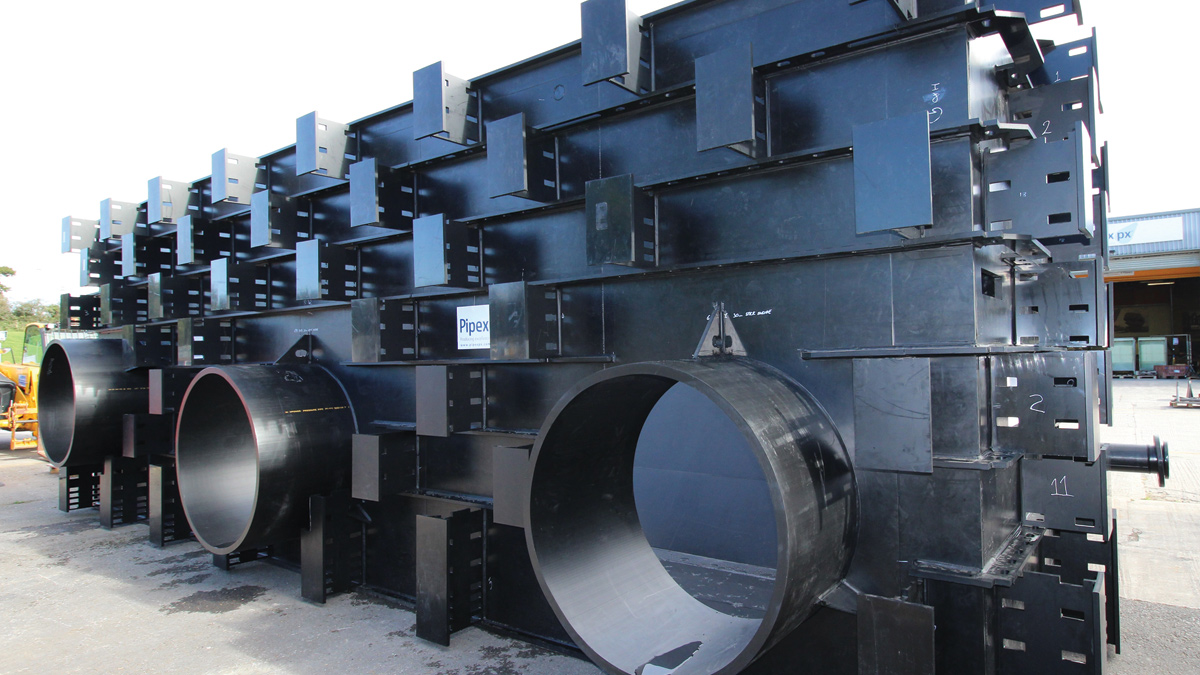
Pipex px® advanced thermoplastic HDPE chamber prior to installation of factory-fitted rebar
In 1989, the UK water industry was privatised, resulting in water companies inheriting reservoirs, treatment works, water mains and sewers which were often outdated and had been outgrown by the increase in population. Since then, investment has been heavily placed in modernising the UK’s water and wastewater services, bringing them in line with strict environmental standards and other UK regulations. An increase in population is not the only challenge for the water companies – routine maintenance of its assets is an on-going battle. Traditionally, the structures and pipework at wastewater treatment works (WwTW) are constructed from concrete – the most used man-made material in the world due to its strength and versatility. However unfortunately, over time concrete cannot compete with the harsh and corrosive substances that it faces within a WwTW. Degradation to structures and pipework within a WwTW can result in on-going and costly maintenance for water companies. Design for Manufacture & Assembly (DfMA) solutions are rapidly becoming the preferred way forward to replace or maintain vital assets at a fraction of the time, and in turn reducing short term and life time costs.
Hayle WwTW
Hayle WwTW in Cornwall, was originally designed and built in the early 1970s to serve the town of Hayle and surrounding villages.
Since its development, the WwTW has undergone multiple extensions and upgrades to cater for the addition of catchment areas stretching from St Ives to Penzance. The WwTW serves an estimated population of over 55,000 people and this number can rise considerably during peak holiday times. It is also a major sludge reception centre, treating industrial wastes, imported sewage and sewage sludge.
In 2016 a scheme was devised by South West Water to upgrade the existing Hayle STW inlet works plant and equipment that had degraded as a result of corrosion caused by prolonged hydrogen sulphide attack.
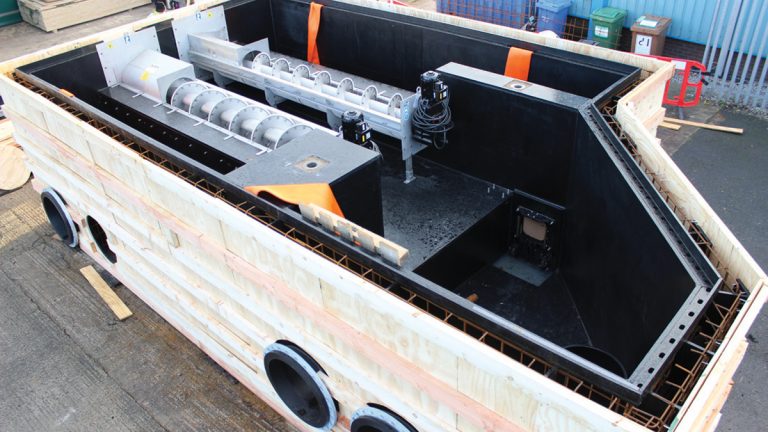
Bespoke Pipex px® civil engineered chamber complete with factory-fitted rebar reinforcement & shuttering and internal equipment
Pipex px®
Pipex px® design services and offsite build capability has solved numerous limited, or complex access issues, providing fit-for-purpose, practical, solutions for an array of applications including:
- Wastewater treatment works.
- Underground and above ground construction.
- SUDS storm water.
- Foul water.
- Restricted access sites, residential, contaminated land, brownfield sites and high water table environments.
Due to the diverse portfolio of off-site built packaged solutions, Pipex px® were approached in 2016 to provide an off-site built Design for Manufacture and Assembly (DfMA) thermoplastic civil engineered chamber as a corrosion resistant, fully sealed, fluid & gas tight alternative to traditional concrete and brick chambers.
At Hayle Sewage Treatment Works (STW), the scope of works included the design, fabrication and delivery of a heavy duty high density polyethylene (HDPE) course screen reception chamber, a fine screen chamber and approximately 27.5m of 1200mm diameter HDPE pipe manifolds as part of the inlet work refurbishment. The bespoke chambers varied in size to suit the project specific requirements – the fine screen reception chamber measured 3.5m wide x 10m long x 2.7m high and the course screen reception chamber measured 9.8m long x 4.9m wide x 3.1m high.
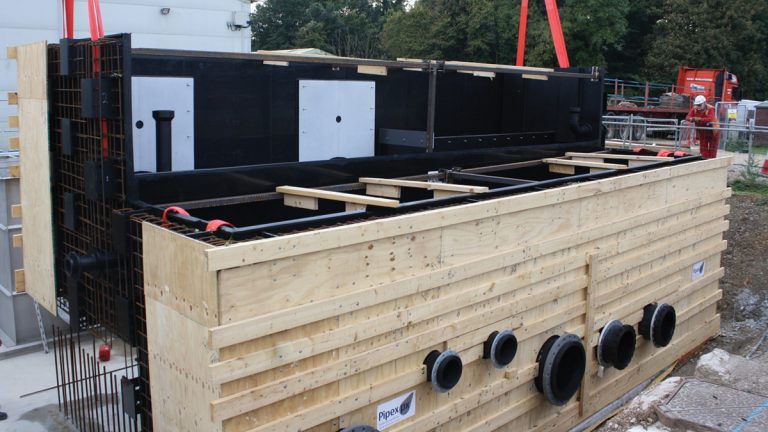
The Pipex px® course screen reception chamber was manufactured, delivered and installed in two sections enabling a fast track installation
Due to its size, the channel screen inlet chamber was manufactured in two sections enabling ease of handling and installation. The chamber was delivered to site on two separate flatbed lorries and lifted into the excavation, where Pipex px® certified site engineers were present to undertake the specialist non-toxic welding, securing the chambers into place. The fine screen inlet chamber was delivered to site as one modular unit.
The chambers were installed in a significantly smaller time frame when compared with traditional build methods. The speed in which the chambers were installed results in a reduction of confined space site works – ultimately reducing health and safety risks for site personnel.
The modular chambers were delivered to site complete with factory fitted steel rebar reinforcement and timber shuttering to accept immediate, site poured, concrete surround with minimal concrete waste. The structural calculations for the steel rebar reinforcement and concrete pour rates were completed by our in-house engineering services department.
Pipex px® bespoke thermoplastic chambers have a 60-year design life dependant on application. The chambers are manufactured to BS EN12573 in reinforced, self-cleansing, hygienic HDPE materials with a smooth internal bore, minimising the risk of leaks, blockages and fats, oils & greases (FOG) accumulation and maintaining flow rates – providing a sustainable and corrosion resistant solution.
Other recent examples of Pipex px® bespoke DfMA thermoplastic civil engineered chambers include projects at Davyhulme in Manchester and Marsh Mills in Plymouth.
Davyhulme STW flow splitter chamber
Pipex px® supplied and fabricated a high density polyethylene (HDPE) flow splitter chamber and sump chamber for Davyhulme Sewage Treatment Works (STW) located in Manchester, UK.
The modular flow splitter chamber was manufactured and delivered in two sections measuring 5.4m long x 5.4m wide x 2.8m high in total. The chamber was delivered to site complete with internal weir and weir plates, factory fitted rebar reinforcement and SAFPLANK® composite grey shuttering. Traditional concrete flow splitter chambers are difficult to construct due to the complex/intricate design. Our thermoplastic civil engineered chambers were manufactured off-site, tested & trial assembled prior to delivery, simultaneously minimising site installation time.
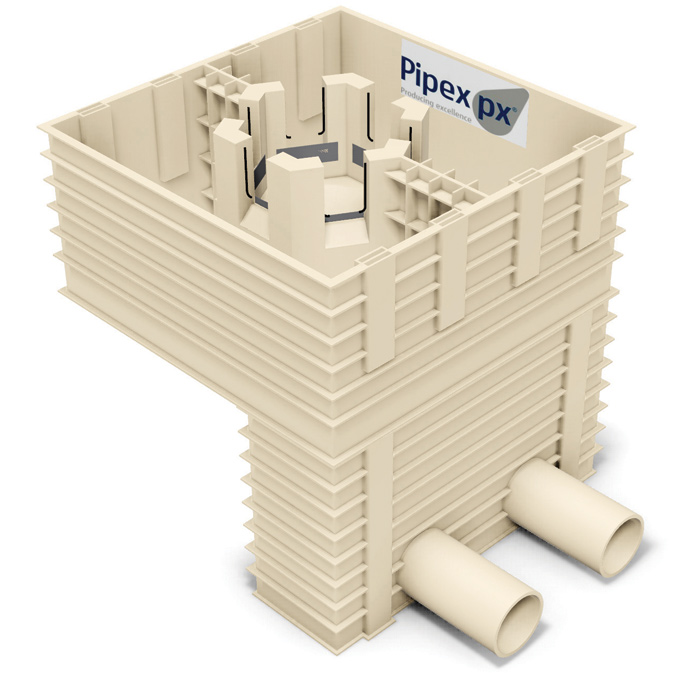
BIM image of Pipex px® flow splitter chamber for Davyhulme STW
Davyhulme STW is one of the largest wastewater treatment works in the UK with flows reaching in excess of 30,000 litres per second during heavy rainfall. The chamber is part of a major modernisation project and will assist with directing the flow of excess wastewater.
Marsh Mills offsite build combined sewer overflow chamber
Pipex px® supplied, fabricated and delivered a high density polyethylene (HDPE) combined sewer overflow (CSO) chamber to divert and screen incoming flows of wastewater for a treatment works in Plymouth, Devon.
The bespoke chamber is positioned above ground and is approximately 8m long x 4m high x 2m deep in size. Steel rebar and timber shuttering were affixed to the chamber to allow for immediate concrete pour once installed onsite.
Pipex px® designed, fabricated and installed a fibre reinforced polymer (FRP) top cover, which was manufactured from EXTREN® FRP support beams and anti-slip Composolite® panels. The design featured a central reservation of access hatches with removable DURADEK® I-6000 grating below for safety.
FRP was the ideal material as it is 1/3rd the weight of traditional building materials. The top odour control cover was required to support 5kN/m2 and rested entirely on top of the chamber to ensure no obstruction was caused to the flow of water below.
The chamber featured twin ROTAMAT storm screens from Huber Technology which were supplied by the client and installed at the factory within the chamber within one day.
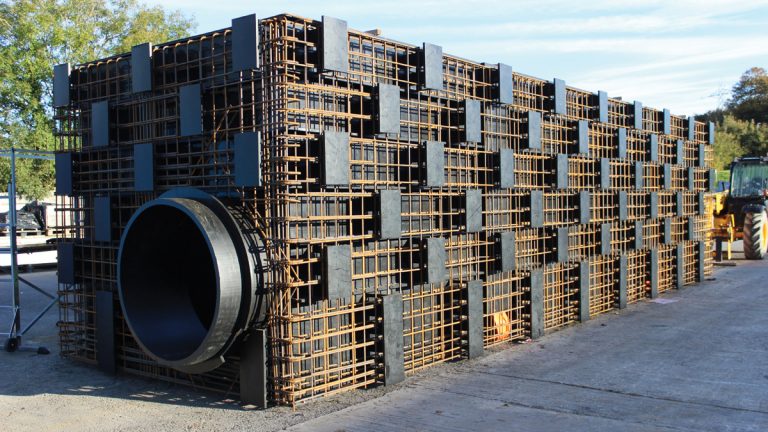
Pipex px® fine screen inlet chamber with factory-fitted rebar reinforcement
Conclusion/summary
Our chambers, as illustrated above, can provide you with a wealth of project advantages including;
- Improved onsite health & safety.
- ‘Fit and forget’ solution with a 60+ year design life.
- Virtually maintenance free.
- Corrosion & chemical resistance.
- Fully sealed, water, fluid and gas tight.
Pipex px® advanced thermoplastic products offer reduced installation time coupled with improvements in safety, quality and time, offering superior design and project flexibility to suit the most demanding of projects.
This paper was prepared by Pipex px®. For more information: +44 1752 581200 | www.pipexltd.com
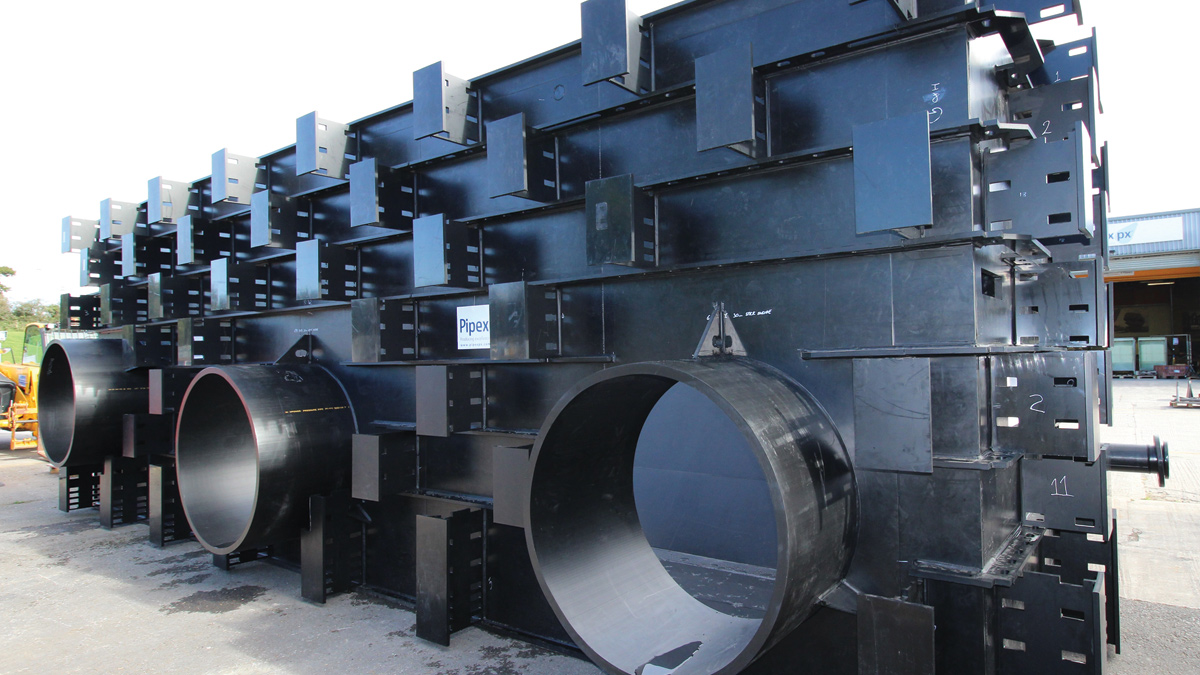
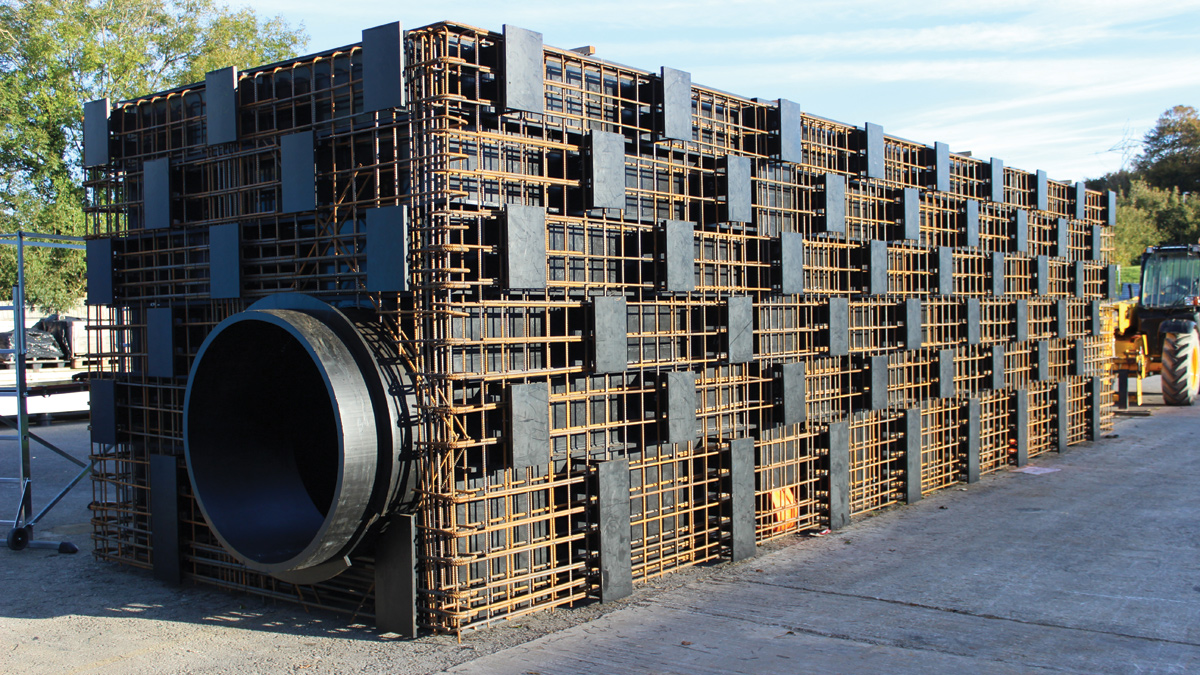
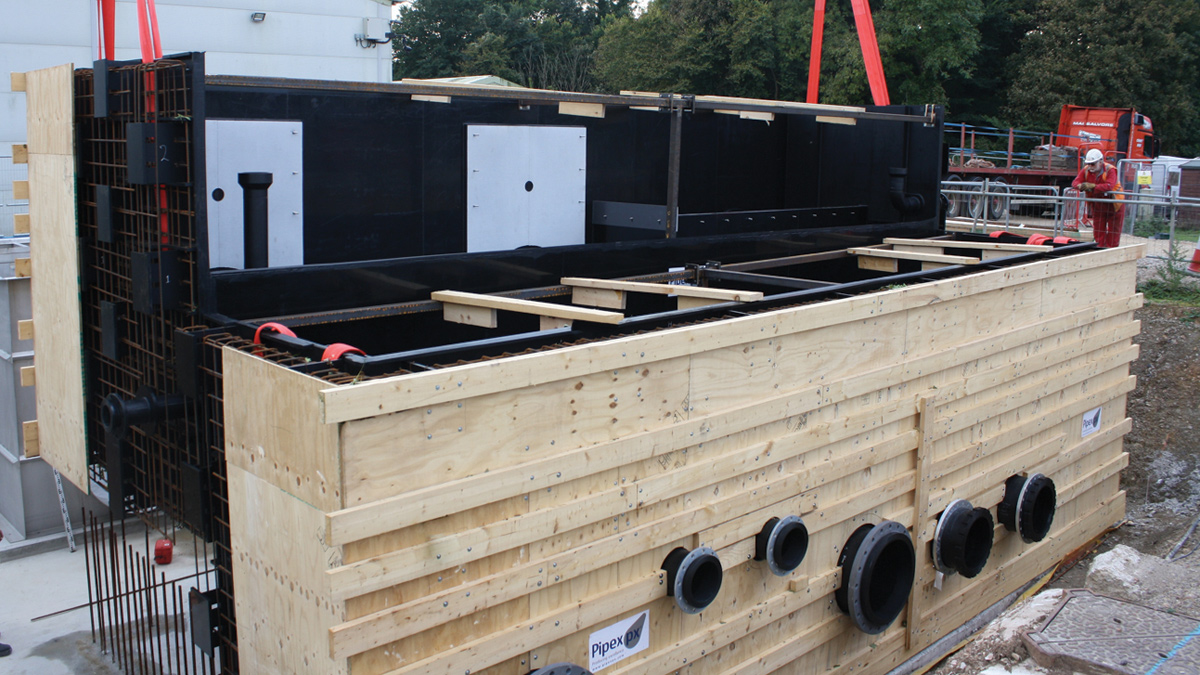
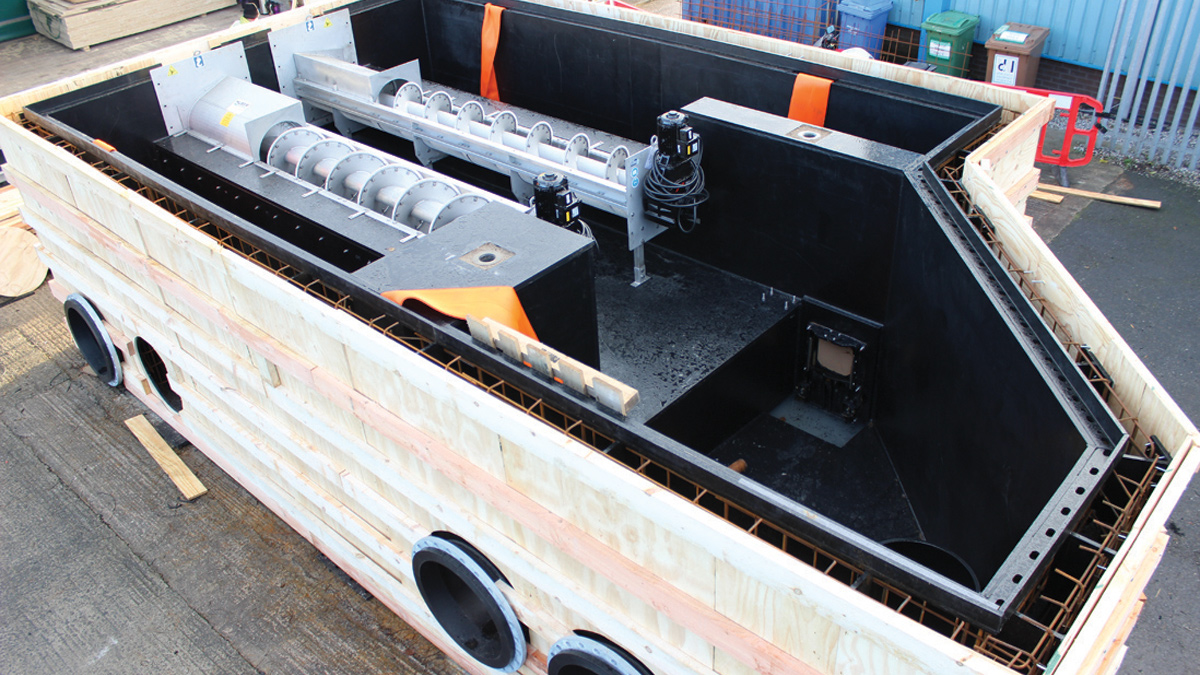