Lletty Brongu & Ruthin STWs (2021)
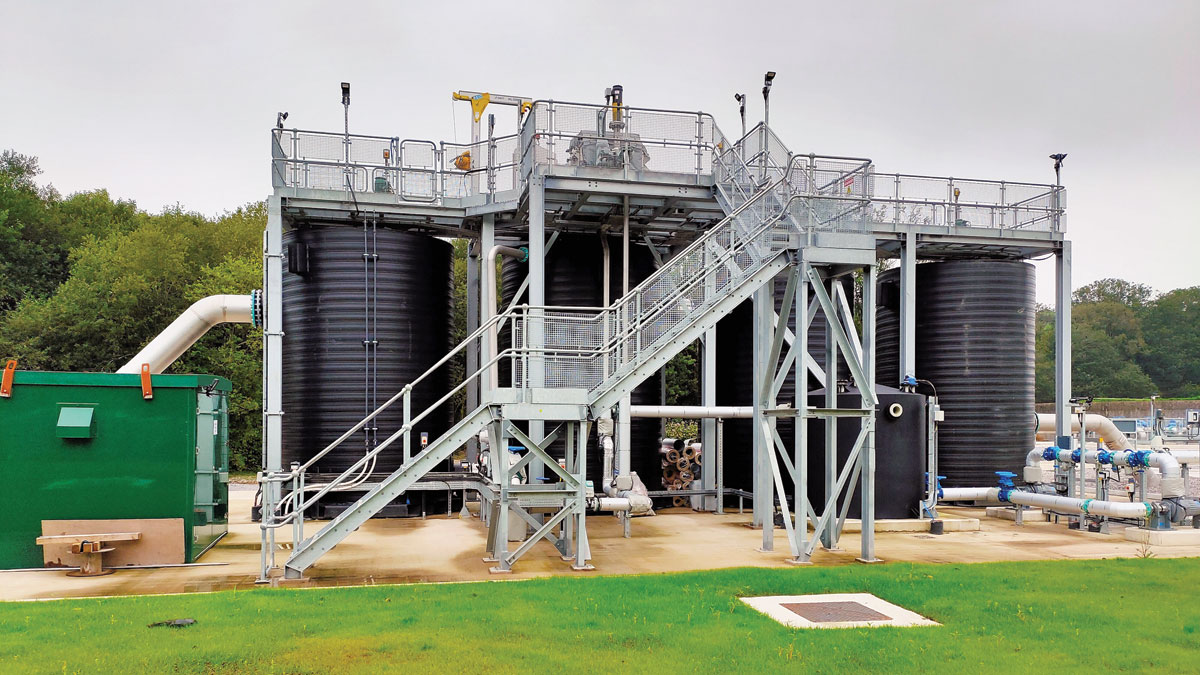
CoMag® system reaction tanks at Lletty Brongu STW - Courtesy of Evoqua Water Technologies
Welsh Water raised a programme of quality schemes for completion in AMP6 to address tightening of phosphorus permits set by Natural Resources Wales (NRW) at ten wastewater treatment works. Some of the sites in the programme were subject to a new total phosphorus (TP) permit of 0.5 mg/l T-P and required the installation of a new treatment process. Following a rigorous commercial, technical and risk assessment process by Welsh Water and their Capital Delivery Alliance partner Mott MacDonald Bentley (MMB), two of the schemes adopted Evoqua Water Technologies unique CoMag® ballasted clarification system, that would provide enhancement of the existing assets on site to achieve these new improved phosphorus permits.
The existing wastewater treatment works (WwTWs)
Located just outside Maesteg near Bridgend in Glamorgan South Wales, the Lletty Brongu WwTW treats a population equivalent of approximately 21,000. The works is comprised of primary settlement, tricking filters and humus settlement tanks.
Ruthin is the county town of present-day Denbighshire in North Wales and a community in the southern part of the Vale of Clwyd. The conventional biological filtration WwTW serves a PE of approximately 6,500 with an average treatment flow of 29 l/s.
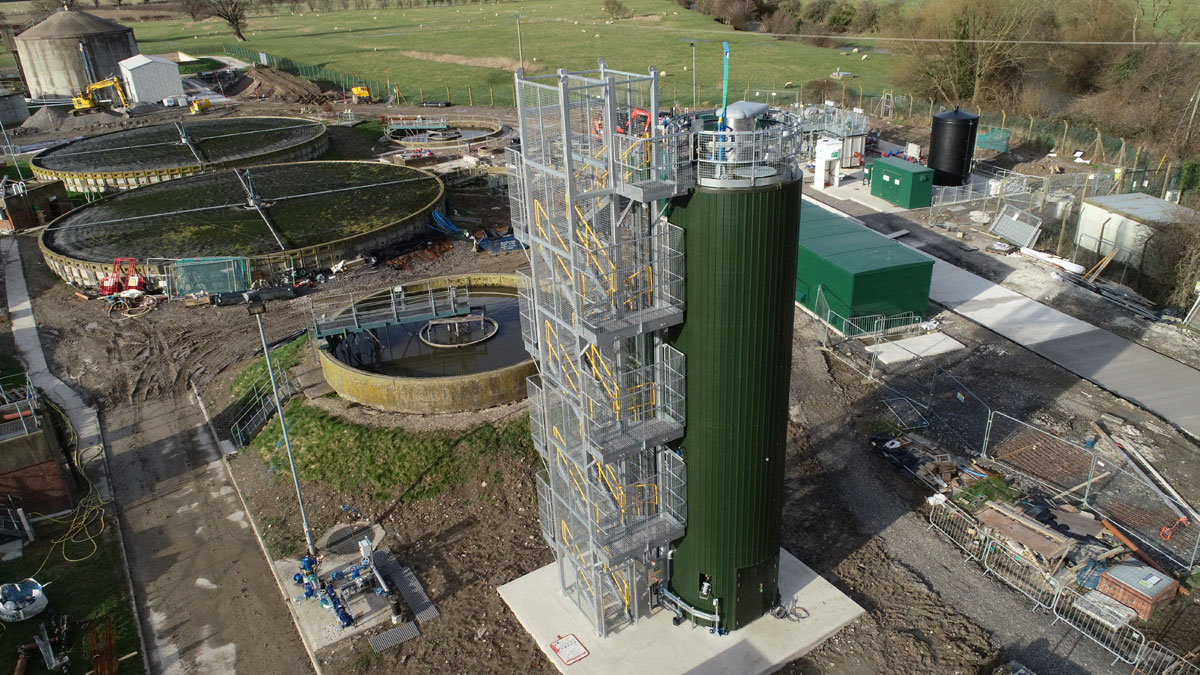
Ruthin sodium bicarbonate powder storage silo – Courtesy of MMB
The solutions implemented
To achieve the new phosphorus permit, primary and humus stage coagulant/chemical precipitation dosing in the form of ferric sulphate was introduced at both sites, along with the addition of the CoMag® system to enhance the secondary settlement stage. Welsh Water and MMB worked to develop a standardised approach to the chemical dosing pump and storage system to lever efficiencies in the design, procurement, construction and commissioning of these rigs across several other sites.
Ferric sulphate consumes alkalinity. To ensure a sufficient alkalinity buffer during process treatment and in the final effluent, a sodium bicarbonate dosing system was introduced after the primary settlement stage. MMB and the supply chain (Rospen at Ruthin and Flexicon at Lletty Brongu) developed bespoke solutions for each site.
At Ruthin WwTW, this consisted of a large powder storage silo, a measuring device more often used in the food industry to ensure accurate dosing and an eductor to mix the powder with carrier water to form a weak slurry to be pumped to the point of application. At Lletty Brongu WwTW, sodium bicarbonate powder is dosed directly into the primary effluent stream.
In order to establish the range of conditions the new CoMag® plant would have to deal with, MMB undertook calculations to estimate population growth to the 2035 design horizon and the effect of the primary dosing on total suspended solids and other parameters.
Other features built on the sites included new sludge tanks to handle the additional sludge generated, automated sludge pumping systems, wash water booster sets and quality instruments to measure pH, ortho-phosphate, iron and turbidity.
A batch procurement approach was developed to ensure purchasing efficiencies and repeat design, build and commissioning activities were realised across all ten sites. A procurement team was convened, consisting of Welsh Water and Capital Delivery Alliance staff and specialist groups were tasked with standardising designs and specifications for these batch wide elements.
The CoMag® treatment system
The CoMag® treatment system is a simple, innovative and proven technology for the removal of solids, heavy metals and other particulate or precipitated contaminants. Since its development in 2007, the CoMag® system has been utilised as a process that can be used to remove phosphorus as a tertiary treatment step on a wastewater treatment works prior to the treated effluent entering the local water course.
The CoMag® system is based on conventional coagulation, and flocculation, but uses an innovative ballast material which differentiates the process from other technologies. The ballast material is magnetite (Fe3O4), which is a fully inert, high specific gravity (5.2), finely ground, iron ore.
Due to its nature and through simple mixing, the magnetite is infused into the metal hydroxide floc, thereby significantly increasing the density of the floc. When the magnetite infused flocs are introduced to the CoMag® clarifier, the flocs settle typically ten times faster than conventional flocs. Rapid settling enables CoMag® systems to employ much smaller and less expensive clarifiers.
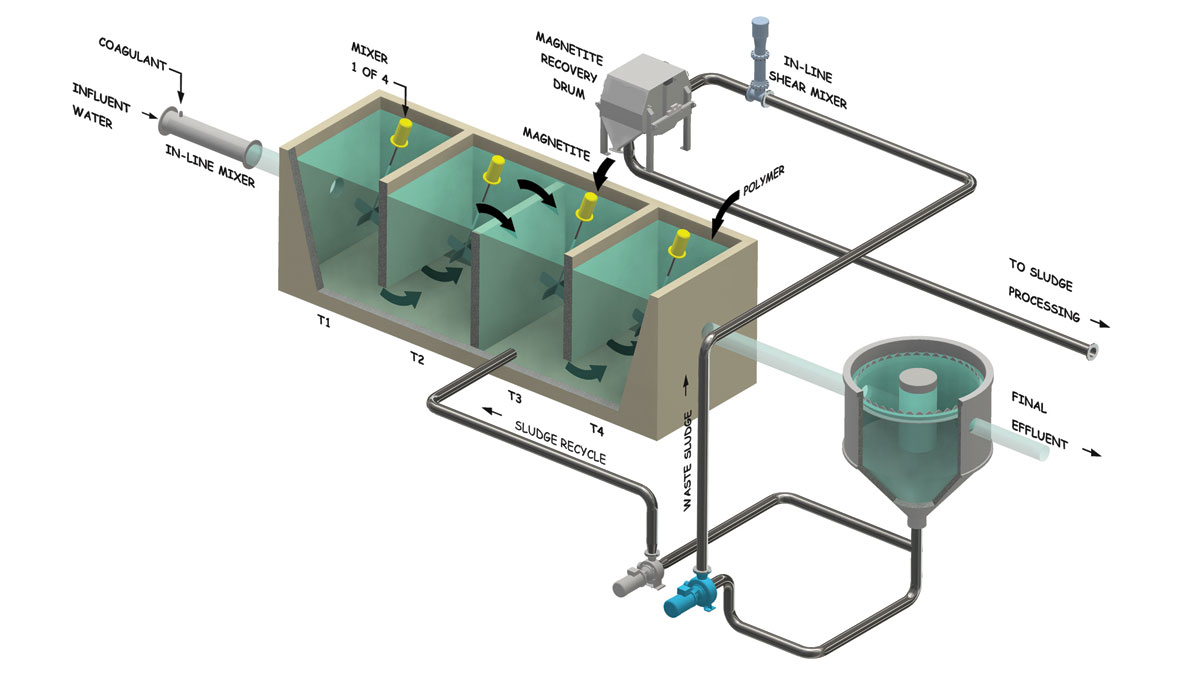
Summary of CoMag® treatment process – Courtesy of Evoqua Water Technologies
Critical to achieving the low phosphorus quality, CoMag® system recycles settled solids from the clarifier back to the reaction tanks to increase nucleation sites, enhance precipitation kinetics and promote floc sweep. The result is superior solids removal and more efficient chemical use.
The magnetite ballast is recovered from the waste sludge magnetically with little energy consumption and returned to the treatment system with very little magnetite loss, thereby assisting to keep consumable and operating costs minimal.
The CoMag® system is a clarification process that separates with gravity rather than with a ‘filtration barrier’, offering a simple, reliable, and highly effective process that easily handles highly variable flows and solids loads.
CoMag® system application at Lletty Brongu and Ruthin WwTWs
Unlike conventional tertiary treatment, for both these sites the CoMag® system was incorporated between the existing trickling filters and associated humus tanks. The effluent leaving the existing trickling filters was directed to the CoMag® system reaction tanks, then returned to the existing humus settlement tanks. Prior to the CoMag® reaction tanks, ferric sulphate coagulant is added to react with the soluble ortho-phosphorus present to form insoluble ferric phosphate. The coagulant also coagulates small particles by sweep floc/charge neutralisation thus enabling the effluent total suspended solids (TSS) to be so low.
Magnetite was added during commissioning and is then recycled back to Tank 3 via the recycle pumps where it embeds in the forming flocs producing heavy particles. In Tank 4, the addition of polymer binds together the smaller flocs to maximise the separation of solids from the effluent prior to the clarifier. The addition of polymer ensures an excellent effluent quality can be achieved.
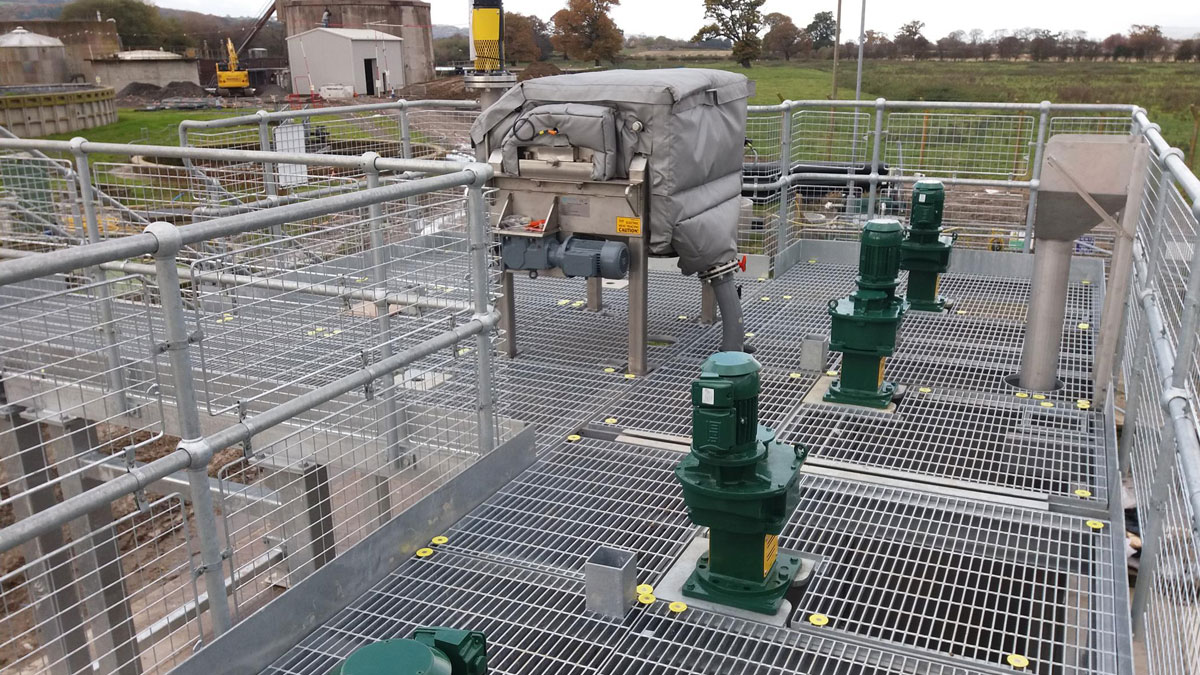
Magnetite recovery drum and mixers from the top of the reaction tanks at Ruthin – Courtesy of Evoqua Water Technologies
In these cases, the water containing the embedded magnetite laden flocs are directed to one of the existing humus tanks that acts as the CoMag® clarifier system. As the settling of the solids is now so efficient these tanks are now oversized for a CoMag® clarifier system but this saves the addition of new clarifiers and reuses the existing asset on site.
This was an innovative approach for this technology, which is normally added as a tertiary stage process. As CoMag® system technology relies on separation by gravity, it does not produce any backwash which meant that additional settlement capacity did not have to be added at these sites. Building less and maximising the use of existing assets, results in lower embodied carbon. In addition, optimisation of the chemicals can be used to target particular TSS and P effluent levels, so the technology has the capacity and ‘built-in resilience’ to achieve lower permit limits which may be enforced in the future.
However, integrating a new process into an existing live treatment stream does not come without its difficulties and MMB and Evoqua’s commissioning teams and Welsh Water’s Operational teams all worked closely together to coordinate shutdowns and develop robust commissioning plans.

CoMag® system reaction tanks at Ruthin – Courtesy of Evoqua Water Technologies
Project execution
Following the engagement into contract with Evoqua Water Technologies in the UK, a collaborative team approach with MMB and Welsh Water at the respective sites resulted in an agreed design for the agreed scope. Following the design phase, the respective equipment was procured and supplied on time. Careful consideration was given to the site access and minimising the site installation time.
Supply chain – key participants
Lletty Brongu STW
- Principal contractor & designer: MMB
- Geotechnical investigation: Geotechnics Ltd
- Enhanced solids removal process: Evoqua Water Technologies (Xylem Water Solutions)
- Ferric sulphate dosing: Colloide Engineering Systems
- Polymer dosing: NPS Group
- Sodium bicarbonate dosing: Flexicon
- MCCs/control panels & systems integration: GPS Group
- Electrical installation: PCS
- Mechanical installation: Samatrix
- Humus tank modifications: DD Engineering
- Temporary solids/liquids separation: Siltbuster Ltd
- Final effluent quality monitoring: Partech
- Final effluent & potable water boosters: Dutypoint Ltd
Ruthin STW
- Principal contractor & designer: MMB
- Geotechnical investigation: Geotechnics Ltd
- Enhanced solids removal process: Evoqua Water Technologies (Xylem Water Solutions)
- Ferric sulphate dosing: Colloide Engineering Systems
- Polymer dosing: NPS Group
- Sodium bicarbonate dosing: Rospen
- Sludge tank: Goodwin Tanks
- MCCs/control panels: Lloyd Morris Electrical Ltd
- Systems integration: Merlin Systems
- Electrical installation: Lloyd Morris Electrical Ltd
- Mechanical installation: JB Fabrications
- Final effluent quality monitoring: Partech
- Final effluent & potable water boosters: Dutypoint Ltd
CoMag® system performance data
The graph below show the positive impact the new process plant is having on the WwTWs’ effluent discharges to the receiving watercourses, with the ‘step change’ drop in phosphorus as required by the new NRW 0.5 mg/l phosphorus permits. This is improving the water quality and aquatic habitat conditions in the respective local areas.
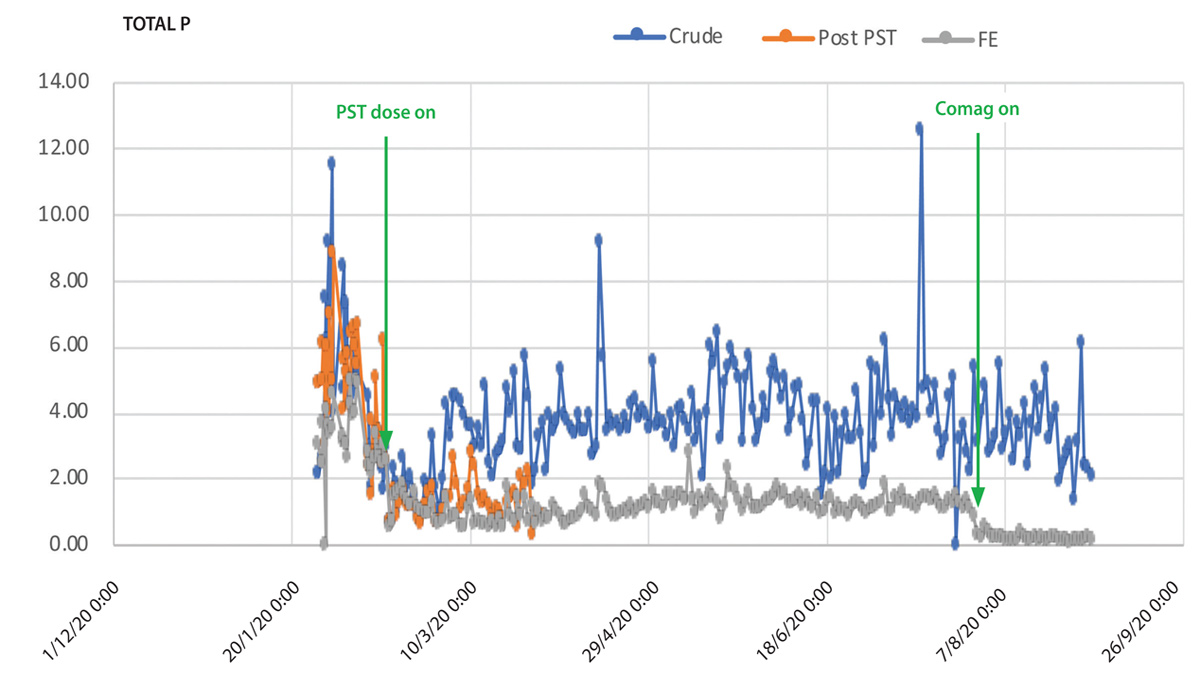
Ruthin WwTW: Impact on total ‘P’ before and after CoMag® system process commissioning – Courtesy of MMB
Conclusion
Welsh Water and MMB’s selection of the CoMag® ballasted clarification system process has led to a significant improvement in the effluent quality leaving the respective sites of Ruthin WwTW and Lletty Brongu WwTW with the new NRW permits for low phosphorus (T-P < 0.5 mg/l) being met almost immediately after the processes were commissioned.