Norton, Presteigne & Weobley WwTWs (2023)
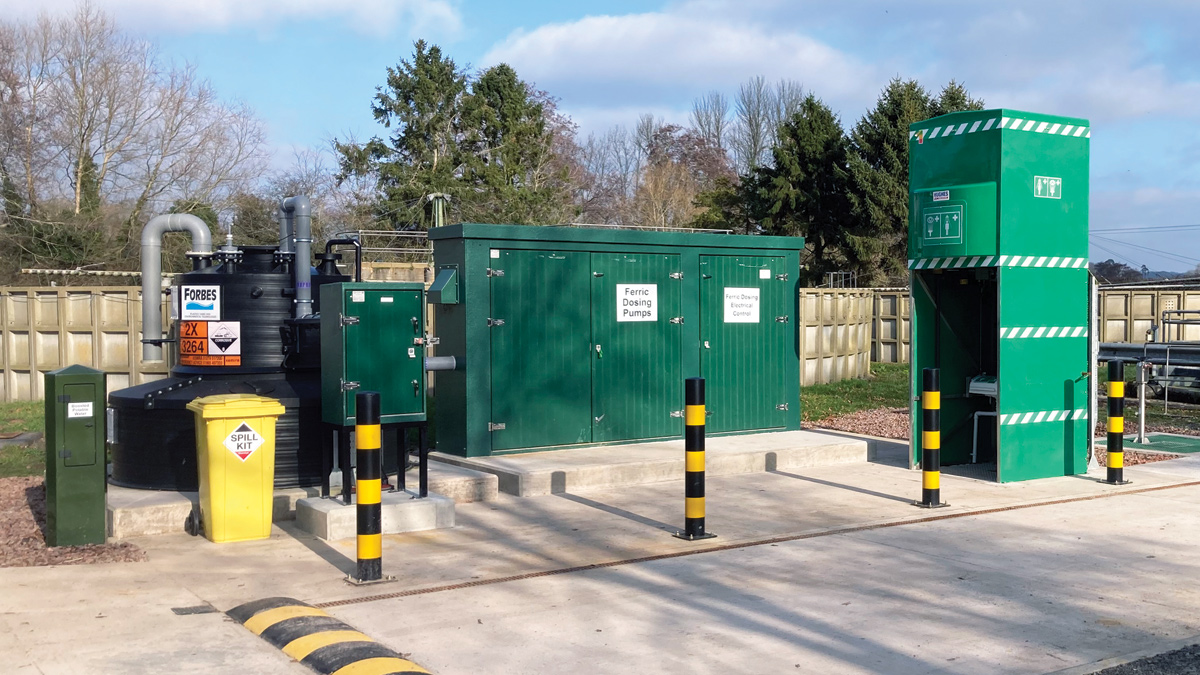
Weobley WwTW: Ferric dosing system from Colloide Engineering - Courtesy of Morgan Sindall Infrastructure
The Rivers Lugg and Wye have been identified as having high levels of phosphorus, which is causing eutrophication of these watercourses. Norton Wastewater Treatment Works (WwTW) discharges treated final effluent to the Norton Brook, a tributary of the River Lugg. Presteigne WwTW discharges treated final effluent directly into the River Lugg downstream of the Norton Brook confluence and Weobley WwTW discharges to Newbridge Brook, a tributary of the River Arrow and then River Lugg before joining the River Wye in Hereford.
Norton WwTW
Norton WwTW is a biofilter works located in Powys serving a population of 320. All wastewater flows arrive to the works by gravity and are treated on site before being discharged. The site previously had a descriptive consent and an unconsented storm discharge. The project driver was to reduce phosphorus to achieve a Total P of 0.65mg/l, with a regulatory completion date of 31 December 2021.
Due to the proximity of Norton WwTW to Presteigne WwTW (approximately 3km), an identified option was to pump the Norton flows to the Presteigne catchment. An assessment of the hydraulic and biological capacity of Presteigne WwTW and the Presteigne sewerage network determined there was sufficient capacity to accept the pump-away solution whilst maintaining compliance with all permits.
Therefore, the agreed solution was to replace Norton WwTW with a terminal pumping station, pump sewage into the existing sewer network draining to Presteigne WwTW. Consequently, the Norton WwTW would be decommissioned.
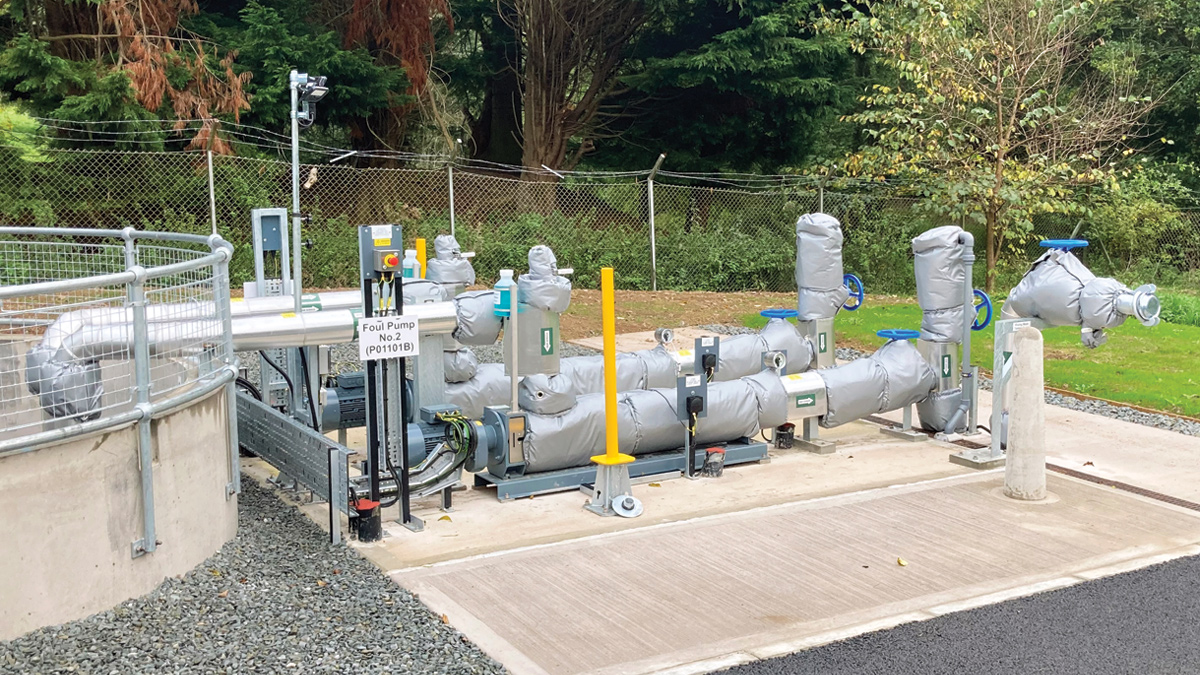
Norton SPS progressive cavity pumps – Courtesy of Morgan Sindall Infrastructure
Norton WwTW: Supply chain – key participants
- Designer: Arup
- Main contractor (WwTW & rising main): Morgan Sindall
- Electrical supply & installation: Protocol Control Systems (PCS) Ltd
- Inlet screens: Haigh Engineering
- Mechanical design/installation & steelwork: Industrial Pipework Services (IPS) Ltd
- Main pumps: Netzsch Pumps
- Washwater booster: Dutypoint Ltd
- MCC supply/install: Bridges Electrical Engineers Ltd
Transfer to Presteigne
Progressive cavity (PC) pumps were selected as the pumping method due to the complex nature of the 2km long rising main. The rising main has a number of peaks and troughs with washouts, air valves and sections operating under gravity. Furthermore, the inverted siphon section of the main may be susceptible to soft blockages which PC pumps were determined to be better suited to than submersible centrifugal pumps. Submersible pumps would be more susceptible to pressure fluctuations caused by potential air gulping in the downhill section of the main.
The PC pumps are positioned on an above-ground slab along with valves and pipework to enable good operator and maintenance access. Split stator casing pumps were specified to provide ease of rotor replacement.
To protect the PC pumps against ragging and wear, an inlet screen and grit chamber were set up upstream of them. The inlet screen is an Ace Screener® from Haigh Engineering Ltd, equipped with an integrated compactor and liquid separator unit. It is located beside the screen to facilitate the discharge of waste material into a skip.
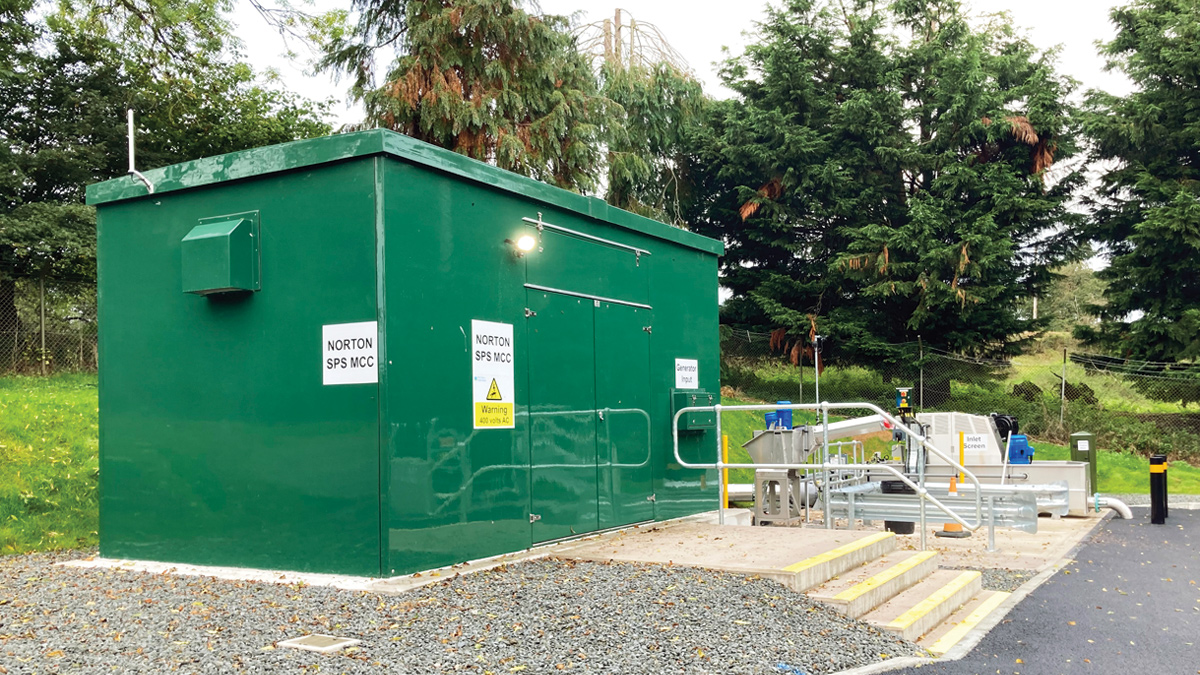
Norton SPS: MCC kiosk and Haigh Engineering inlet screen – Courtesy of Morgan Sindall Infrastructure
Rising main
Due to the length of the rising main, and the low flows coming into the pumping station on a regular basis, the output from the SPS would have been likely to suffer from septicity. This would cause particular odour problems as the discharge makes its way through the Presteigne network towards Presteigne WwTW. It was decided that potable water dosing be included within the design to reduce the risk of septicity. This has the added benefit of assisting in moving solids along the long rising main, which reduced the risk of soft blockages in the inverted siphon section of the main.
During the construction of the rising main, a spider plough was utilised for sections within fields. This allowed for simultaneous excavation, pipe-laying, and covering to take place, resulting in minimal visual impact on the landscape. Additionally, this approach resulted in reduced staff involvement during this stage of construction, which was another advantage.
A final air valve was required on the rising main before discharge, which is in close proximity to local housing and a children’s park. To prevent any odour-related complaints that might arise from the air valve, a carbon filter has been installed to scrub odours from the air released from the air valve. The chosen filter is a passive filter that can be easily installed within the air valve chamber.
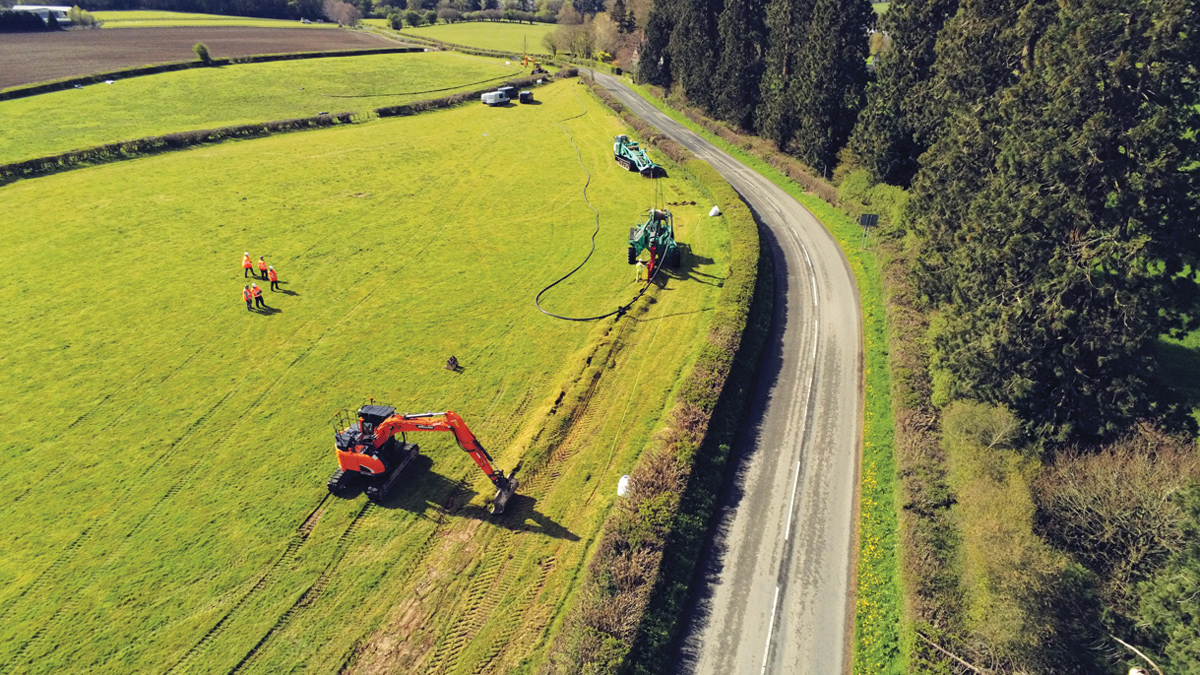
Spider plough operation to construct the Norton WwTW pump away rising main – Courtesy of Morgan Sindall Infrastructure
Presteigne WwTW
Presteigne WwTW is a biofilter works serving a population of 1,906 with a driver to reduce Total P to 1mg/l. The proposed solution is to provide chemical dosing at Presteigne to treat all the Presteigne network flows along with the additional pumped flows from Norton WwTW.
The chosen system was ferric dosing with primary dosing upstream of the existing primary settlement tank (PST). A ferric delivery area design included a bunded tanker area in case of ferric spillages. This area had drainage with an interlock system, which meant the drainage penstock would close during ferric filling to prevent uncontrolled spillage to the environment. Innovative new dosing pipelines were utilised of flexible reinforced PVC type ‘hose-within-hose’ to provide double containment and an integral leakage detection system and alarm. This meant long continuous hose lengths can be run without breaks. An anti-ragging static mixer and pipework were located above ground to reduce health and safety risks, costs and environmental impacts associated with excavation works.
To cope with the increased sludge production due to primary ferric dosing, a new sludge pumping station using PC pumps was designed. This is located alongside the existing PST de-sludge chamber. This was an above-ground element of mechanical plant, with access provided for operation and maintenance. Split casing pumps were specified to provide ease of rotor replacement. The progressive cavity pumps (duty/standby) couple directly into the sludge hopper chamber of the PST.
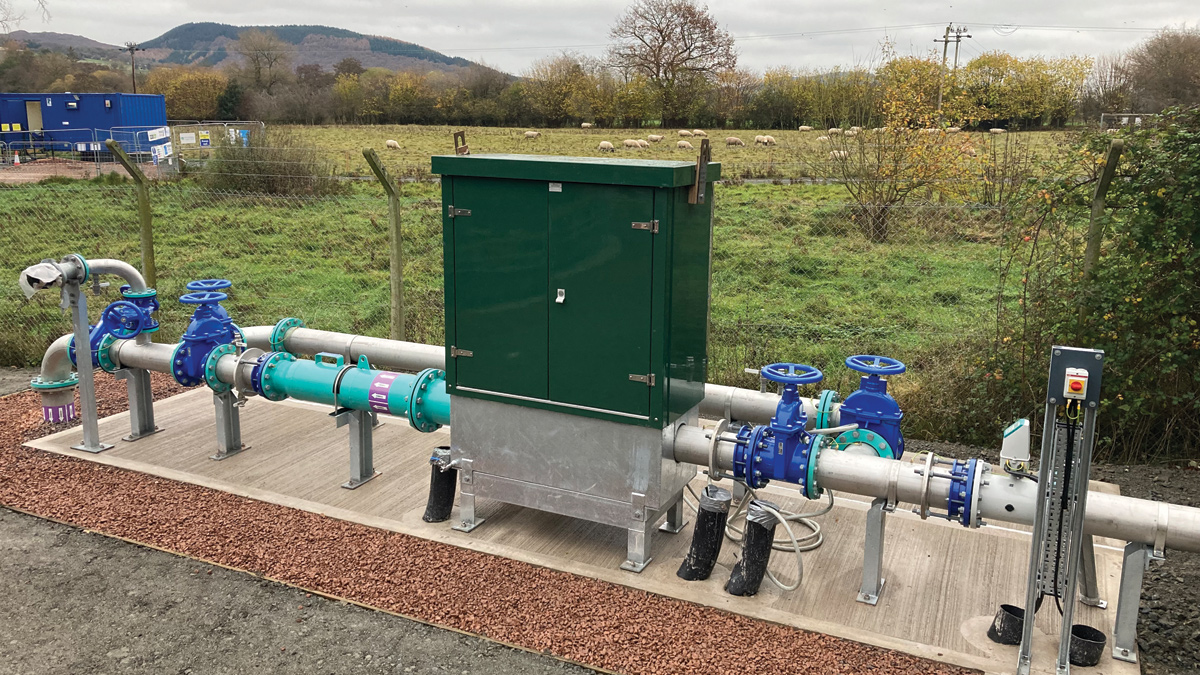
Presteigne WwTW: Ferric point of application (PoA) unit – Courtesy of Morgan Sindall Infrastructure
Alkalinity dosing was required as a result of the new ferric dosing. The identified solution for this was a small bag dosing plant with on-site mixing to create a liquid dose. A new point of application facility located on the side of the existing PST which discharges to the biological filter. It was determined that this point had enough hydraulic mixing for an effective alkalinity dose.
The new works is achieving its ammonia consent with the current loading, but it had been identified that ammonia compliance could be a risk during AMP9. Nitrifying sand filters have been proposed as a technology to treat the ammoniacal nitrogen as a tertiary treatment solution. This has an added benefit of tertiary solids removal to give confidence in the total phosphorus consent. However, given the excellent performance of the works against consent and nitrifying capacity of the existing biofilters, the nitrifying sand filters will be phased into the works when required.
Works included a new sampling arrangement with sampling kiosk, complete with an upstream diversion and reception chamber for when the nitrifying sand filter is constructed.
Presteigne WwTW: Supply chain – key participants
- Designer: Arup
- Main contractor: Morgan Sindall
- Electrical supply & installation: Protocol Control Systems (PCS) Ltd
- Ferric dosing: Colloide Engineering
- Mechanical design/installation & steelwork: Industrial Pipework Services (IPS) Ltd
- Alkalinity dosing – BiCarb: Rospen Industries
- Primary settlement tank auto-desludge: SEEPEX UK Ltd
- Motor control centre supply & installation: GPS Group
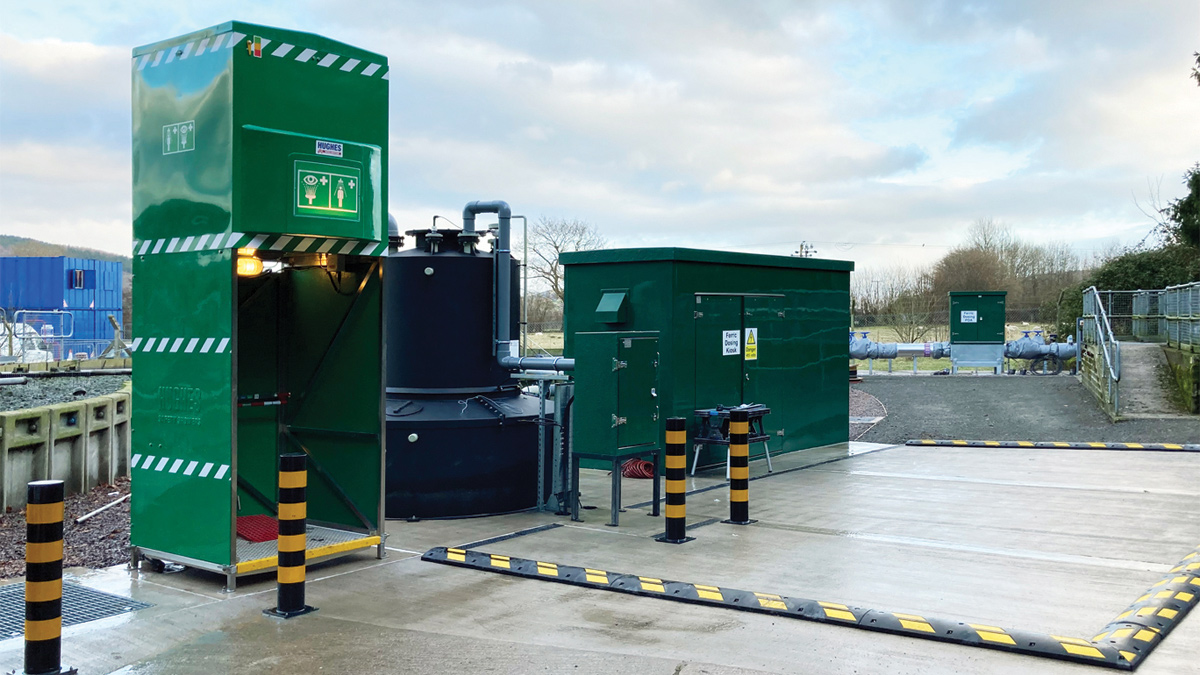
Presteigne WwTW: Ferric dosing system and safety shower – Courtesy of Morgan Sindall Infrastructure
Innovations
A number of innovations have been developed throughout the detailed design stage of Presteigne, including removing a number of pumping operations, thereby simplifying the process, and reducing costs and environmental impacts. The design also allowed for the removal of motorised mixing points for chemical dosing in favour of using the works hydraulics for mixing. Furthermore, a conventional solution would have called for an additional PST and humus settlement tank (HST) to provide redundancy to the works.
By investigating the process performance, it was determined that the existing single PST and HST were sufficient across the operating range of the works. Therefore, the design proposed temporary bypass connection points upstream of both the PST and HST, with identified lay-down areas for temporary settlement units to be brought on site if required. This meant that the construction works could be completed within the existing site land boundary and saving capital and operational cost and carbon emissions.
Weobley WwTW
Weobley WwTW is a biofilter works located in Herefordshire serving a population of 1,153. All flows arrive to the works by gravity and are treated on site before being discharged. The works has P removal driver to achieve a Total P of 1.5mg/l.
As at Presteigne WwTW, the proposed solution was to provide chemical dosing to reduce phosphorus. A ferric dosing system with primary dosing upstream of the existing PST complete with a ferric delivery area was provided. Given the added ferric dosing, it was expected there would be more sludge production. The existing sludge holding tanks had low abilities for controlling decant. The solution included for a new discharge tree with access arrangement to the existing sludge holding tanks for better operation.
The existing works had no inlet screening, with only a macerator on site upstream of primary settlement. A Huber Technology RO9 screen with integrated screenings handling was installed in the existing inlet channel and provided new mechanical flooring with removable sections to provide flexibility for operating and maintenance of the screen.
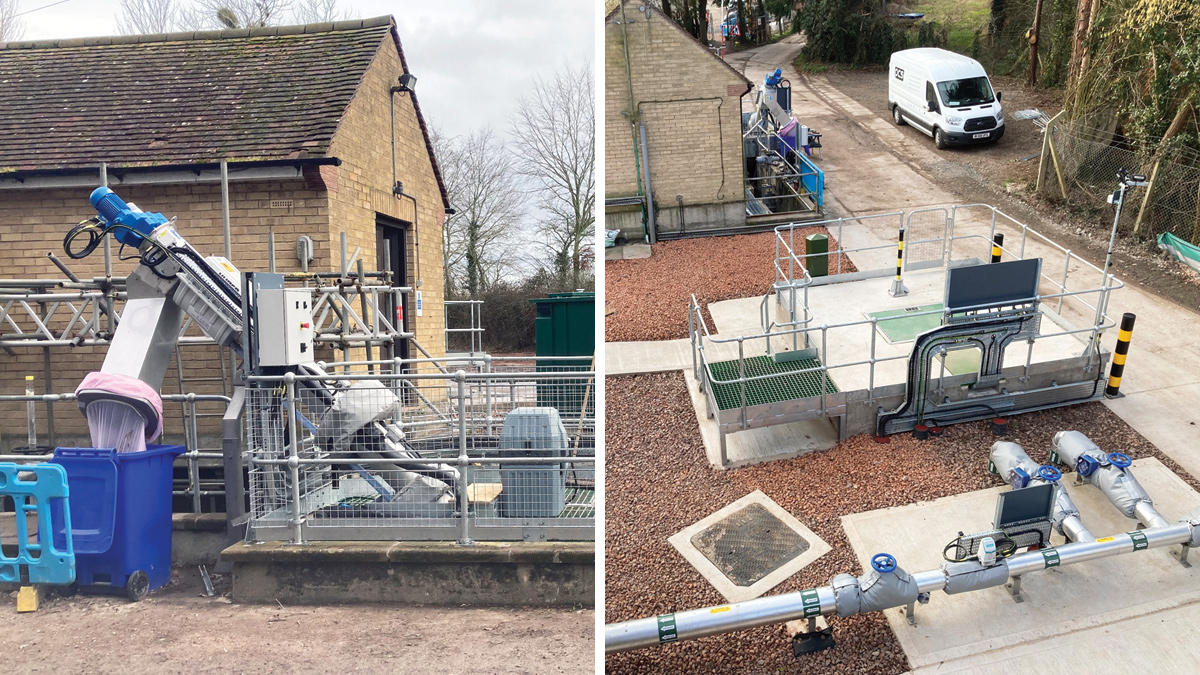
Weobley WwTW: (left) Huber Technology inlet screen and (right) flow to full treatment pump station – Courtesy of Morgan Sindall Infrastructure
This provided significant cost and embodied carbon savings compared to a completely new screening installation. Downstream of the screen, an inlet flume was provided for flow measurement and control of the downstream lift pumping station. The flume was constructed off-site, allowing for greater dimensional accuracy than an on-site constructed flume, as well as reduced downtime for the site.
A new lift pumping station for all incoming flows for treatment was required to provide a separate lift to the balancing tanks then the unscreened storm flows. The existing inlet pumping station was re-purposed as the storm pumping station, meaning the more efficient pumping station was operating for more of the time compared to the older storm pumping station, which only operated intermittently – hence saving on energy usage and operational carbon.
An existing multi-use returns pumping station was used to pump humus returns and storm returns to the head of the works. This asset consisted of outdated and poorly operating pumps and valve work. A solution was developed to replace mechanical equipment within the existing dry-well, saving the need for a new complete pumping station.
Weobley WwTW: Supply chain – key participants
- Designer: Arup
- Main contractor: Morgan Sindall
- Electrical supply & installation: Protocol Control Systems (PCS) Ltd
- Mechanical design & installation: Whitland Engineering
- MCC supply & installation: Lloyd Morris Electrical Ltd
- Pumps & package pump station: Xylem Water Solutions
- Potable water booster supply: Dutypoint Ltd
- Ferric dosing supply: Colloide Engineering
- Inlet screen supply: Huber Technology
- Safety shower supply: Hughes Safety Showers
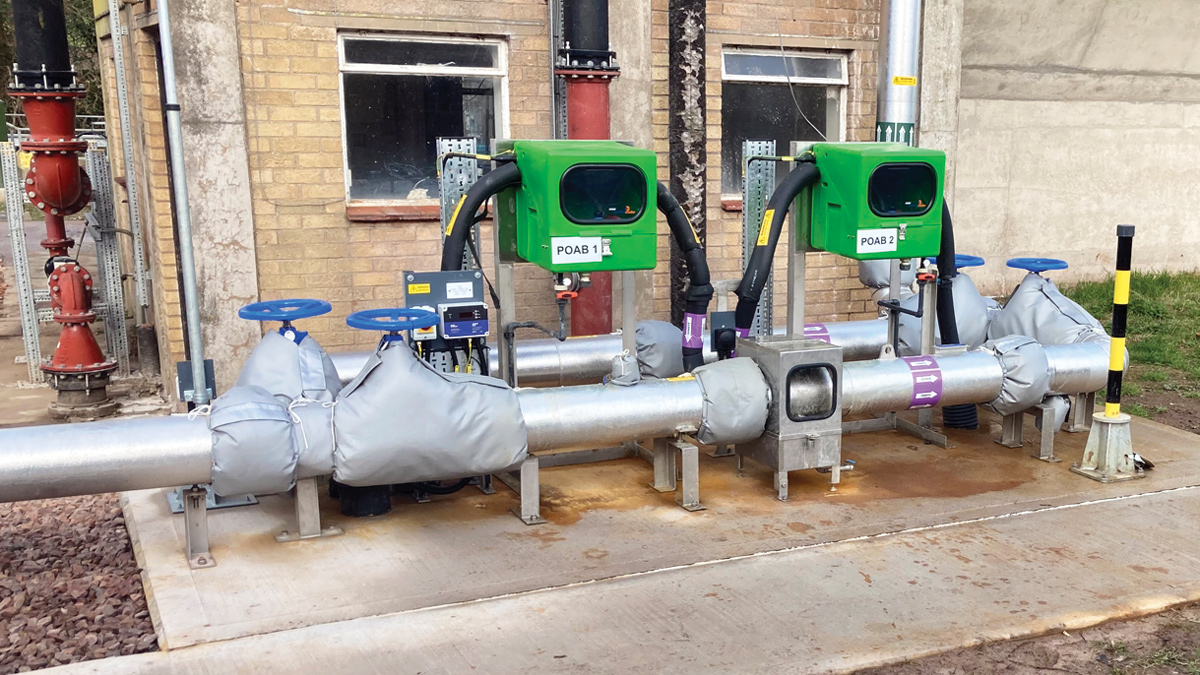
Weobley WwTW: Ferric point of application units – Courtesy of Morgan Sindall Infrastructure
BIM
BIM capabilities were utilised at all three sites to design the schemes, and the wider engineering team used site-wide 3D models to great effect to review the works and propose any improvements. Furthermore, this provided an engaging and relatable interface to present the schemes solution to stakeholders, as well as using engineering drawings.
Project completion
Welsh Water’s have invested £5.9m at the Norton and Presteigne WwTWs and £2.7m at Weobley WwTW. These phosphorous removal schemes are the first tranche to be completed of a programme of upgrades to existing wastewater treatment works that will improve water quality in the Wye and Lugg river basin catchments.
Learnings from these schemes have been used by Arup and Morgan Sindall and shared with the Welsh Water Capital Delivery Alliance partners to improve scheme delivery of other rural wastewater treatment works. Through early engagement with chemical dosing suppliers, potable water designs and DfMA MCC suppliers, design enabling efficiencies in design and construction costs to be realised have been standardised.
Norton & Presteigne WwTWs were commissioned in March 2022 and Weobley WwTW was commissioned in March 2023.
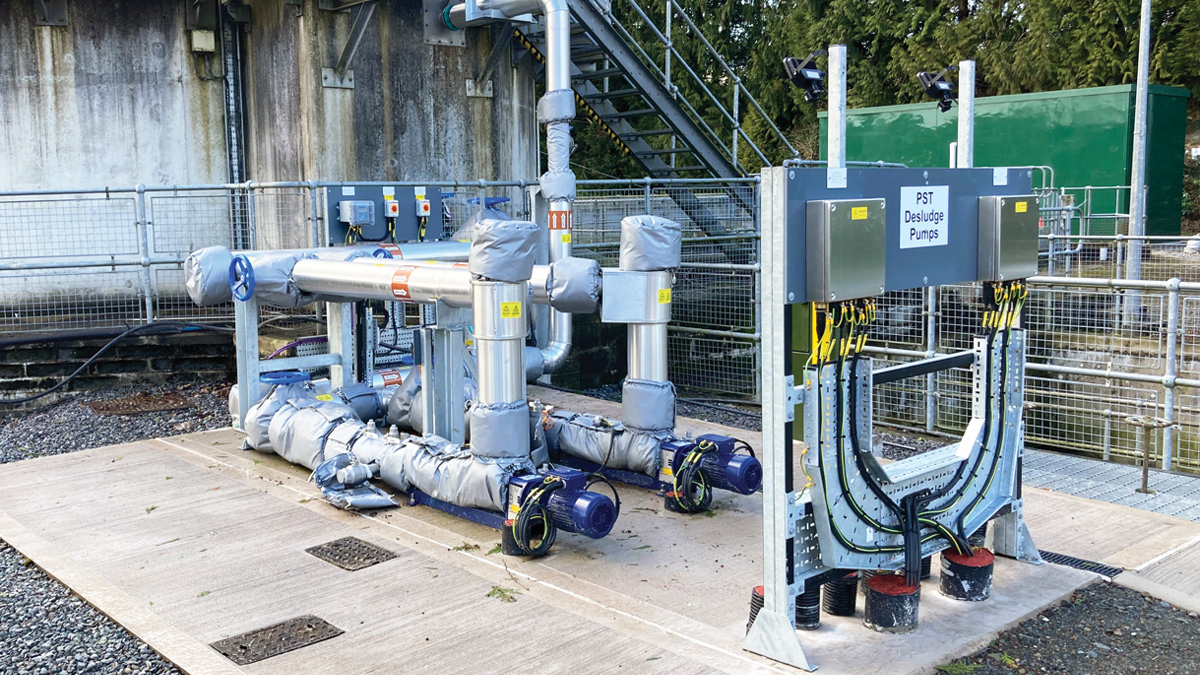
Presteigne WwTW: Primary settlement tank de-sludge PC pumps - Courtesy of Morgan Sindall Infrastructure