Leominster WwTW (2024)
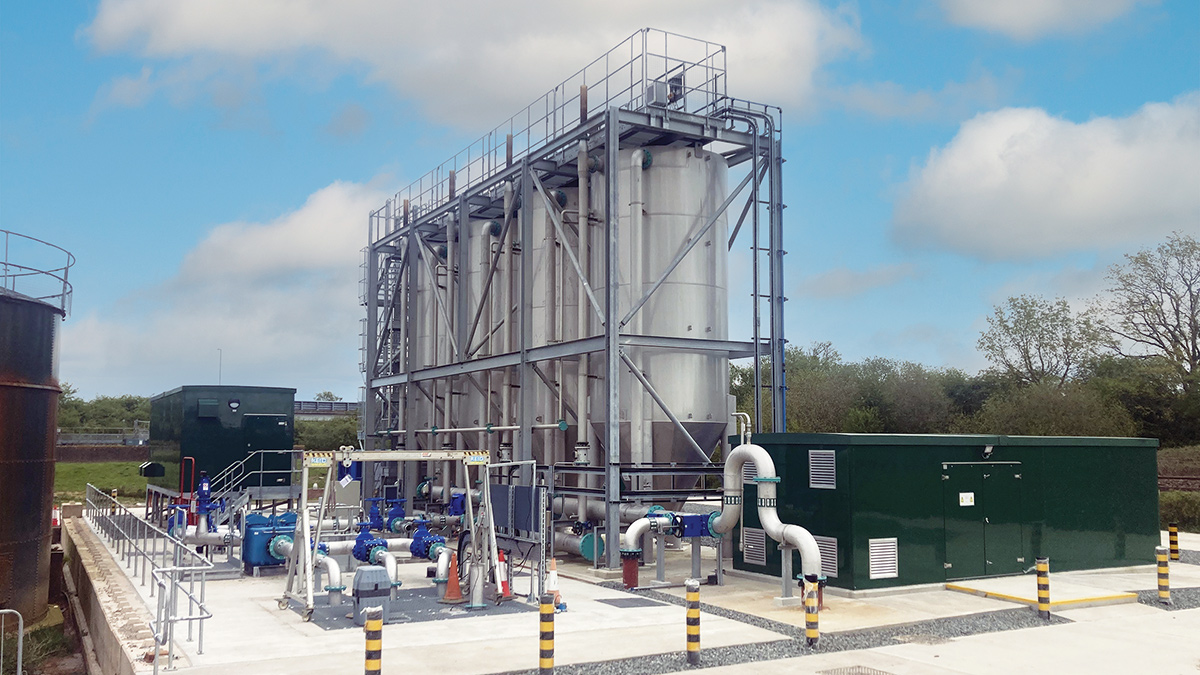
Leominster WwTW: New tertiary nitrifying sand filter system for phosphorus removal - Courtesy of Morgan Sindall Infrastructure
Leominster WwTW is a medium sized biofilter sludge works, treating a population equivalent of approximately 11,000. Welsh Water have invested £12.1m to deliver the process enhancements at the works as part of Welsh Waters’s commitment to deliver on improved water quality in the Wye River basin catchment. Other enhancement works were completed on existing sites including Eign, Rotherwas and Kingston & Madeley WwTWs. As part of the National Environmental Programme (NEP) commitments to meet the obligations of the Water Framework Directive in AMP7, new permit limits were put in place for 31 March 2025. The project exceeded this milestone by one year, achieving the tightened permit and Welsh Water’s annual commitment for river reach improvement.
Existing works
In advance of the improvement scheme, the works comprised an inlet works, primary settlement tank (PST), seven mineral media biofilters, two humus settlement tanks (HSTs), ferric dosing, two storm tanks and sludge storage.
The works treated mainly domestic sewage from the catchment of Leominster, Herefordshire.
The planned improvement works
The upgraded Leominster WwTW is designed to cater for increased treatment flows equating to a design horizon population equivalent of 16,685 (46% growth) and a tightening of the phosphorus permit from 1mg/l to 0.5mg/l. The new works design included for the integration of the following process improvements into the existing treatment works infrastructure:
- Four new tertiary nitrifying sand filters (including a tertiary lift pumping station and backwash returns system).
- New ferric sulphate dosing system for primary, secondary, and tertiary dosing points of application (including a new dosing equipment kiosk and safety shower).
- New sodium bicarbonate dosing system to supply additional alkalinity to the process for pH correction (including a chemical storage silo and dosing system).
- Inlet works refurbishment, upgrading the two existing escalator screens with two new 6mm screens, screenings trough, screenings transfer to two new compactors.
- New passive bypass screen with improved operation and maintenance access provision.
- New access platform around the screens to reduce the need for operator access into confined space areas.
- New potable water booster pumping station.
- New final effluent sampling system.
- New low voltage distribution board and inlet works MCC.
- New tertiary treatment MCC.
Scope of works
As part of Welsh Water Capital Delivery Alliance (CDA), Morgan Sindall, in partnership with designers, Arcadis, was appointed as the main contractor by Welsh Water. The scope of works for the project included the investigation, assessment, design, procurement, construction, and commissioning of existing and new treatment facilities; thus providing capacity to treat increased sewage loadings to meet discharge permit standards agreed with the Environment Agency (EA).
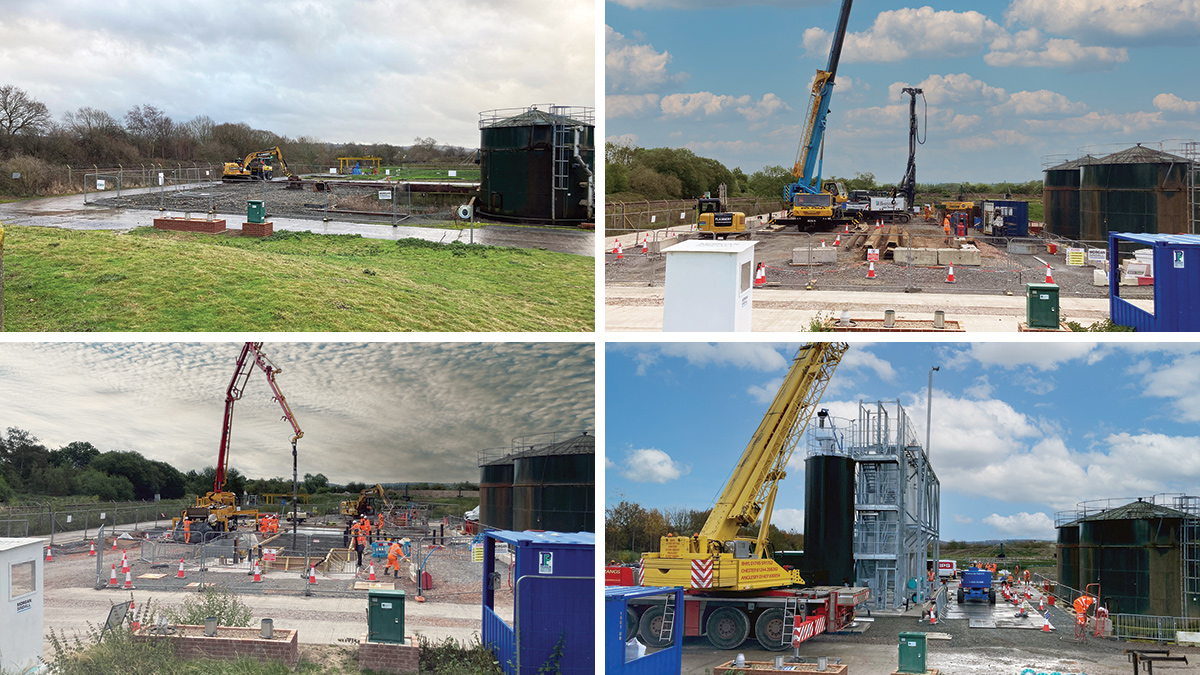
(top left) Construction of tertiary treatment system December 2022, (top right) construction of tertiary treatment system May 2023, (bottom left) Construction of tertiary treatment system July 2023, and (bottom right) Construction of tertiary treatment system November 2023 – Courtesy of Morgan Sindall Infrastructure
Innovative solution selection
Welsh Water, Arcadis and Morgan Sindall collaboratively assessed multiple options as part of the optioneering phase of the outline design, which included optioneering workshops for shortlisting, and risk and value assessments to select the most cost-effective solution based on whole life cost and risk. A schedule of innovative solutions included:
- New nitrifying sand filter to combine the need for tertiary solids removal, to achieve the tightened phosphorus permit, and increase nitrification capacity to relieve pressure on the works to meet the existing ammonia permit. Removed need for additional secondary treatment.
- Re-use of the inlet structure for the new 6mm screens, improving access and removing need to go in confined space during routine maintenance procedures.
- Re-use of the existing ferric sulphate storage tanks.
- Assessment of innovative alternative chemical to ferric sulphate (rare earth minerals).
- Use of BIM 3D modelling to ensure integration of mechanical design and location for the alkalinity silo and tertiary plant and avoid clashes with existing underground pipework.
- Gravity fed sampling system for final effluent monitoring.
- Design for Manufacture and Assembly (DfMA) MCC kiosk (used in the development of Welsh Water standard design).
- Re-assessed the need to refurbish existing sludge holding tanks through modification of sludge imports.
- Re-use of old Dortmund style rectangular/pyramidal standby PSTs.
- Re-purposing and re-establishment of area of works with abandoned process treatment assets– reducing the need for land purchase.
- Utilise existing static mixers on secondary ferric sulphate dosing.
- Ferric sulphate dosing flexibility (primary, secondary and tertiary).
Project initiation and whole supply chain early engagement
The overall delivery programme for the treatment upgrade scheme at Leominster presented the Welsh Water CDA team a challenge to meet the NEP regulatory output dates for end of March 2025 and ODI date for 31 March 2024. To efficiently meet this milestone, the team developed a joint collaborative plan to work to with the key project stakeholders, including members from Welsh Water asset and operations teams and key supply chain members.
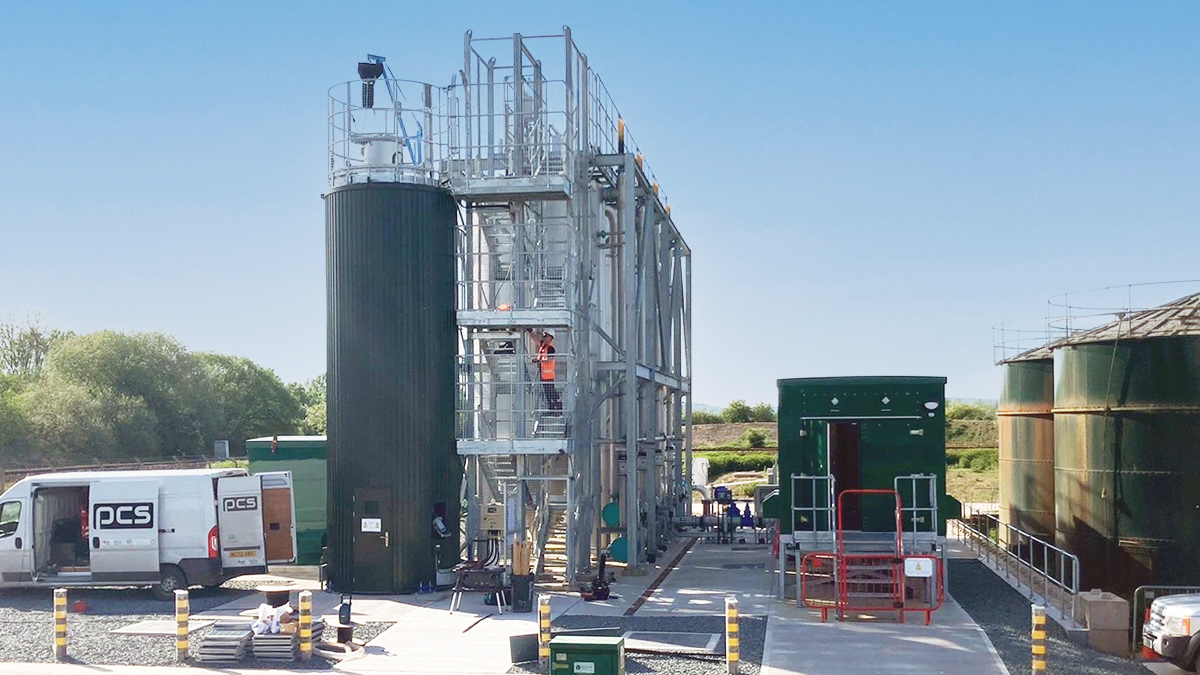
Construction of tertiary treatment system February 2024 – Courtesy of Morgan Sindall Infrastructure
The development of up-front outline design specifications and subsequent letting of Early Contractor Involvement (ECI) contracts with the supply chain allowed for all parties to truly work collaboratively in setting out and advancing the design strategy in an efficient manner. The ECI contracts enabled the supply chain and Arcadis to work together in an open and transparent manner through driving greater design efficiencies through sharing of ideas, skills, industry experiences, true value engineering opportunities, developing design and construction innovations, all resulting in a positive influence to the final scheme solution.
The successful working relationship was maintained through regular joint online progress meetings and workshops, where design efficiencies were discussed and implemented, and where any potential blockers were removed, to benefit design and construction. Other joint stakeholder meetings which assisted the advancement of the delivery programme included HAZOP’s, Access, Lifting and Maintenance (ALM) reviews, DSEAR meetings, referencing lesson learnt from previous schemes, progressing DfMA opportunities, production of outline commissioning plans early, and holding regular buildability review meetings as the design progressed. Having a common project management system, where all members of the joint delivery team shared information, was hugely beneficial, in addition to the open access to the scheme’s federated 3D BIM model.
Leominster WwTW: Supply chain – key participants
- Client: Welsh Water
- Principal contractor & civils: Morgan Sindall Infrastructure
- Designer & environmental consultants: Arcadis
- CFA piling rig: Foundation Piling Ltd
- Shaft installation: B&W Tunnelling Ltd
- Sheet piled interlocked cofferdam: Berryrange Ltd
- Mechanical installation: Industrial Pipework Services Ltd
- Electrical installation: PCS Ltd
- Earthing specialist subcontractor: BEST Services Ltd
- Tertiary nitrifying sand treatment: Brightwork BV
- Tertiary nitrifying sand treatment: Nijhuis Industries UK & Ireland
- Ferric dosing system: Colloide
- Alkalinity dosing system: Rospen Industries Ltd
- MCC & ICA controls: GPS Group
- Kiosks: Morgan Marine
- PLC network: Mitsubishi
- Below ground access chambers: Cubis Systems
- Pumps: Xylem Water Solutions
- Inlet screens and screening handling: SPIRAC Ltd
- Potable water booster system: Dutypoint Ltd
- Static mixer: Statiflo Ltd
- Temporary pump specialist: Hydrainer Pumps
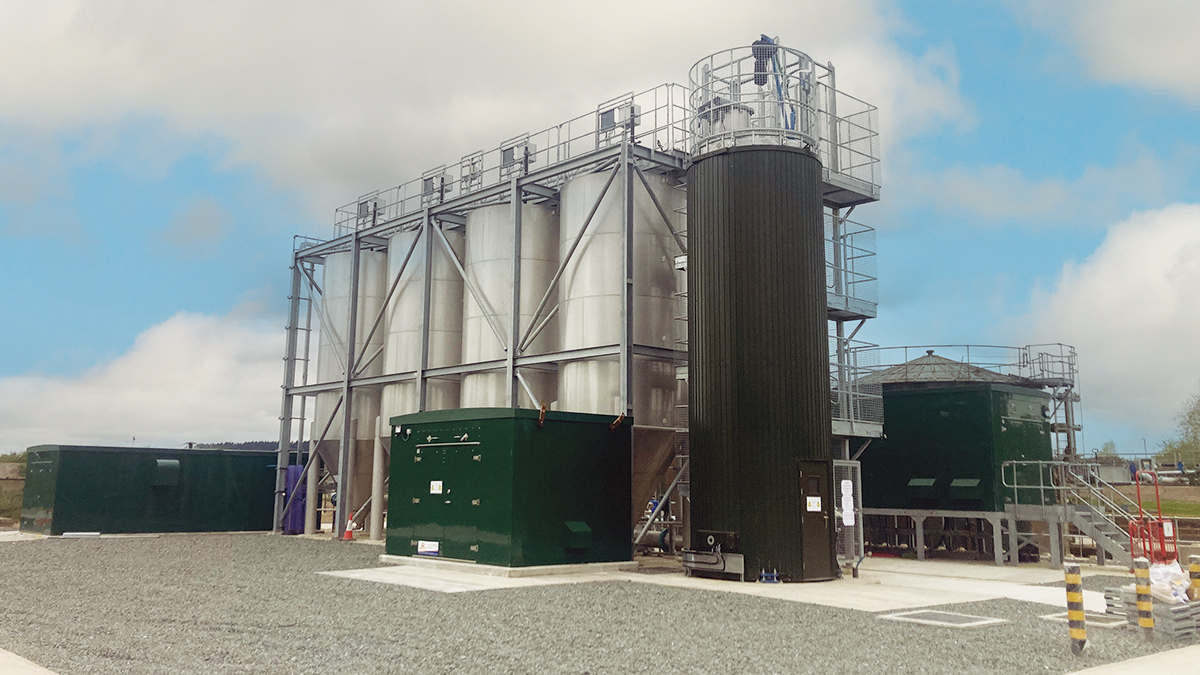
Fully constructed tertiary treatment system integrated into existing treatment works – Courtesy of Morgan Sindall Infrastructure
Sustainable and efficient design and construction
The new tertiary treatment plant and associated pipework, utilities and control kiosks were installed in an area within the boundary of the existing treatment site, where disused sludge drying beds were previously located. Re-purposing this area led to a more sustainable solution as it avoided the associated expenditure, programme, and environmental requirements that land purchase would have involved.
Due to this area of the existing treatment site being near the final effluent pipework, it enabled the flow diversion to the new tertiary lift pumping station to be achieved via a short length of below ground gravity pipe at a shallow depth. This is also a more sustainable design as it avoided the increased excavation and carbon footprint requirements that additional manholes, longer/deeper pipe lengths and a pumped solution would have required.
Other examples included surveying existing duct runs and draw pits to review capacity and reuse, where possible, as well as refurbishing the existing ferric dosing system and containment bund, instead of installing new plant, thus providing efficiencies and cost savings to Welsh Water.
Another element of efficient design and construction was the civil bases associated with the three new MCC kiosks for the new plant and equipment being installed.
As the two larger kiosks were to be DfMA and hence delivered to site with the panels already installed within the kiosk, a support frame for the kiosk and floor was also provided. Due to the panels requiring man access below them for installation of cables, the support frame included for vertical legs and steps for access into the kiosk that was installed on a simple concrete flat slab with mesh reinforcement. This was a more sustainable solution as it minimised the excavation requirements and reduced the total volume of concrete and steel when compared with sitting the kiosk at ground level on a below ground concrete trench and base slab with more steel reinforcement. The solution led to a quicker installation and better from a Health & Safety perspective as the extent of confined space working was reduced due to the absence of a trench.
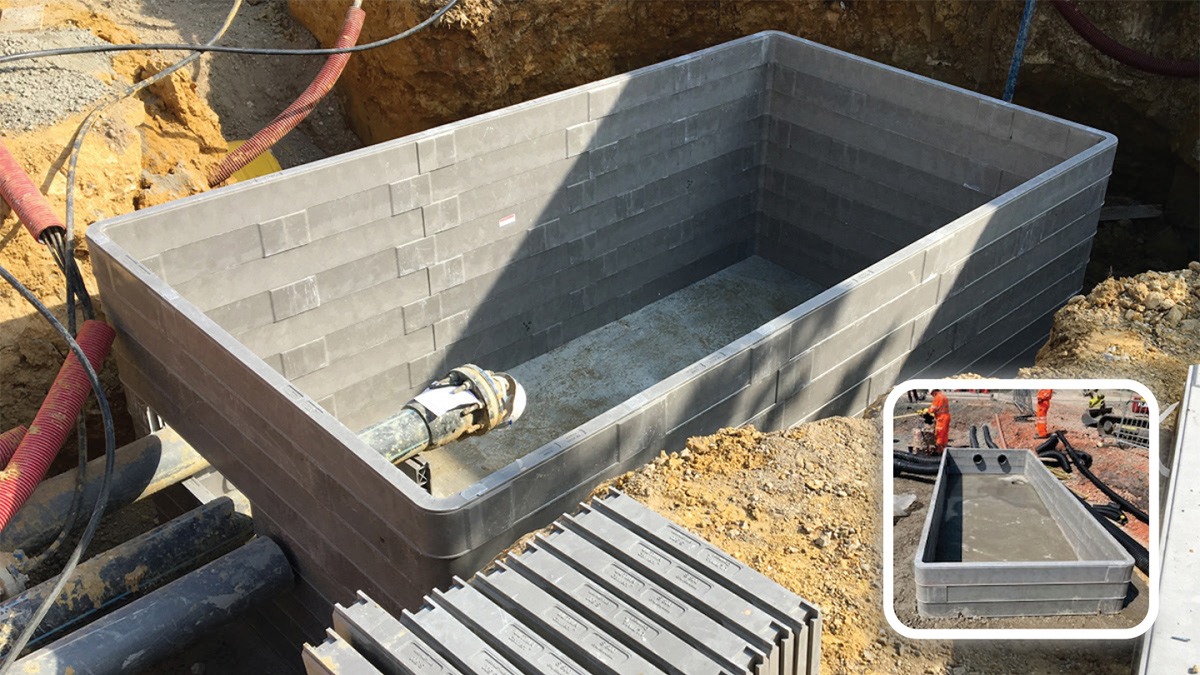
Example of a Cubis Systems modular chamber and (inset) chamber being assembled at Leominster- Courtesy of Cubis Systems & Morgan Sindall
For the smaller alkalinity MCC kiosk (not DfMA), it was decided that the kiosk would sit at ground level but as it still required access under the panel for installation, a below ground trench was required. To make the construction process more efficient, the trench comprised of innovative and sustainable HDPE recycled plastic modular units from Cubis Systems, that were put together on site and built around with minimal concrete surround and base slab and backfill to support the kiosk. As well as the material of the modular solution being more sustainable, it also led to a reduced carbon footprint in delivery due to it being very light weight. This also made it a safer and quicker installation as the manual handling involved was minimal.
Cubis Systems products were also used for the draw pit construction where the rapid stack modular units were utilised to form the main structure saving man hours with additional safety benefits.
The existing layout of the inlet works presented increased risks to operations with the main components below ground level and within a confined space. The new design involved raising the working platform to ground level, around the new screens and creating a better working environment and removing the need for operations to enter the previous confined space areas.
Design efficiencies
Working together with Welsh Water and the framework MCC subcontractor (GPS Group), the team were instrumental in the development of the standardised design for manufacture and assembly (DfMA) design for MCC kiosks within the Welsh Water business. The Leominster team delivered this standard product in the form of a new low voltage distribution board kiosk and a new tertiary filter MCC kiosk at the site.
The DfMA GRP kiosks are mounted on a raised steel frame floor to support the MCC and the access covers while giving ample space beneath the structure for cable connections and testing.
This kiosk design reduced health and safety risks associated with installation and commissioning and led to considerable reduction in installation time on site, as the kiosks were delivered to site, off loaded, and fixed down, all within a few hours.
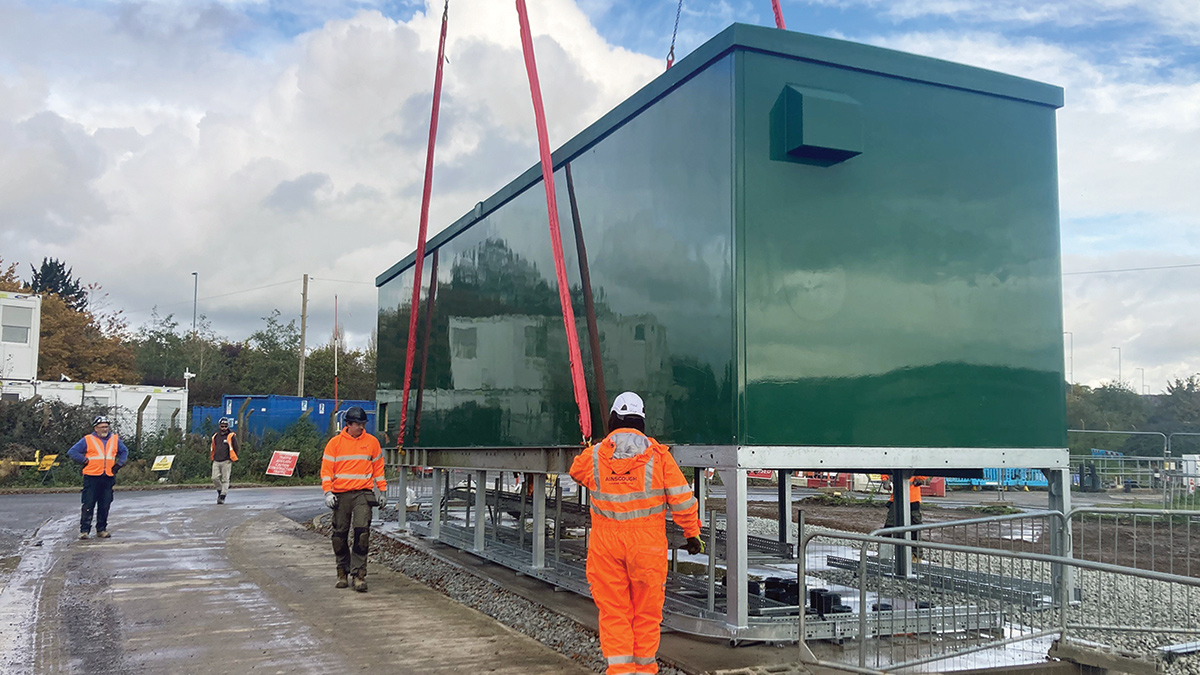
Installation of DfMA low voltage distribution board MCC kiosk – Courtesy of Morgan Sindall Infrastructure
The early engagement, with the electrical installation subcontractor, PCS Ltd, through an agreed Early Contractor Involvement contract arrangement, ensured that cable design and routes were agreed early in the design, to the new plant and equipment.
The standard designs for lighting, junction boxes and emergency stops were used where possible. In addition, the Welsh Water Capital Delivery Alliance team worked collaboratively with PCS Ltd and BEST Services Ltd, an earthing specialist subcontractor, to fully understand the earthing requirements for the site. Regular design review meetings were held to develop a workable earthing design, considering the impact of this deliverable with numerous site constraints.
Conversion of the existing Siemens PLCs to remote I/O, allowed for integration of all existing signals into the new schemes Mitsubishi PLC network. This minimised the number of telemetry outstations on the site, bringing all control associated with these MCCs into the new PLC network.
Hydraulic integration of new process scope into existing works
The new project scope required integrated into the existing treatment works hydraulic design and included the incorporation of two new SPIRAC Ltd escalator screens and storm bypass static screen within the existing civil structure, and the installation of new flow control weirs into the existing biofilter and humus tank distribution chambers.

New Fineguard inlet screens from SPIRAC Ltd with improved safe access for operators – Courtesy of Morgan Sindall Infrastructure
The new weir design was needed to achieve an appropriate flow distribution across the two sets of existing biofilters and the three existing humus tanks. To ensure seamless integration and maintain safe flow throughout the facility during the implementation of these changes, a comprehensive hydraulic assessment was conducted to verify the incorporation of new process assets within the treatment stream without negatively impacting on the existing asset structures.
To maximise the reuse of the existing works pipeline infrastructure and flow hydraulics, the team positioned the new tertiary treatment filters within the site layout to optimise the existing final effluent pipework arrangement by rerouting the flows from the existing humus tanks to the new tertiary treatment lift pumping station and then reintegrated the treated effluent from the tertiary filters back, by gravity, into the existing pipework to the final effluent lift pump station.
This approach reduced costs and construction time for the delivery of the project, reduced the impact of maintaining the existing works operation during the construction period and removed the need to agree a new final effluent sampling point location with the Environment Agency.
Digital delivery
To maximise the understanding and detail of the existing site arrangement and optimise the design process, a point cloud survey was undertaken, and a 3D Revit model produced. Along with existing as built drawings, asset and topographical survey information and historical as built drawings, the 3D model was developed further and then used to produce and develop a 3D model of the design proposals.
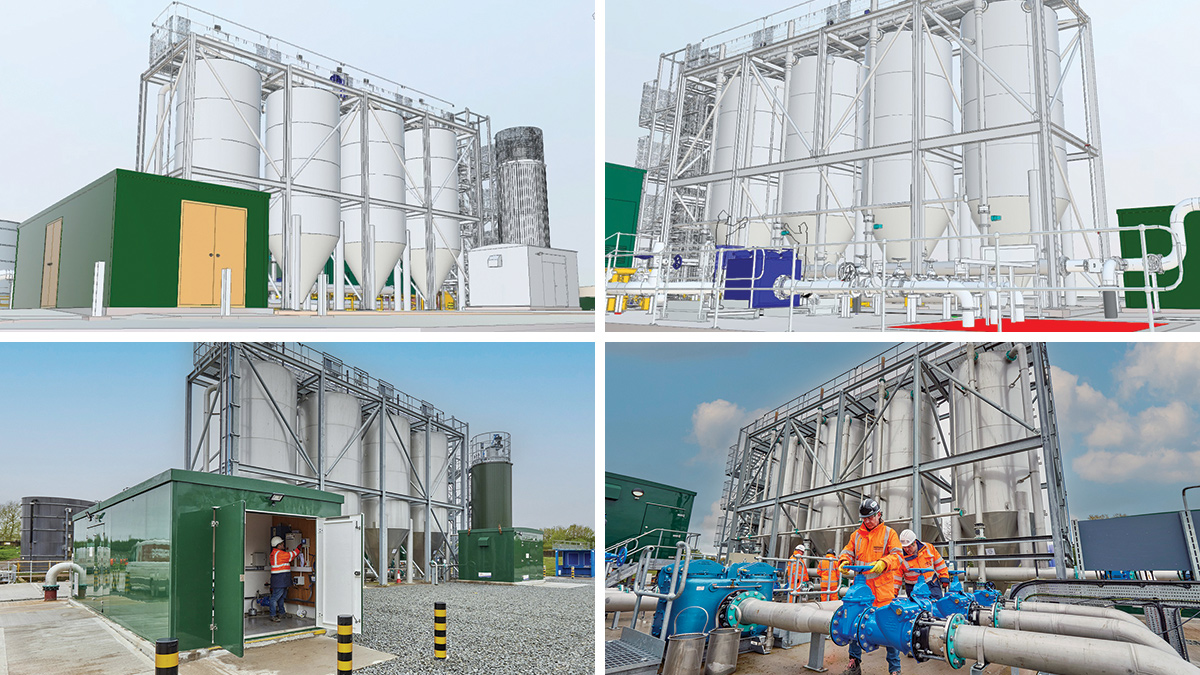
(top left) Federated 3D model capture of sampling kiosk with tertiary filters – Courtesy of Arcadis, (bottom left) as built sampling kiosk with tertiary filters – Courtesy of Morgan Sindall Infrastructure, (top right) Federated 3D model capture of lift pumping station with tertiary filters – Courtesy of Arcadis, and (bottom right) As built tertiary filter lift pumping station pipework with duplex filter and tertiary filters – Courtesy of Morgan Sindall Infrastructure
The 3D model was federated to include all the different design models (including those by the design subcontractors) and then used in internal meetings to agree on design proposals, by being marked up for updating. The federated model was also used to avoid underground clashes with existing pipework and produced the 2D drawings that informed the pricing and construction of the proposals and was also instrumental in getting acceptance from the stakeholders when used in project gateway approvals, HAZOP and ALM meetings.
This digital strategy for the project led to significant efficiencies in design as the federated model that contained the developed design proposals was uploaded to a BIM Docs page for the project, where all design deliverables were also kept, reviewed, and issued to the key stakeholders via the workflows and transmittals tools. The whole project team (designers, subcontractors, suppliers, stakeholders) were able to easily access and view the pertinent design information and subsequently design reviews and project decisions could be made easily which was instrumental in fostering a collaborative approach on this project.
Engineering challenges
Groundwater: As part of the overall design, a 3m diameter and 6m deep tertiary lift pumping station, was designed to lift and transfer influent flows, intercepted and diverted from an existing 450mm diameter final effluent gravity pipe, to the four new tertiary sand nitrifying filters.
During ground investigative works, it was identified that there was a high-water table present that would make construction of the shaft difficult. To fully understand the impact, pump tests were carried out to quantitate the expected groundwater influx during excavation and allow Arcadis to prepare and submit applications for abstraction and discharge (A&D) licences from the EA.
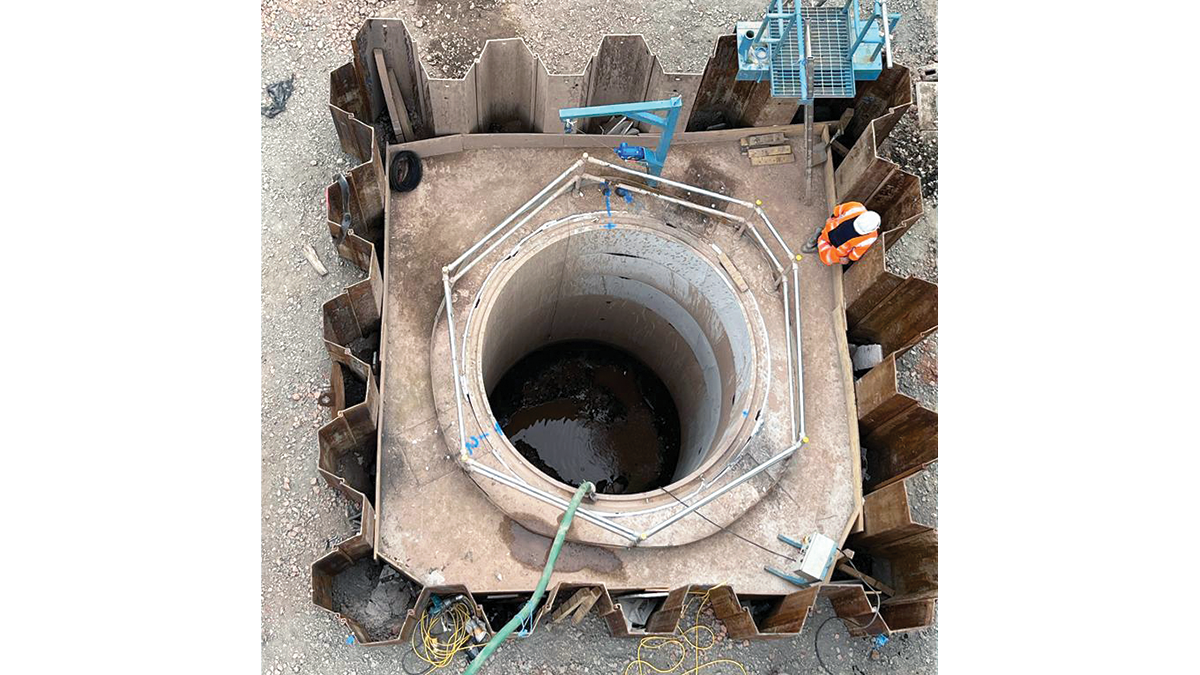
Lift pumping station – Courtesy of Morgan Sindall Infrastructure
However, due to the lengthy time-frame expected to obtain EA approval for an A&D licences, the team needed to reconsider the construction methodology of the lift pumping station in order to meet the consented target date of 31 March 2024.
B&W Tunnelling Ltd, who had been appointed to undertake the original caisson installation, jointly developed a solution with Morgan Sindall that would enable the pumping station to be constructed without the need to abstract any significant amount of groundwater. The agreed method was to drive interlocked sheet piles around the perimeter of the planned structure to a depth at which it will cut off any groundwater. With the groundwater under control, the caisson could then be installed under ‘dry’ conditions.
A 4.8m x 4.8m cofferdam was installed using 12m long GU27N sheet piles to penetrate the underlying mudstone formation. During construction the piles were required to stand as cantilevers. The temporary sheet piles were used for the construction period only, and were extracted once the caisson was complete. The Berryrange Ltd cofferdam allowed for safe construction of the shaft/lift pumping station and ensured the project kept on programme.
Network Rail: The location of the new tertiary plant on the site was in close proximity to the busy railway line that runs from South Wales to North Wales and Manchester. Network Rail were consulted, and mitigation measures agreed to ensure the safest method of constructing the new asset was followed.
A basic asset protection agreement (BAPA) was approved, which enabled Network Rail to review the safety documentation of lift plans (tandem lift method), method statements and temporary works design ahead of the planned work to install the filter tanks, sodium bicarbonate storage silo and associated high level stairs and working platform structures.
An appointed Network Rail Supervisor attended site to oversee the construction operations, which included the safe operation of piling rigs, multiple cranes, concrete pumps and the safe use of excavators in the vicinity of the operational railway line. This process was undertaken for over 20 separate operations through the programme period, all of which were undertaken safely and successfully.
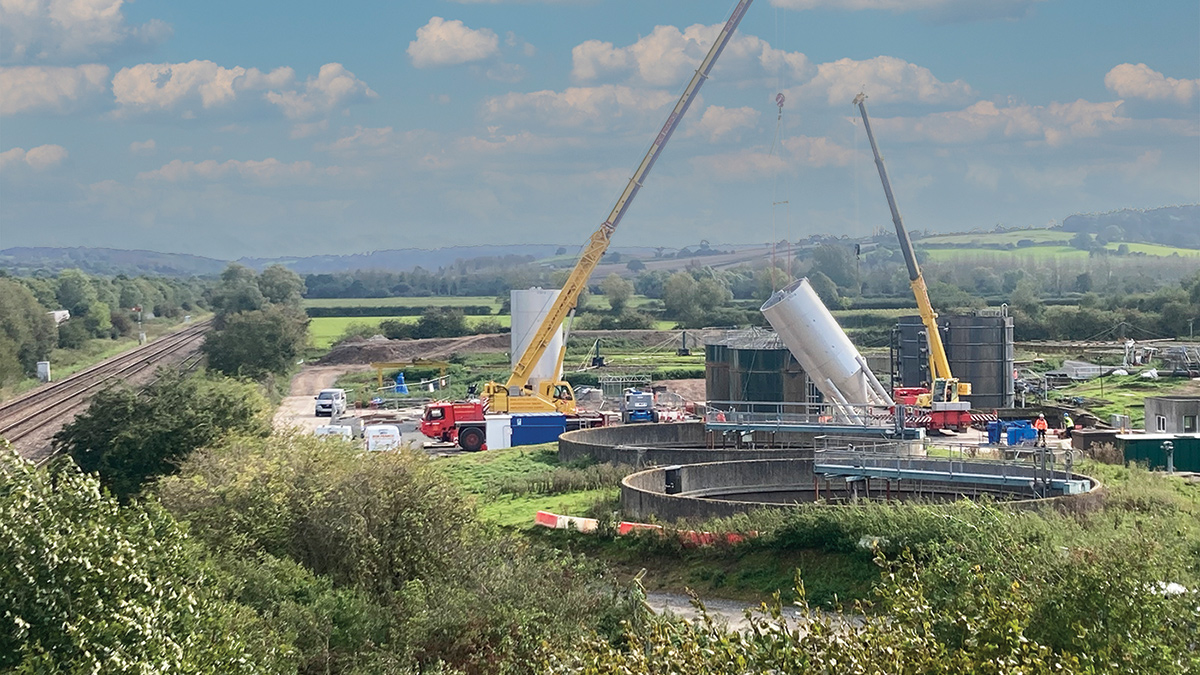
Installation of tertiary sand filters adjacent to railway line under agreed BAPA procedures – Courtesy of Morgan Sindall Infrastructure
Health & Safety
As always, during wastewater upgrades or extensions, the challenge and onus on the team is to integrate the new plant and processes, safely and efficiently, into the existing treatment works infrastructure, while ensuring that the existing process is not impacted or interrupted.
To formalise these crucial planning activities, Welsh Water required Morgan Sindall to work to their Business Continuity Plan (BCP) process. This BCP process encompasses the development and joint agreement of a detailed activity plan, initially, between Morgan Sindall and Welsh Water local operations teams, followed by presentation of the safe systems of work to Welsh Water senior managers for their final acceptance and approval.
As the integration of the new assets were built in and around the existing works, construction activities were proactively reviewed and agreed with Welsh Water to ensure minimal disruption to the operational site during the periods when these improvement works were being conducted.
Instances where the BCP process was followed included:
- When temporary over pumping was needed to construct two intercepting manholes on the existing final effluent gravity pipeline.
- During over pumping of incoming sewage from the inlet works structure and during the installation of the new screening units.
- During construction of two flow meters on the feed pipes to the two sets of existing biological filters
- During the power upgrade to site and transfer of mains control to the new LVDB MCC unit from the old.
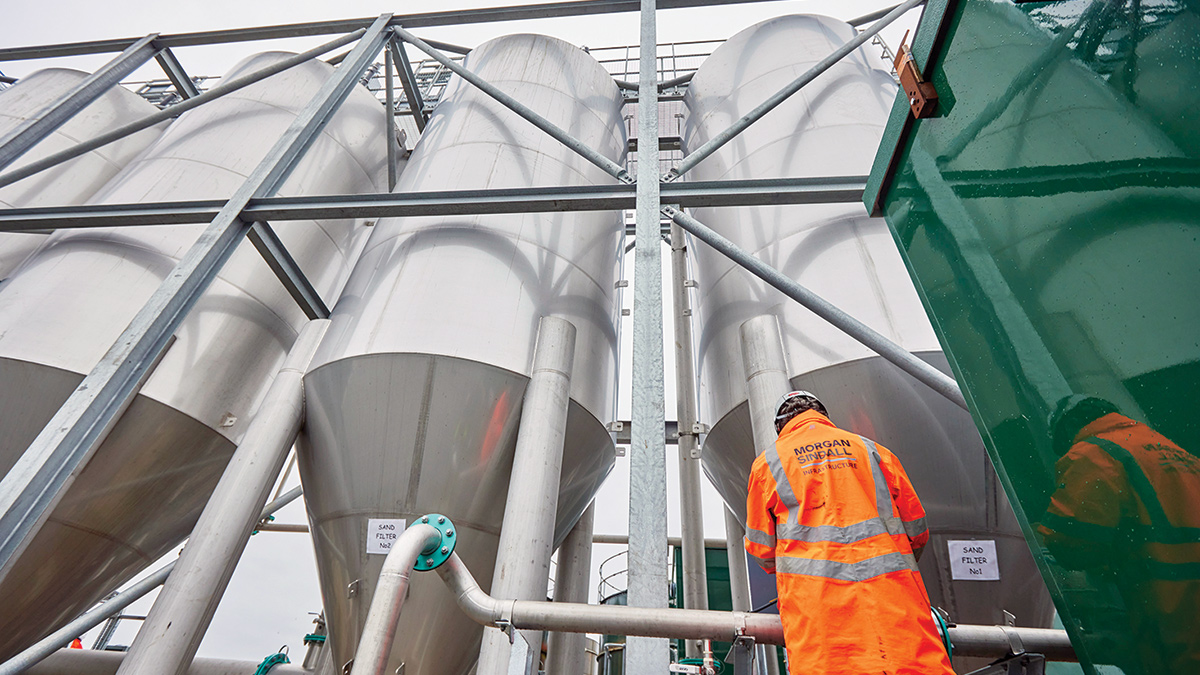
Leominster WwTW: Tertiary sand filters – Courtesy of Morgan Sindall Infrastructure
In the case of the installation of the biological filter feed flow meters, a gravity solution was selected due to the hydraulic sensitivity of the biofilters and fluctuating flowrates of the incoming wastewater with the weather. The construction required several shutdowns and temporary storage of incoming flows as well as the installation of a network of above ground pipelines with flow control valves and flow meters over a 200m distance across the operational site.
Enhancing communities
During summer 2023, the Leominster team approached the local country park to enquire if there was any community-based volunteering work that the team could assist with. The Park Ranger highlighted an area of which they were planning on creating a community garden.
The Morgan Sindall and Welsh Water team assisted the local country park rangers with clearing a large area of brash and vegetation at Queenswood Park to open the space up. In addition, the team assisted in providing a new stone footpath and bridge to enhance access for the public. Several bird boxes were installed to encourage and enhance local bird populations in the area.
Another example where the team have helped and supported the local community was through the provision of food parcels to the local Food Bank. Staff from Welsh Water, Morgan Sindall and the project supply chain, all donated food parcels to the local charity to distribute.
To encourage and assist with the development of future engineers, the team invited two Year 11 students to undertake work experience on the site for a week and hosted a new graduate on the site as part of the Year in Industry placement scheme.
To celebrate British Science week, the Herefordshire Women’s Institute attended site during construction. The Leominster Town Clerk and numerous local councillors were also invited to site to explain the environmental benefits of the new enhancement works to the existing treatment works.
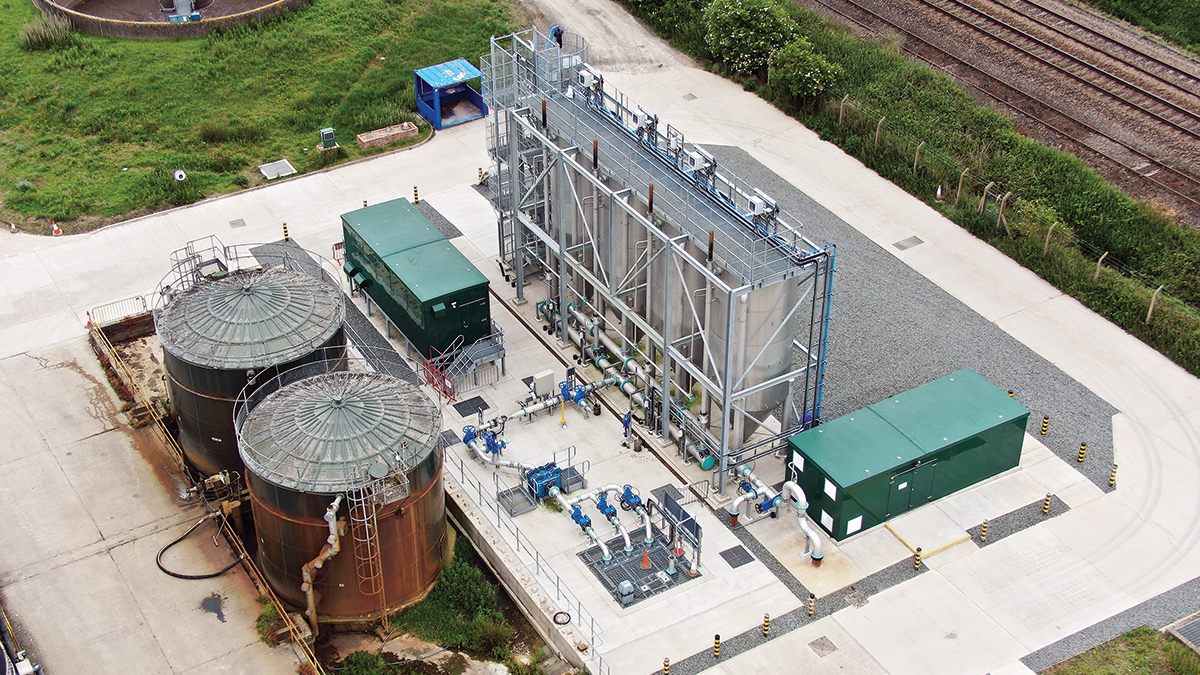
Fully constructed tertiary treatment system integrated into existing treatment works – Courtesy of Morgan Sindall Infrastructure
Programme
Scheduled collaborative planning was undertaken at the design stage with all project stakeholders ensuring key deliverables were targeted and met to enable start on site. The collaborative planning sessions were also carried through to the construction phase where the main project programme was developed with all disciplines and key supply chain partners to achieve the milestones set.
Coupled with the regular planning sessions weekly site progress meetings were undertaken with all parties ensuring everyone was aware of the planned and forthcoming works with progress monitored throughout.
The main construction programme consisted of separate civil working areas ensuring the foundations and main structures were in place before mechanical and electrical supply chain partners were integrated into the programme to work alongside each safely to optimise the working time of the programme.
All parties worked together on site successfully with a standard daily safety brief to everyone ensuring all individuals were aware of the planned activities.
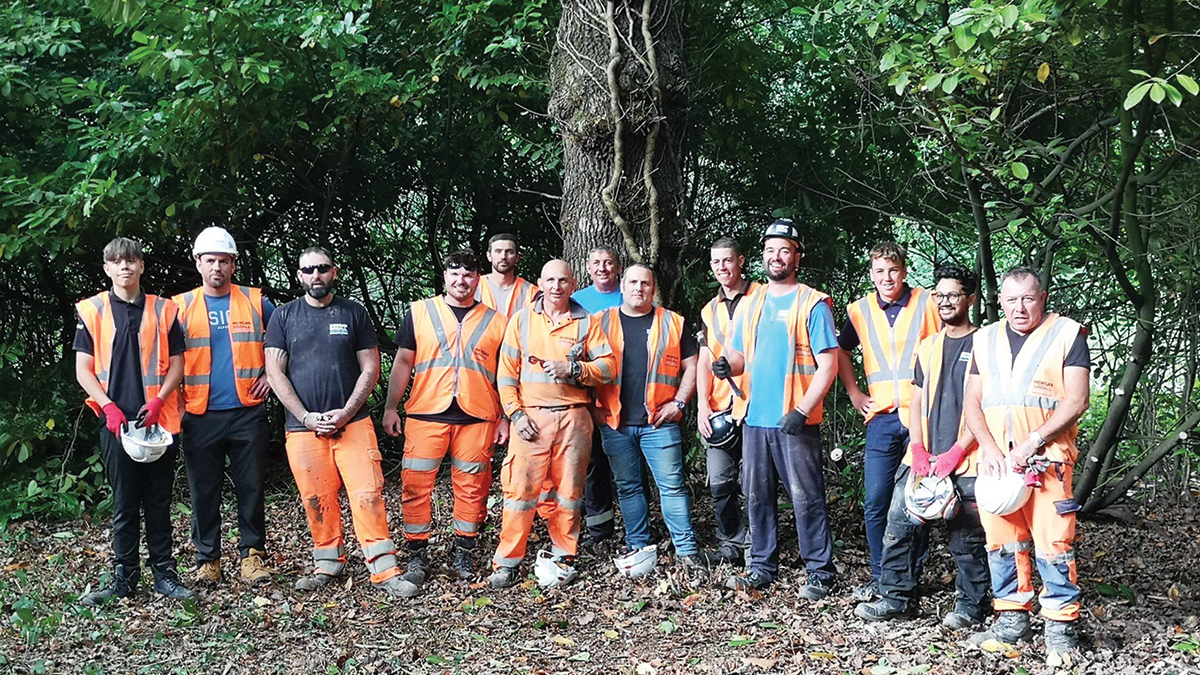
Morgan Sindall and Welsh Water team volunteers bringing improvements at Queenswood Park - Courtesy of Morgan Sindall Infrastructure