Mogden STW (2017)

(left) Mogden STW and (right) CHP flue with associated equipment on gantry - Courtesy of eight2O
Mogden Sewage Treatment Works is the second largest in the UK. The first phase was built between 1931 and 1935 at a cost of £1.7 million and covers an area of 55 hectares. The facility treats wastewater from a population equivalent of 1.9 million across a 60 square mile catchment area of north and west London. The works has subsequently been extended and currently the treatment capacity of Mogden STW meets the needs of London’s expected population growth by 2021. This paper looks at two recent projects completed in early 2017; CHP enhancements and the air main resilience project.
CHP enhancements
Project drivers: The existing combined heat and power (CHP) plant comprised 4 (No.) 2.2MWe dual-fuel Mirrlees Blackstone engines that had been installed in 1989. Issues included:
- The CHP plant had reached the end of its service life.
- The CHP reliability was poor, with three of the four engines operating continuously and the fourth engine offline for regular service and maintenance intervals scheduled every 10,000 hours.
- The engines were installed within the existing power house building, causing noise pollution well above 110dBA.
- The dual-fuel engines ran on a diesel ignition process and the emissions were not as clean as the modern spark ignition counterpart. Efficiency was low in comparison to more modern engine technology.
- Sourcing genuine parts was also problematic.
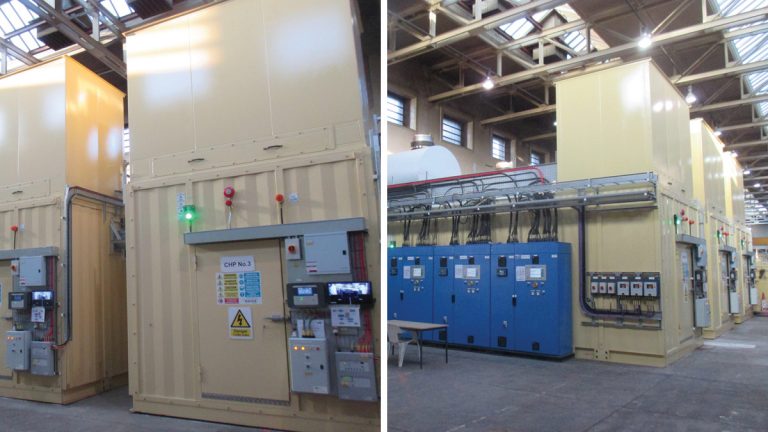
(left) End view of new CHPs and (right) side view of CHPs with control panels – Courtesy of eight2O
New CHP plant: Edina Group was contracted to supply, install and maintain 3 (No.) 2MWe MWM TCG 2020 V20 biogas reciprocating CHP engines as part of the upgrades to the existing CHP system.
The £24.6m CHP enhancement project improved serviceability and power generation, whilst reducing operational costs and the sites environmental impact. It was installed in an area adjacent to the existing CHP plant, allowing for the this to be kept operational during installation, commissioning, and performance testing of the new plant.
A new flue stack was erected to comply with the chimney heights regulations, and coolers from excess heat dump and intercoolers were all installed outside the 80-year old power house. Similar to the biogas line, the hot water circuit was interrupted and a diversion circuit was created in the basement of the power house so that the heat from the new engines could be easily diverted into the boilers feeding the pasteurisation process whilst still maintaining the heating from both the old CHPs and the boilers.
By containerising the CHP engines in individual acoustic enclosures, and the shutting down of the old CHP engines, the noise level within the powerhouse has significantly reduced, with the Edina CHP engines operating at 65dBA.
Mogden STW CHP Enhancements: Supply chain – key participants
- 3 (No.) CHP units: Edina
- 2 (No.) HV transformers & 3 (No.) Fault limiting current reactors: Winder Electric
- 1 (No.) HV Panel S8: Siemens
- 1 (No.) LV panel D91: Boulting Group
- 1 (No.) Flue stack and ducting: James Engineering
- 1 (No.) Siloxane Filter: Parker PpTek
- 1 (No.) Pressure Reducing Station: Active Flow
- 3 (No.) Intercooler radiators: Edina
- 3 (No.) Dump radiators: Edina
- Electrical installation: FSDL
- Support gantry (external): R&B Engineering
- Biogas pipework: Franklyn Yates & Edina
- Hot water pipework: Franklyn Yates
- Piling: Screw Fast
- PMS upgrade in incorporate new CHP and remove existing CHP: Brush
Work started on site on 12 November 2015 and the CHP station was providing beneficial use on 1 February 2017. In April 2017, the CHP station finished its 28-day reliability trial period and is showing some significant results reported by Thames Water. In its first few weeks of operation, reports suggest that the CHP has generated a 47% increase in electricity when compared to the same period in 2015. Although the energy generated does vary week on week, it potentially represents a weekly cost reduction of £123,000 for Thames Water.
Air main resilience project
Project drivers: The key driver for the Mogden STW Air Main Project is the reduction of the significant business risk associated with the life-expired asset, which is one of Wholesale Wastewater’s Top 3 asset risks.
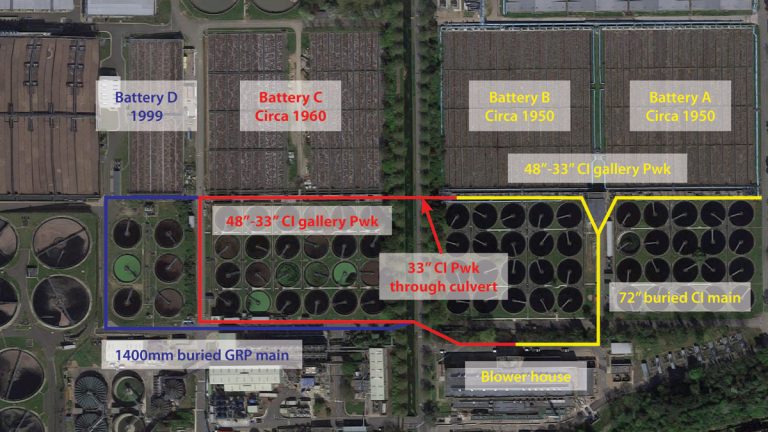
Mogden Air Main Replacement Project – final report October 2012 – Courtesy of Black & Veatch
The section of existing air main that is of most concern is an 80 year old cast iron main (coloured yellow in the schematic above), which is currently showing significant evidence of early failure with a risk of total failure.
This air main is a single point of failure for four of the five ASP batteries (A, B, C and D). Loss of aeration for greater than 45 minutes will lead to a final effluent compliance failure which will negatively impact the following performance commitments:
- SB1 WWNI Asset Health.
- SC2 Consented and Unconsented Pollution Incidents.
- SC3 Discharge Compliance.
These possess a significant (£10-£20m) regulatory, environmental and reputational penalty.
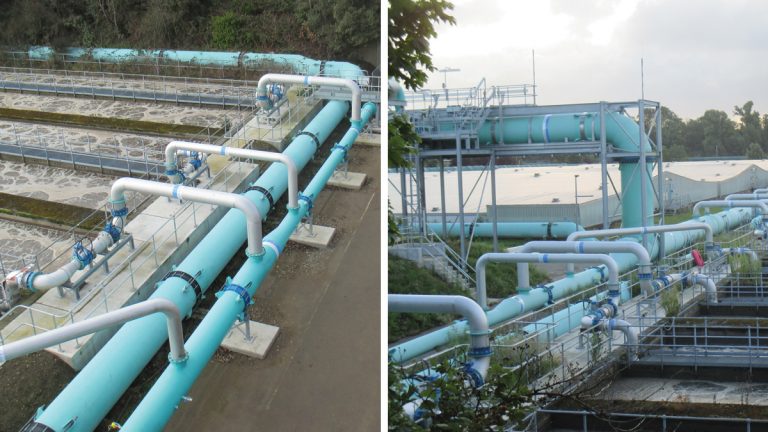
(left) Air pipework feeding lanes west of road crossing and (right) air main distribution pipework road crossing to lane header pipework – Courtesy of eight2O
In addition, six of the eight existing blowers are past their design life and have become very difficult and expensive to maintain. Spare gearbox parts need to be reverse engineered as they are no longer commercially available. Blowers for Batteries A, B, C and D are all housed in the main blower house which is another single point of failure in the event of fire.
Mogden STW Air Main Resilience Project: Supply chain – key participants
- 4 (No.) HV blowers: Howden
- 2 (No.) HV and 2 (No.) LV transformers: Winder Electric
- 1 (No.) HV and 1 (No.) LV panel: ATG
- Electrical installation: FSDL
- 1 (N0.) MCC kiosk: Morgan Marine
- Kiosk access stairs & platforms: Step on Safety Ltd
- Air main inc. supports: Franklyn Yates
- Piling: Screw Fast
- Civil Infrastructure: Ward & Burke
- Electrical installation FSDL 1 (No.) PMS panel and PMS interface with C726 (CHP project): Brush
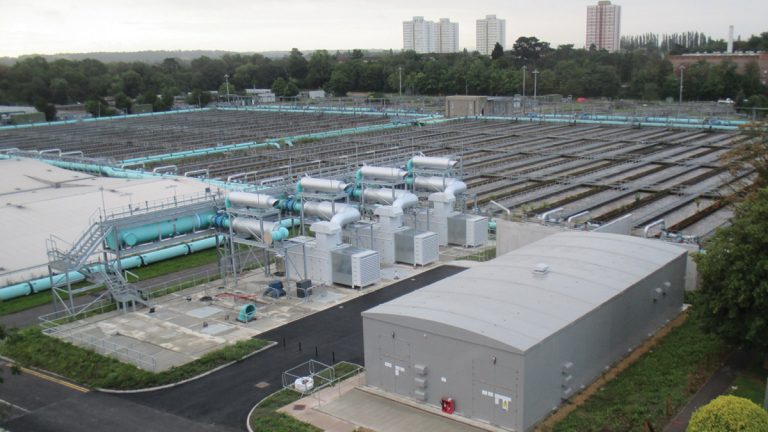
Air Main blower station (blowers, MCC and switchgear kiosk, air distribution header main) – Courtesy of eight2O
Key scope of work
The project has provided a new blower installation and dedicated air main for Batteries A and B, removing these batteries from the life expired ring main, which is a single point of failure.
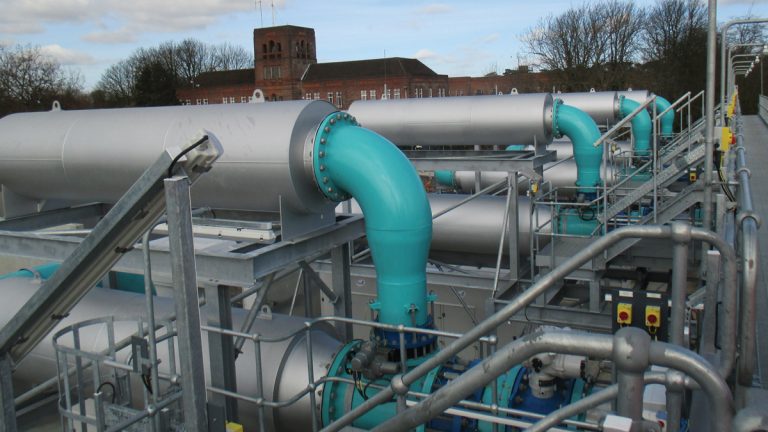
High view of air main blowers distribution pipework, including silencers – Courtesy of eight2O
Blowers are located outside adjacent to the administration building and north of the lanes and provided with weatherproof acoustic enclosures. This will result in Batteries A and B having dedicated new blowers and new air main. This has removed the single point of failure that currently exists by having the blowers for Batteries A, B, C and D all located in one location (the Power House Blower House). Batteries C and D air main is due for replacement in AMP7 with a new blower location and air main, thereby making the full air main redundant. Until this is constructed risk of aeration failure will remain for batteries C and D.
The £17.6m air main resilience project started on site on 18 November 2015 and the blowers started supplying air to all of battery A and B on 26 April 2017.