Strongford STW – THP (2018)
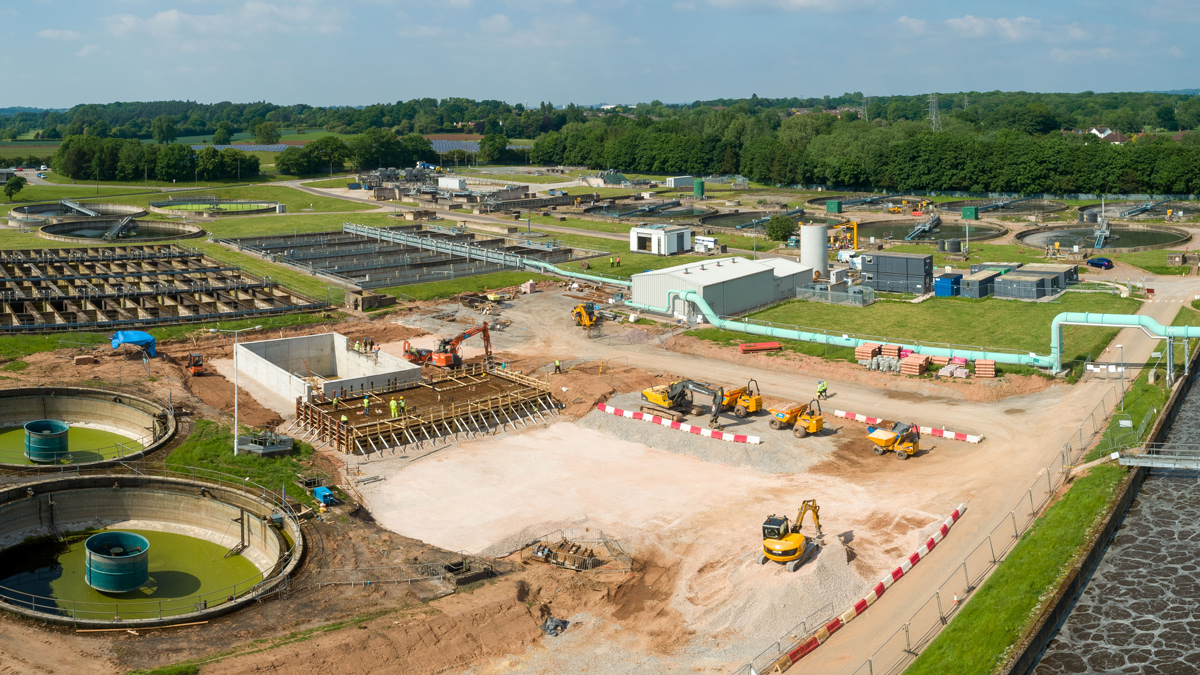
Looking north-east at the sludge dewatering, cake handling and THP area. Final preparations being made for the cake silos base slab concrete pour - Courtesy of Severn Trent Water
Strongford STW is located at the north west end of Severn Trent’s region and covers a significant catchment in and around Stoke-on-Trent with a population equivalent of 350,000. The Strongford digestion plant currently processes 34 tonnes dry solid per day (tds/day) indigenous; and 14 tds/day liquid imports which includes 7 tds/day from the recently closed digestion plant at Checkley. Going forward the plant will receive a further 19 tds/day as 23% dry solids (ds) cake from the digestion plants planned for closure at Coalport, Four Ashes (Cannock) and Brancote (Stafford). This gives a total base load on the plant of 66tds/day. There is scope within the local authority planning permission for this to rise to 80tds/day (no net change in traffic movements). Exploiting the full capacity of the proposed THP would require a different way of importing sludge and/or exporting digestate.
Benefits of the thermal hydrolysis plant (THP)
Adopting thermal hydrolysis as part of the sludge recycling process helps Severn Trent Water meet a number of strategic and tactical goals including:
- Increasing renewable energy production.
- Increasing sludge recycling land bank security with enhanced sludge product.
- Reducing operation costs.
The Strongford THP team is regularly tapping into knowledge and experience being gained as Severn Trent Water’s first THP plant at Minworth STW (Birmingham) goes into operation.
Undertakings and budget
The budget for the whole project is £33.6m. This includes £27.4m for the work at Strongford STW and £6.2m to install thickening and dewatering facilities at three satellite sites where existing single digester plants will be closed and sludges exported to Strongford. Doosan Enpure Ltd is acting as CDM principal designer and principal contractor for the works at Strongford.
Existing STW and sludge treatment facilities
The existing STW consists of inlet, primary and storm settlement, a mix of carbonaceous and nitrifying ASPs and NSAF. The final effluent consent in mg/l is BOD:12/SS:30/ NH3 :3/P:1.
An existing mesophilic anaerobic digestion plant consists of 4 (No.) 2500m3 and 3 (No.) 3000m3 conventional mesophilic anaerobic digesters. The plant has a throughput of up to 48 tonnes dry solid (tds/day). In practice, this is up to 1000m3 of sludge per day. The primary heating source is 2 (No.) 1000mW Jembacher biogas fired CHP engines with supplementary biogas only boilers available to assist. All additional gas is passed to a Malmberg gas upgrade plant from where it is exported to grid.
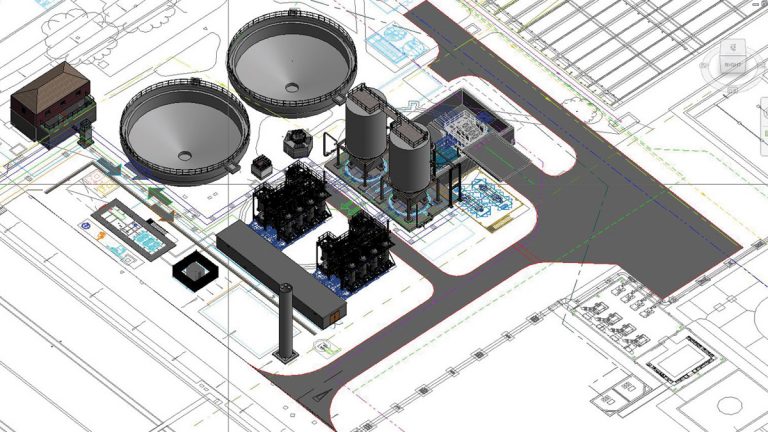
Partial image from 3-D model of sludge dewatering, cake handling and THP area (looking north-west) – Courtesy of Severn Trent Water
Proposed work at Strongford
Indigenous and imported (liquid) sludges – imported sludge cake: At the front end, handling of indigenous sludges and liquid imports will remain largely unchanged. Low percentage dry solids sludges will be thickened (primary and SAS separately) to target 6% dry solids before being mixed with imports, strain pressed and pumped to the new sludge handling facilities.
Here sludges will be dewatered to target 23% dry solids in one of 2 (No.) Alfa Laval G3 centrifuges (duty/duty) and stored in one of 2 (No.) CTM Systems Ltd 300m3 silos. Imported cake will be delivered to a below ground 31.5m3 bunker and transferred by 2 (No.) Mono Pumps model No. C21D (duty/duty) into the silos. Silos are dedicated one per THP stream. Sludges are transferred from the silos with 2 (No.) Mono Pumps model No. W1BC (duty/standby) and re-watered to a target 16% dry solids using primarily final effluent, but with an option to supplement with liquid imported trade waste.
The thermal hydrolysis plant: After some considerable work with potential suppliers the team has settled on Cambi for the supply of the THP plant. It will consist of 2 (No.) streams of its B4 model (with a combined maximum throughput of 94 tds/day).
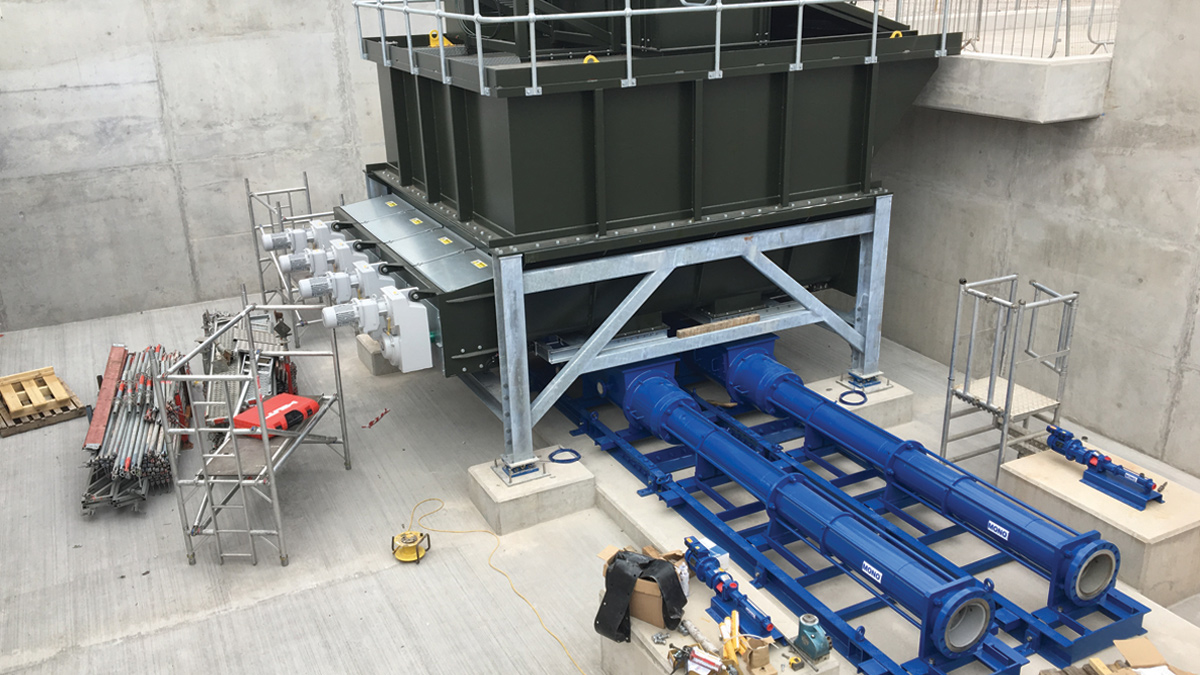
CTM Systems Ltd cake reception equipment being installed – Courtesy of Severn Trent Water
THP heating: The THP process heats and holds sludge at 160°C at 6 bar pressure for 45 minutes. The heating medium is steam. Steam for the THP will be generated by 1 (No.) Steamatic Fire Tube steam boiler (model FT 400/15/Biogas–CH4) and 1 (No.) heat recovery steam boiler (model FTR 400/15/BIOGAS-CH4/ Combi) both with capacities of 3.080kg/h generation.
Both boilers, incorporating CIB-Unigas burners, are supplied by Thorne Industrial Boiler Services. In addition, boiler water feed will be pre-heated using:
- Jacket and exhaust heat recovered from a new Jembacher 420 biogas fuelled combined heat and power (CHP) engine supplying electricity into HV ring main around Strongford.
- Water loop used to cool sludges exiting the THP.
The CHP engine is supplied and installed by Clarke Energy Ltd contracted directly to Severn Trent. The civils and all other infrastructure to agreed battery limits is provided by Doosan.
Mesophilic anaerobic digesters (MADs): After THP Process, thermally hydrolysed sludges will be passed forward to the MADs which will have been refurbished. During the transfer, sludges will be cooled to 55° and thickness reduced to target 10.5% using a combination of HRS heat exchanges and mixing with micro-strained and UV treated final effluent. UV treatment will ensure digested sludge retains its enhanced status. The UV treatment plant is being designed and delivered by Doosan.
Emptying cleaning and inspection: Six out of the 7 (No.) digesters will be refurbished and upgraded to receive THP sludges. Digesters will be taken out of service, one at a time, for refurbishment. The task of emptying purging and cleaning is outside Doosan’s scope. This work is being undertaken by GTS Maintenance Ltd managed by ST Digester Cleaning Team.
Empty digesters are then force vented and handed over to Doosan. Digesters are inspected using a camera fitted to a drone. At this stage it will be determined whether a full birdcage scaffold will be needed to facilitate repair/replacement of the gas space lining or a single tower scaffold to enable installation of gas mixing manifold feed pipes only.
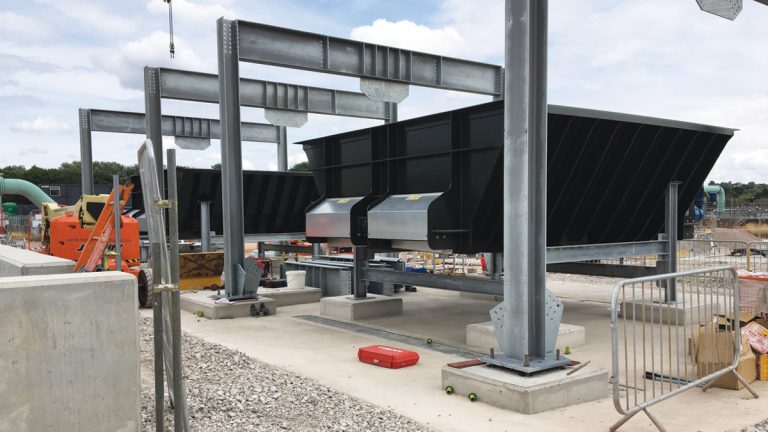
Completed sludge silo base with bottom section of silos fitted – Courtesy of Severn Trent Water
Digester modifications/refurbishment: Digester refurbishment comprises stripping out the existing gas mixing equipment then re-fitting with new. Mixing will remain a continuous unconfined type. A single ring of diffusers in the digester base is to be replaced with two concentric rings of leaf-spring diffusers connected by dedicated down-pipes from a manifold on the digester roof.
The duty-only gas compressors at ground level on each digester will be replaced. All this work is being undertaken by Utile Engineering.
Replacement temperature probes, new radar level detection, foam detection and the facility for retro-fitting foam suppression later, are all installed at this stage. Inlet and outlet pipework is to be modified to take on board lessons from Thames Water published in a paper by Fountain and De Macedo.
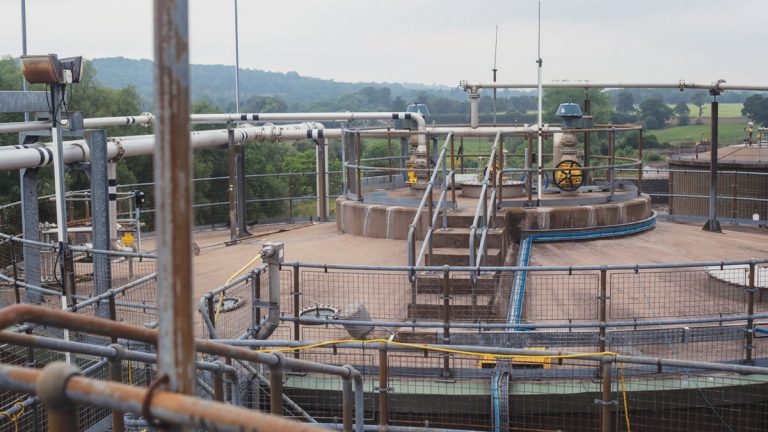
Existing digesters are refurbished to deal with THP’d feed sludges. Roofs are fitted with radar level measurement, foam detection and foam suppression equipment – Courtesy of Severn Trent Water
Modifications to the digester outlet will lower the top water level and increase the gas space to mitigate the potential effects from low density mousse-like sludges often found in the upper portions of post-THP digesters. Digester refurbishment is being undertaken by North Midland Construction or one of their suppliers under a sub-contract agreement with Doosan.
Gas system changes: The completed plant will produce significantly more biogas than the plant does at present. The gas system modelling by Utile Engineering has identified the need to modify and reinforce some of the gas pipework. Further amendments are required to ensure the plant matches Severn Trent’s design manual recommendations. Changes include:
- A new gas holder.
- A new gas flare and vent.
- Replacement pressure/vacuum valves.
- Re-orientation of some pipework to separate gas producing and gas consuming elements in relation to the gas holder.
Treating post-digestion dewatering liquors: MADs fed with thermally hydrolysed sludge produce sludge and post-digestion dewatering liquors with significantly higher levels of ammonia than conventionally fed MADs.
Dewatering liquors currently return to the head of Strongford works without any special treatment and contain, on average, 700kg/ammonia per day. Going forward it is expected that the liquors will contain up to 2,700kg of ammonia per day. The project team is working through a number of options on how to provide the best TOTEX solution for treating these liquors both in the short, medium and long term.
A solution using the lanes and final tanks of an abandoned ASP is likely. Historical and ongoing calcite issues in centrate lines has precluded the use of lime to provide alkalinity in more traditional approaches (eg: ASP or oxidation ditch).
Site constraints
The sludge cake reception, sludge dewatering, THP equipment including the boilers and CHP, will be sited as close as possible to the existing sludge thickening and digestion plant. The plot allocated is a restricted area on all sides. It is bounded by an elevated air pipe to existing ASPs, site road and the abandoned ASP2.
Two final settlement tanks (FSTs) have to be demolished to make way for the new equipment, whilst 2 (No.) FSTs will be retained for possible incorporation into the liquor treatment solution.
Strongford STW Thermal Hydrolysis Plant: Key Project Participants
Contracted directly with Severn Trent Water
- Digester emptying, cleaning and recommissioning: GTS Maintenance Ltd
- Combined heat and power engine: Clarke Energy Ltd
- Delivery of THP, CDM principal designer and principal contractor: Doosan Enpure Ltd
Contracted directly with Doosan Enpure
- Civils construction and digester refurbishment: Galliford Try
- Cake reception plant: CTM Systems Ltd
- Cake reception pump supplier: Mono Pumps Ltd
- Thermal hydrolysis plant: Cambi UK Ltd
- Centrifuges: Alfa Laval Ltd
- Sludge storage silos: CTM Systems Ltd
- Sludge screen/strain presses: Huber Technology
- Polyelectrolyte silo, make-up and dosing: Richard Alan Engineering Company
- Safety showers & eyebaths: Aqua Safety Showers International Ltd
- Steam boilers: Thorne International Boiler Services Combustion Ltd
- Heat exchanger sludge coolers: HRS Group Ltd
Sub-contracted to North Midland Construction
- Civil designer: GHD
- Gas compressor/mixing: Utile Engineering Company Ltd
- Formwork, reinforcement and concrete: TCL Structures Ltd
Progress
At the time of writing (June 2018) work to clean out and refurbish the existing MADs has begun – three digesters have been emptied, cleaned and inspected. In each case no work has been required to gas space liners. Not having to install complex scaffolding has saved time and money on this section of the work. New mixing equipment and inlet and outlet pipework has been installed; and the first two digesters have been put back into service.
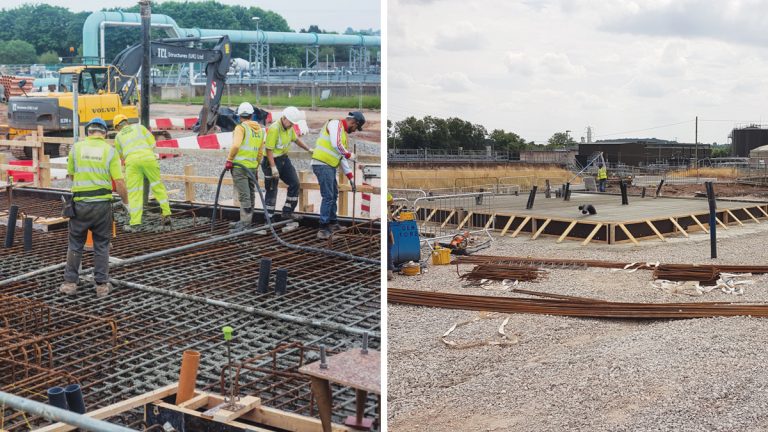
(left) Part way through 190m3 concrete pour of the sludge cake silos base and (right) surface finishes being applied following concrete pour at CAMBI base No. 1: Courtesy of Severn Trent
Elsewhere on the site the two of the four redundant FSTs have been demolished. This has made way for the deepest chamber on the site to be constructed. This structure will contain the import sludge cake reception bin and cake handling equipment. Completion of this structure has allowed backfilling of this area which releases work areas for sludge silo bases, and very soon after that areas for boiler, CHP engine and THP equipment itself.
Construction work is programmed to finish December 2018; with the first sludges thermally hydrolysed in February 2019. Plant handover is due in July 2019. Work on satellite sites will follow on from so the plant will be running at the intended 66tds/day throughput by February 2020.