Monkmoor STW (2024)
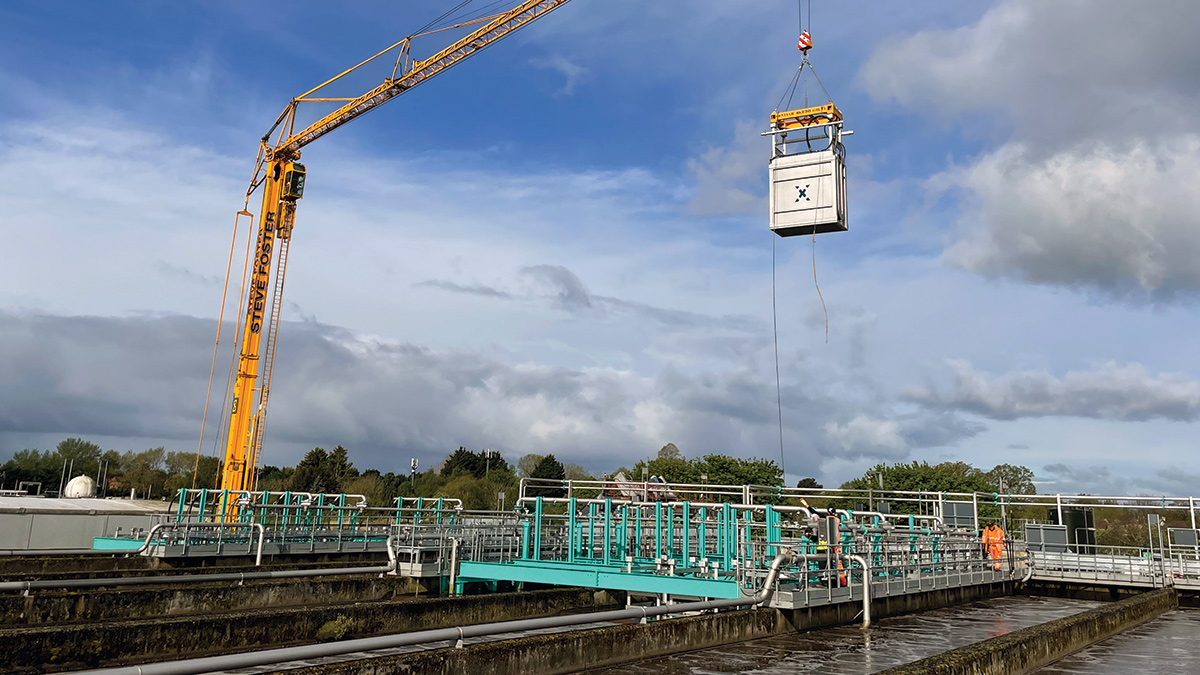
MABR module being lowered into place within a bespoke steelwork frame - Courtesy of OxyMem Ltd
Monkmoor Sewage Treatment Works currently serves a catchment of 116,000 (PE) in Shrewsbury, which is expected to grow to 146,000 by 2033. The works is a conventional activated sludge plant (ASP) and treats a combination of domestic and trade waste, consisting of landfill leachate, wastewater from other traders, meat process wastewater and sludge imports. The existing site consists of an inlet works, four storm tanks, four primary settlement tanks, four ASP lanes, four final settlement tanks, and a sludge treatment facility, which digests indigenous and imported sludge from surrounding sites.
Tightened permits
The table below shows the current and revised:
Current permit | Revised permit | ||
BOD | 25 mg/l | BOD | 25 mg/l |
SS | 45 mg/l | SS | 45 mg/l |
NH3 | 10 mg/l | NH3 | 10 mg/l |
P | – | P | 1 mg/l |
Fe | – | Fe | 4 mg/l |
The solution to meet the tightened P permit was to provide a new chemical dosing facility and additional final effluent monitoring equipment. In order to meet the growth driver, Membrane Aerated Biofilm Reactor (MABR) units were to be installed into the existing anoxic zones.
The aim was also to reduce the mixed liquor concentration within the ASP, thereby reducing the load to the final settlement tanks, helping to counteract the additional solids produced by chemical dosing. Installing MABR also had a CAPEX and OPEX saving over building new ASP lanes. The total value of the project was £6.2m.
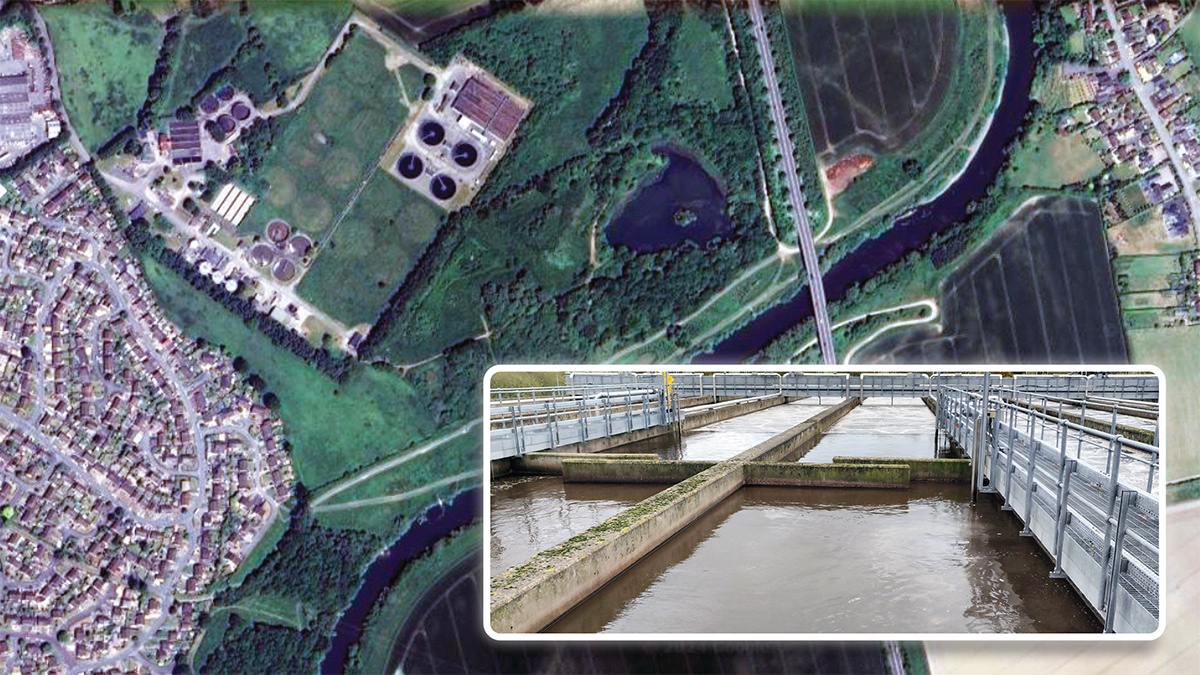
(left) Google Maps image showing Monkmoor STW and (inset) the existing anoxic zone – Courtesy of Mott MacDonald Bentley
Chemical dosing and FE monitoring
Two 60m3 ferric sulphate storage tanks were installed to meet the new phosphorous consent. The dose location was at the top of the ASP feed screw pumps as this is a turbulent area.
Existing ducts were used to cross the road to avoid breakout of concrete. The tanks were placed in a bund and instead of a delivery lay-by, sleeping policemen were used to contain the drainage in the delivery area from the rest of the road. As traffic will be stopped during delivery, this separates the delivery personnel from the live traffic.
The drainage is designed to gravitate from the chemical dosing area to the settled sewage. This is beneficial as the alternative location, the inlet works, is well over 300m away. This prevented additional excavation and removed the need for an additional pump station.
In the existing final effluent chamber, new iron and phosphorus monitors were installed. The existing kiosk was replaced, and existing monitors were relocated to the new kiosk, which was placed on the opposite side of the chamber to the existing, which allowed reuse of existing cables.
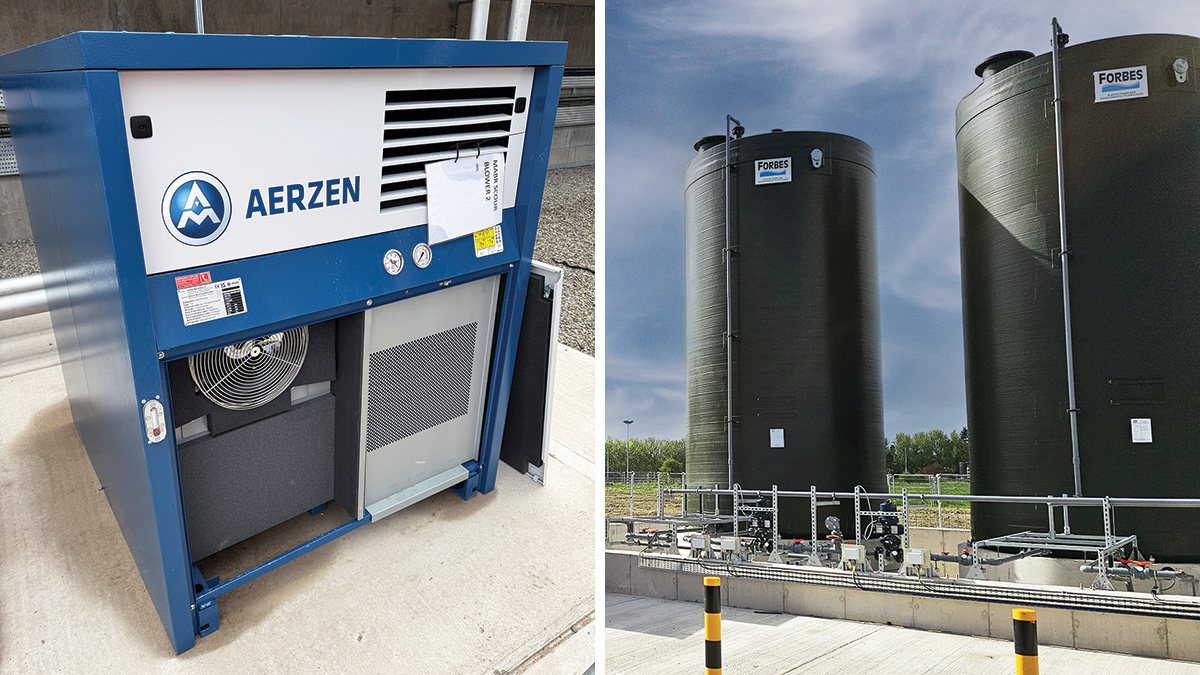
(left) MABR blower from Aerzen Machines and (right) two 60m3 ferric sulphate storage tanks installed in the chemical dosing area – Courtesy of Mott MacDonald Bentley
Introduction to Membrane Aerated Biofilm Reactor
The Membrane Aerated Biofilm Reactor (MABR) from OxyMem Ltd uses gas permeable polydimethylsiloxane (PDMS; also known as silicone) hollow fibre membranes, which supply oxygen for aerobic oxidation as well as providing a surface for the growth of the biofilm.
PDMS membranes are dense; meaning they have no pores. Process air is fed to the PDMS hollow fibres and the oxygen diffuses through the PDMS by molecular diffusion into the biofilm. This can simply be described as bubble-less aeration. The biofilm, which receives its oxygen directly from the surface on which it is growing, performs biological treatment for carbon and nitrogen removal, the two major pollutants in municipal wastewater.
Each OxyMem MABR module is made up of individual membrane fibres grouped together into bunches containing 550 fibres. A cassette is made up of 25 of these bunches, each potted into a PVC header. A number of cassettes are then placed into a module and connected to the inlet and outlet distribution manifolds.
As process air is fed to the module through the top distribution manifold, it travels through the fibres and is collected at the bottom manifold. The exhaust air collected is used to power two airlift pumps, so no moving parts or extra power is required. The airlift pumps ensure the zone below the modules is mixed and helps to ‘pull’ MLSS into each module. The MABR modules are designed with a top cowling that prevents bypass and ensures all the flow must travel vertically past an established biofilm on the network of high surface area membranes before it can exit the module and MABR zone.
Scouring the biofilm with air is essential to remove excess sludge and keep the biofilm thickness optimal during operation, maximising the MABR performance. Scouring is achieved using a dedicated scour blower, which supplies air through a distribution grid, installed at the bottom of the MABR modules, at a high flow rate in discontinuous mode. This grid is integrated within the module.
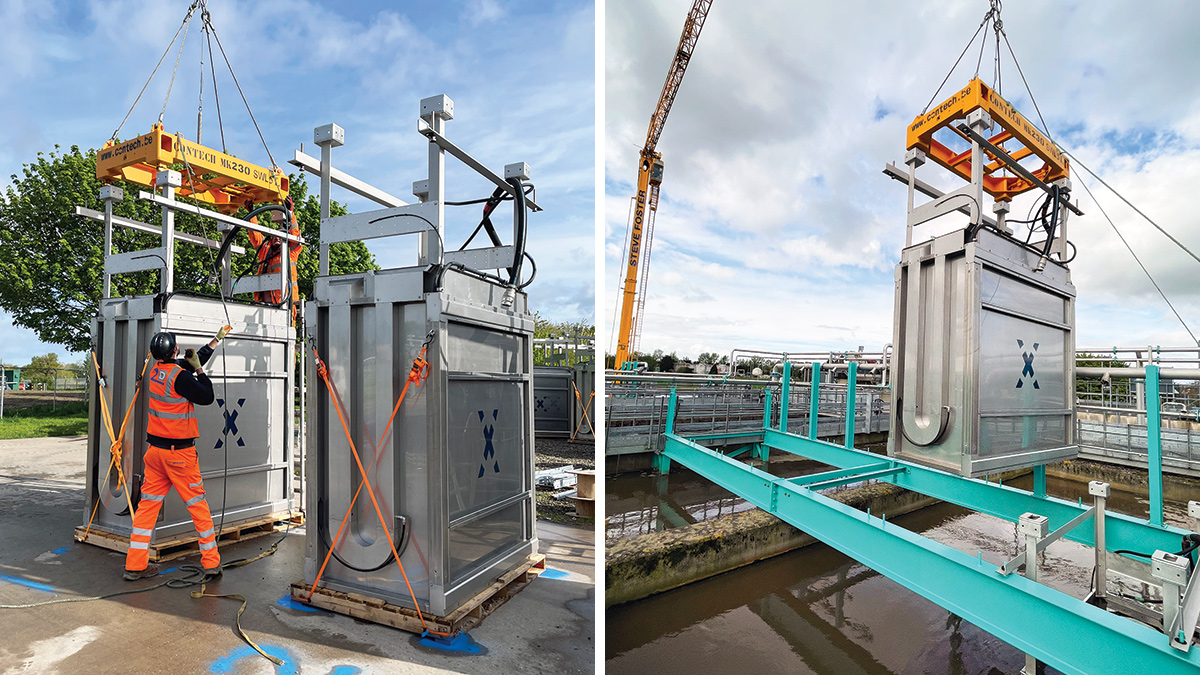
(left) MABR units being readied for crane lift and (right) lowering an MABR module into the support steelwork installed on the ASP anoxic zone – Courtesy of OxyMem Ltd
The MABR system implemented at Monkmoor is an MABR integrated with activated sludge (called MABR-IFAS or Hybrid-MABR), where the modules are dropped into the existing ASP anoxic zone. There are several key benefits to using an MABR system:
- Additional biological capacity.
- Minimal to zero additional footprint.
- No need to drain tanks (in most cases).
- Reduction of process spikes.
- Ease stress on existing assets.
- Low process emissions.
- Resilient process.
At Monkmoor, due to the growth driver, more ammonia needed to be removed from the ASP lanes. One option was to build more lanes, but the MABR solution allowed a retrofit of the existing tanks.
The requirement was that 162 kg N–NH4/d must be removed from the anoxic zones. Therefore, 48 (No.) OxyMem MABR units were installed; 12 per lane. The modules were grouped into banks of three; with each lane having four groups. Process air is supplied continuously to each module and the scour cycle operates periodically on each bank. To provide both process and scour air to the modules, four 15 kW blowers were installed. The process blowers were sized to provide 712 Nm3/hr of air and the scour blowers sized for 577 Nm3/hr of air.
MABR technology has previously been installed at Spernal STW but only ten OxyMem and five Veolia units had been installed as part of a trial. Monkmoor was the first large-scale installation of MABR within the UK.
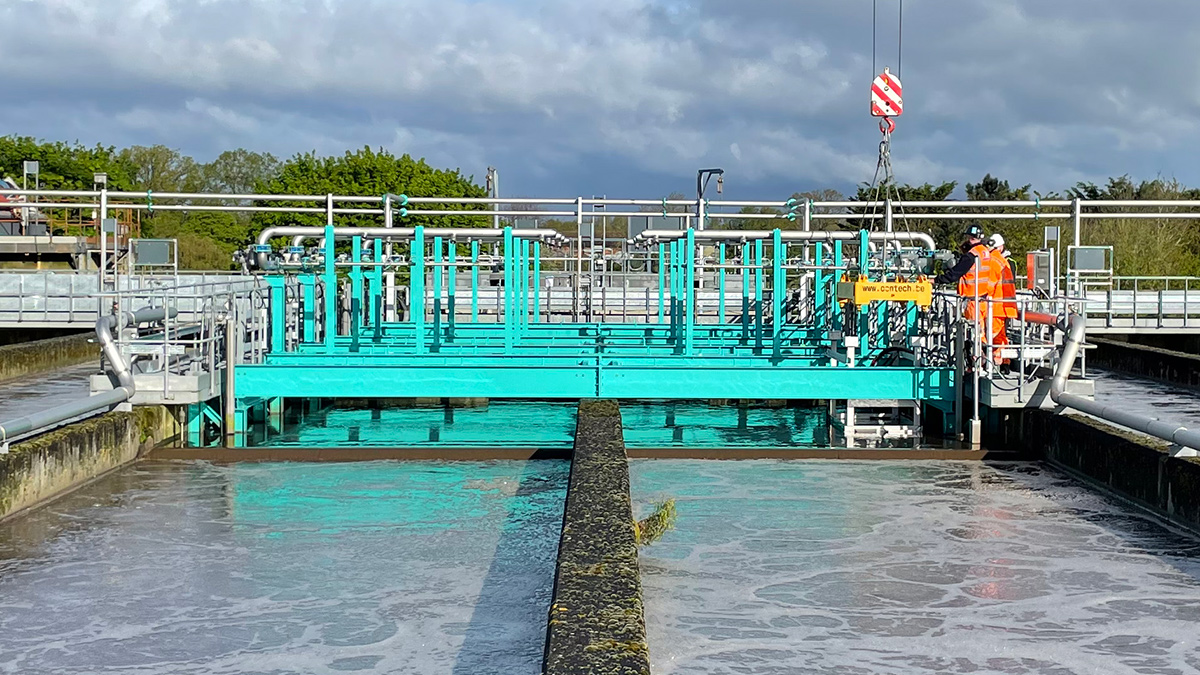
MABR installation – Courtesy of OxyMem Ltd
Monkmoor STW: Supply chain – key participants
- Client: Severn Trent
- Principal designer & contractor: Mott MacDonald Bentley
- MABR technology: OxyMem Ltd
- Mechanical installation: Alpha Plus Ltd
- Electrical installation: Lloyd Morris Electrical Ltd
- Chemical dosing: Colloide
- Quality monitoring: Servitech International Ltd
- MCC: CEMA Group
- Blowers: Aerzen Machines
- MCC kiosk: Dutypoint Ltd
Design decisions
Throughout the design process, MMB liaised with the Severn Trent operations team, to ensure they were onboard with the new assets, helping to give the team confidence in the design.
The mechanical installation was completed by Alpha Plus Ltd, who worked with MMB to design and install the steelwork to support the modules, and the pipework connecting the modules to the blowers. The design of the steelwork required consideration of the interfacing with the existing walkways. The key benefit of the MABR solution is the modifications to the ASP enabled the whole install to be undertaken whilst keeping the existing process live. This was a key consideration when deciding how to support the modules.
The final design involved steelwork spanning across the existing anoxic zones and dropping down underneath the existing walkways, to be supported by the concrete walls of the ASP. Structural checks were completed to ensure the existing ASP walls were suitable.
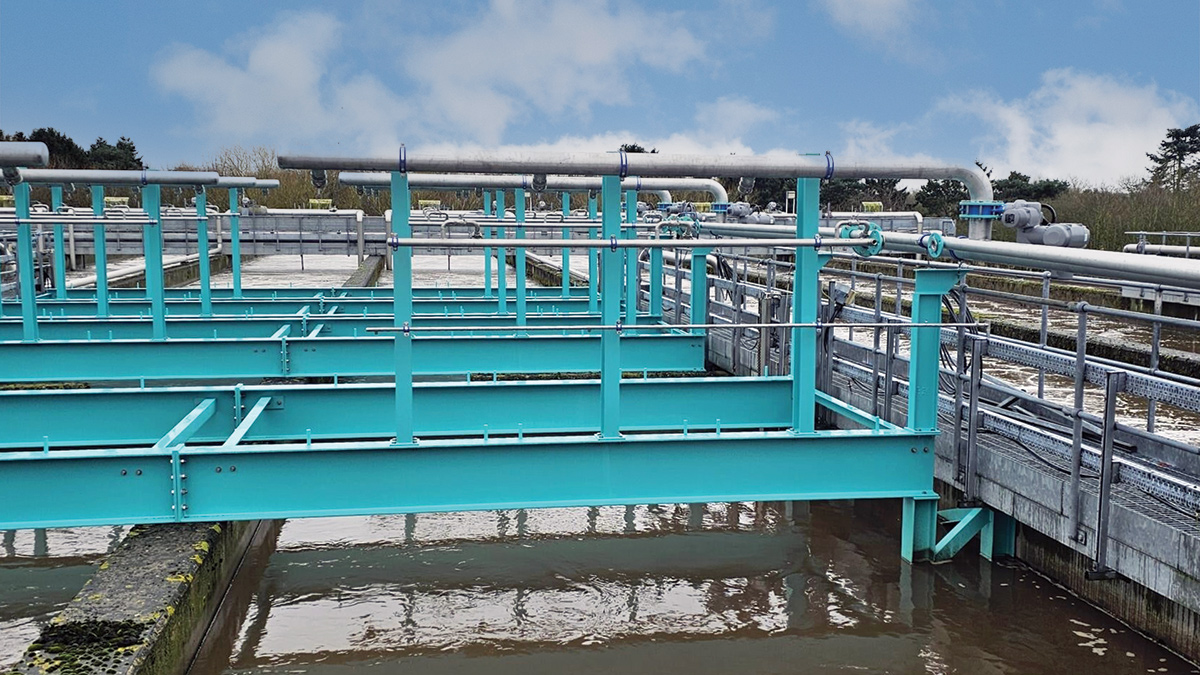
MABR support steelwork – Courtesy of OxyMem Ltd
Access was required in order to make the connections for the process and scour air. There were many options considered in terms of how access should be provided. By holding a design sprint, it was decided that in order to avoid installing walkways over aerated water, the existing walkways would be used as the main access. Installing additional walkways would reduce the area in which MABR units could be installed and would provide an access platform that would require authorised entry only.
The modules were installed using a lifting frame that enabled installation without needing access to the top of the modules. The pipework was made using a man riding basket. After installation, limited access is required so a non-permanent, temporary access solution can be used. By considering the interfaces with the existing walkways and the access challenges they posed, it was possible to complete the installation without draining the lanes. The modules were lifted into the tank using a crane and the existing crane pads on site were reused for this.
Flexible hosing attached to the module, supplied by OxyMem Ltd, was attached using a camlock to the process and scour air manifolds. Banks of three modules were connected to these manifolds. The manifolds were connected to common pipe runs back to the duty/standby process and scour blowers. It was important to ensure the aeration pipework had falls to low points to enable condensate collection and drains. When designing the pipework and steelwork, consideration for operator access for maintenance was also a priority. For example, the existing mixers within the anoxic zones were retained and need still to be able to be lifted out for maintenance, the layout of the new process enabled this. The pipework was designed so that it creates a vertical gallery on the main ASP walkway, enabling access to both new and existing equipment.

MABR module being lowered into place within a bespoke steelwork frame – Courtesy of OxyMem Ltd
For the steelwork, there were three options; 316 stainless steel sections, a 316 stainless steel lattice or FBE coated mild steel. It was not possible to procure the stainless-steel section sizes required. A stainless-steel lattice would be more readily available than stainless steel sections. However, there would be an increased risk of ragging, a lot of welding required, and it would be difficult to keep in tolerance due to the tendency of stainless steel to warp/pull forwards following welding. Additionally, if there was any ragging, this could lead to the water becoming stagnant and therefore corrosive to the stainless steel. In the end, despite possible re-coating being required if cut or drilled, FBE coated mild steel was selected. This was because the section sizes were more readily available, pipe support attachments would be easier as they could be bolted onto the beam flange, there would be possible cost savings over stainless steel and there was no increased risk of corrosion.
In order to monitor the performance of the MABR units, DO, redox and pH meters were installed into the anoxic zone on one lane. Additionally, an ammonia monitor was installed on the ASP distribution chamber and at the end of one of the anoxic zones.
These monitors were designed to be moved between lanes in to enable a performance assessment of each lane if required. An additional off-gas pipe was added to the first bank of modules on each lane so that if required, in the future, additional monitoring of the off-gas could be completed to determine the potential of MABR units to remove NOx.
The MABR units were constructed off-site in OxyMem Ltd’s factory. On site, the top cowling was installed, and the units were lowered into the lanes.
Conclusions/summary
A successful large-scale installation of MABR was completed, along with chemical dosing and FE monitoring equipment. Data is still being collected to show the performance of the MABR units but initial results are showing that the units are meeting the required ammonia removal target. The biofilm grew quickly and the required removal was taking place within a month.
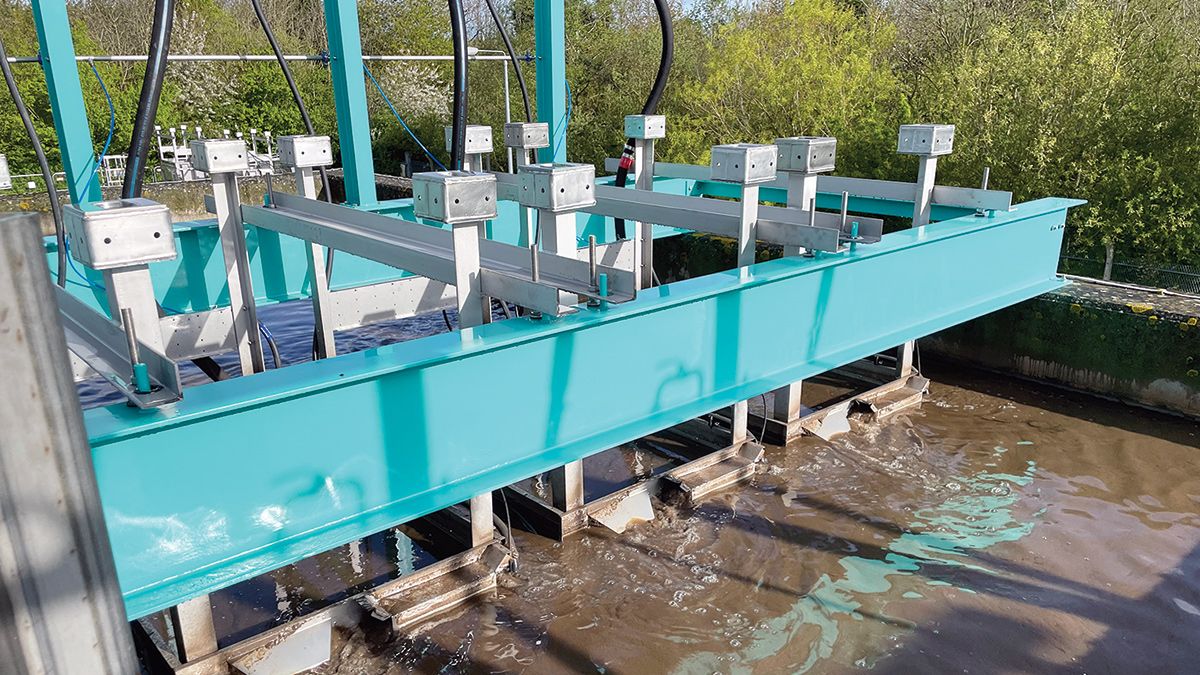
MABR support steelwork - Courtesy of OxyMem Ltd