Sundon Water Treatment Facility (2024)
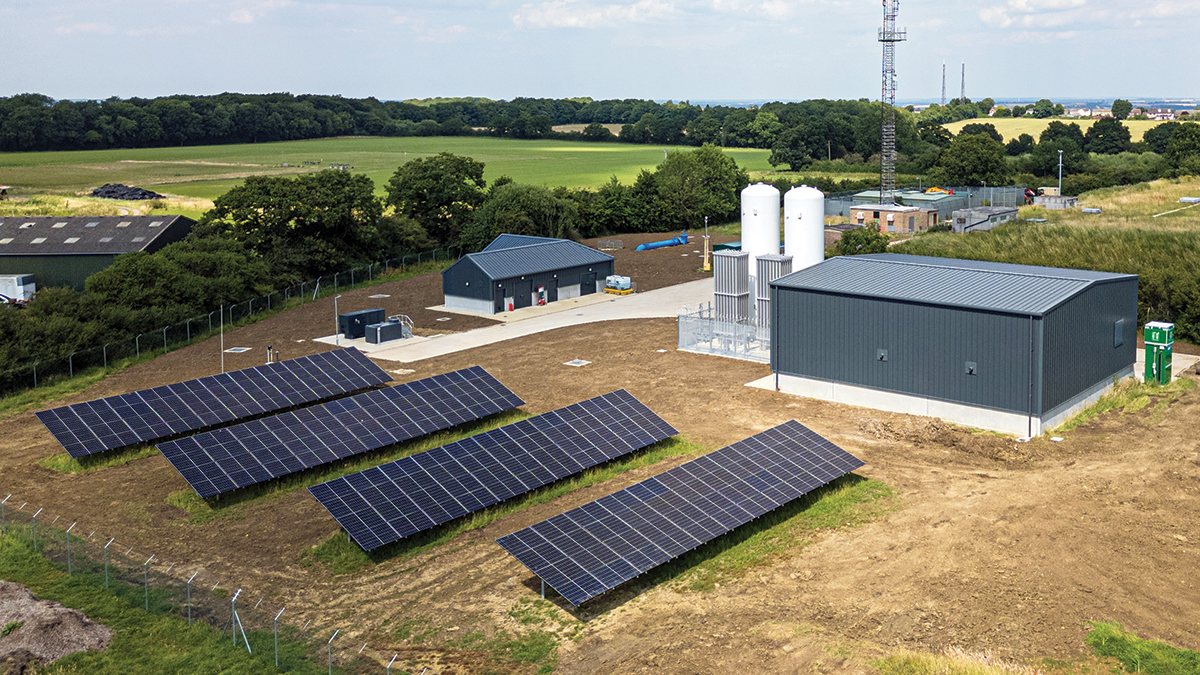
Sundon Water Treatment Facility - Courtesy of Ward & Burke
Between 2015 and 2020, Affinity Water reduced abstraction from chalk groundwater sources by 42 million litres per day (MLD) and aims to cut an additional 36 MLD by 2025. These efforts are crucial for sustainably providing high-quality drinking water to their customers. While Affinity Water does not manage sewage, it plays a key role in maintaining the ecological health of rivers by reducing water abstraction and making other environmental improvements. To protect chalk streams and their wildlife, Affinity Water is importing more water from Anglian Water’s Grafham Water Reservoir. Affinity Water has acquired Sundon Reservoir, an underground clean water facility reservoir near Luton, originally built by Anglian Water. As part of the plans, a treatment facility was constructed to adjust the Larson-Skold Index and free chlorine levels, as well as refurbishing the reservoir with a dividing wall for improved resilience.
Purpose of the new water treatment facility
The treated water from Grafham Water Treatment Works (WTW) has a different water chemistry to that of the vast majority of treated water in Affinity’s network.
The Larson-Skold Index (LSI) is an empirical scale that measures the corrosivity of water towards mild steel. During an early feasibility study, it was noted that the LSI of the water from Grafham will be much higher than that of water treated by Affinity. Therefore, if Affinity Water is to import such an increased amount from Grafham WTW to Sundon, then further water treatment would be required.
Reservoir additions and modifications
The first phase of this project saw some work being undertaken on the existing concrete reservoir structure. The tank was bypassed and drained, with work being carried out in off-peak months as to make the most of the lower demand period. A reinforced concrete in situ dividing wall was constructed down the centre of the tank to split the single cell reservoir into two. This provides storage resilience during decennial inspections.
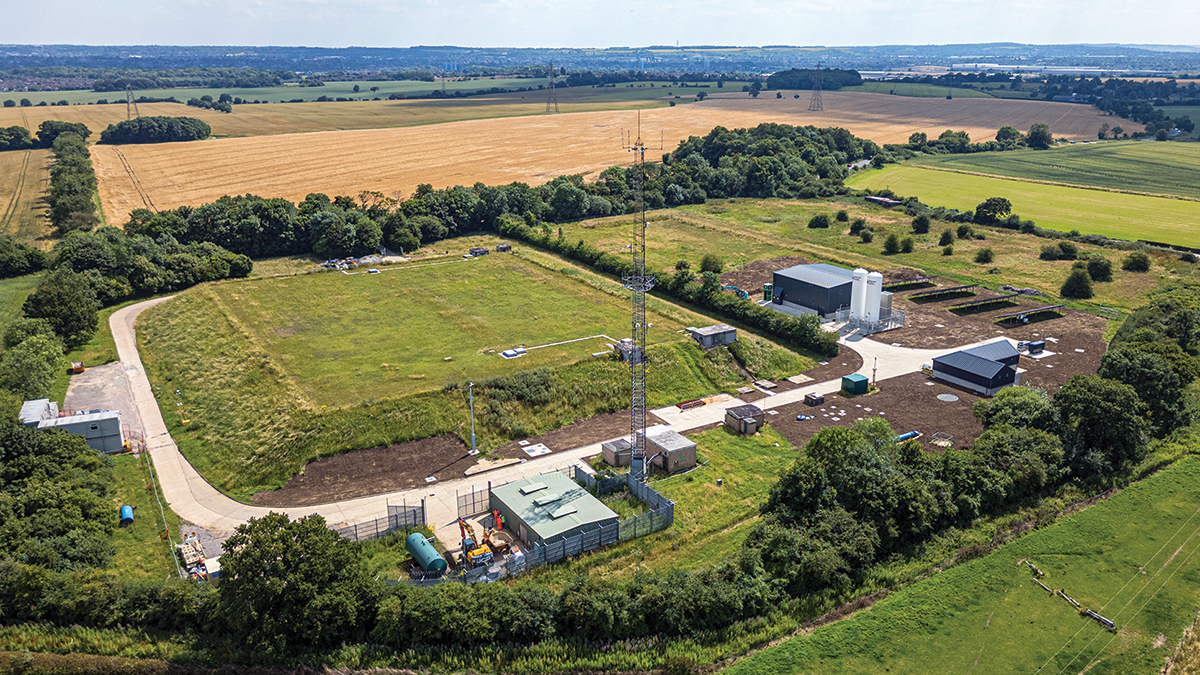
Sundon Reservoir and Water Treatment Facility – Courtesy of Ward & Burke
The incoming twin mains were brought together and a new DN800 ABB flow meter was installed. Tapering up to DN1200, the main was brought above ground into the new building before diving back down and on towards the reservoir. Existing inlet, outlet, overflow and washout pipes were reused for one cell, while new ones were installed for the second cell.
Other modifications included new access hatches, ladders, pipe hop-overs and overbanding on existing concrete joints. A baffle curtain was installed in each cell to channel the water down to one end of the reservoir and back before leaving, creating the contact time required for the chlorine to reach ‘breakpoint’ (see the following section).
As such, the reservoir used for storage as a primary purpose, was also being used as a contact tank. Prior to returning the cells to service, the structure was inspected, hydrostatically tested, thoroughly cleaned and subsequently sampled.
Chemical dosing
Sodium hypochlorite dosing: There are two components to the dosing of sodium hypochlorite:
- To destroy the chloramines (breakpoint).
- To leave a free chlorine residual in the outgoing water.
The dosing is calculated using the results from the import water quality analysers; Hach’s ammonia analyser and Swan Analytical’s free and total chlorine analysers. To determine the free chlorine levels after breakpoint chlorination had been reached, a vessel was used to simulate 30-minute old water before being analysed. This 30-minute value was arrived at experimentally through a bench test in outline design. Finally, the calculated dose per litre of water is then multiplied up to be flow proportional using the new flow meter.

Water quality analysers – Courtesy of Ward & Burke
Bulk quantities of sodium hypochlorite at 14-15% w/w concentration are stored in vertical cylindrical tanks, manufactured by Forbes Technologies Ltd. The tanks are manufactured from GRP with a uPVC lining inside, with typical connections for inlet, outlet, drain, vent and overflow. Pressure instruments installed at low level are used for chemical level readings as to remove any working at height. The duty tank is selected using an actuated valve on the tank’s outlet, taking the chemical into the dosing skid.
Grundfos manufactured the dosing skid for this project. Two duty/standby configured Grundfos DDA120 smart pumps are used in a standard dosing skid configuration with components including, but not limited to, pulsation dampers, loading valves and PRVs.
Duty/standby outlets are provided for two dosing hoses that connect the dosing skid in one building, to the point of application (POA) cabinet in another building. The dosing hoses used, stretching a distance of around 50m, is PF Detect dual contained, leak detection hosing from FT Water Treatment. This hose-inside-a-hose has two copper wires in a helix sandwiched between the two hoses. In the case of the internal carrier hose bursting, chemical leaks into the gap between hoses and by capillary action, fills the gap until a short is created across the two copper wires, indicating a fault at the control panel. This automatically switches to the standby dosing line immediately, preventing any further leakage. Note that the leakage is contained thanks to the outer hose’s extremely high burst pressure. This has allowed for transfer of chemicals through ducts over a great length without using catchpots and rigid outer piping.
The POA cabinet is situated adjacent to the static mixer on the water main. It is of typical construction with a loading valve and flow switch. Finally, withdrawable injection lances are used in the DN1200 static mixer to dose the sodium hypochlorite into the water main.
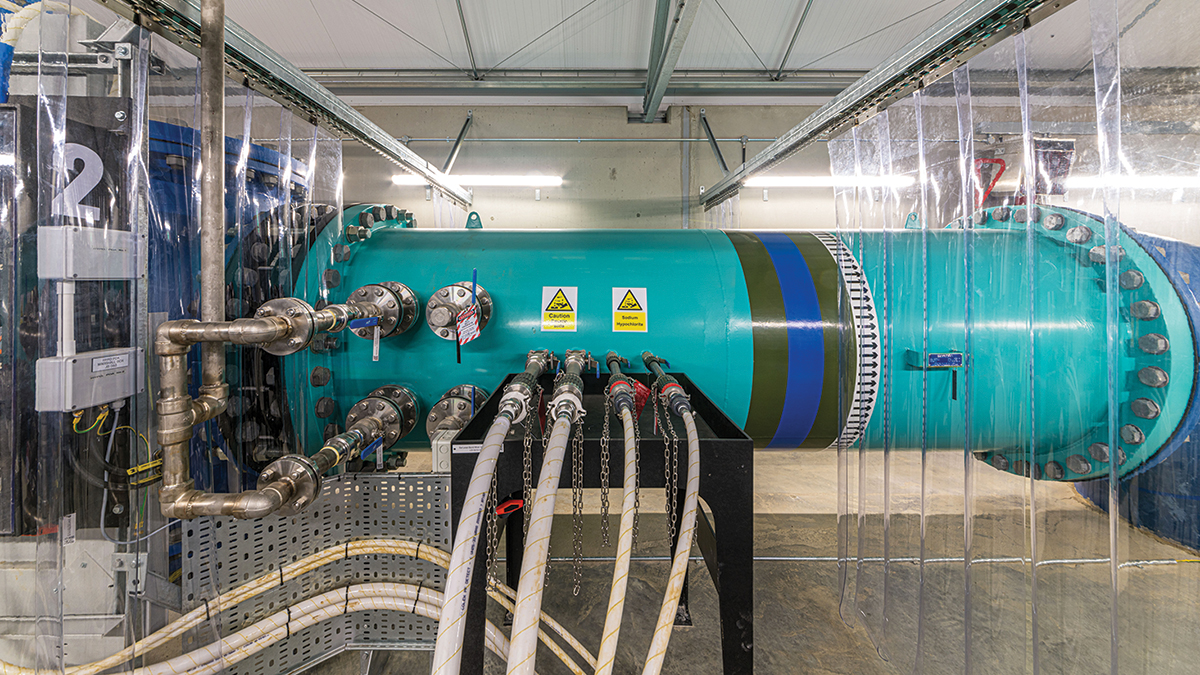
Chemical injection at static mixer – Courtesy of Ward & Burke
Sodium hydroxide dosing: The Larson-Skold Index (LSI) is an empirical scale to measure the corrosivity of water towards mild steel. This is an issue for Affinity’s network that has not seen such a high LSI as it can lead to pipe deterioration and water discolouration. It is a ratio of sulphate and chloride content, to alkalinity content (in the form of bicarbonate and carbonate).
The sulphate and chloride content of the import water is measured using some of Hach’s EZ4000 series analysers, and does not change very much day on day. As such, in order to reduce the LSI, alkalinity is increased by the addition of sodium hydroxide. The alkalinity is measured at the import, as well as after dosing, using a Hach EZ4000 series also. A trim function is coded in to bring the dosing closer to the set-point if it is slightly out. As a bi-product of this dosing however, the pH of the water would increase, and this is where carbon dioxide dosing comes in (see following section).
The sodium hydroxide is stored in bulk quantities at a concentration of 50% w/w. Similar tanks are used, however are of HDPE PE100 construction, also manufactured by Forbes.
The connections and instrumentation are identical to that of the sodium hypochlorite tanks, with the addition of a temperature transmitter and heater. Sodium hydroxide at this concentration has a freezing temperature of +7°C and as a result, the tanks’ contents are maintained at 25°C. The temperature transmitter informs of any drop in temperature before it is too late. It should be noted that the tanks’ stainless-steel fill and outlet lines were all heat traced and lagged also.
Grundfos also manufactured the dosing skid for this chemical. Three DME940 pumps were used in a duty/assist/standby configuration, along with the usual components as above. The same PF Detect hosing was used to get the chemical to the POA cabinet and these lines were heat traced and lagged. Furthermore, the dosing skid and POA cabinet each contained heaters.
Components in the POA cabinet were identical to that of the sodium hypochlorite, with withdrawable stainless steel injection lances in the static mixer to complete the dosing.

(top left) Sodium hypochlorite storage and dosing, (top right) sodium hydroxide storage, (bottom left) sodium hydroxide dosing, and (bottom right) point of application cabinets – Courtesy of Ward & Burke
Carbon dioxide dosing: Working in tandem with the sodium hydroxide dosing, the gaseous carbon dioxide is dosed into the water to bring the pH back down to the set-point. This means that both dosing systems must be working at the same time. It should be noted that the carbon dioxide does not affect the LSI at all.
As with most industrial gas use, the storage vessels are rented from the gas supplier. Nippon Gases are the supplier of carbon dioxide for this project. Delivery and storage is in liquid form, with the storage vessels being insulated with a vacuum layer, akin to a Thermos flask. Vaporisers are also rented from Nippon Gases UK and convert the liquid carbon dioxide into gaseous form for dosing. The gas is heated using trim heaters before the pressure is reduced, prior to going through flow control valves and a flow meter to control quantities for dosing.
Sundon Water Treatment Facility: Supply chain – key participants
- Client: Affinity Water
- Principal designer & contractor: Ward & Burke
- CFD analysis: Wilde Analysis
- Precast concrete: Shay Murtagh Precast
- Electrical installation: Enisca Ltd
- System integration: Riverside Automation
- Concrete repair: Concrete Repairs Ltd
- Stainless steel pipework: ABC Stainless Ltd
- Dosing skids & pumps: Grundfos
- CO2 storage & vaporisation: Nippon Gases
- Water quality monitors: Swan Analytical UK Ltd
- Water quality monitors: Hach
- Water quality monitors: ABB Ltd
- MCC & panels: Motrol (now Profitec)
- Static mixer: Statiflo International
- Permanent generator: Bells Power
- Solar panels: GeoGreen Power
- Chemical filling kiosk: Northern Pump Suppliers
- Chemical storage tanks: Forbes Technologies Ltd
- PF Detect dual contained hoses: FT Water Treatment
- DI pipework: Saint Gobain PAM UK
- Heat tracing & lagging: Jade Insulation
- Heating & ventilation: Air Technology Systems Ltd
- Lightning protection: Bailey International
New buildings & compound
Two new buildings were constructed:
- The chemical building to store chemicals and dosing equipment.
- The control building to house the static mixer, water quality monitors and main MCC.
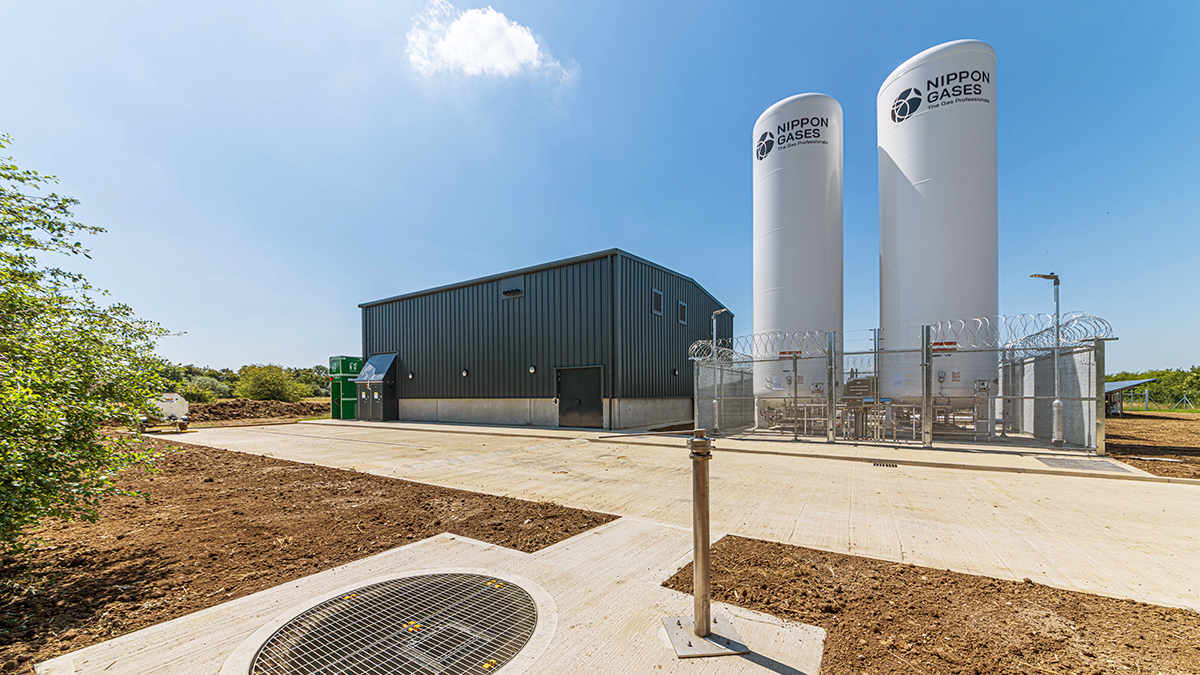
Chemical delivery area & carbon dioxide vessels – Courtesy of Ward & Burke
Despite their differences in size, both buildings were constructed with an in situ RC base, with precast concrete columns, beams and wall panels. Purlins in the chemical building were precast too. The precast concrete avenue was first explored due to a requirement to construct buildings with a 60 year design life. Due to the nature of the off-gassing of sodium hypochlorite degrading metals over time, a steel portal frame construction was not an option. Since concrete walls were required for satisfying security ratings anyway, the precast concrete route was a perfect option. An additional benefit of this design for manufacturing and assembly (DfMA) approach was the considerable reduction of on-site construction risks related to working at height and handling of tall and heavy rebar cages. Other notable benefits included fewer concrete wagons on local roads, less material waste and reduced construction time.
Both buildings were clad with insulated Kingspan cladding to the planning permission colour and security rated doors supplied by Bradbury were installed. Heating and ventilation systems in all rooms were designed and installed by Air Technology Systems, with duty/standby fans in rooms with critical ventilation requirements. Finally, lightning protection systems were installed by Bailey International on all buildings, as well as other plant at risk on site.
A fenced slab was constructed for all the carbon dioxide equipment in proximity to the road for deliveries. Outside the chemical building is the chemical delivery area for the sodium hypochlorite and hydroxide. It features a security rated fill kiosk with connections for each of the tanks, a tepid water emergency shower and blind tank with an interlock valve. This valve’s purpose is to isolate the rainwater drainage system during a tanker discharge to contain any spill. The valve must be shut to release a key to open to the fill kiosk door to prevent human error.
Electrical
A new MCC with ICA section was supplied by Motrol (now Profitec) in collaboration with Enisca Ltd completing the electrical installation. Said MCC was housed in a dedicated room in the control building with a trench beneath it, cast in situ during base construction allowing for easy and tidy bottom cable entry. A remote IO (RIO) panel was installed in the chemical building with an HMI to monitor and control the process.
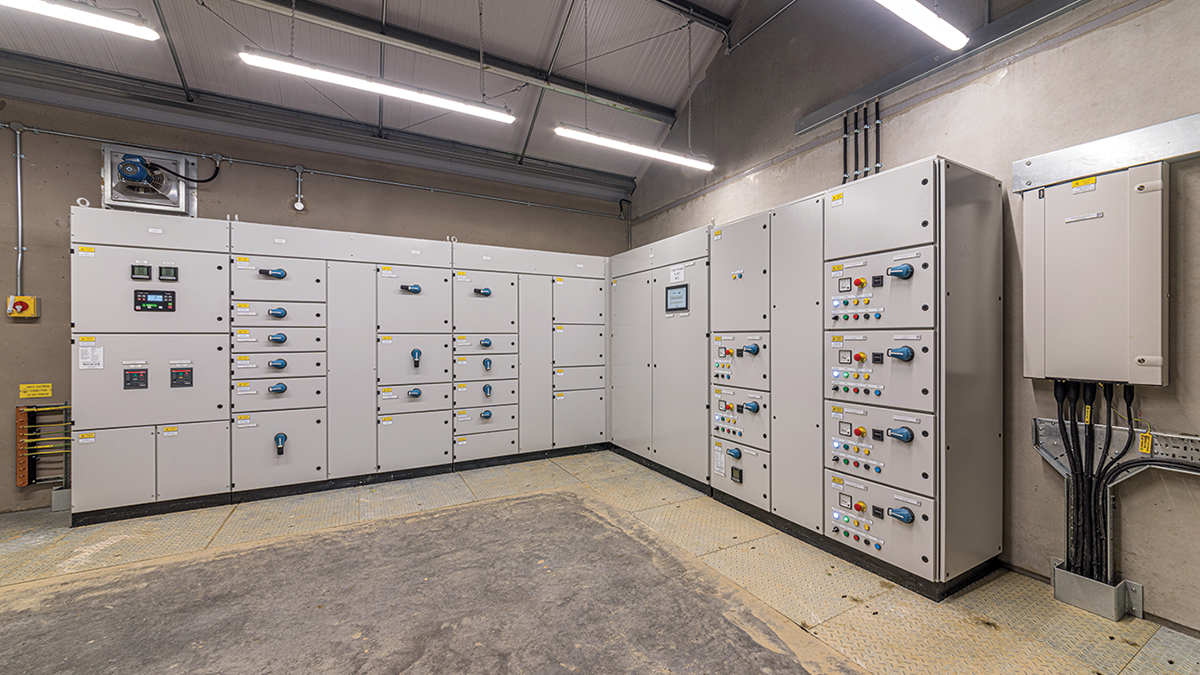
New MCC – Courtesy of Ward & Burke
With Anglian Water owning the pumping station feeding Sundon, there was a focus on ensuring raw signals of reservoir level were provided to both water authorities. In contrast, any other interfaces were minimised as far as reasonably practicable to expedite any future maintenance or works that would have previously required both company’s inputs.
Solar panels were installed to provide power to the MCC at all times, with any surplus required made up by mains power. In the event of a mains power outage, an auto-changeover in the MCC will call on the permanent generator to kick in to keep the site running until mains power is restored.
Commissioning
As of August 2024, the plant is in its commissioning phase, with chemical dosing being brought online after extensive offline testing. In the coming months, Affinity Water will focus on fine-tuning and optimising the plant’s chemical usage to meet network requirements.
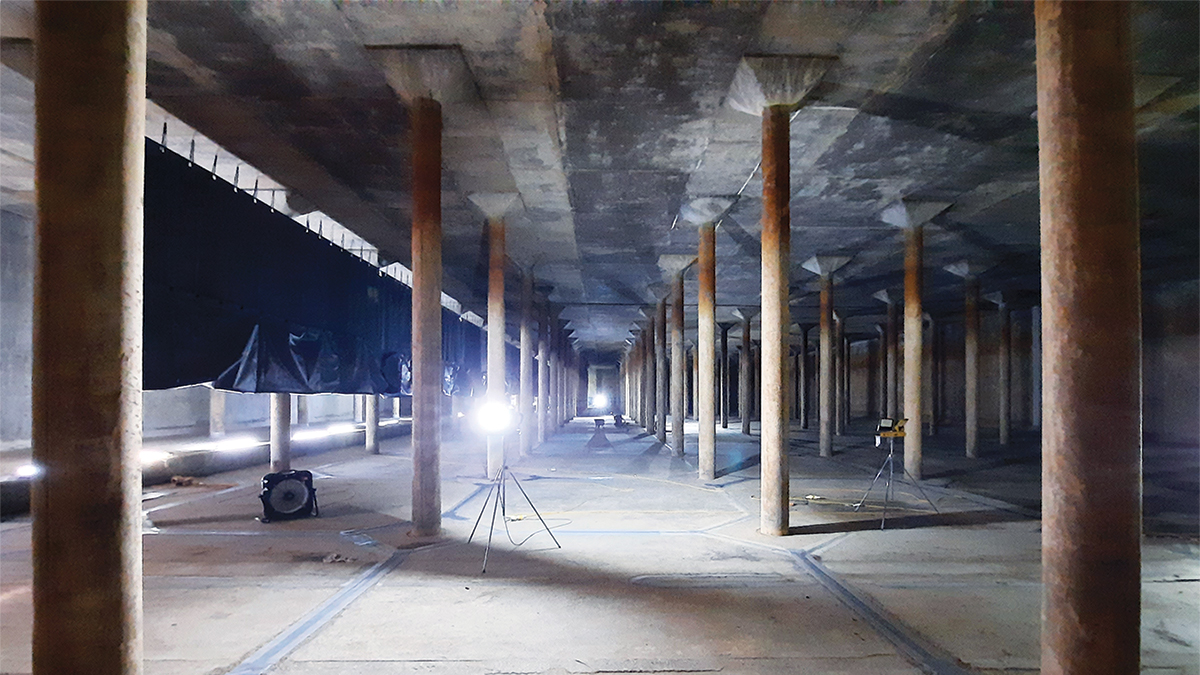
Inside the Sundon Reservoir - Courtesy of Ward & Burke