Saint Gobain PAM UK
We lead markets in the supply of:
- Ductile iron water and sewer pipes, fittings, valves & couplings & adaptors.
- Ductile iron access covers & gratings.
- Cast iron soil and drainage and rainwater systems.
Across each of these categories we can provide:
- Innovative products and processes.
- Specialist engineering services.
- Total technical support.
…offering you complete service integration.
The Saint Gobain Group employs around 9000 people and generates annual sales of £1.2 billion in over 120 countries and with the support from the international group, Saint Gobain PAM (UK) are able to offer unrivalled technical support, a total solution approach and unparalleled quality and innovation. A UK based business, with two foundries and a distribution centre in the Midlands, we combine international reach with local, specific solutions across all of our customers.
We continually invest time, energy and expertise to create an extensive range of innovative solutions, which are easy to install, simple to joint- and simply offer better value for money in terms of total life costs.
All parts of our operation have audited quality management systems and fully satisfy ISO 9001:2008. All products are third party assessed and approved against all relevant world-wide regulations and standards.
We are committed to sustainable and ethical development in all aspects of our business. Made from greater than 80% recycled material and 100% recyclable at the end of their long life, both ductile and cast iron provide a cost effective solution whilst protecting the environment.
With Saint Gobain PAM and the PAM brand, you can be assured of Quality, Innovation and Technical Expertise at all times.
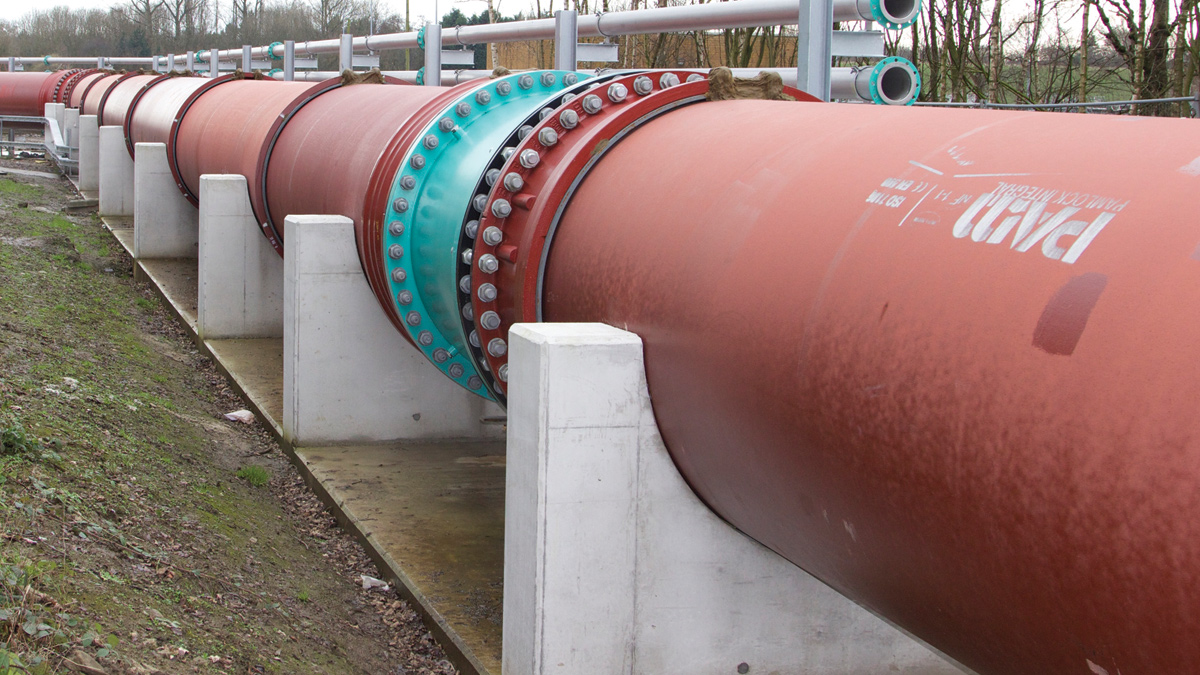
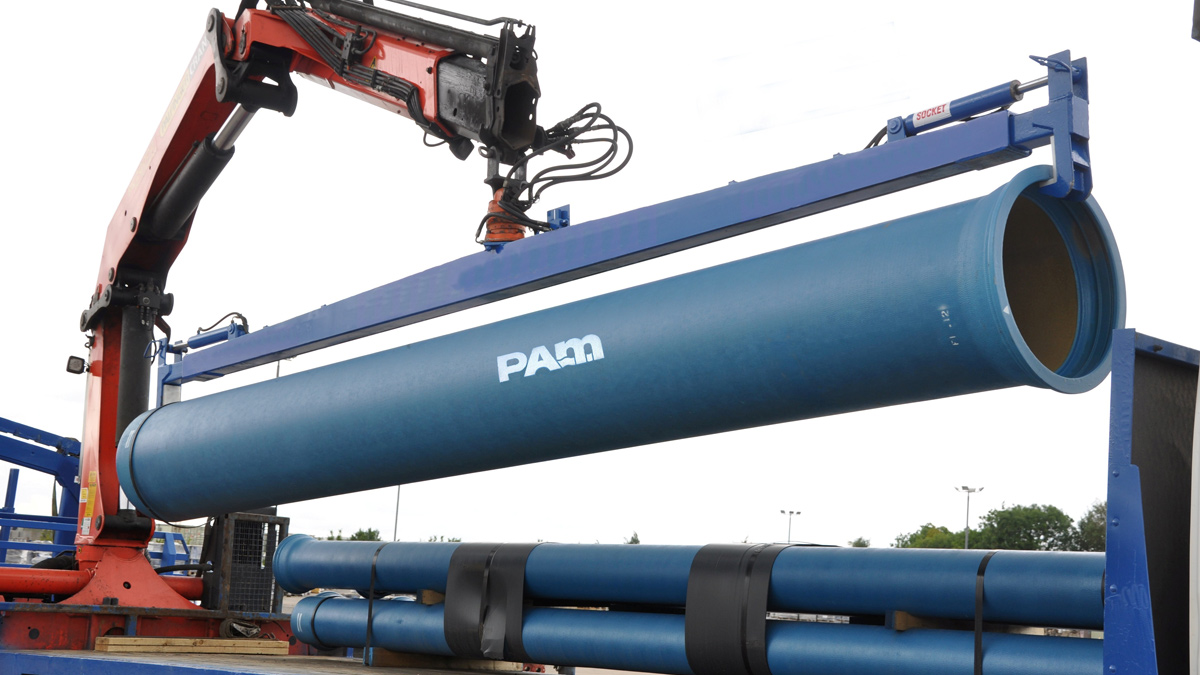
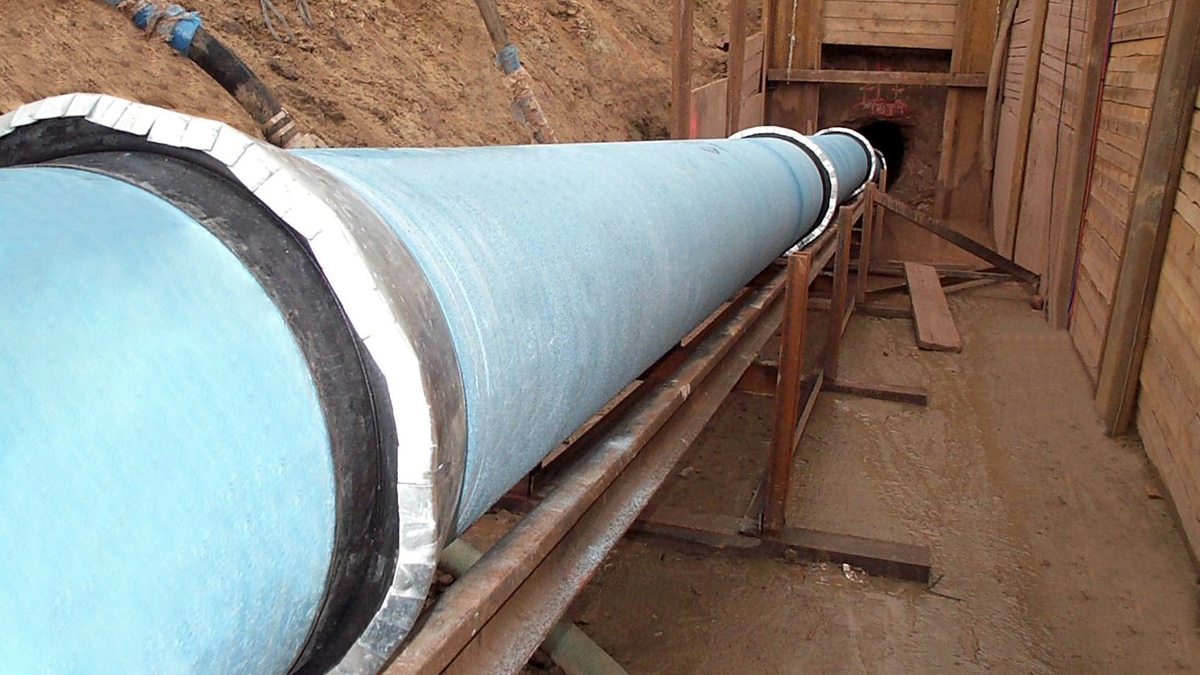
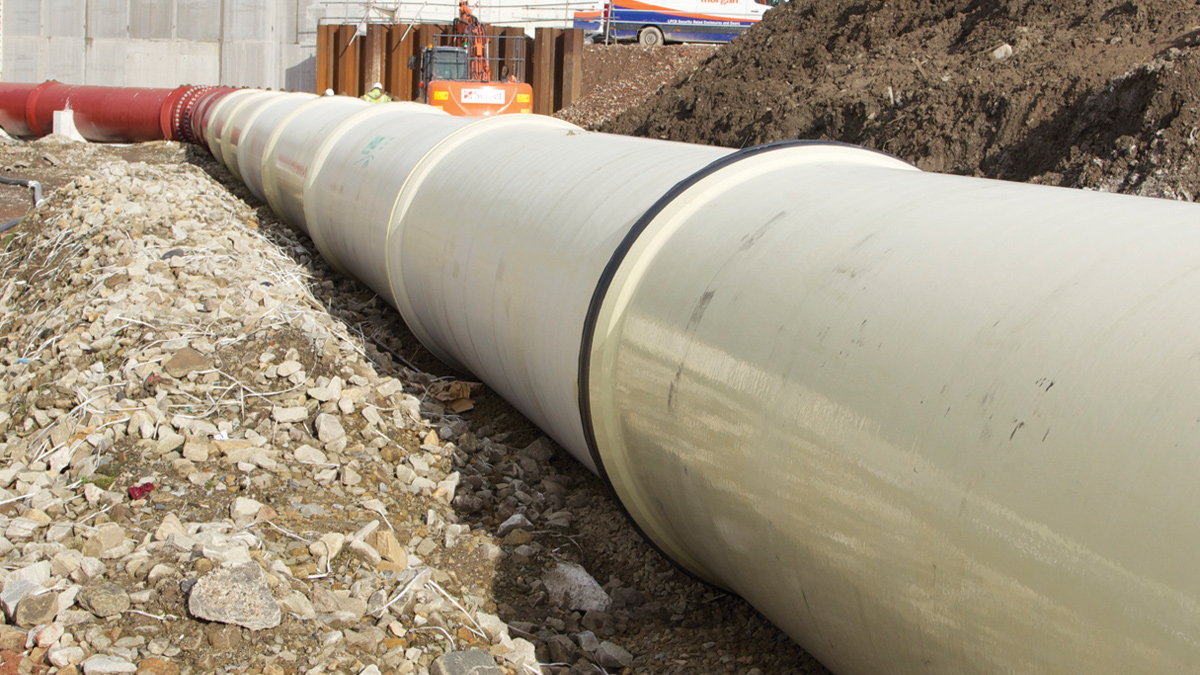
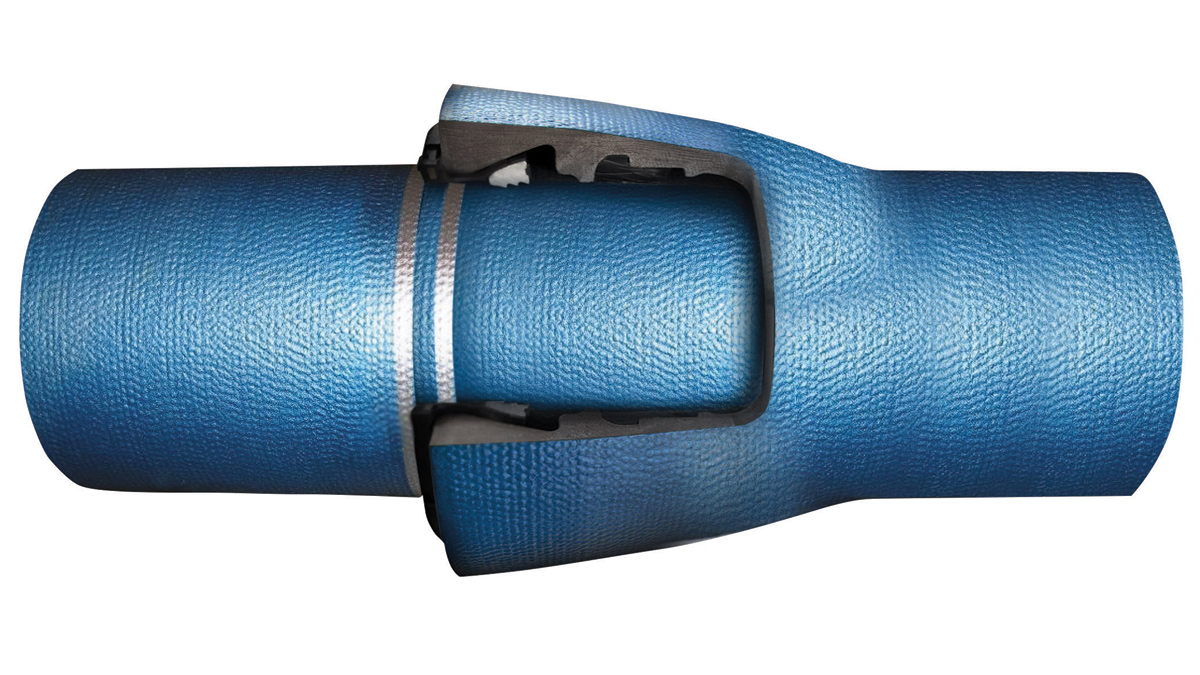
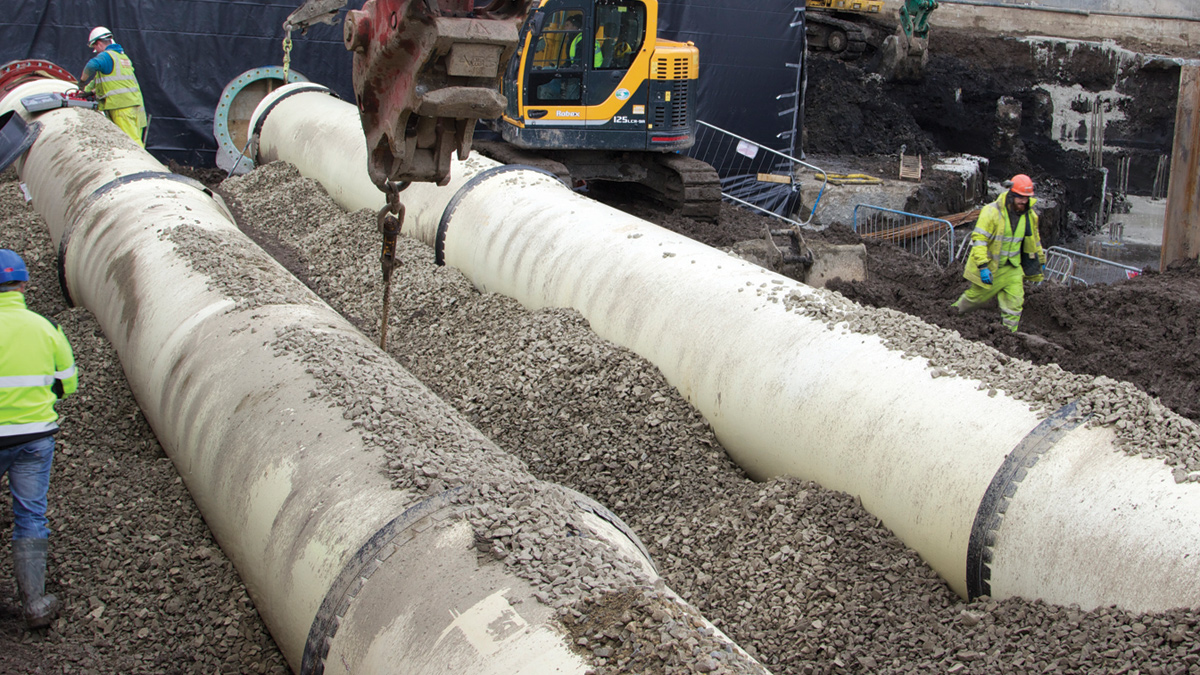
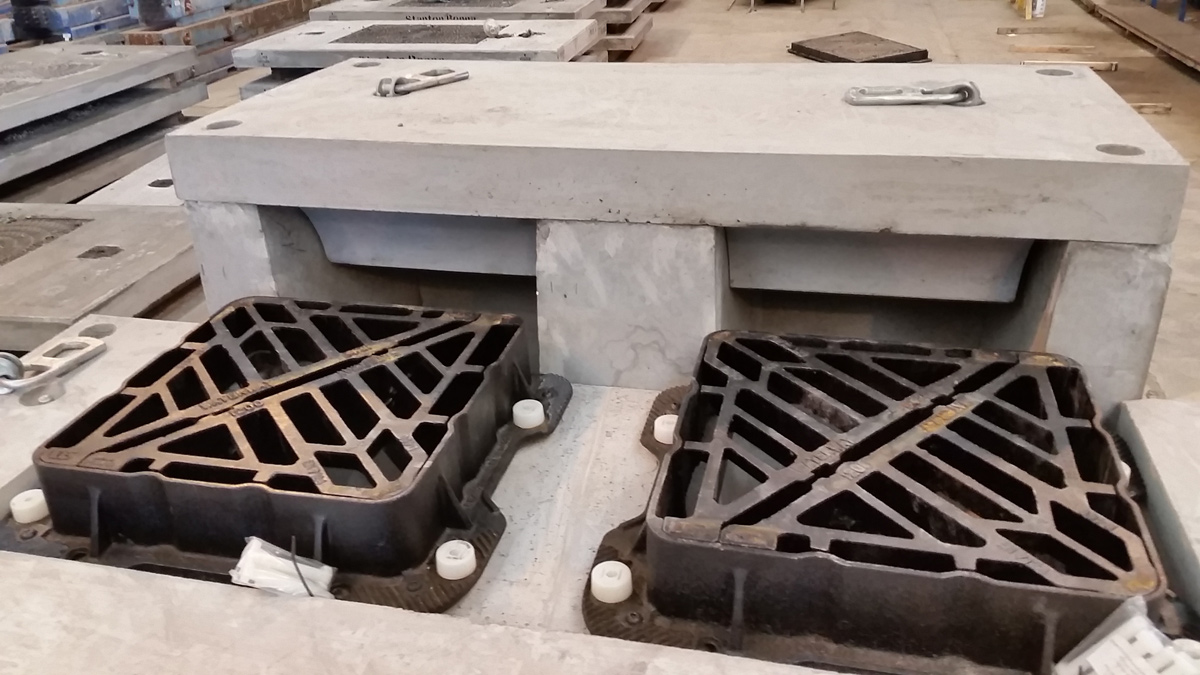