SEEPEX UK Ltd
Smart Air Injection
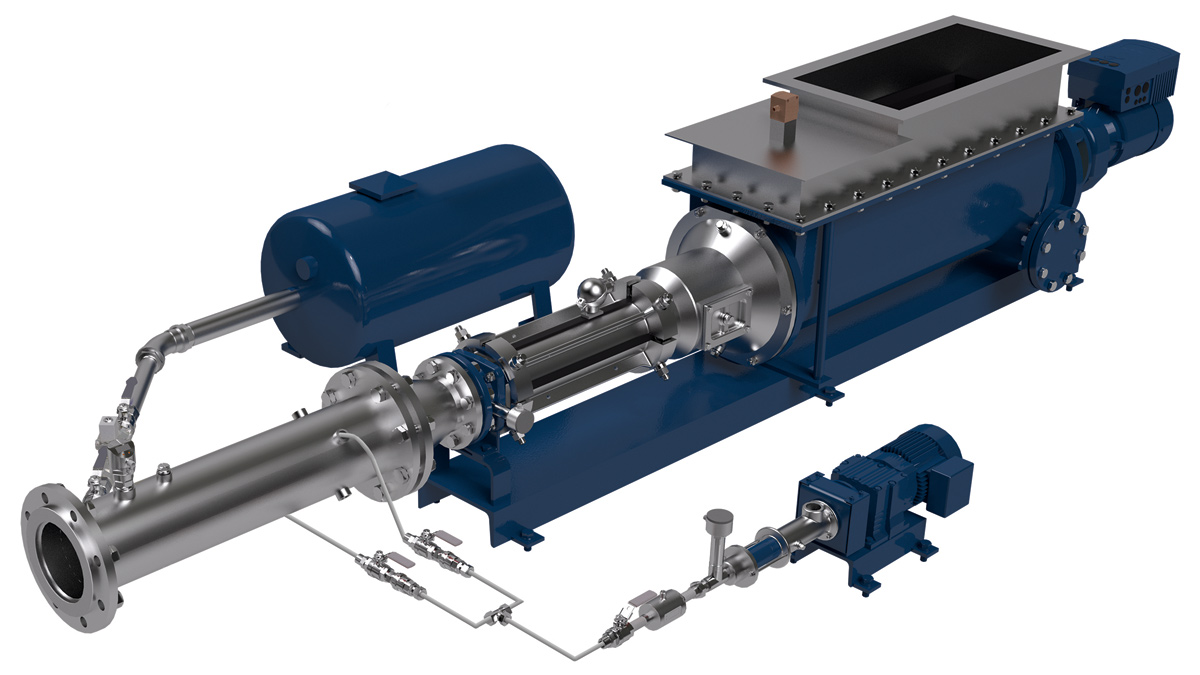
Smart Air Injection (SAI) pump from SEEPEX. Long distance pump system for highly viscous products
The Water 2020 report, published by the regulator Ofwat, encourages sludge trading markets between Water Authorities so that sludge can always be treated in the most cost effective way. Ofwat modelling suggests that if its proposed changes are implemented, around 30% of all sludge could move between different water companies. Sludge needs to be processed, whether in thermal processing, recycling or agriculture and this will make it increasingly necessary to transport dewatered sludge over long distances. With the patent-pending Smart Air Injection (SAI), SEEPEX is launching a customized solution, which combines the advantages of two conveying technologies to transport dewatered sludge, with high dry solids content, over long distances in an energy-efficient manner. SAI uses a combination of SEEPEX’s progressive cavity pump technology with dense phase pneumatic conveying. Dewatered sludge (or other highly viscous media) is introduced into the pipeline using a progressive cavity pump, forming compacted material which is split into ‘plugs’ and pushed down pipelines up to 1000m using compressed air.
The future of sludge transfer
This alternative to conventional means of handling dewatered sludge has already been installed at a number of plants throughout Europe and has generated a rapid return on investment. There are a number of considerations that could make the use of the new SEEPEX system solution an attractive alternative for some of the country’s sludge treatment centres, as not only can Smart Air Injection (SAI) transfer dewatered sludge over distances of up to a kilometer, but is also remarkably economical, because the total investment costs, and running costs are comparatively low.
SEEPEX already has its first reference clients on the international market, with SAI being integrated into one of the UK’s largest water companies in 2018. The new system is now available to customers as an energy-efficient, high-performance alternative to conventional sludge handling systems. The customized pumping solution is engineered to fulfill the requirements of the plant and to be configured at the location for optimum energy consumption.
Sludge under pressure
The new SEEPEX product is a pioneering solution with numerous advantages compared to the established methods currently used.
Until now, long distance transfer of dewatered sludge has been carried out by belt and screw conveyors and bucket elevators, which require a lot of maintenance, often made costly by the need for working at heights if silos are filled. In addition, the systems are frequently open to the environment, which can result in unpleasant odors and rehydration by rainwater, and complications on vertical or inclined transportation.
Alternatively, closed piping can be used in conjunction with multi-stage progressive cavity pumps and piston pumps, which are suitable for highly viscous media and high pressures. Because of the high counter-pressure, however, these require comparatively high investment costs for higher pressure rated pipework and valves (in some cases more than 100 bar). Piston pumps in particular also have significant maintenance requirements and costs, long downtime during maintenance, may suffer from hydraulic oil leaks and have relatively high drive power and energy consumption. This was proven by SEEPEX at Thames Water where piston pumps were replaced by PC pumps, reducing the discharge pressures and reducing energy consumption by over 50%.
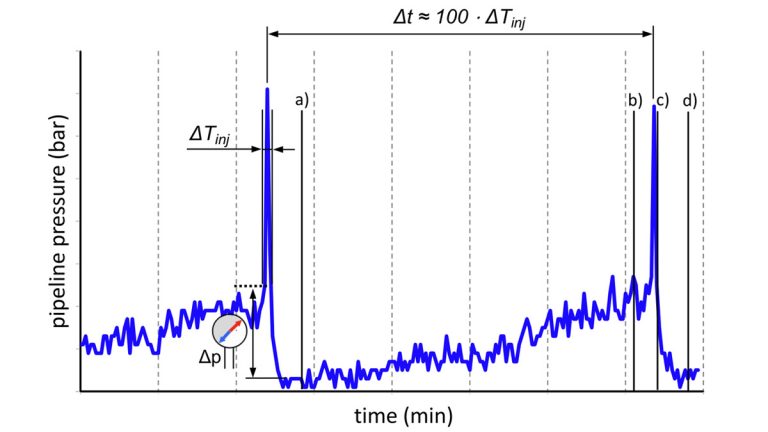
Schematic pressure curve at the injection point of the sludge pipeline. When a pre-defined pressure level is reached, compressed air is injected for a few seconds, after which the pressure in the sludge pipeline drops. The PC pump is then used over a period of several minutes to pump a new sludge plug into place, whereupon another compressed air injection takes place.
Pioneering solution helps lower costs
SAI uses a combination of progressive cavity pump technology and dense phase pneumatic conveying. This overcomes the challenges posed by the dewatered sludge as well as by the ever-increasing transport distances; dewatered sludge stands out due to its high viscosity creating high friction losses in the discharge pipework. The aim was to find an alternative to the current conveying practice, in order to overcome the challenge of long distance transport, using a cost-effective and energy efficient solution.
In the SAI system, a solid ‘plug’ of dewatered sludge is formed by an open hopper pump with auger feed screw, which is then transported onwards by means of pulsed compressed air injection which is pressure-controlled via an algorithm optimized for the application. The pneumatically transported sludge ‘plug’ is lubricated with boundary layer liquid, for example polymer solution. This reduces friction in the pipeline, and thus improves the energy efficiency of the system as a whole.
The combination of pump and dense phase pneumatic conveying permanently reduces the pressure in the entire pipeline to below 10 bar generated by the pump to set the sludge plug in motion. Once the static friction force has been overcome, the sludge plug is moved by compressed air, which again reduces the discharge pressure in the pipeline. Adjusting system parameters such as polymer and air volumes at the location makes it possible to set a plant-specific, energy-optimized operating point.
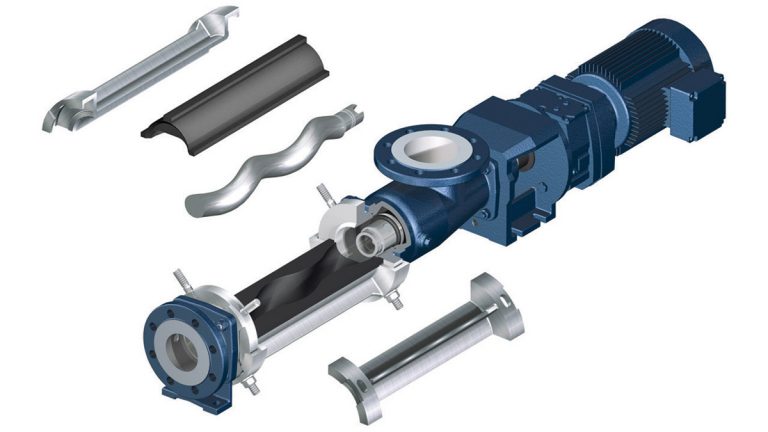
Smart Conveying Technology (SCT). Reduced maintenance costs for SEEPEX progressive cavity pumps
Smart systems
The reduction in friction losses and the discharge pressure requirements means that pumps fitted with Smart Conveying Technology (SCT) can be used for long distance, high viscosity transfer duties. Pump maintenance time is minimal (rotor stator replacement in less than an hour) as pipework removal is not required for maintenance. The lower discharge pressure additionally ensures an increased service life for the components which is further extended by SCT whereby the stator can be adjusted to maintain pumping performance as performance drops. Additionally in the automated SAI system process monitoring can be integrated into existing automation and control systems via conventional interfaces. All functional components, sensors and actuators, are part of the scope of supply, and are integrated into the control software SAI, which is optimized for the respective application.
Fir more information contact SEEPEX UK: +44 (0)1935 472376 | (w) www.seepex.com
SEEPEX UK Ltd is the UK subsidiary of SEEPEX, a global developer and manufacturer of progressive cavity pumps, macerators and control systems. Established in 1972, SEEPEX has more than 700 employees serving customers in over 70 countries worldwide, across a variety of industries including water and waste water, food and beverage, oil and pharmaceutical, chemical and many more. SEEPEX provides a comprehensive sales and support service for its products, ensuring that customers enjoy the best technical and commercial pumping solutions.
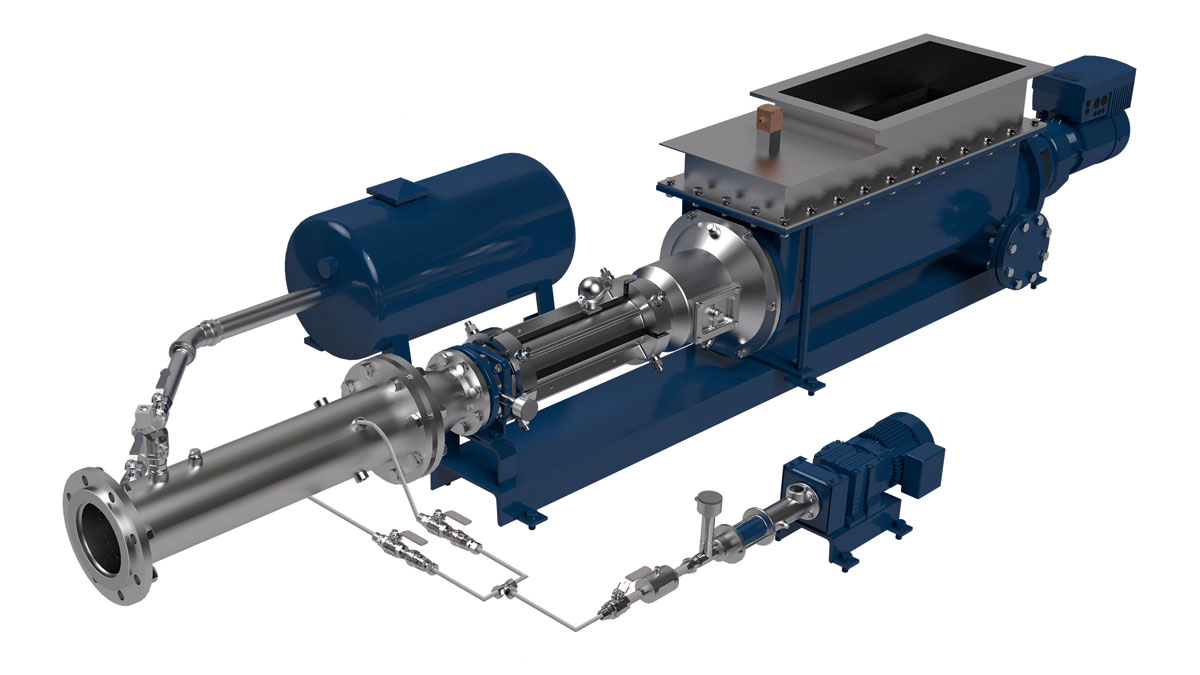
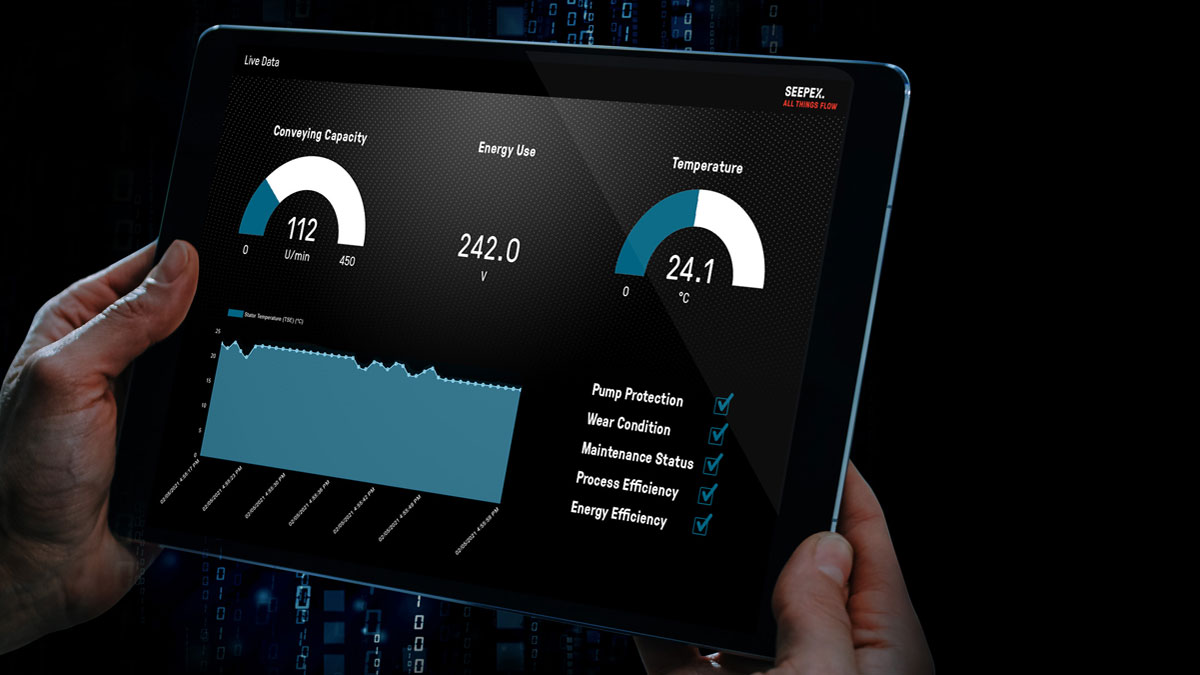
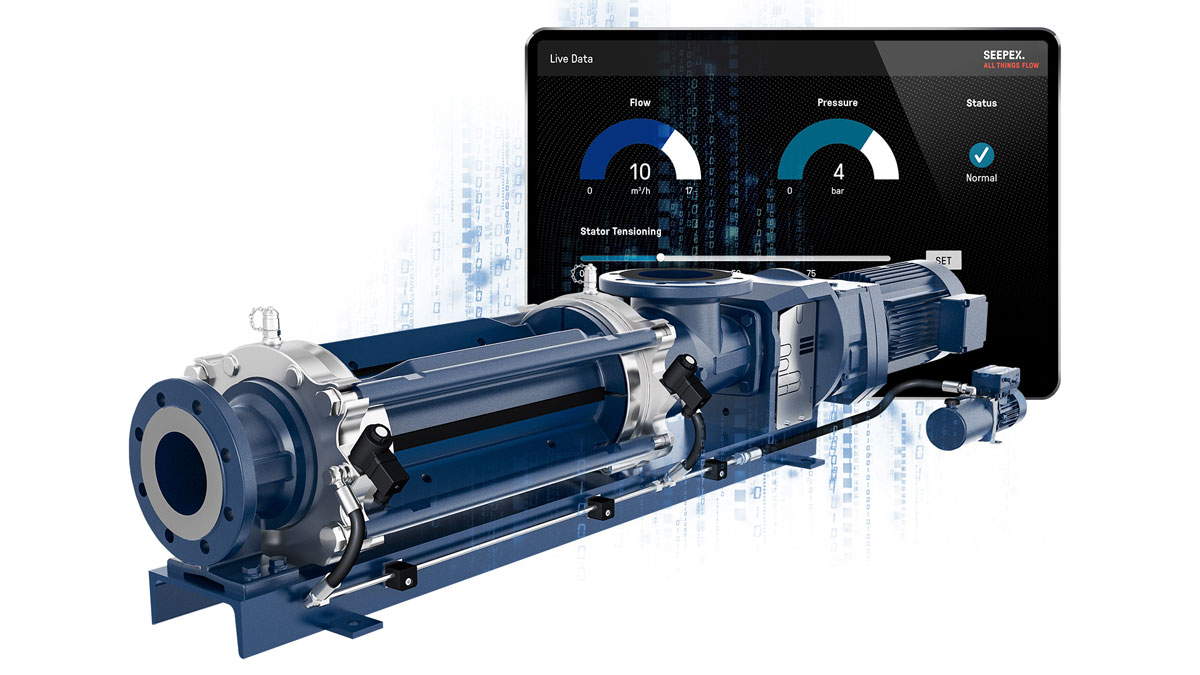
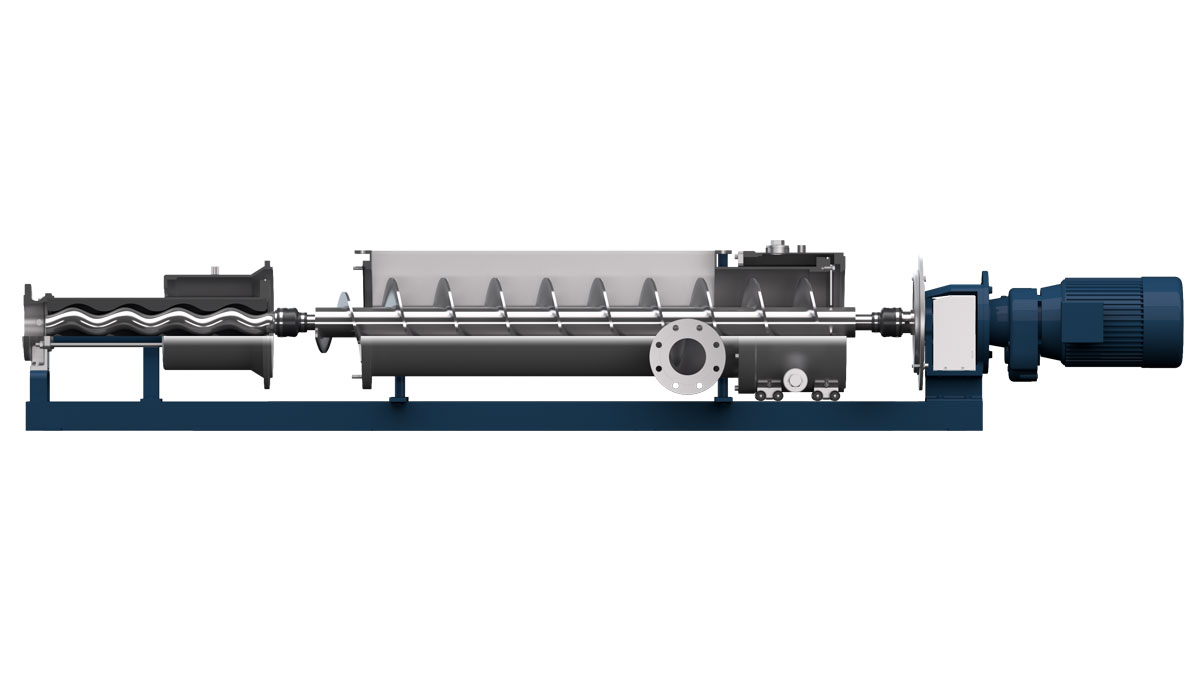
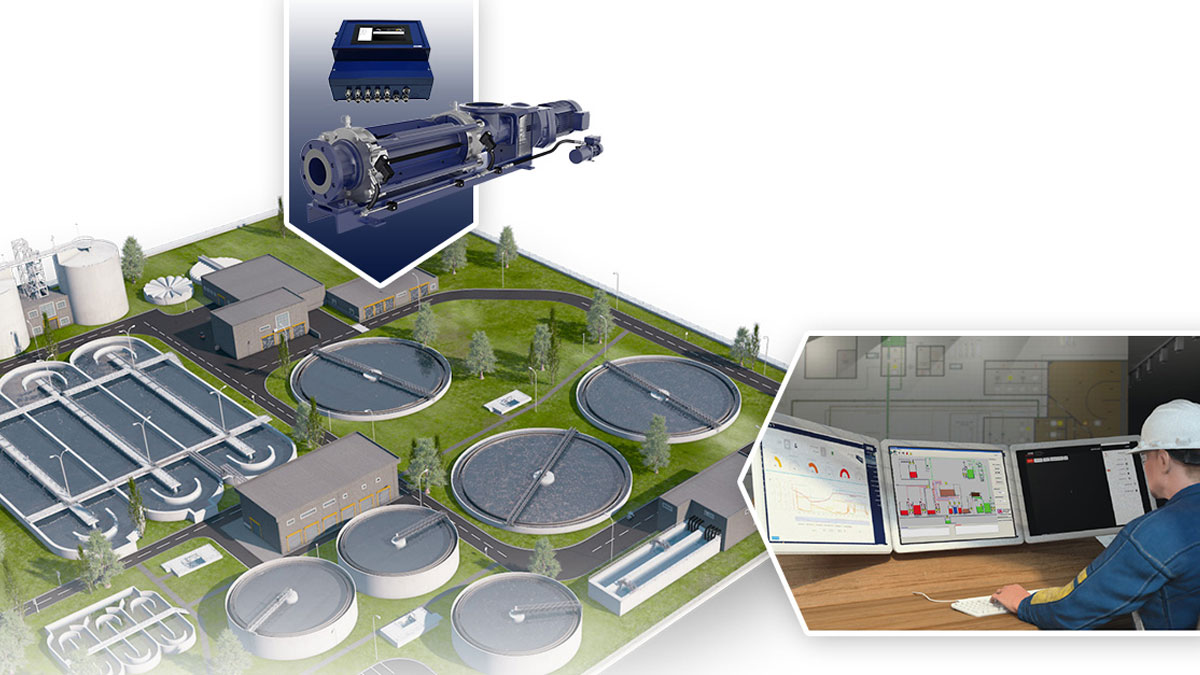
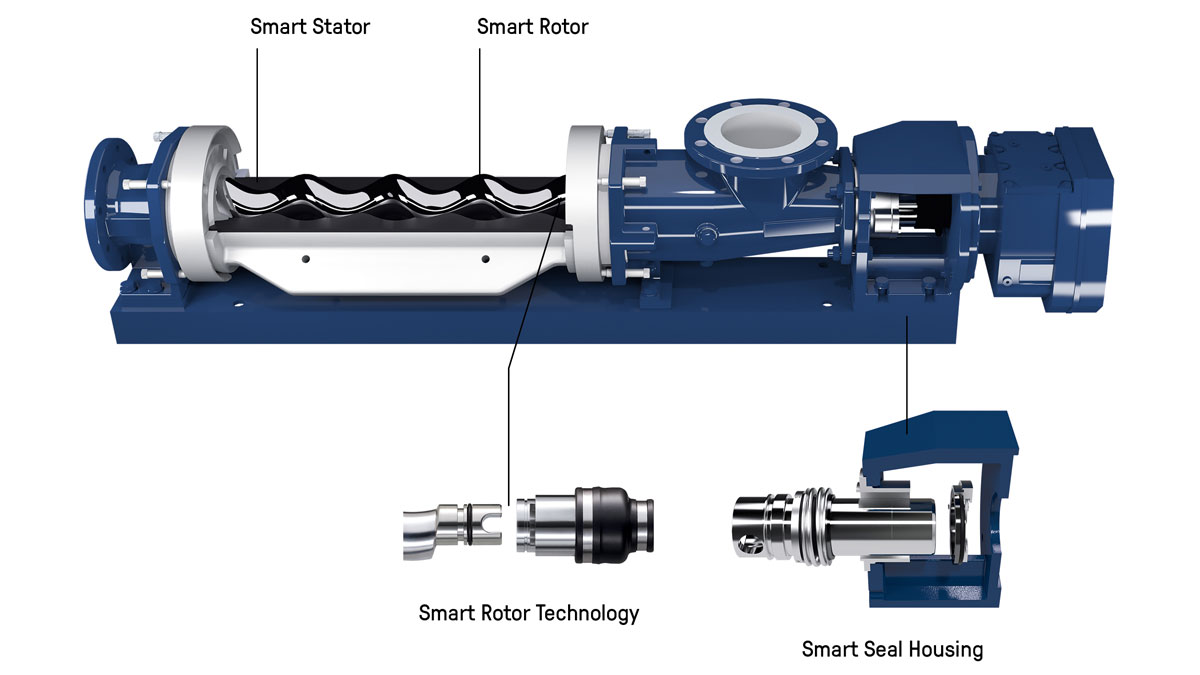