Anchorsholme Long Sea Outfall (2019)
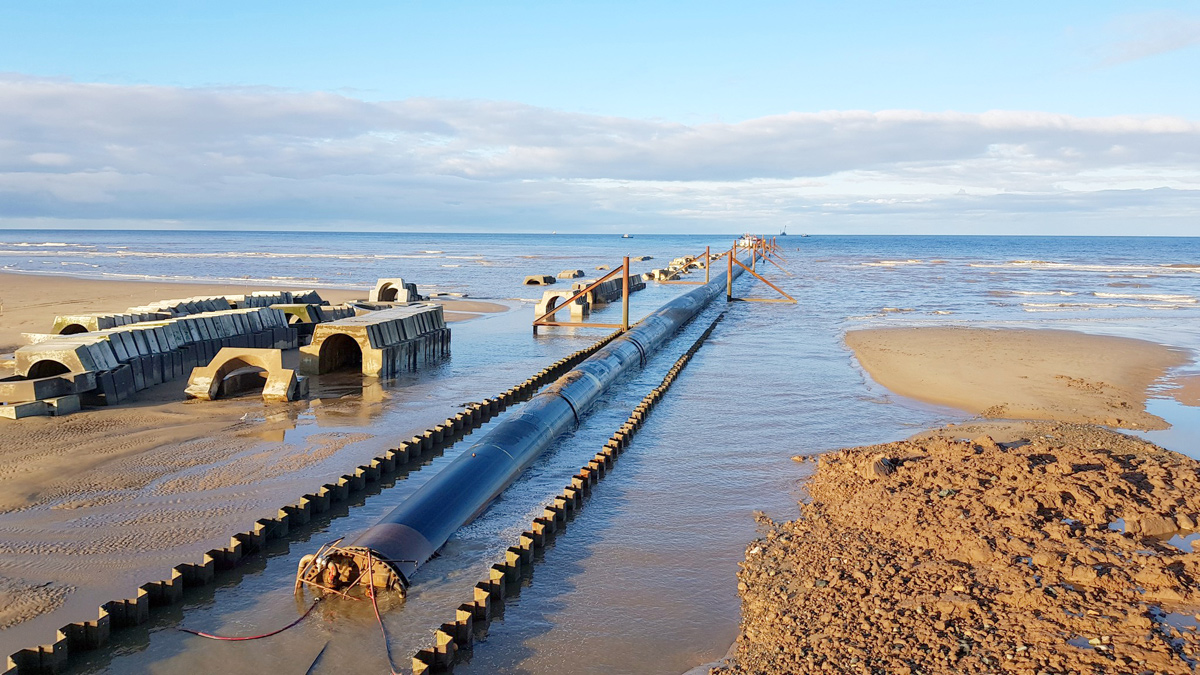
Pipeline being installed within cofferdam - Courtesy of United Utilities
Anchorsholme Park is located on the coast 4 miles north of Blackpool Tower. The long sea outfall (LSO) project is the third of three phases contributing to improving bathing waters on the Fylde Coast. The objective of the overall scheme is to complete the AMP6 obligations on the Fylde Coast of the ‘moving towards three spills per bathing season’ National Environment Programme (NEP) driver. The first phase to construct a 12,000m3 stormwater storage facility within the park was successfully completed in 2016 and was featured in UK Water Projects 2016. The construction of the 12m3/s outfall pumping station and renovation of Anchorsholme Park is the second phase, is due to be completed in late 2019.
The third phase is the construction of the 3.75km LSO, which is the focus of this article.
Project scope and pipeline selection
In July 2016, United Utilities (UU) awarded a design and build NEC3 Contract to J Murphy & Sons Ltd (JMS) whose supply chain partners included: Shay Murtagh Precast, Pipelife Norge AS, Rhode Neilson, Sheet Piling (UK) Ltd, Seawork Marine Services and J&M Fabrications.
The engineering and construction work undertaken by JMS involved the design and construction of a new 2.5m diameter solid wall polyethylene pumped outfall pipe to discharge the consented flows 3.75km offshore. Following detailed initial hydraulic concept design by UU Engineering and dispersion modelling, comprehensive discussions were held with the Environment Agency and a distance of 3.75km was agreed to minimise quality impacts on bathing waters.
At an early stage, UU decided that a polyethylene pipe was to be used to ensure the design life of the outfall was to be met. As a result, UU Engineering undertook the design of the pipeline in conjunction with Pipelife Norge AS, and subsequently purchased the 3.75km, 2.5m OD pipeline. This was to ensure that the outfall was guaranteed to be available for readiness in spring 2017. The pipe was vested to JMS once the main contract had been awarded.
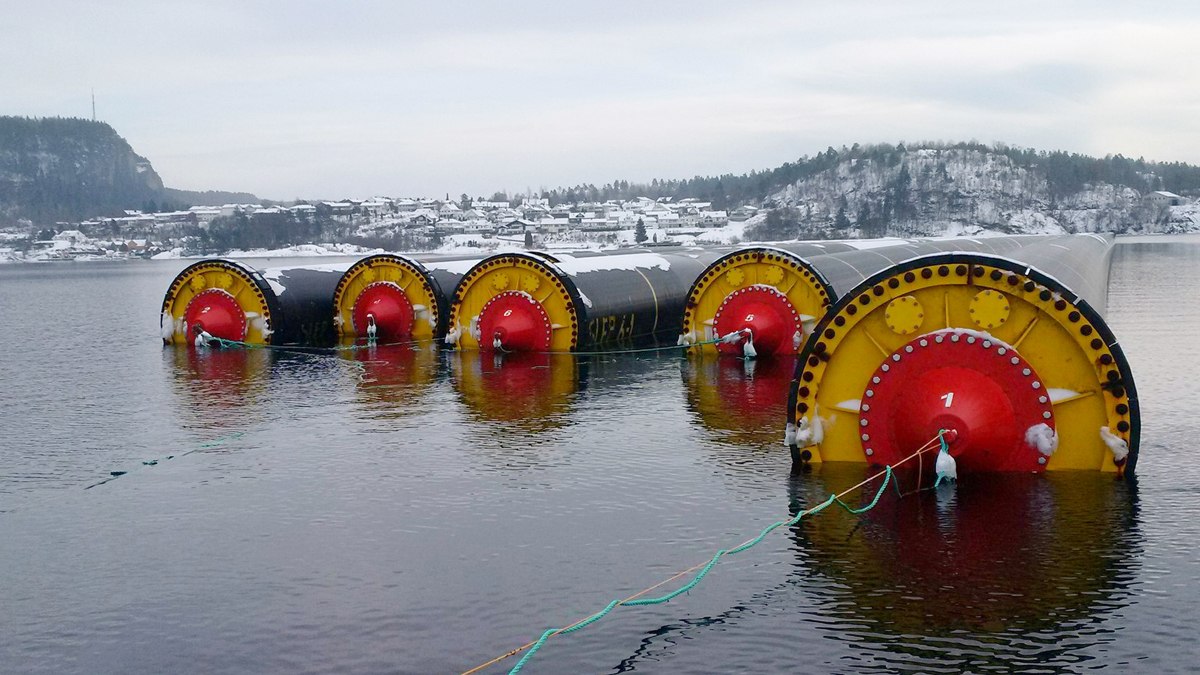
625m long pipes stored in Norway – Courtesy of Pipelife Norge AS
The contract with Pipelife Norge AS and UU included the fabrication of polyethylene (PE100 SDR 26) pipe in 6 lengths, each 625m long. The pipes are rated at 6 bar and have flanged stub ends for jointing with steel backing rings. UU has over 20 years of experience with Pipelife in a number of projects including Harrowside LSO (featured in the 2015 edition). Following contract award, JMS visited Pipelife’s facility to discuss the fabrication and delivery schedule. The technical specifications of the pipeline and proposed installation methodology were also discussed, including the pipe stresses during the flooding installation S-curve. Contact between all parties was maintained throughout the project to ensure that any technical and installation issues were managed throughout the design.
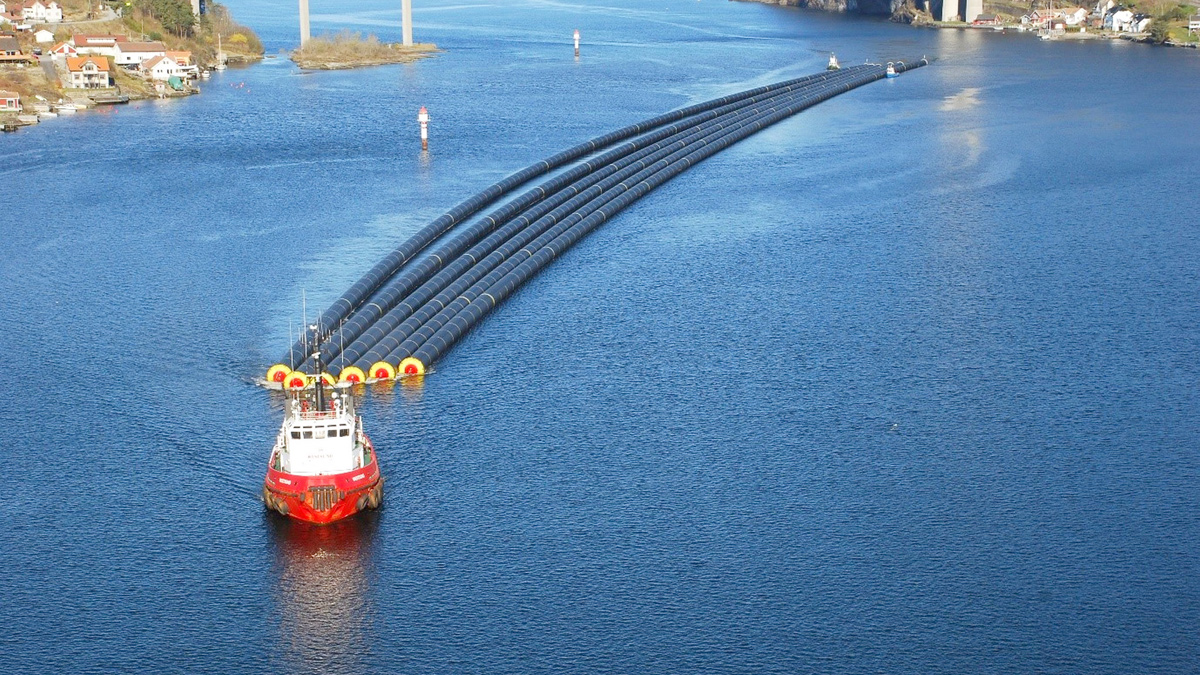
625m long pipes being towed from Norway – Courtesy of Pipelife Norge A/S
Temporary works design
To install the LSO, a trench was required from chainage 0m to 3750m. It comprised of a tidal cofferdam up to 455m and then a marine dredged trench from 455m to 3750m. In order to construct the works, including the tidal cofferdam, a compound area behind the sea defence at the edge of Anchorsholme Park was provided by UU in agreement with Blackpool Borough Council. A plant refuge area was also provided on the old upper and lower promenade for spring high tides, which was 600m from the work area.
A temporary ramp was installed by C2V+ in Phase 2 of the works to ensure that access was ready for this contract. A sheet piled enclosed cofferdam with ramp, was installed to provide a safe haven and provided shelter from the high neap tides to plant during periods of calm weather. This ensured that productivity was maintained, as the travel time from compound site took up to 30 minutes in each direction. The safe haven was also designed to include for a 100t winch spread to pull the floating pipe into the cofferdam.
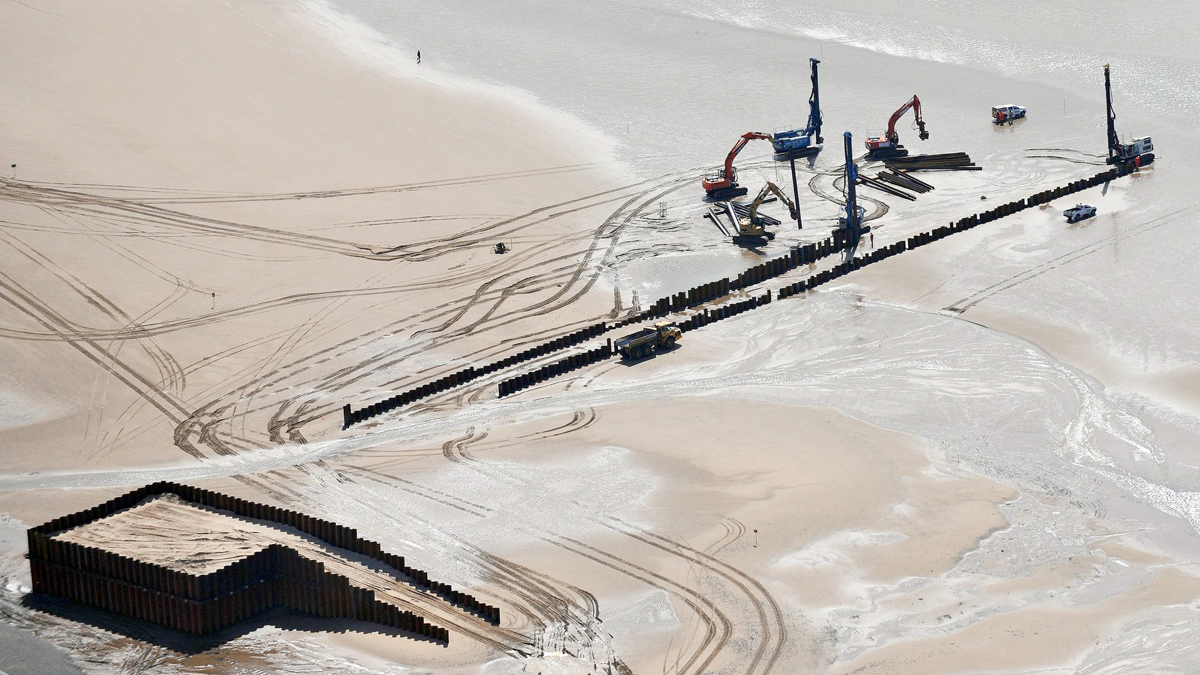
Cofferdam construction – Courtesy of United Utilities
The sheet piled tidal cofferdam was constructed throughout all times of the day to utilise the working window whilst the tide was out, with noise levels monitored throughout. The cofferdam was 7.2m wide, constructed from 12m piles and protruded 1.1m above the beach level at time of construction. This was to ensure that a safe level of edge protection was provided during the period of construction and to prevent the public from entering the trench. In addition there were markings on the beach and a 24/7 security presence. Circular guide piles constructed from 0.50m diameter steel tubes, were installed at 40m centres on alternating sides of the trench. These were installed to ensure the pipe stayed within the confines of the cofferdam in all states of the tide when being winched in.
The cofferdam was excavated to formation level using land based equipment during the low tides. The excavation was constantly maintained due to the sand infill from tidal beach changes.
Dredging and challenges of geology
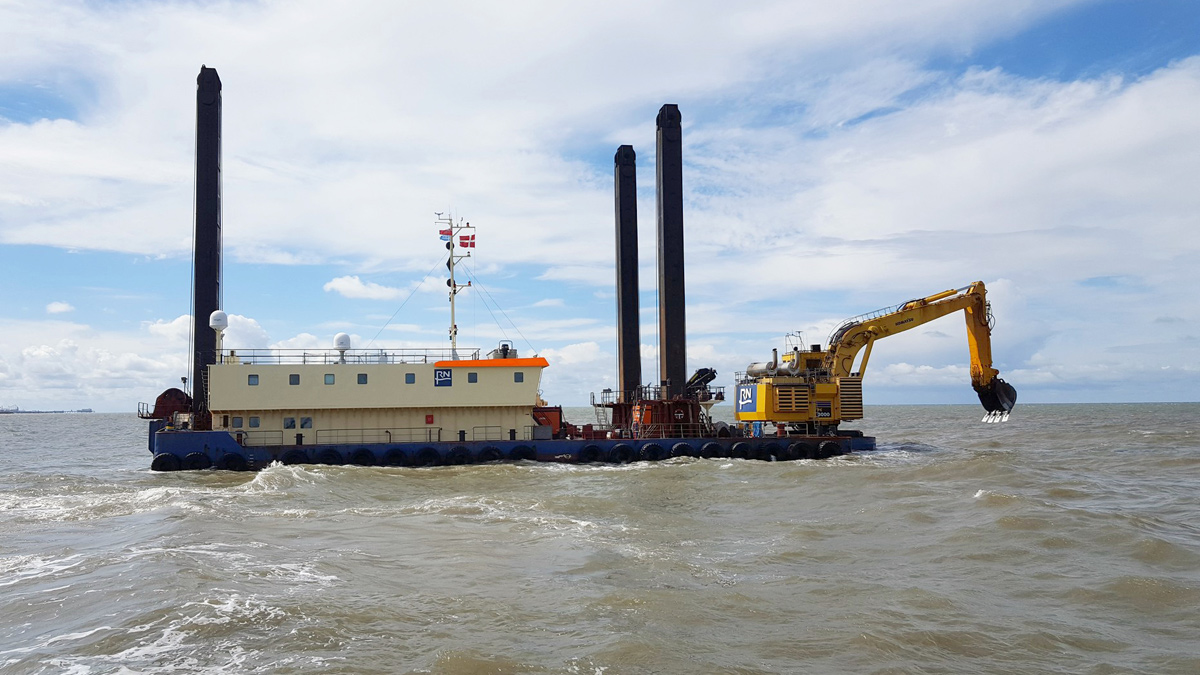
Mjolner dredging the hard clays offshore – Courtesy of Rohde Nielsen A/S
JMS’s dredging partner Rohde Nielsen A/S were subcontracted for the offshore dredging and backfilling works using the backhoe dredger Mjølner R (with attendant split hopper barges), grab dredger on DP Heimdal R and Trailer Suction Hopper dredgers Freja R, Njord R and Brage R in water depths of up to 20m.
The dredging scope was to create a trench of 3.3km long between the end of the beach cofferdam at mean low water and the offshore diffuser. The trench bottom width was a minimum of 6m wide to accommodate the 5m wide concrete ballast weights that were attached to the pipeline.
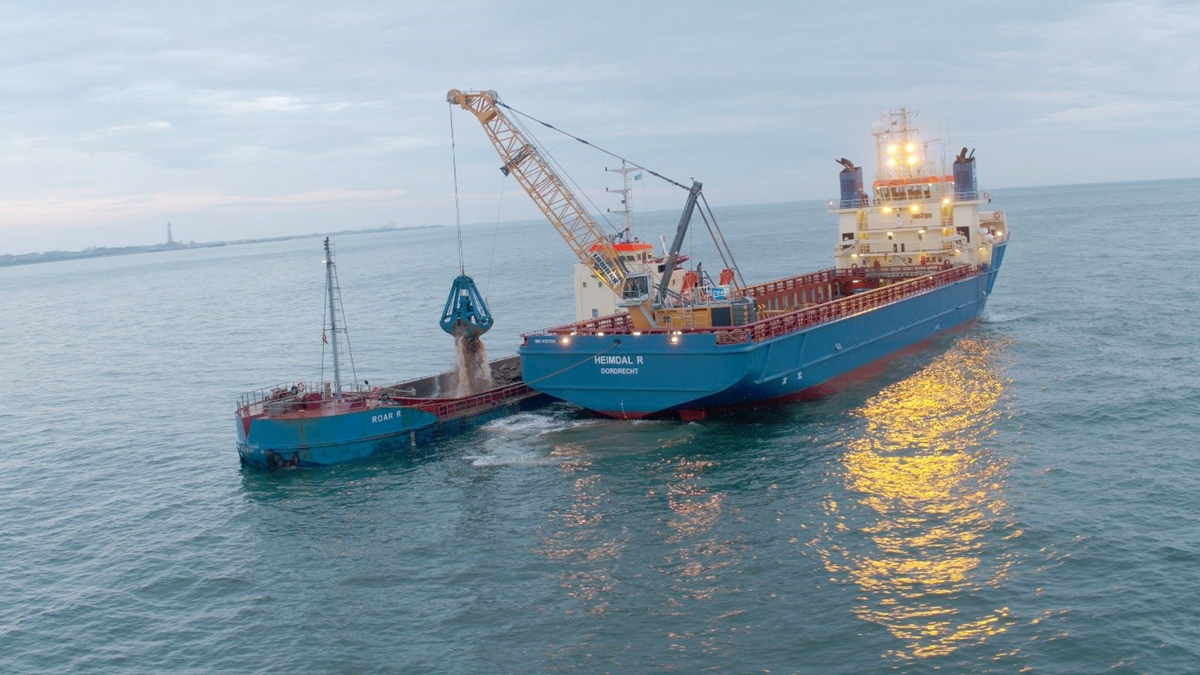
Heimdal R dredger in operation – Courtesy of Rohde Nielsen A/S
The material dredged was mostly sand (around 70% of the total volume of over 300,000m3) with hard clay underneath. The cohesive strength of the clay varied between 100kPa to 600kPa which required the full power of the 250Te excavator on the backhoe dredger to remove the stiffest clays. The trench design in sand was a 1:4 side slope and 1:2 in the clays.
The material was partly stockpiled alongside the trench through side casting or through dumping by split hopper barges in designated dump boxes along the trench. The clay was taken by the barges to the nearby offshore designated disposal area stated in the MMO licence.
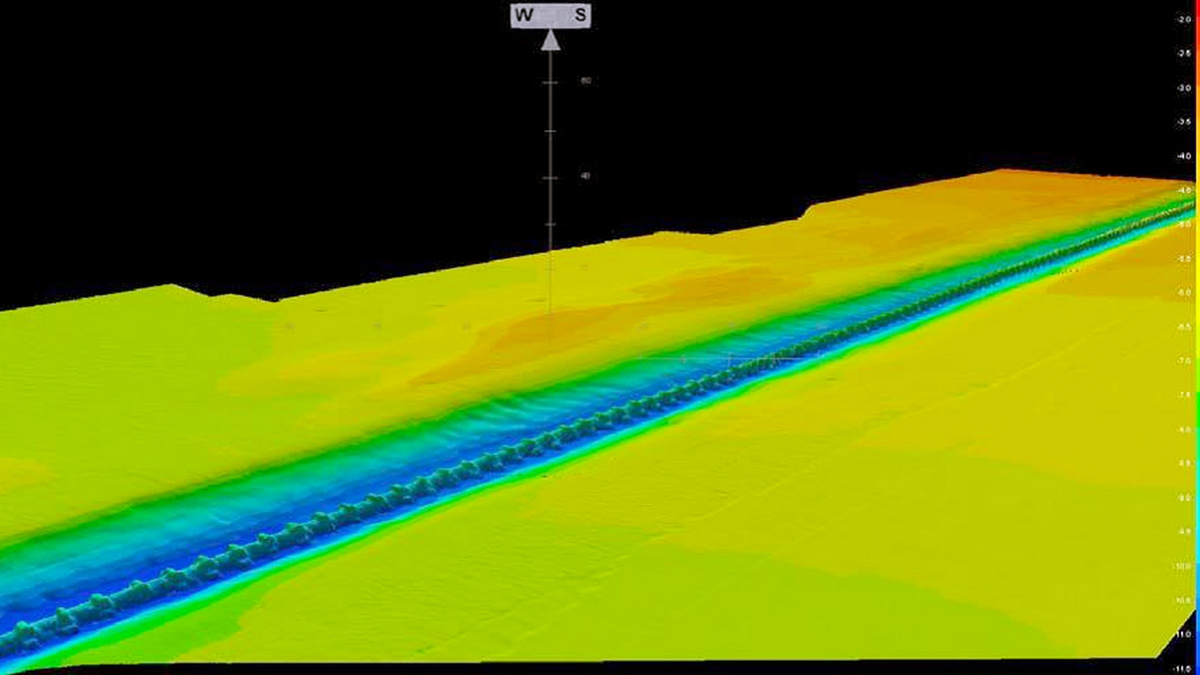
Ongoing surveys undertaken by Rimfaxe – Courtesy of Rohde Nielsen A/S
The survey vessel Rimfaxe R was used throughout the works with 24-hour cover, to ensure that the latest data was used to track progress and to update the on-board dredging computer allowing the operators to visualise the actual situation of the dredging area compared to the design.
The large 10m tidal range in combination with the swell conditions at Blackpool meant that careful planning was required to optimise the productivity of the dredging plant in the varying depths of water along the trench profile. Twice daily offshore weather reports were used to optimise the planning of the dredging and backfilling works with the nearby Port of Heysham and River Wyre used for shelter when required.
Pipe construction and Lough Foyle
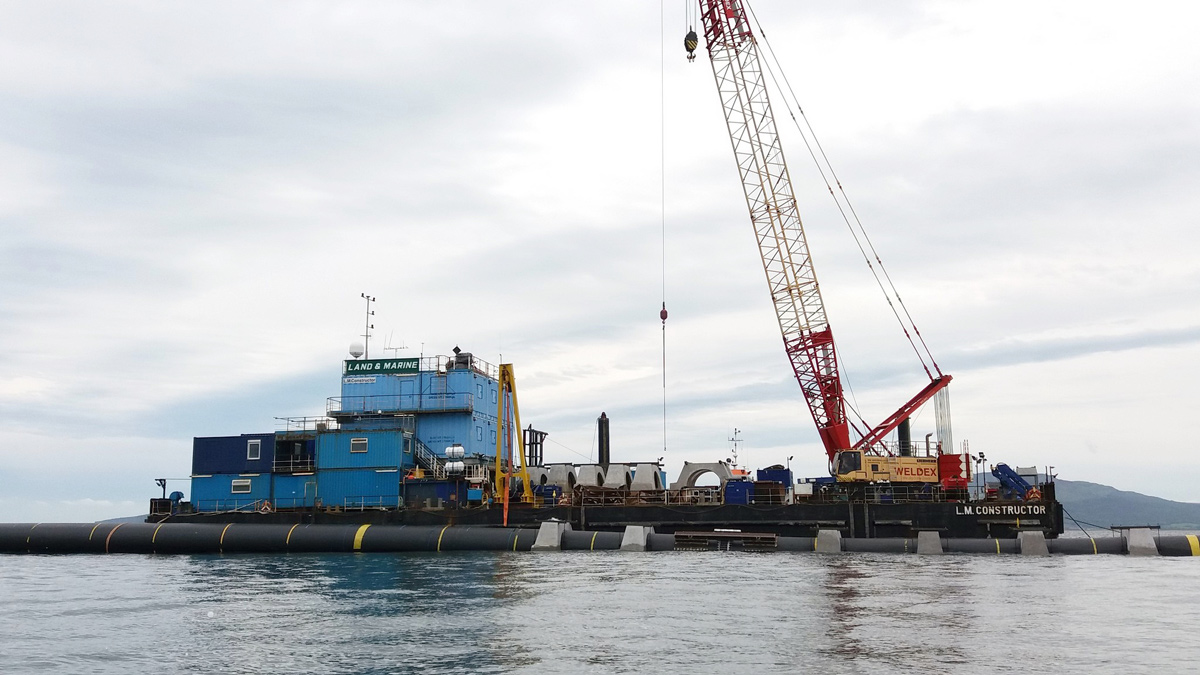
Pipe assembly in Lough Foyle using LM Constructor – Courtesy of J Murphy & Sons
Due to the large length of the outfall, it was necessary to construct the pipeline off site. Various locations around the Irish Sea were considered, before deciding to use Lough Foyle near Londonderry. The size of the Lough and the substantial facilities available at Foyle Port were the key factors in the decision to assemble the pipeline there.
To achieve the required permanent stability (min. SG of 1.35) 600 (No.) 25Te concrete ballast weights were needed. These were precast in Ireland by Shay Murtagh Precast and delivered to Foyle Port where they were offloaded, prepared and stored prior to transporting to the pipestrings in the Lough by barge.
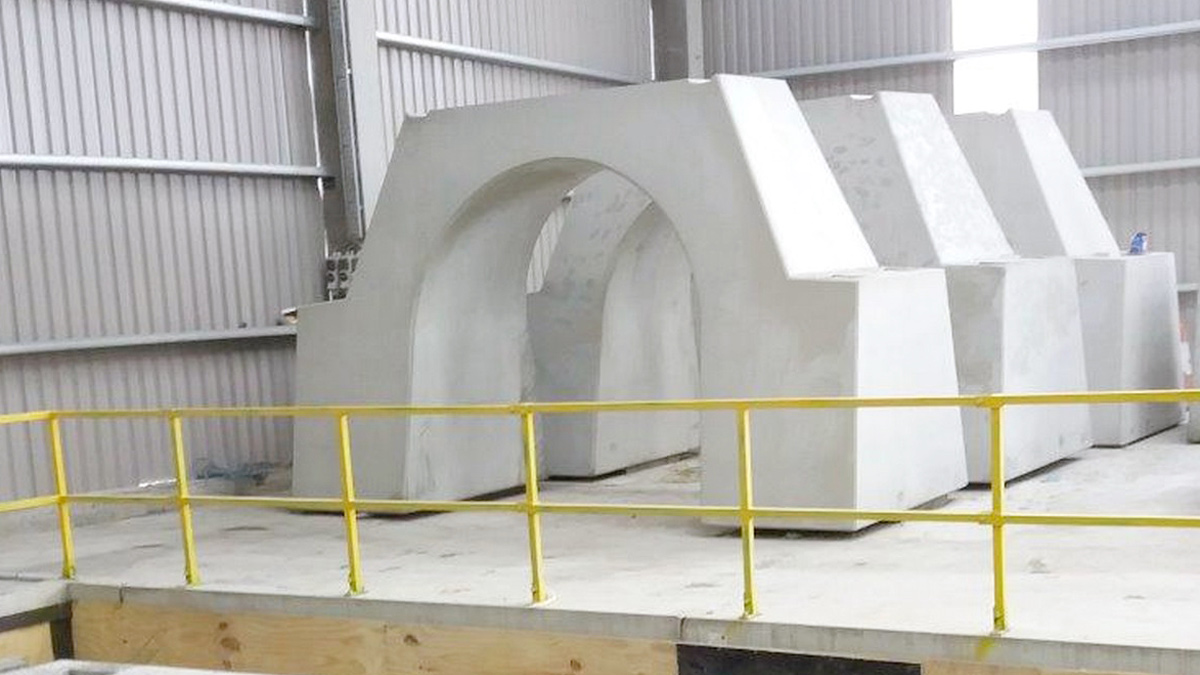
Shay Murtagh Precast concrete collars – Courtesy of J Murphy & Sons
In order to ensure the programme was met and quality standards maintained, Shay Murtagh Precast extended their precast factory and built a subterranean facility to allow the units to be lifted out by the standard overhead crane. This was predominantly due to the size of the precast mould and the amount of head room required to lift the mould off the precast element in the factory.
The quayside at Foyle Port had adequate storage space for around 100 concrete collars and large dock cranes were available to off-load. The concrete collars were installed onto the pipeline by JMS’ LM Constructor work barge, equipped with spud legs, 4-point mooring system and a 300Te crane. The pipestrings were connected together using a davit type lifting arrangement from the side of the LM Constructor.
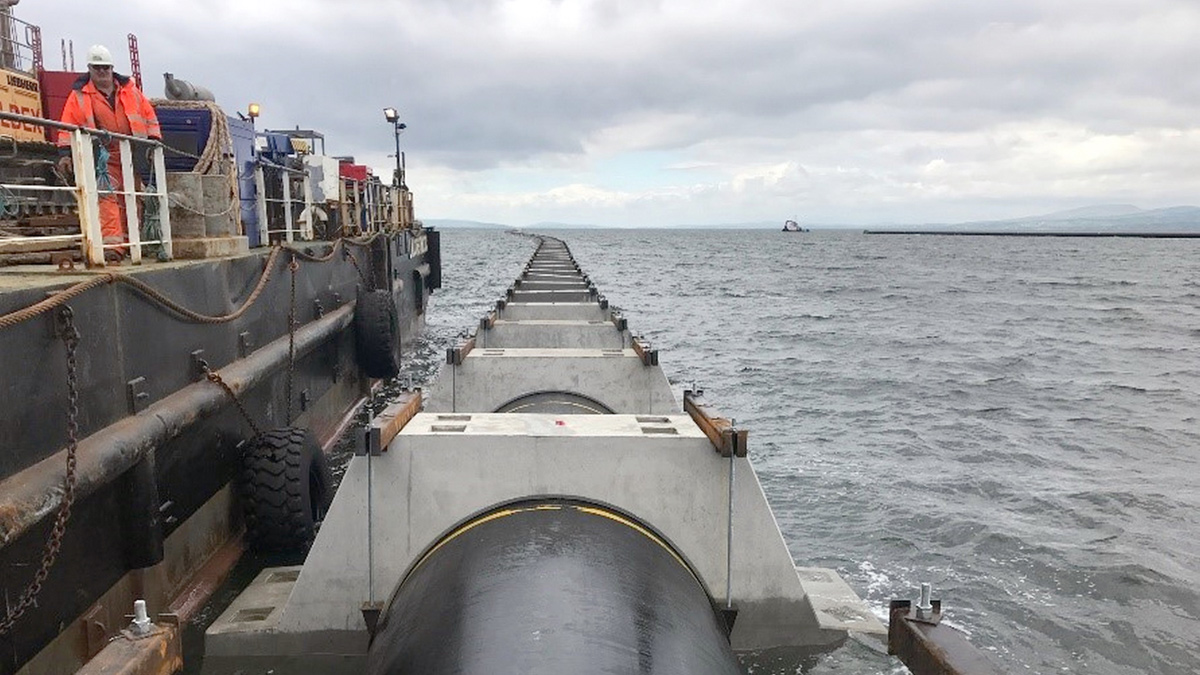
Concrete collars fitted in Lough Foyle – Courtesy of J Murphy & Sons
The 16m steel diffuser extension constructed by J&M fabrications was also installed onto the end of the pipe at Lough Foyle. This was bolted to the flange of the last pipestring; however the final diffuser riser assemblies were not installed. Instead, a temporary flooding arrangement was installed on the riser flanges for installation at Anchorsholme. All steel structures installed on the pipeline were protected by cathodic protection.
To ensure that the polyethylene flanges were not subject to forces outside the original S-curve design and there was no air loss through transportation/installation, JMS designed mild steel pipe stiffener frames. These sacrificial structures installed at every joint were 6m long, which ensured the clamp attached to the pipe 1m either side of the joint.
Pipe transport and installation
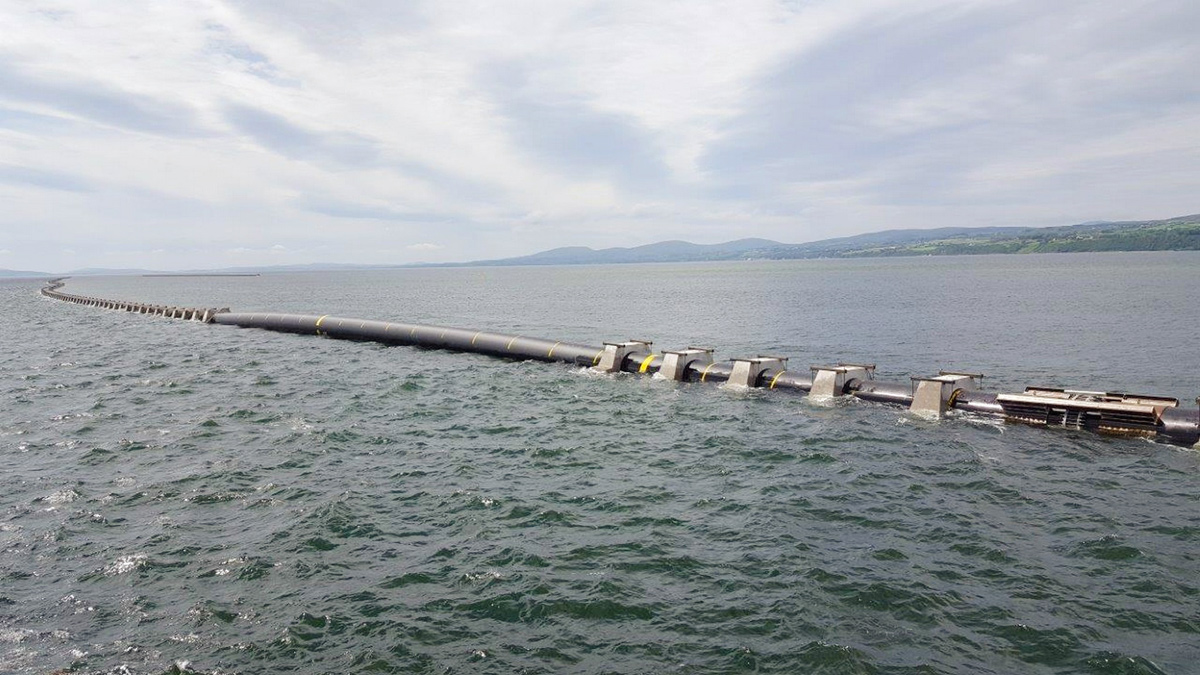
Pipe being assembled in Lough Foyle – Courtesy of United Utilities
Prior to the pipe tow, the entire trench had to be at the correct formation level to receive the incoming pipe, and due to the tidal conditions offshore at Anchorsholme there was significant infilling of wash sands into the trench. This meant that the 3.3km offshore trench was continually dredged on a daily basis by the Mjolner R and the trailer suction hoppers, which was then surveyed daily by the Rimfaxe R.
The 455m cofferdam section was maintained by land-based excavators and was surveyed by land based surveying techniques. The offshore section proved to be a little difficult, as the survey data showed that there was continuous infilling of the trench. Following detailed discussions and visual inspections using the Mjolner R, it was deemed that the survey beam was reflecting off a band of floating mud particles.
The pre-installation survey results confirmed that the trench was at the required formation and the pipe could be brought to Anchorsholme. Daily surveys and maintenance continued until the pipe arrived.
It was considered to install one pipe at a time and then undertake a subsea connection, however; due to the 5 connections required in a volatile coastal environment, it was decided to undertake the installation in a single 3.75km length. This was due to the availability and size of ports within a reasonable towing distance of the site, the potential for constant dredging around the installed pipe flanges, risk with the connections on the sea bed and the number of calm weather periods that would be required.
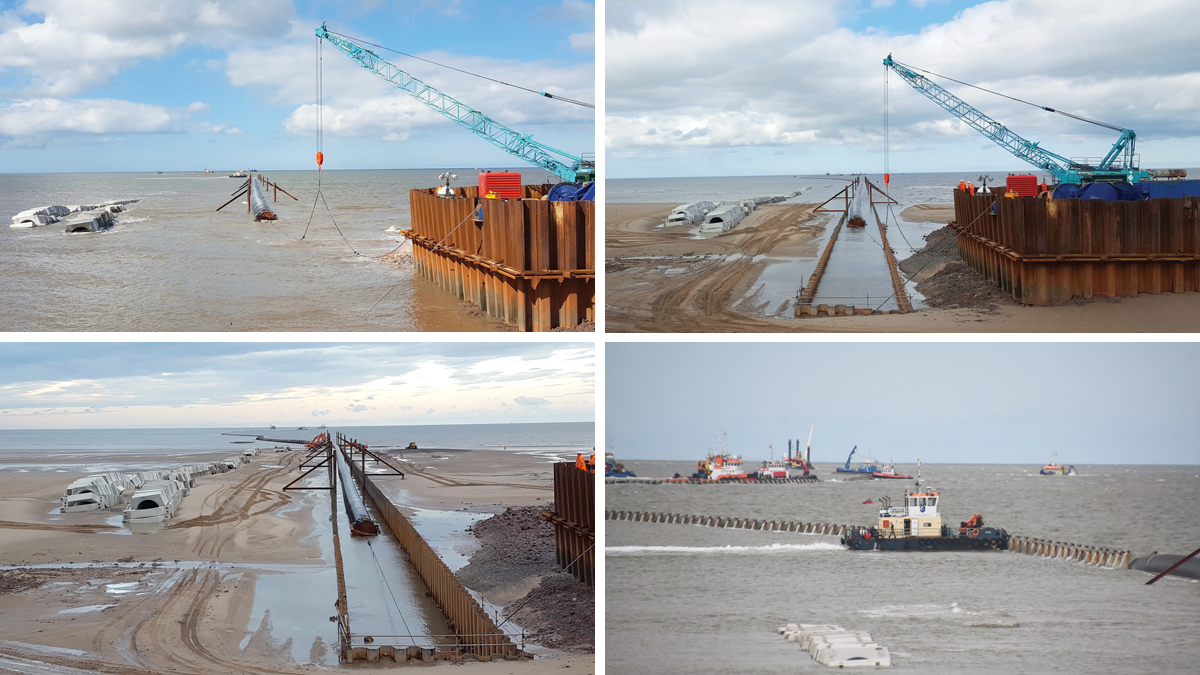
Installation of pipeline – Courtesy of United Utilities
JMS devised a towage route and detailed programme for the transport and installation of the pipe, and it was expected that it would take 5 days in total to undertake the works. Weather had to be assessed during all stages of the tow and installation to ensure that the weather did not exceed a force 5 on the Beaufort scale.
A pressure of 2 Barg was kept within the pipe throughout its journey across the Irish Sea, to ensure that if there were any minor leaks at the joints, the positive pressure would prevent the sea water entering the pipe during the 3-day tow. There was also a trail vessel attached to the pipe to keep tension during the tow, which ensured that the pipe was controlled during its journey to prevent any unnecessary stresses on the pipe and joints.
The pipe arrived at Anchorsholme as planned; however, due to the weather window changing rapidly and issues arising during the construction, it was decided to flood the pipe and sink it where it was. At this stage there was approximately 75% installed within the dredged trench with the diffuser in its final position.
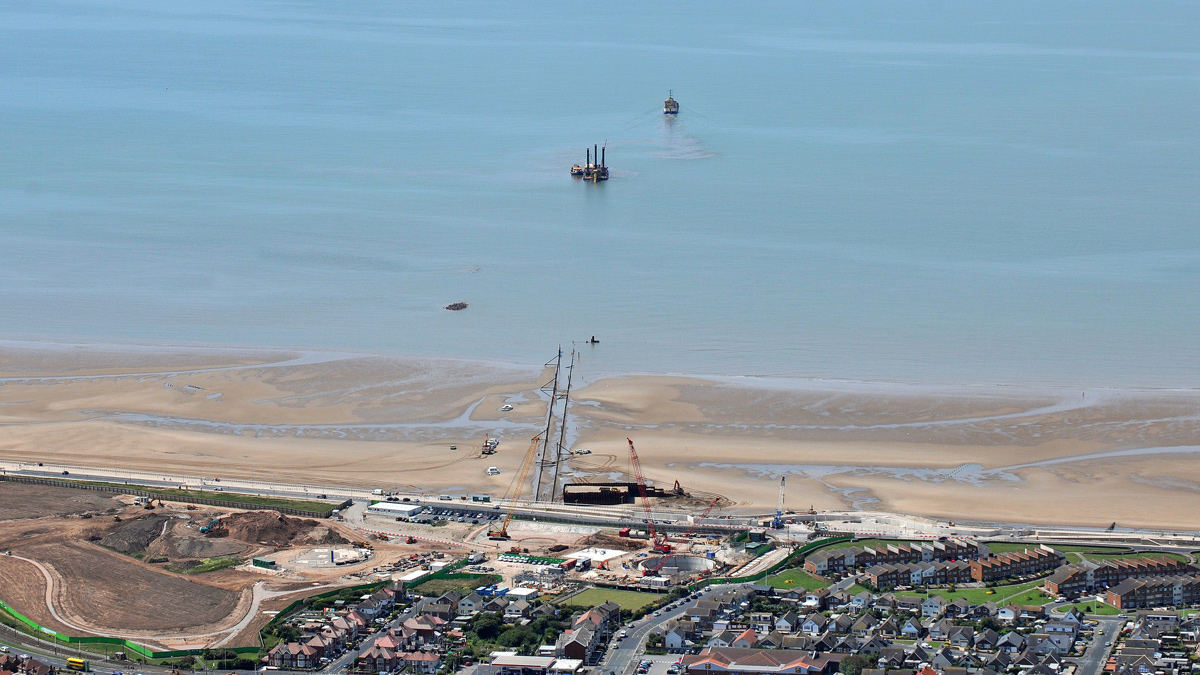
Aerial of the LSO under construction – Courtesy of United Utilities
Conclusion
Following extensive liaison with the Marine Management Organisation (MMO), a licence was provided to allow the works between April and September due to constraints with Wintering birds, which was identified in our Environmental Impact Assessment (EIA). The project team did exceptionally well to enable the complex project to hit its programmed installation date.
Installation and final commissioning of the pipe brought with it a unique set of challenges, which we will report on further when the project is completed.