The Woodlands Water Recycling Centre (2024)
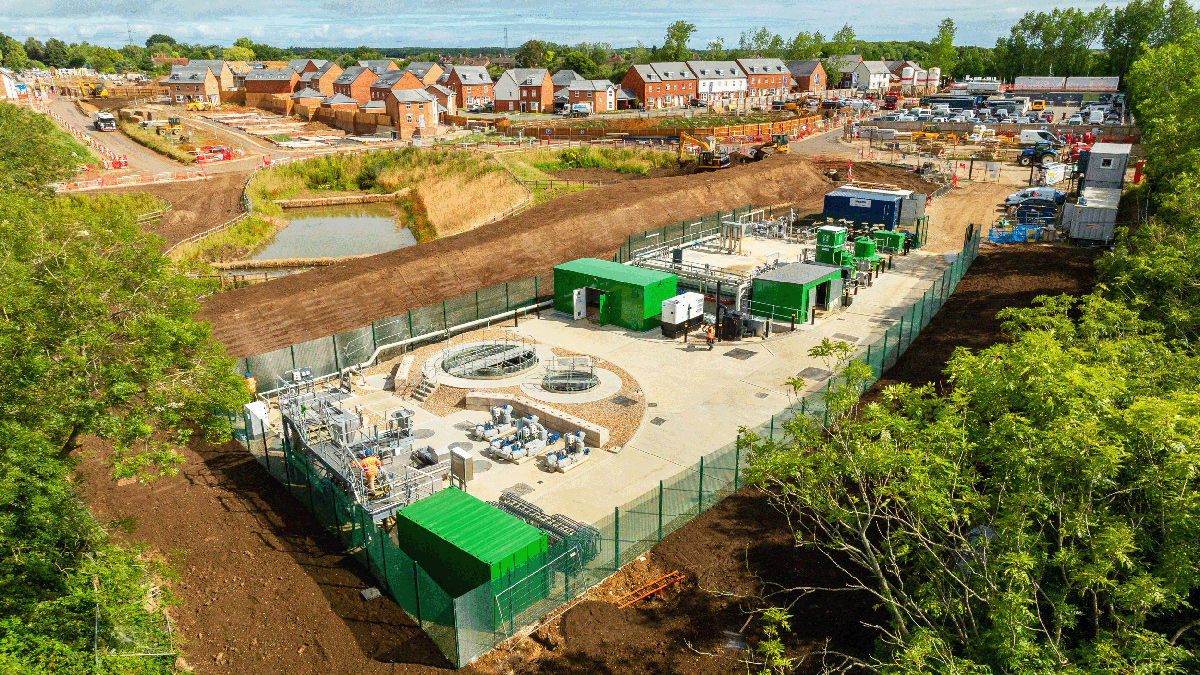
Aerial view of The Woodlands Water Recycling Centre shortly before completion and takeover - Courtesy of EPS Water
Nutrient Neutrality was introduced to mitigate environmental issues caused by nutrient pollution as a result of development, with areas listed by Natural England as protected under the Habitats Regulations. In particular, excess nutrients in the form of nitrogen and phosphorus are being targeted in these areas. In the context of proposed new housing developments, this means that nutrient loadings from additional wastewater from the housing development must be treated to a high standard so that the nutrient load does not exceed that of the original land use.
The Woodlands development
The Woodlands is a development of 456 residential units, comprising houses and apartments, located in Broad Oak, Sturry to the north-east of Canterbury, which has been constructed by Barratt David Wilson Homes.
The site lies within the catchment of the Stodmarsh, a 620-hectare ‘Ramsar’ wetland within the valley of the River Stour, which is designated as a Site of Special Scientific Interest, a Special Area of Conservation and a Special Protection Area. As a result, The Woodlands is subject to the provisions of Nutrient Neutrality for both nitrogen and phosphorus.
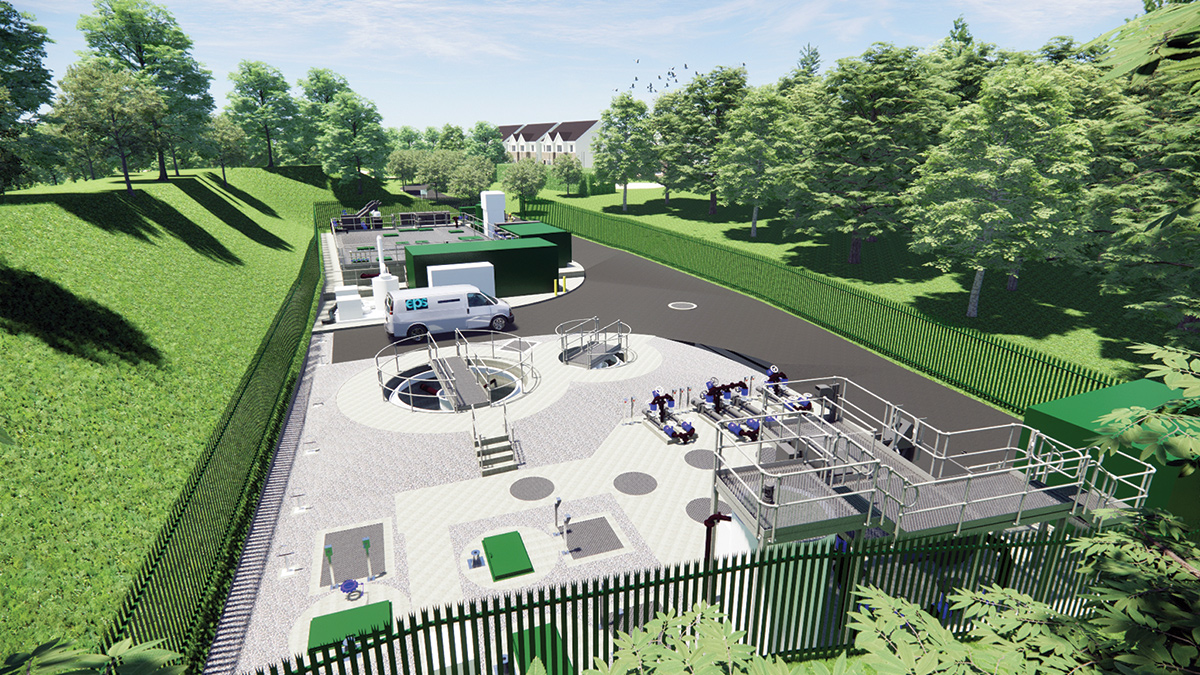
Rendered 3D model of The Woodlands WRC – Courtesy of EPS Water
Project approach
During the planning process, the site was subject to a detailed nutrients assessments with a set of nutrient balance calculations competed to determine the level of intervention needed to achieve neutrality, while taking into account the availability of nutrient credits in the local area.
From this, it was determined that an on-site wastewater treatment solution would be needed in order to achieve the required outcomes. It was decided to propose treatment to the best industry accepted economically-viable standards, and to use SuDS and wetlands features to provide additional treatment where needed to deliver full Nutrient Neutrality.
The proposed discharge standards for the water recycling centre were as follows:
Parameter | Value | Compliance basis |
Population equivalent | 1,094 PE | – |
Biological oxygen demand | 10 mg/l | 95%ile |
Total suspended solids | 15 mg/l | 95%ile |
Ammoniacal nitrogen as N | 1 mg/l | 95%ile |
Total phosphorus as P | 0.3 mg/l | Annual average |
Total nitrogen as N | 15 mg/l | Annual average |
EPS Water was engaged by Barratt David Wilson Homes on a multi-stage contract to design, construct and commission a new turnkey Water Recycling Centre for the site, in order to provide the necessary level of wastewater treatment to achieve Nutrient Neutrality in conjunction with downstream wetlands/sustainable drainage systems (SuDS) infrastructure.
Simultaneously, Barratt David Wilson Homes engaged an operator to apply for an appointment under OFWAT’s New Appointments & Variations (NAV) process, to vary the operator’s licence to includes The Woodlands development.
This variation allowed the operator to own and operate the plant in preference to the regional water and sewerage company (Southern Water). The operator subsequently made an application to the Environment Agency for a discharge permit for the plant in line with the above parameters.
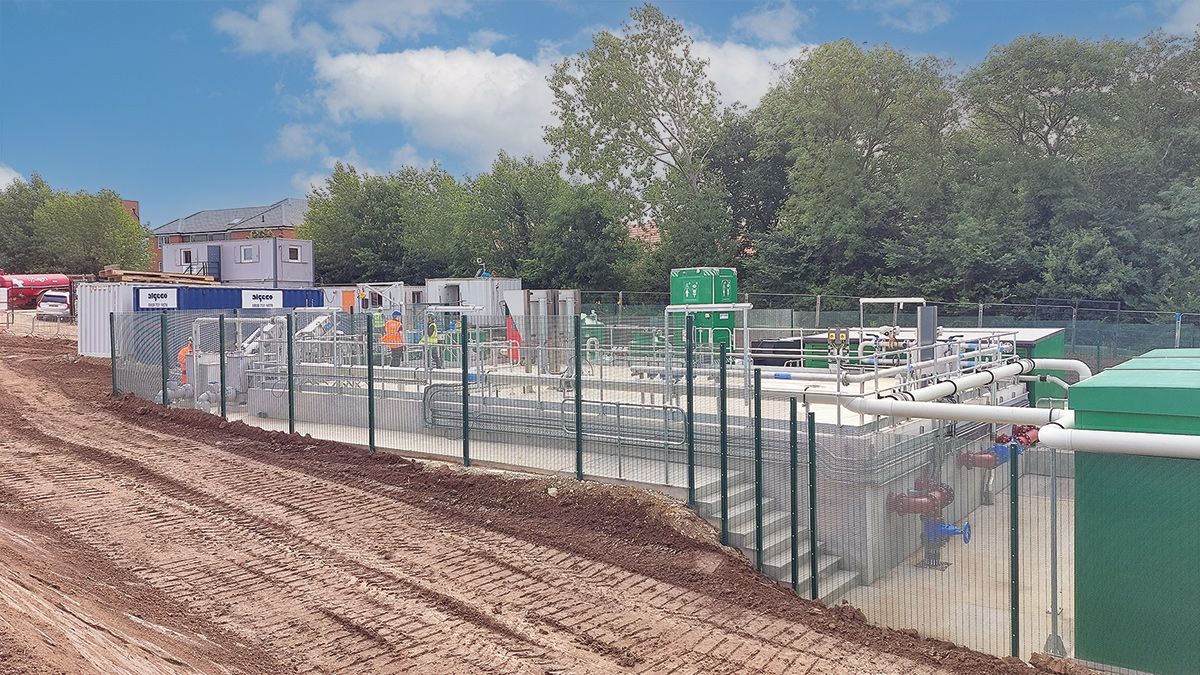
View of the main MBBR treatment block – Courtesy of EPS Water
In developing an outline design for the Water Recycling Centre some other key requirements and constraints had to be taken into consideration, as follows:
- Process tanks and structures had to be kept as low as possible to minimise visual impact – a target maximum height above ground of 2.5m was agreed.
- Provision was to be made for a substantial visual screening bund along the north-western boundary of the site.
- Odour control was to be provided to the main potentially odour-generating elements within the treatment process.
- Noise control measures were to be provided to minimise potential noise arising from air blowers, pumps, screens, etc.
- Opportunities to minimise operating costs were to be identified and adopted where possible.
- Provision was to be made for remote operator interaction.
Key design aspects
The selection of a moving bed biofilm reactor (MBBR) process followed a detailed optioneering exercise which focused on the key objectives and constraints of the project. These included the need for denitrification, carbon removal and nitrification, the ability to operate the plant at low loadings initially, footprint constraints, visual impact considerations and low sludge production rates. At the scale proposed, MBBR was found to be the preferred technology over and above six others that were assessed.
Care was taken in the overall design to allow regular operation and maintenance to be completed using a single operator whenever possible. Particular care was taken to minimise operator input, as the site will not be staffed permanently but instead monitored remotely. Instrumentation was carefully selected to provide good visibility of performance and a detailed control philosophy was written to reflect the robustness of the MBBR system.
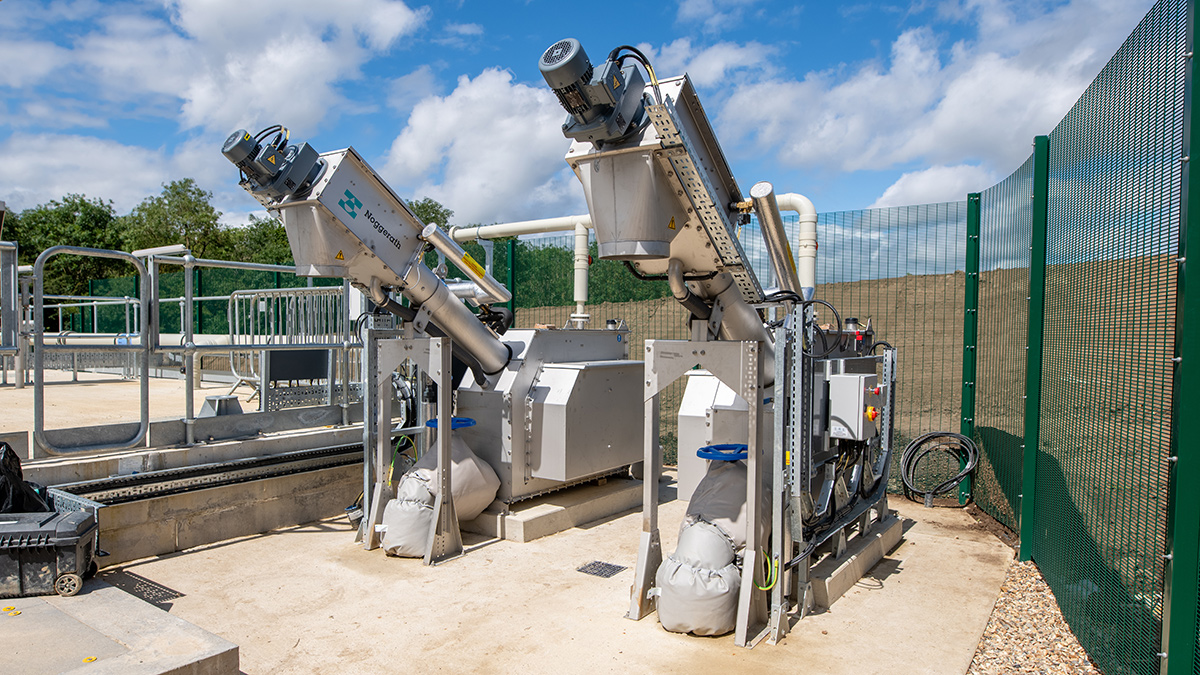
Noggerath® inlet fine screens at The Woodlands WRC – Courtesy of EPS Water
The use of advanced digital design tools enabled EPS Water to plan, develop and consult on the design in a fully 3D environment, actively collaborating with suppliers and sub-contractors along the way. Rendered imagery and fly-through animations were used to support client engagement and design reviews.
The models were then uploaded to Autodesk BIM360 Construction Cloud, to facilitate smooth, real-time design management of construction and design changes as site work progressed.
The Woodlands WRC: Supply chain – key participants
- Main design-build contractor: EPS Water
- Process design: WEW Engineering Ltd
- Civils & electrical design: Robert Walpole & Partners
- Civils sub-contractor: Cleantech Civils
- Electrical installation: SRE Services
- Inlet screens: Aqseptence Group (Noggerath®)
- Precast MBBR tanks: FP McCann
- MBBR media: Warden Biomedia
- MBBR media screens: Aqseptence Group (Johnson Screens)
- Aeration diffusers: ATAC Solutions
- Aeration blowers: Aerzen Machines
- Chemical dosing cabinet: EPS Water
- Chemical storage tank: Flocktons TVP
- Safety showers: Aqua Safety Showers International Ltd
- Clarifiers: KEE Process Ltd
- Tertiary solids removal: Nuove Energie
- Tertiary solids removal: Eliquo Hydrok Ltd
- Submersible pumps: Xylem Water Solutions
- Submersible mixers: Sulzer Pumps Wastewater Ltd
- Flocculation mixer: Belmar Technologies
- Progressive cavity pumps: SEEPEX UK Ltd
- Odour control: CMI John Cockerill
- Kiosks: Quinshield Ltd
- Kiosks: AGS Noise Control
- Access covers: Technocover
- Washwater booster set: Pedrollo Distribution
- MCC & ICA: Profitec Solutions
- PLC/HMI & instruments: Siemens
- PLC/HMI & instruments: Hach
- Emergency generator: P&I Generators Ltd
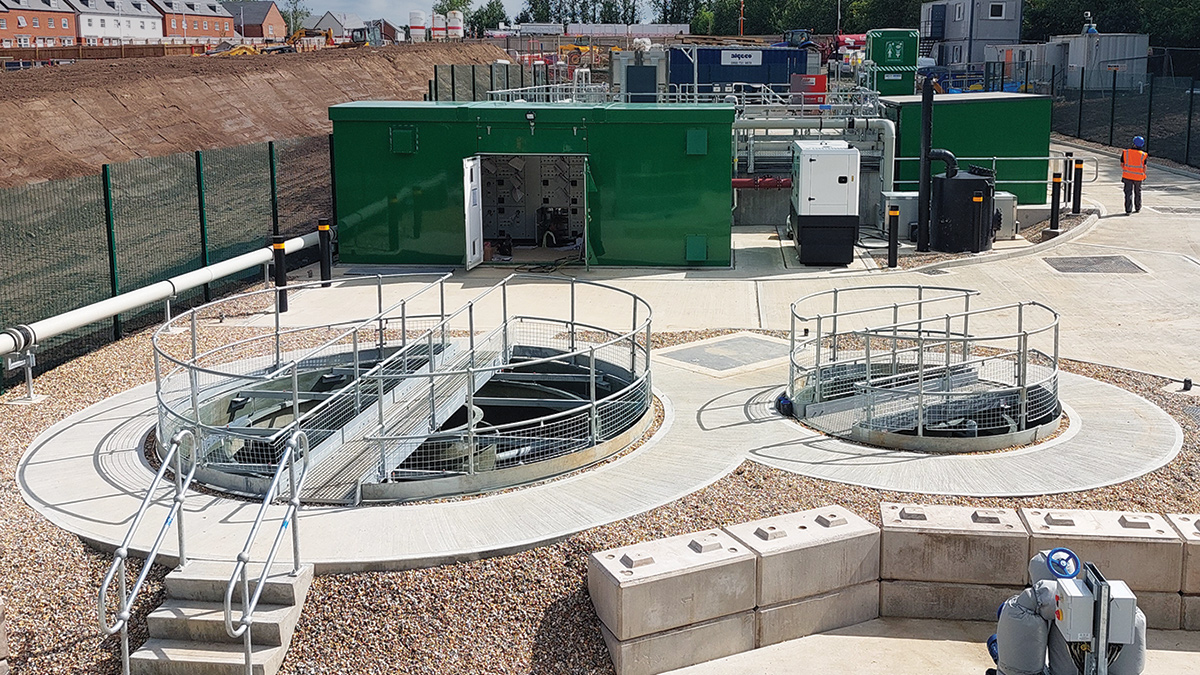
View of the clarifier, sludge thickener & MCC kiosk – Courtesy of EPS Water
Project scope
The Woodlands Water Recycling Centre was designed to accommodate gradual increase of flows and loads, which comes as the housing development phases are completed, up to a total population equivalent of 1,094 (PE).
This includes a design to ensure that adequate treatment could be provided to meet the consent during commissioning with initial low loads prior to houses being occupied.
The design of the new The Woodlands Water Recycling Centre at Broad Oak comprised the following:
- Inlet pumping station.
- Dual inlet fine screens.
- Balance tank and forward feed pumping station.
- Three moving bed bio-reactors (MBBRs) for denitrification, carbon removal and nitrification including recirculation pumping.
- Aeration system with process air blowers.
- Ferric sulphate chemical dosing.
- Sodium hydroxide chemical dosing.
- Final settlement tank.
- Tertiary solids removal plant.
- Final effluent pumping station with discharge into attenuation ponds.
- Sludge thickening tank.
- Sludge storage tank.
- Odour control system.
- Motor control centre.
- Emergency generator.
- Site office building.
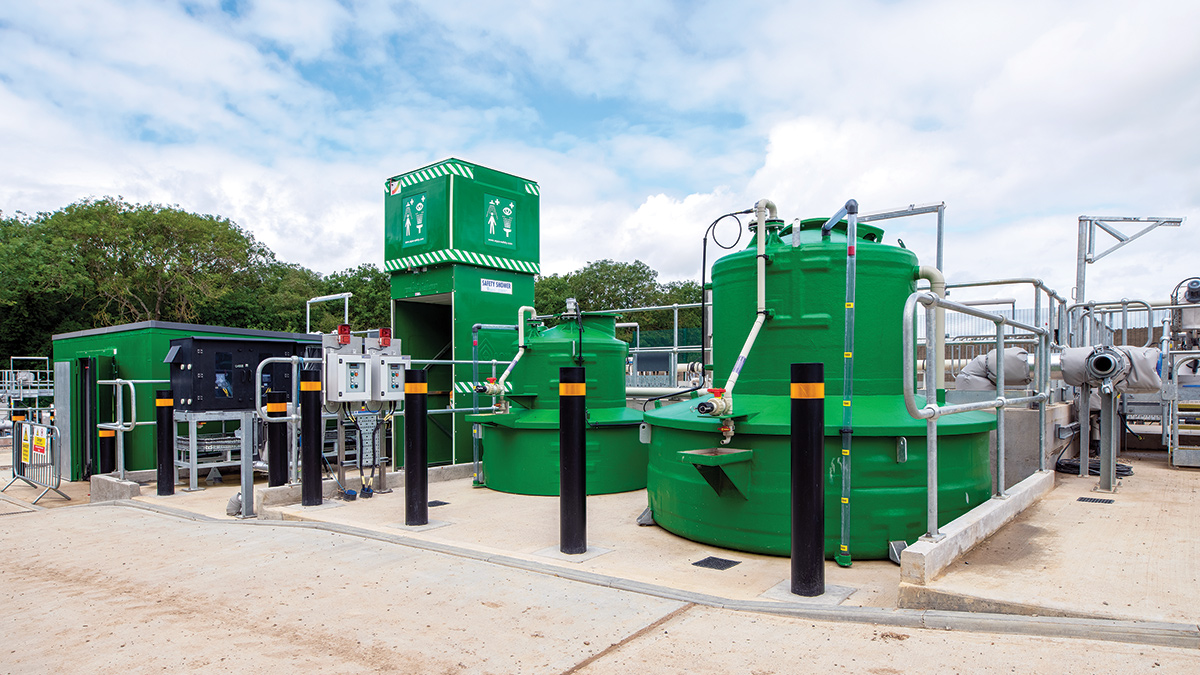
Chemical dosing plant at The Woodlands WRC – Courtesy of EPS Water
Raw wastewater gravitates from the housing development foul network to the inlet pumping station. Pumped flows from the inlet pumping station are screened via two screens in a duty/duty arrangement (size for duty/standby when needed), with screenings compacted and discharged into dedicated bins.
Screened wastewater then gravitates into the balance tank, where a submersible mixer keeps influent mixed for partial hydrolysis of wastewater prior to secondary treatment. Forward feed submersible pumps in a duty/standby arrangement transfer this to the first stage moving bed bio-reactor tank. The first stage MBBR is under anoxic conditions to promote denitrification, along with a nitrate return from the settlement tank. Additional alkalinity is provided by an EPS sodium hydroxide chemical dosing system. A submersible mixer operates continuously to allow a homogeneous mixture to occur.
Flow then gravitates to the second stage MBBR for carbon removal and then onto the third stage MBBR for nitrification. These reactors are aerated by a dedicated blower and are fitted with coarse air diffuser grids. Media screens are fitted on the outlet of the reactor tanks to prevent media carry-over into the later treatment stages.
A settlement tank receives gravitated flows from the third stage MBBR for solids removal. Chemical precipitation of phosphorus using ferric sulphate, which is dosed into the third stage MBBR, also promotes suspended solids removal. Treated effluent overflows the outlet weirs and is pumped, via the tertiary feed pumping station, to the flocculator tank.
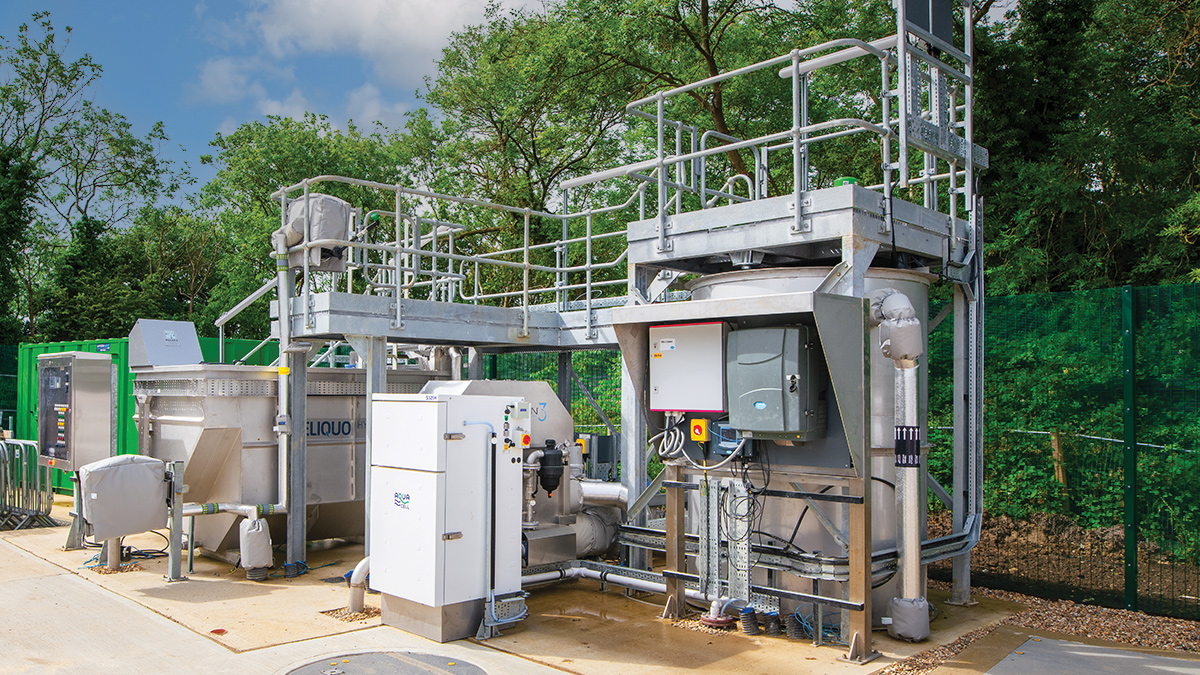
Tertiary solids removal plant – Courtesy of EPS Water
Tertiary solids removal is achieved by either a Mecana Pile Cloth Media Filter or a Nuove Energie Ultrascreen Generation 3 Disc Filter, set up in a duty/standby arrangement. These filtration units were selected due to their high performance in the removal of fine suspended solids. Together with a further ferric sulphate dose, these will bring the suspended solids and total phosphorus concentrations below the stated consent limit.
Finally, final effluent from the tertiary filters gravitates to the sampling chamber and onto the final effluent pumping station. Pumped final effluent discharges into a combined storm water attenuation pond and constructed wetlands system within the site’s SUDS network, before passing to the receiving stream.
Project delivery
Construction of The Woodlands WRC began on site in March 2023, with EPS Water taking over the relevant part of the Barratt David Wilson Homes site as principal contractor for the water recycling centre. The civil works were challenging due to extended spells of wet weather combined with some unforeseen ground conditions and the extremely constrained site footprint. Notwithstanding this, the construction works continued broadly in line with the agreed programme.
Completion and takeover of the site took place in August 2024 with commissioning of the works progressing immediately thereafter. Initially fed by tankers, the site started receiving all flows directly from the housing development in early September 2024.