Walsall Wood STW (2019)
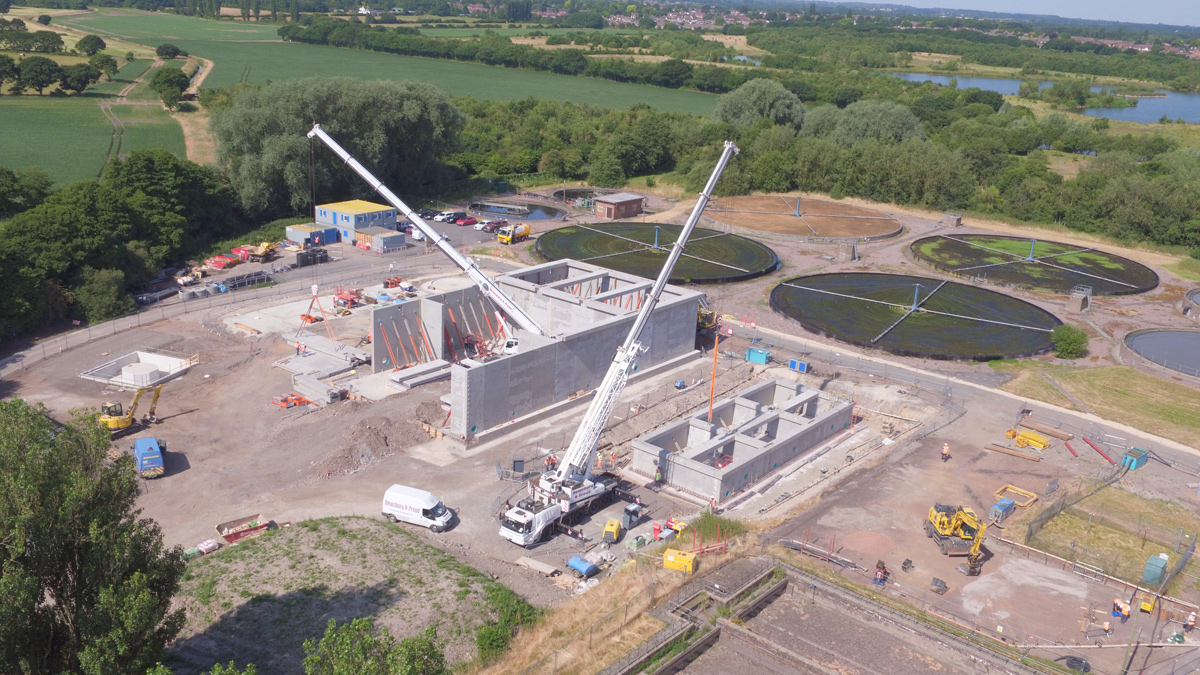
Wallsall Wood STW: Main installation of precast units - Courtesy of MMB
Walsall Wood Sewage Treatment Works was a trickling filter site discharging into the Ford Brook, part of the River Tame catchment. Under the new Water Framework Directive, the site was required to comply with stringent new standards for phosphorus and ammonia levels in wastewater (BOD: 10 mg/l, NH3: 1.9 mg/l, Total P: 0.5 mg/l). The design for this project had to consider the future population equivalent of 26,250 for the 2026 design horizon, as well as its inherent calculated loads. Using Nereda® and Mecana technology, MMB have been able to deliver the most cost-effective TOTEX alternative and offer a solution that requires a third of the area of a conventional activated sludge installation with only two thirds of the whole life cost carbon footprint for an equivalent water quality output.
Collaborative working
This project is part of the Activated Sludge Process (ASP) Batch, which consists of twenty-six wastewater projects with a contract value of £179m delivered by a JV agreement between Mott MacDonald Bentley (MMB), CiM6 (Costain and Stantec), nmcn PLC and Severn Trent with fully shared risk and reward.
This gave the opportunity for collaborative working, sharing knowledge of engineering principles and judgement. A joint group was created with representatives from the four companies, focusing on planning and communicating efficiencies in design, procurement and management. The synergies achieved meant tight deadlines were met, substantially completing the detailed design in under 6 months. By batching orders, the procurement teams saved more than £210K and by using the same subcontractors, lessons learned from early installations yielded additional efficiency.
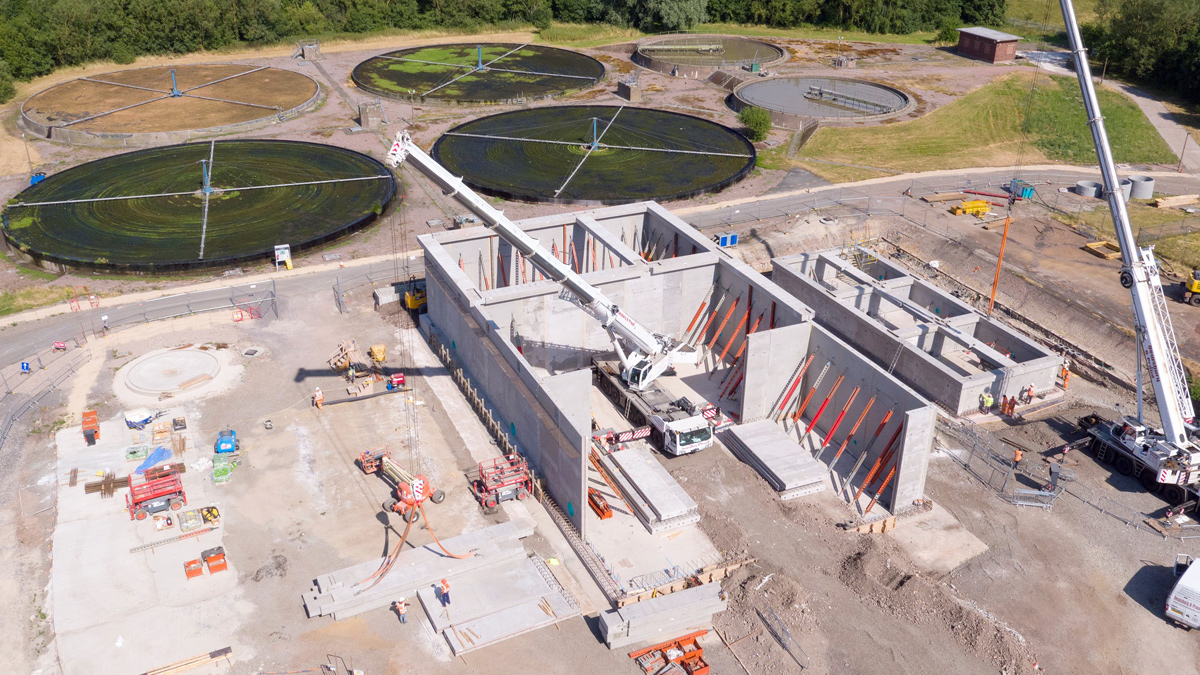
Wallsall Wood STW: Main installation of precast units – Courtesy of MMB
Technology options at Walsall Wood
A multi-disciplinary core team consisting of members from MMB and Severn Trent produced a detailed study of different technologies that could achieve the desired outcome. The options were analysed based on CAPEX, OPEX and carbon footprint, whilst also evaluating risks and opportunities.
As a result, the team identified an innovative and sustainable solution, which was to implement the Nereda Granular Activated Sludge (GAS) process from Royal HaskoningDHV, followed by a Mecana tertiary solids removal cloth filter from Eliquo Hydrok Ltd.
Walsall Wood was the first project in the Severn Trent area to implement a Nereda solution, however there were two more sites in the ASP Batch that were identified to benefit from the same technology; Barston STW and Radcliffe STW.
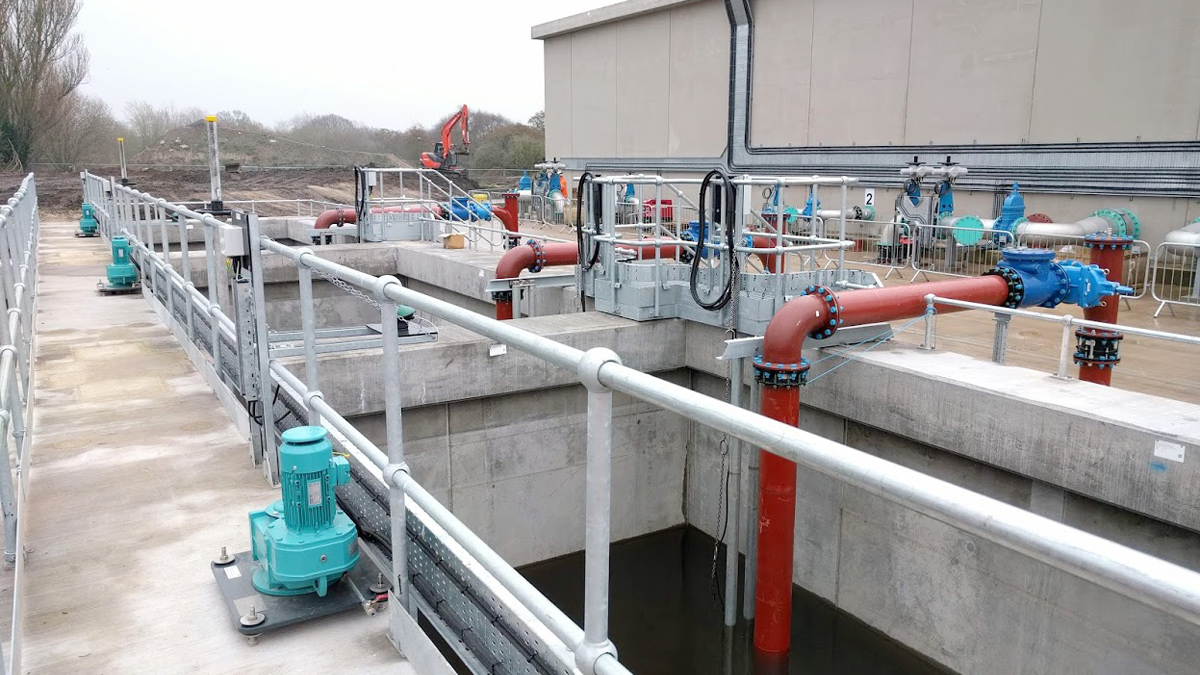
Buffer tank and Nereda reactors – Courtesy of MMB
The Wallsall Wood project
In addition to the Nereda and Mecana technologies, the project included new inlet screens, a manual system to clean the storm tanks, pre- tertiary solids removal (TSR), chemical dosing and wash water facilities with a buffer tank. Modifications in the inlet works were key to allow compliance with the strict requirements for the Nereda system, as rag over the screens would result in a blockage.
Ferric chemical dosing was necessary to precipitate the residual ortho-P from the Nereda system before the TSR cloth filter plant to meet the future Total-P and BOD permits. Redundancy factors were applied in all the designed elements to allow the plant to operate even in case of maintenance or failure of one of the elements.
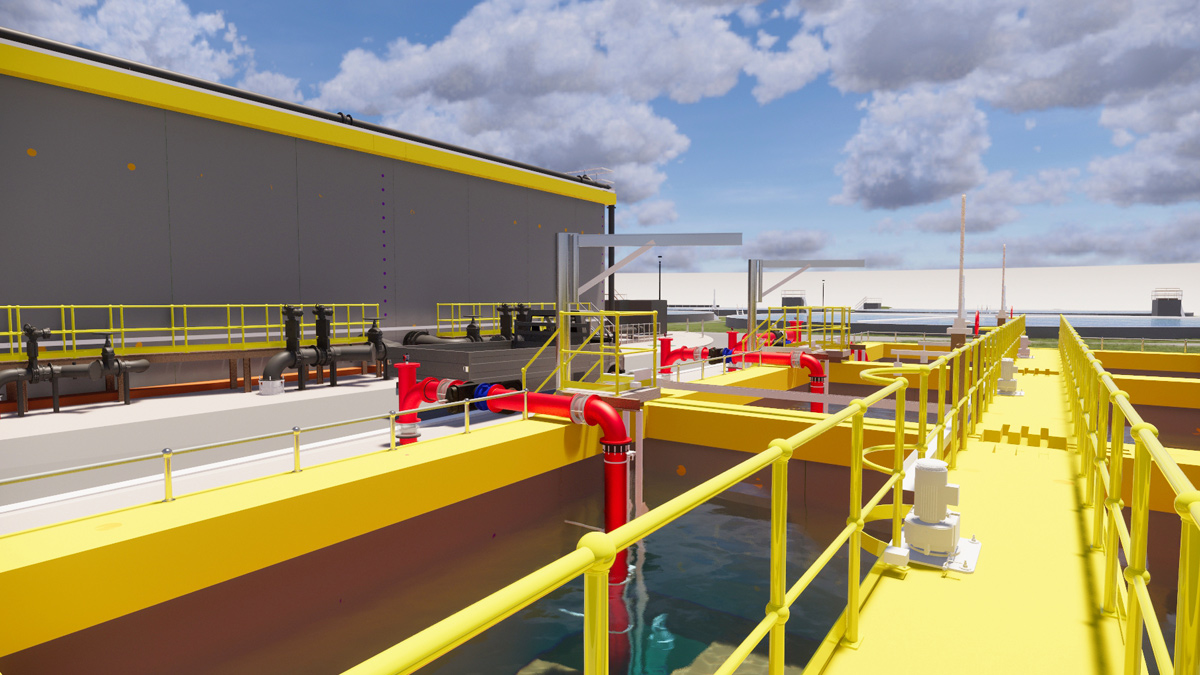
BIM model – Courtesy of MMB
Innovations
The design team made use of digital technology to set up the BIM model and organised virtual reality sessions with both the construction team and the final operational user to ensure high standards for occupational health and welfare planning.
The team implemented innovative ideas such as factory production to reduce the programme on site and design out H&S risks. For instance, MMB used a precast concrete solution for the water retaining structures which removed the need for in situ stitching between precast units, therefore allowing safer, faster construction.
Vibro Menard controlled modulus columns were used instead of conventional piling for the foundations of the reactors, resulting in 900m2 of ground improvement in half the initially planned time.
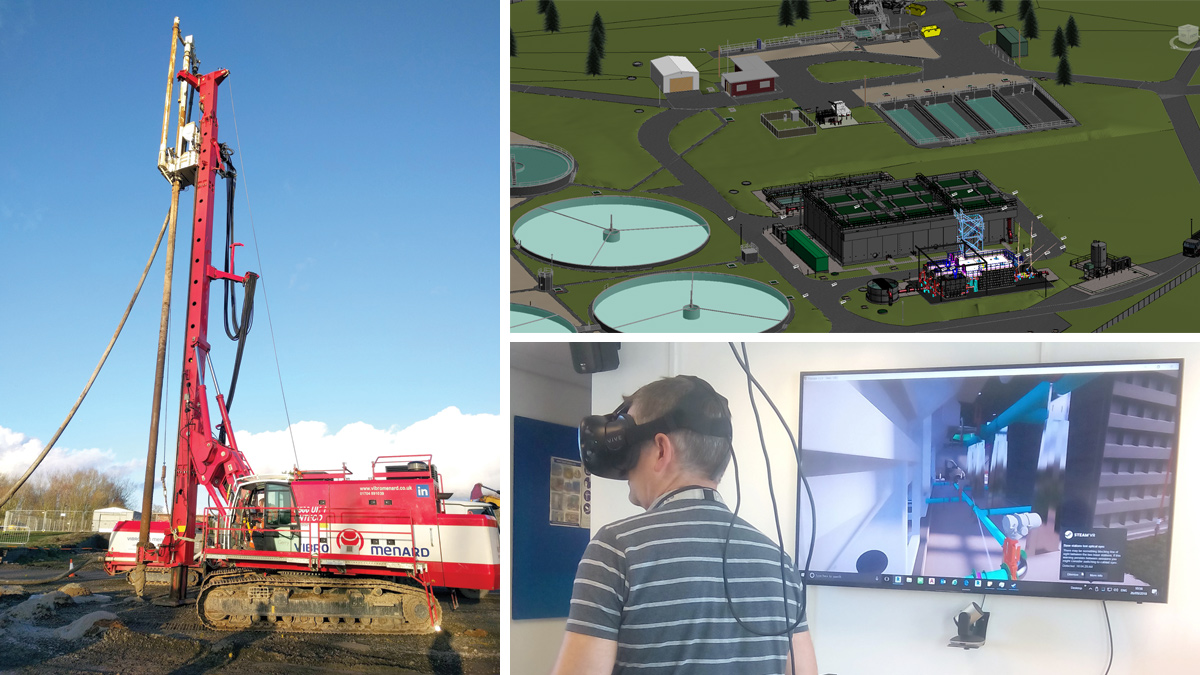
Innovations: (left) Vibro Menard controlled modulus columns (top right) BIM 3D model and (bottom right) use of virtual reality – Courtesy of MMB
Walsall Wood STW: Supply chain
- Principal contractor & designer: Mott MacDonald Bentley
- Process design: Severn Trent
- Secondary process engineering: Royal HaskoningDHV
- TSR process engineering: Eliquo Hydrok Ltd
- MCCs & software: Boulting Group
- Electrical design: Imac
- Ground stabilisation: Vibro Menard
- Civils structures: FP McCann
- Mechanical installation: Rosewood Engineering
- Nereda internals: Suprafilt Ltd
- Ferric dosing: EPS Water Group
- Inlet screens: M and N Electrical and Mechanical Services
- Organic return pumps: Tuke & Bell Ltd
- Blowers: Aerzen Machines Ltd
- Penstocks: Ham Baker Group
- Iron monitor: Servitech
- Lifting equipment: T-Allen Engineering Services
- Pumps: Grundfos UK
- Mixers: Corgin Ltd
Conclusion
This chosen solution offered a reduction in the construction footprint by a third compared to a conventional activated sludge process, a CAPEX saving of £500k over a £8.7m commercial value, a TOTEX saving of £1.6m in 20 years and a whole life carbon footprint reduction of 1.3 TCO2e.
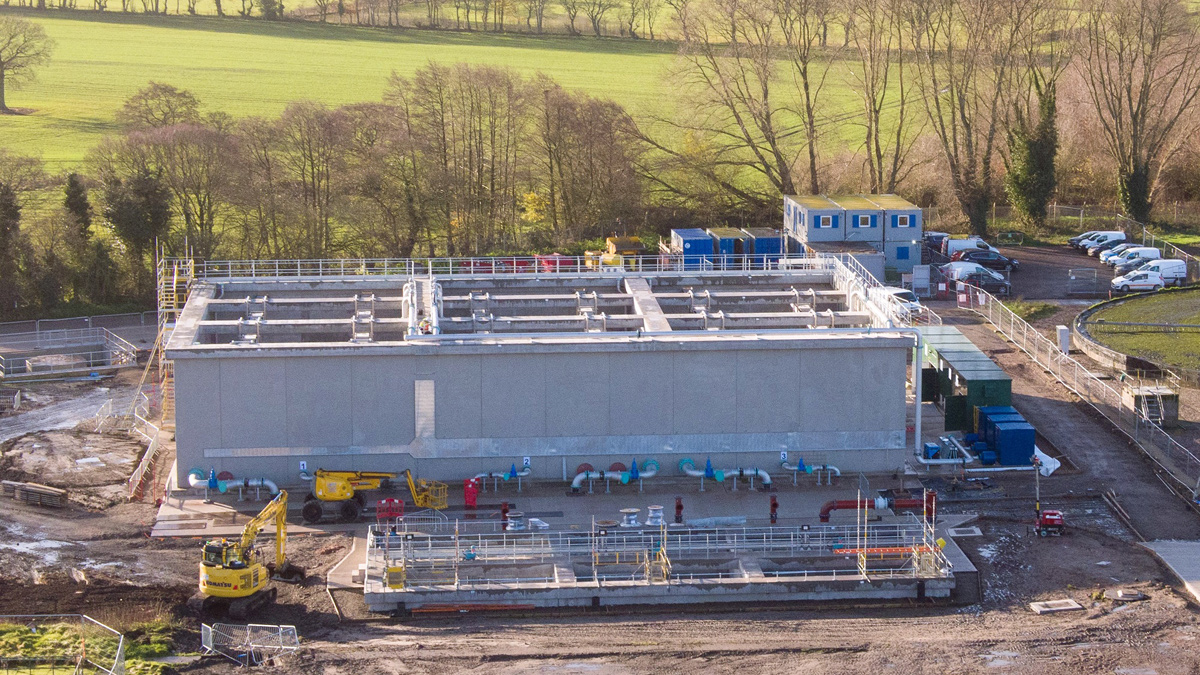
Walsall Wood site in November 2018 – Courtesy of MMB
During construction the site team got positive feedback from Severn Trent stating Walsall Wood was “a job you should be proud of”. The dry and wet commissioning were a massive success, having been complimented by Royal HaskoningDHV who stated, “we have never seen the site acceptance tests (SAT) going this well anywhere else in the world before”.
At the time of writing (May 2019) the new plant is performing well and discharging to watercourse. The process optimisation is due to be finished in August 2019.