Hydrolox
Our engineered polymer traveling water screens are changing the way facilities think about intake screen performance. Proven to exclude debris and reduce harm to aquatic life, these effective, longer-lasting solutions are easy to install and require virtually no maintenance. Our screens address the needs of water-extracting facilities across a wide range of industries, while ensuring compliance with the UK Eels Regulations and the EU Water Framework directive.
We offer single-point-of-contact project management services to help eliminate bottlenecks during screen installation. Our team supervises the entire process, working with your preferred subcontractors and in-house crew (as needed) to help you minimize downtime while optimizing in-house resources, screen performance, and screen life. This process can include initial site surveys to develop scope of work, project meetings, and factory acceptance testing.
All Our screens are backed with industry-leading three-year or four-year warranties (warranty terms determined by specifics of screen, application, and installation). In addition to comprehensive on-site support before, during, and after installation, we also provide ongoing expert technical support and award-winning customer service.
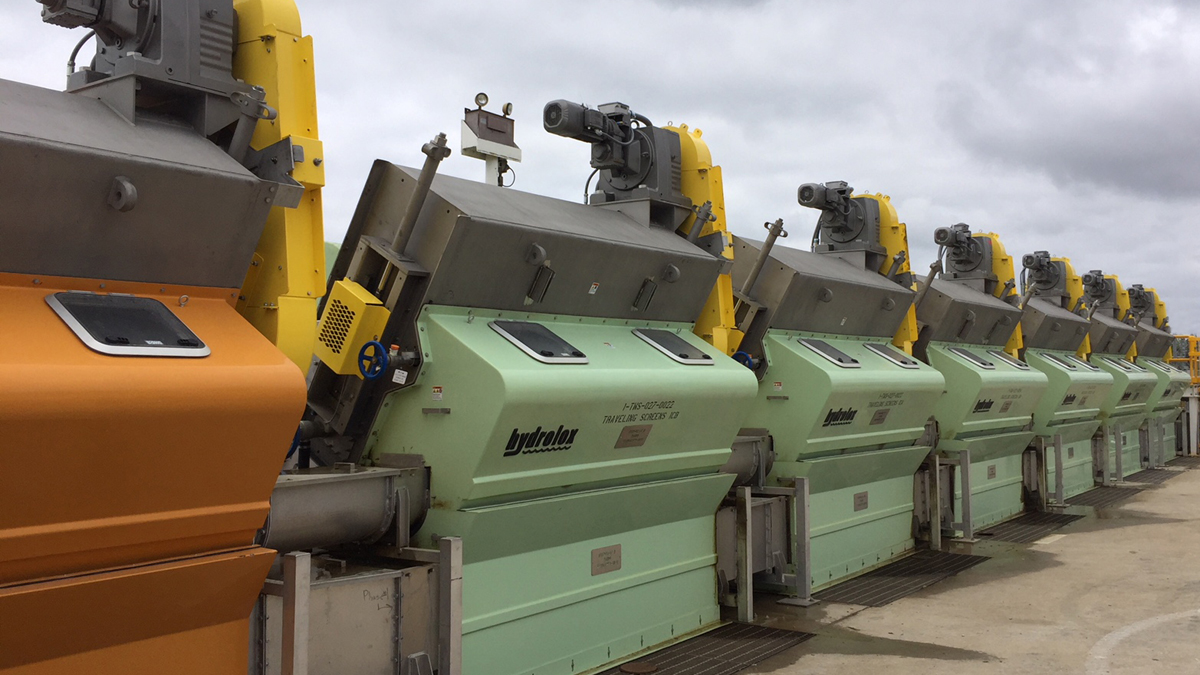
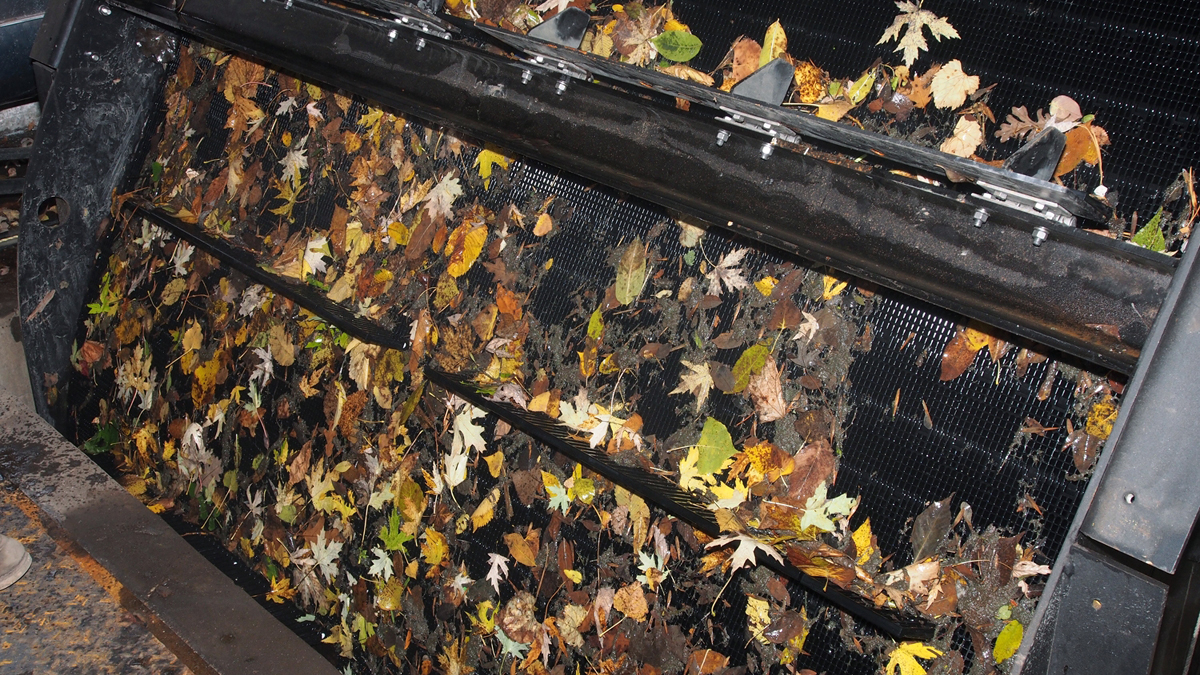
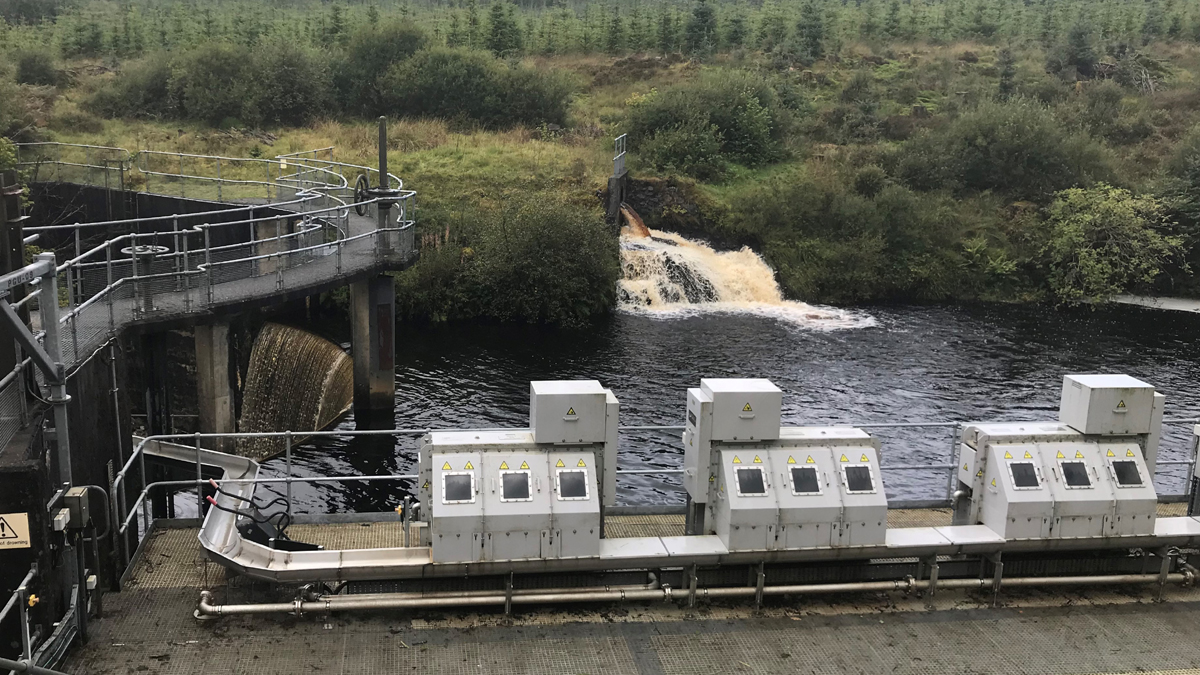
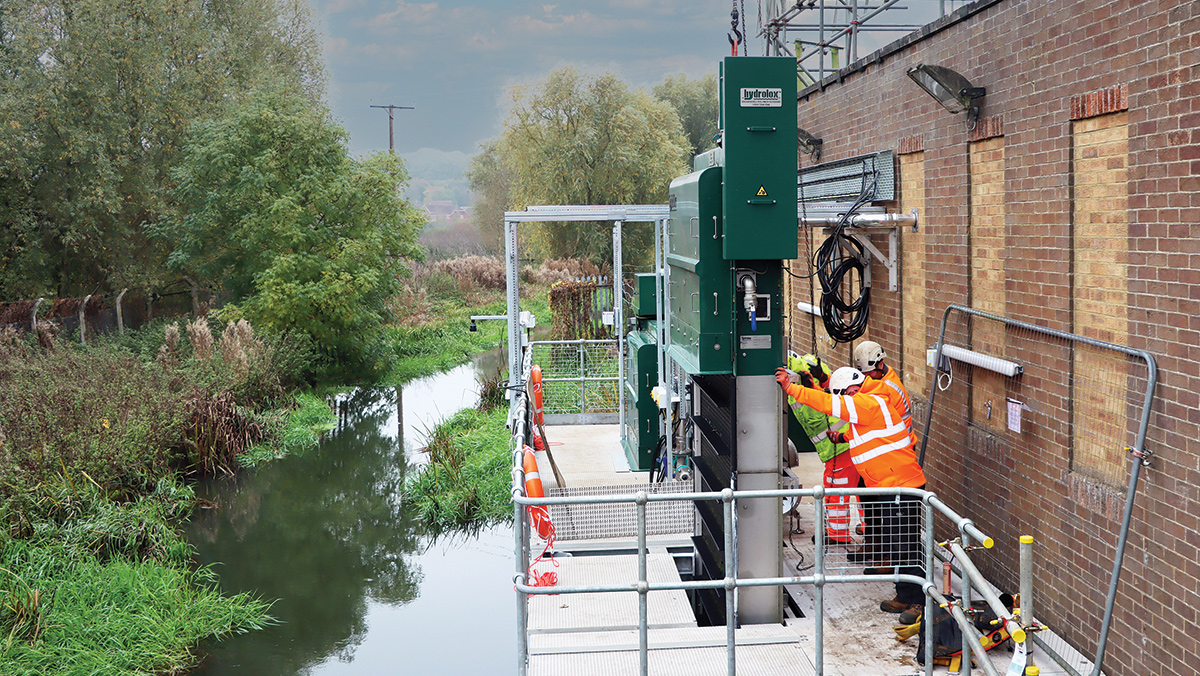
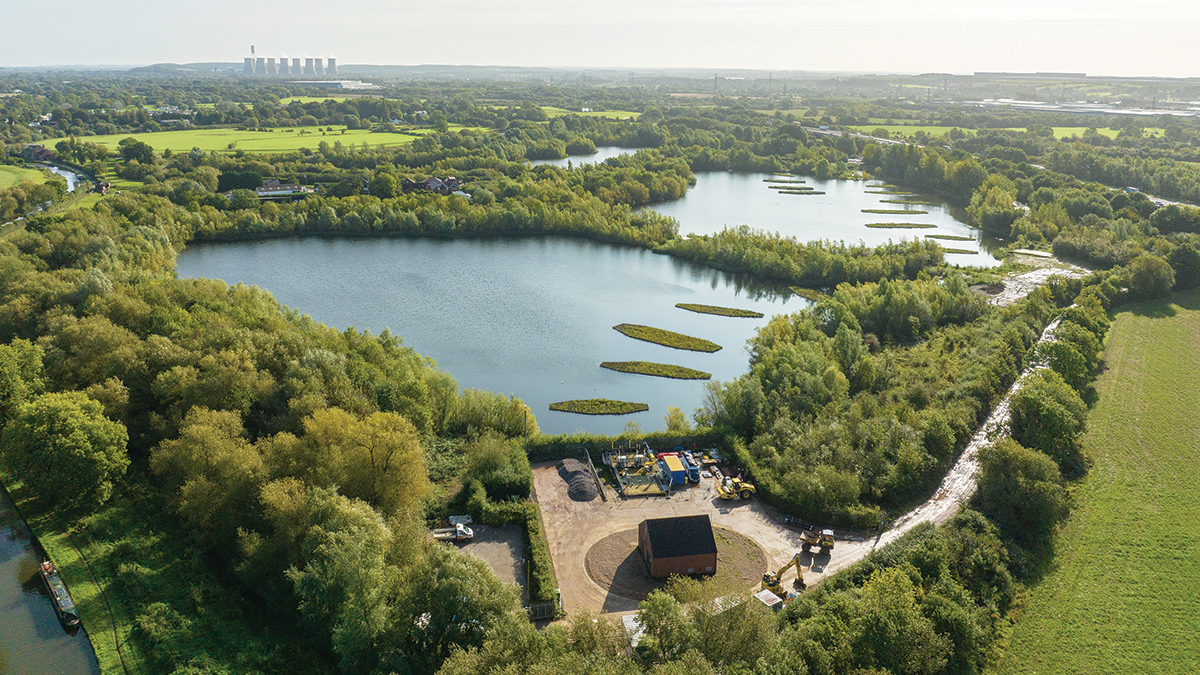