Sunderland Groundwater Stations (2021)
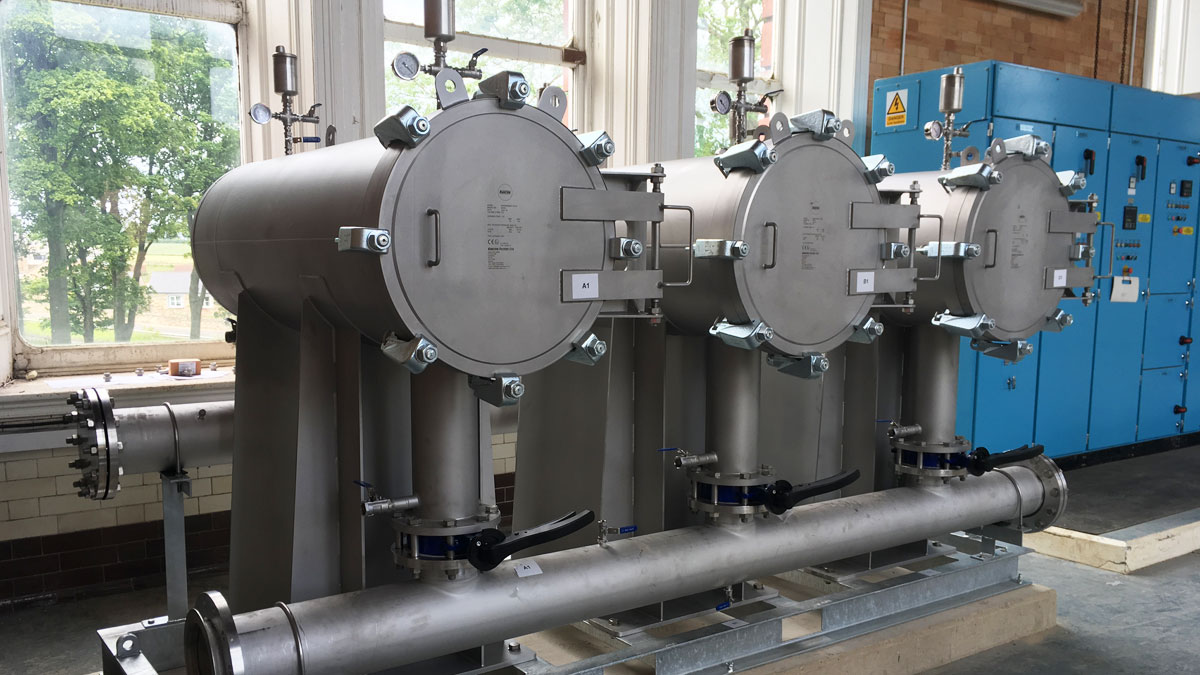
Filter units installed at Stoneygate GWS (pre-pipework connections) - Courtesy of Northumbrian Water
The Sunderland Groundwater Stations (GWS) have historically provided a reliable and cost-effective source of good quality water to the Wearside distribution area. They were mostly built in the late 19th and early 20th centuries and consist of one or more shafts, of up to 150m in depth, into the magnesian limestone aquifer. Each station has service buildings that house plant and equipment; two of which have listed building status. There are eight GWSs in the network which are required to deliver an output of 44 Mld during peak demand periods. However, the GWS system is operated flexibly, supplementing water from other surface water sources in the Wearside area as demand dictates which can result in one or more of the stations being out of supply for periods at a time. This paper focusses on the refurbishment of five of the eight stations (Stoneygate, Hawthorn, Thorpe, Dalton and Fulwell).
Background and drivers
A feasibility study and hydrogeological assessment, completed in 2014, confirmed that the GWSs had a 25 year plus remaining life (with maintenance) and the recommendation was to retain and refurbish them. Investment was required if their use as key assets was to be continued. The scope of the project has changed since first inception, however investment to date stands at £6.2m on the upgrade and refurbishment of the five identified sites.
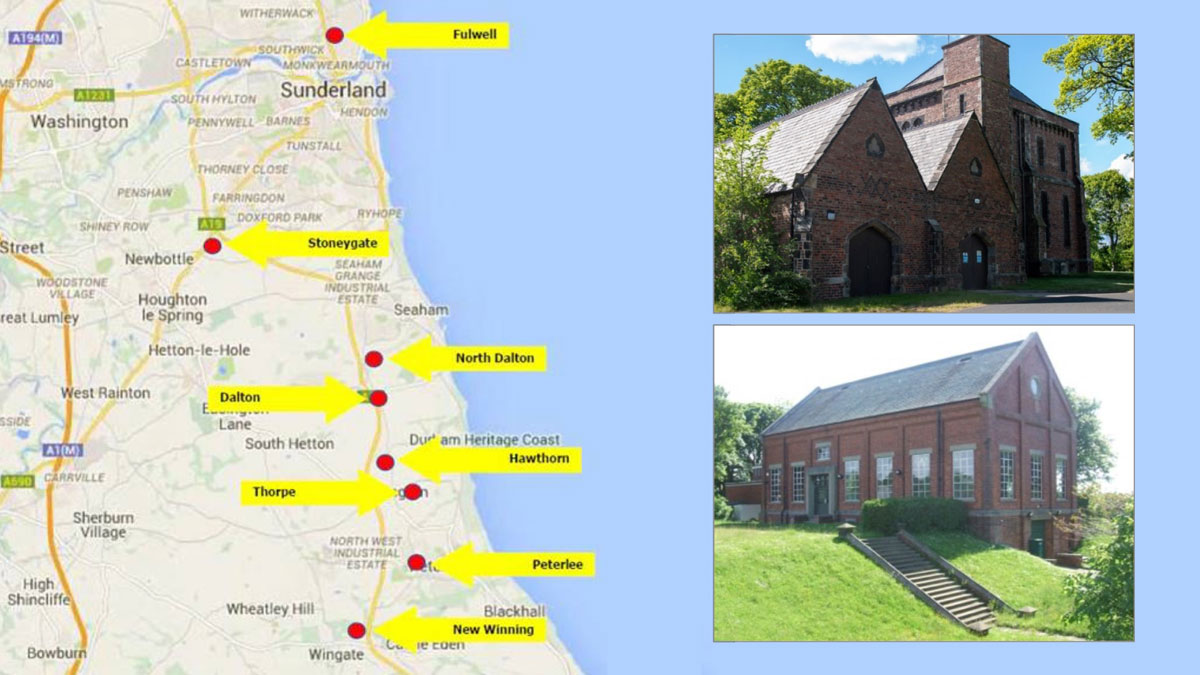
Geographic distribution of the Sunderland Groundwater stations. This project relates to Stoneygate, Hawthorn, Thorpe, Dalton (lower photo) and Fulwell (upper photo). Refurbishment of the Victorian assets presented a range of challenges relating to the planning, construction, and subsequent process integration aspects of the project – Courtesy of Northumbrian Water
The following areas were recognized as areas targeted for improvement:
Water quality: One of the key drivers of the project was to improve the quality of drinking water for customers in the area. In addition to increased customer satisfaction, enhancements to the water quality would also improve overall drinking water compliance as determined by the recently introduced regulatory water quality measure, the Compliance Risk Index (CRI).
The GWS have historically generated low-level turbidity occurrences in the region, particularly on start up. This was primarily due to the on/off nature of the stations as demand fluctuates, and the absence of smooth pump control. The project was required to remove the risk of turbidity affecting the operation of the plant or the quality of customers supplies.
An additional objective was to improve overall mean zonal compliance in the area in relation to taste and odour contacts; these typically materialised as a consequence of changing water supplies. Greater remote and auto control of the sites would result in reduced start/ stop frequencies and a reduction in associated customer contacts.
Resilience: The eight sites have a peak target deployable output of 44Mld, a target the existing assets could not reliably meet. Improvements to the site pumps and remote auto control would create resilient assets allowing the identified quantities of water to be produced as and when required. This resilience would allow the network to be operated in an efficient and economic manner.
Environmental compliance: To ensure compliant water entered the potable distribution network, on start up the sites diverted water to waste. These discharged to a sewer where practicable or to a watercourse under existing Environment Agency consents. Work was required to automate the start up at each site, including improving the quality and quantity of discharges to the environment in accordance with stringent regulatory measures.
Health and Safety (H&S): Safe operation and maintenance of the treatment sites was identified as a priority. As an example, to maintain, remove and install pumps at Dalton GWS man-entry was required to a depth of over 70m below ground.
At Thorpe GWS the top platform had reached the end of its design life; an inspection confirmed that prior to any further maintenance or replacement of the pumps it would need to be addressed, putting supply from the site at risk.
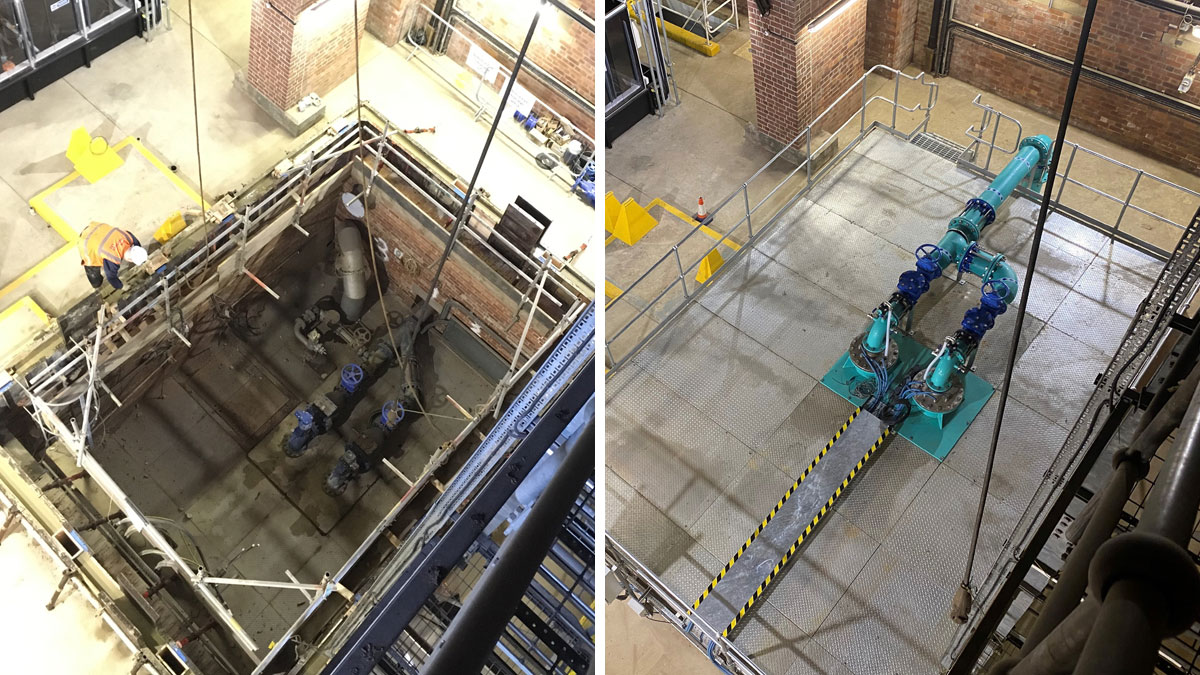
(left) Existing Thorpe GWS and (right) Thorpe GWS post works on the top platform and pump installation – Courtesy of Northumbrian Water
Design and construct
On behalf of Northumbrian Water, Interserve Construction (now Tilbury Douglas) commenced work on the design and construct contract in 2014. Wood Plc were engaged by Interserve as designers. The scope of the works focussed on providing more flexible operation of the sites whilst addressing compliance and H&S concerns at the individual sites.
The works includes the design, procurement, installation, testing and commissioning of the following:
- Man-entry avoidance.
- Automated run to waste (RtW).
- Automated local and remote start up.
- Provision of variable speed drives.
- Replacement pumps.
- Automated dechlorination facilities at sites discharging to a watercourse.
- Installation of filters.
- Associated MEICA and civils modifications.
A review of the existing individual assets and operations was undertaken resulting in a combination of requirements across the five sites, as seen in Table 1 below.
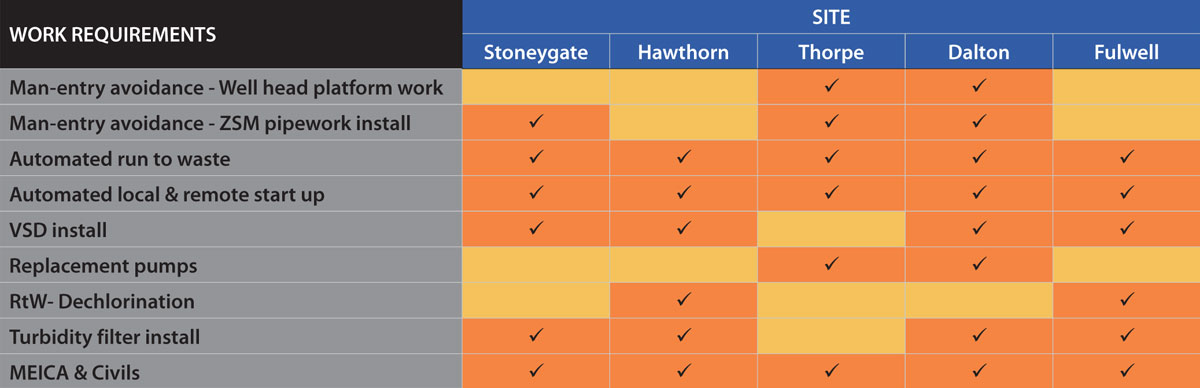
Table 1: Summary of work undertaken at each GWS
As part of the TOTEX evaluation and design efficiencies the design incorporated the reuse of existing Northumbrian Water assets where possible, and integrated operational and maintenance task requirements in line with best practice procedures. To facilitate this, existing installations and the proposed new assets were modelled using AutoDesk Revit Building Information Modelling software allowing for the visualisation of the asset installations.
On site construction commenced spring 2018 at the first site. The sites were completed sequentially, with some overlap where the supply network could facilitate the prolonged outages.
Sunderland Groundwater Stations: Supply chain – key participants
- Principal contractor: Tilbury Douglas Construction
- Designer: Wood Plc
- Boreholes, pumps & pipework: G Stow Plc
- Systems integration: IDEC Technical Services Ltd
- Control panels: CEMA Ltd
- Filter supplier: Amazon Filters Ltd
- Electrical: Intelect
- Electrical: Labtec
- Chemical dosing: Sheers
Construction
The design and build requirements of the man-entry avoidance incorporated the following:
- The design of the new top platforms must allow safe man access into the shaft.
- Well tops must be sealed to avoid ingress of material into the well.
- Ramped sections of metalwork are to be provided for protection of the pump motor cables running over the platform.
- Pumps to be located at similar depth to recent operating levels.
- New pumps and quick coupled stainless steel ZSM pipework to be installed where required.
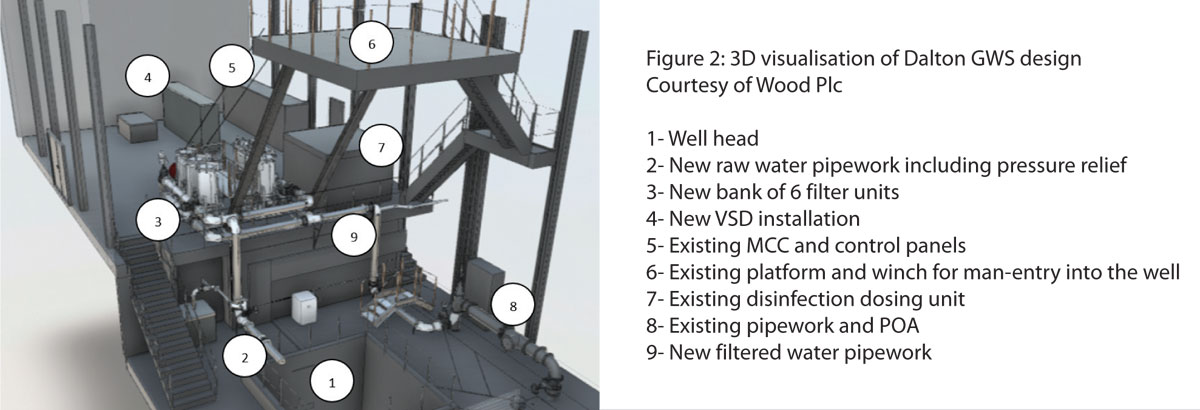
Dalton GWS visualisation – Courtesy of Wood Plc
The design and build requirements of the dechlorination system incorporated the following aspects:
- A new dosing system package comprising a storage tank and delivery point, single dosing pump, skid pipework and valves, adequately sized bunding and screens, local control panel.
- Double contained dosing line, with catch pot at the lowest point, and loading valve at the point of application.
- Sample system with 1 (No.) chlorine residual and 1 (No.) oxygen reduction potential analyser (ORP) or equivalent.
- Dosing chamber containing static mixer, considering adequate access arrangements.
- Chemical to be used sodium bisulphite (strength 23% w/v).
The dechlorination systems have been installed at two sites; Hawthorn and Fulwell. During early design the two analysers were changed to use one Evoqua DEOX2000 dechlorination analyser. The analyser was installed due to its ability to monitor chlorine concentrations to low levels and also control to ensure no overdosing of sodium bisulphite. The systems have been integrated into the start up control philosophy to operate when required.
The design and build requirements of the turbidity filters incorporated the following aspects:
- Remove particulates to keep turbidity less than the operational requirement of 0.3 NTU.
- Ability to bypass the filters during a start up to prolong the life of the cartridges.
- Ease of access for routine maintenance (e.g. monthly cartridge replacements).
- Materials fully compliant with the drinking water regulations.
- Ability to monitor performance using appropriate turbidity, pressure and flow instruments.
At Stoneygate and Dalton GWSs, Amazon Ltd filtration units were installed, with each housing unit containing 40 filter cartridges. At Dalton a bank of six filtration units were installed.
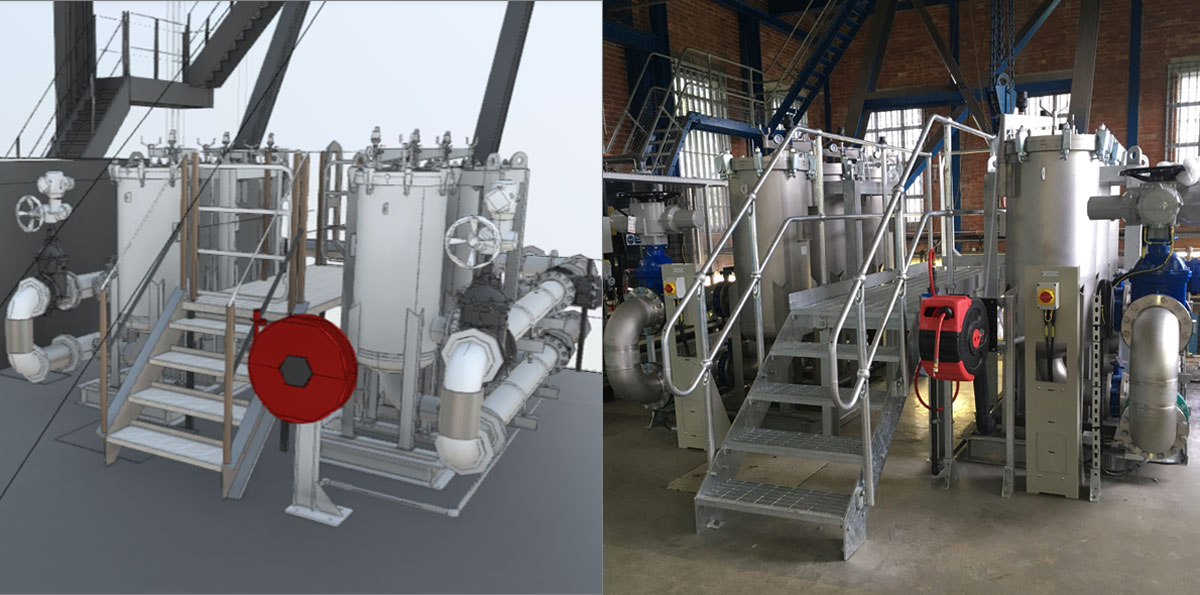
(left) Dalton GWS design model and (right) as built filter installation – Courtesy of Northumbrian Water
Challenges
Construction was undertaken in situ but off-line, which facilitated programme delivery. Commissioning elements were also completed offline with few exceptions. The main challenges throughout the design, construction and commissioning phases have been identified as follows:
- Integrating the new assets and processes with the existing aged assets on site. This relates to MEICA elements, and also restrictions imposed by the layout and space within the existing buildings and grounds.
- Commissioning the de-chlorination systems. Innovative analysers new to the design, commissioning and NWG teams were utilised. These have proved challenging to fully commission with ongoing modifications and lessons learnt between the sites to fully integrate the systems.
- Constraints and delays on works outage availability. Coordinated planned outages of each site were required to maintain network resilience and allow other essential maintenance works to be undertaken concurrently. Superimposed over these planned outages was variable seasonal network demand and reactive network adjustments.
- Changing compliance targets and operational expectations. Between feasibility (2016) and final commissioning (2020) a number of standards and compliance targets were amended, primarily relating to water quality and H&S. This resulted in significant scope change and design modification to meet these and the operational business requirements.
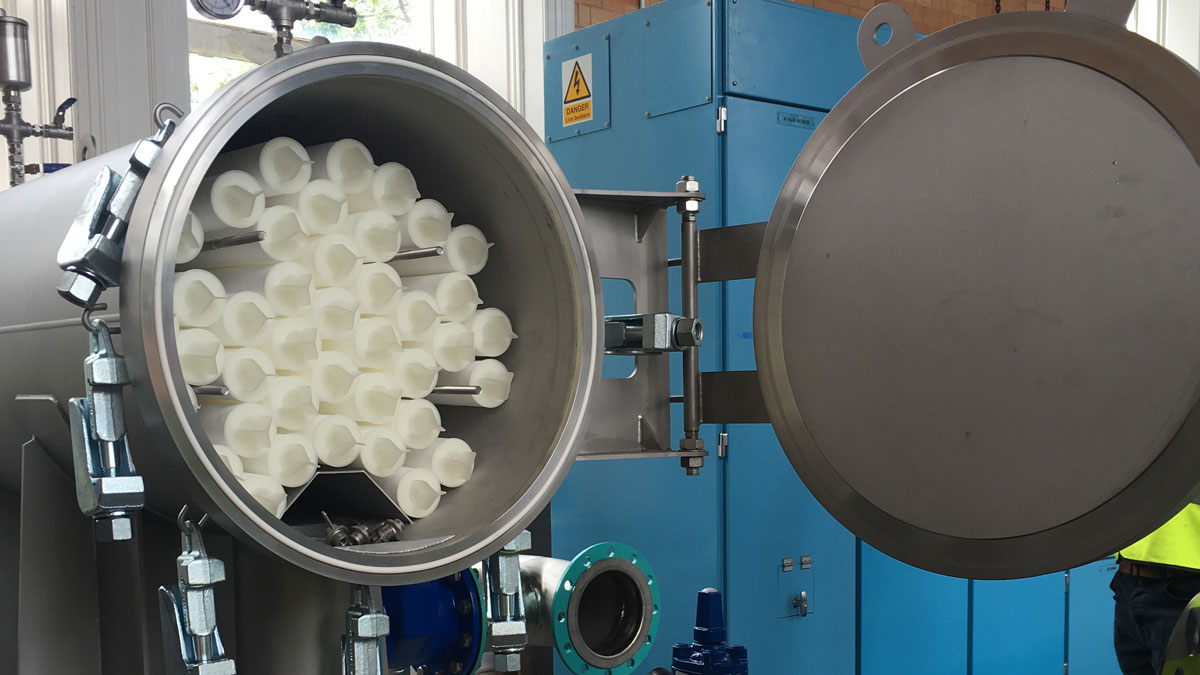
Filter units at Stoneygate GWS (pre-pipework connections) containing 40 (No.) Supaspun II R31 compliant cartridges remove particulates and subsequently reduce turbidity and its associated risks – Courtesy of Northumbrian Water
Conclusions
The works were substantially completed mid-2020, with final commissioning of the run to waste systems at two sites due for completion summer 2021. This successful delivery of five refurbished groundwater stations demonstrates the benefits of collaborative working between multiple framework contractors and internal stakeholders.
With the work undertaken sequentially across several sites, lessons learnt were transferred and integrated which facilitated the efficient delivery of the scheme and improved the quality of the assets upon handover to the end users.
The investment on the five sites has delivered significant benefits to Northumbrian Water and its customers including:
- Five robust, sustainable assets with extended operational life provided by the reuse of existing assets which delivered the most efficient TOTEX solution. These improve the Wearside network resilience and quality of the water being produced whilst simultaneously reducing operational and maintenance reactive tasks.
- Improved water quality performance by reducing the risk of turbidity. The replacement of fixed speed pumps with VSDs facilitates the flexible operation of the GWS providing the ability to gradually increase or decrease flows as demand dictates. The new pump operation, alongside the filter installation, significantly reduces the risk of turbidity both on start-up and during operation.
- Improved environmental compliance via the automated, controlled prevention of un-chlorinated water entering the environment and monitoring of the quantities of water that are discharged (due for completion summer 2021).
- Increased resilience of customer supplies as the production rates from each site can now be altered relatively quickly, without requiring significant operational intervention and incurring operational costs.
- More robust assets gives Northumbrian Water the ability to optimise power consumption and reduce the reliance on more expensive water sources.
- The removal of the health and safety issues associated with man-entry into the wells.