Technocover Ltd
Cardiff Bay Barrage – Access Hatch Solutions (2019)
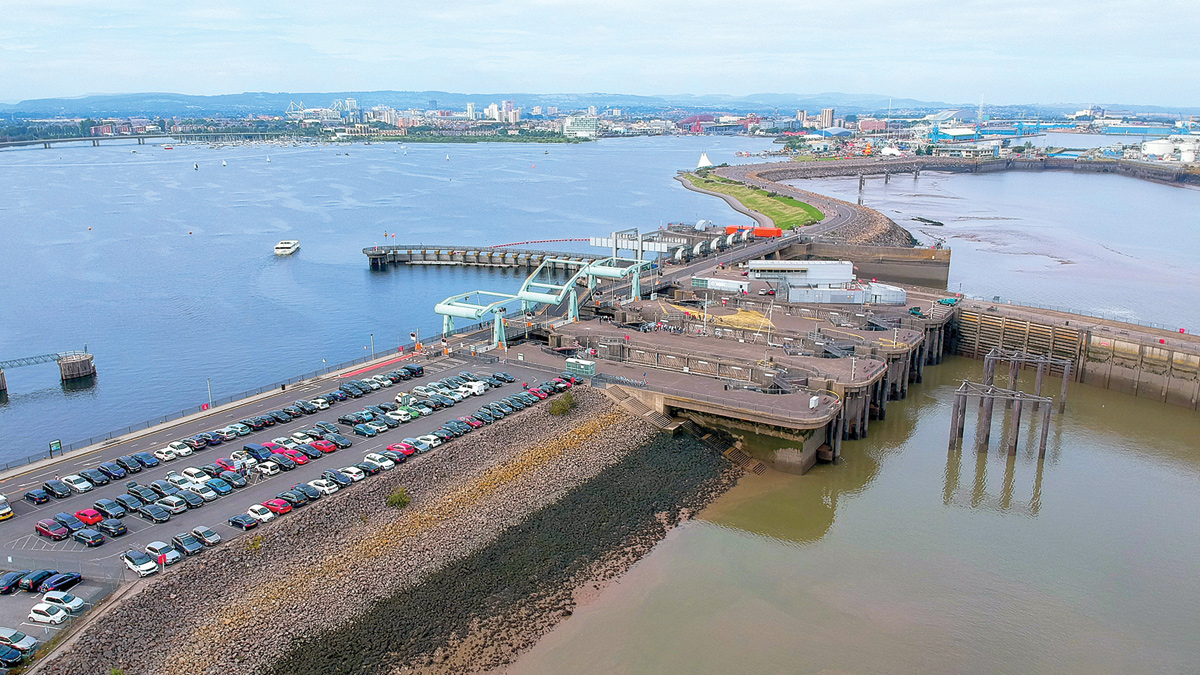
View of the Cardiff Bay Barrage impounding structure with the locks and bascule bridges shown centre
Completed in 1999, the Cardiff Bay Barrage was designed to regenerate the city waterfront as a vibrant and attractive destination while creating an efficient, two-way control interface between the tidal waters of Cardiff basin and the river estuaries beyond. The challenge of achieving this balance of functionality both sides of the barrage is reflected to a degree in a more recent engineering feat – though on a very much smaller scale. Two-way access management, water resistance along with discrete appearance are embodied in the design of access hatches installed to enhance the safety and resilience of the barrage plant gallery. When asked to engineer these special access solutions, Technocover’s surveyors and technical team soon realised that more than standard galvanised steel access covers would be required.
Tidal range
The £220m civil engineering project saw the creation of a focal 200 ha freshwater lake or bay, the catalyst for a £2 billion regeneration of the old dockland areas of Cardiff and Penarth. The bay replaced the unattractive sight of mud flats exposed within an urban estuary with a tidal range of 14m, the second highest in the world.
The barrage features several bascule bridges, locks, sluice gates and a fish pass, as well as a landscaped embankment area providing public space to promenade and picnic.
At the centre of operations is the barrage control room, the main point of contact for boats navigating to and from Cardiff Bay. This is staffed 24 hours a day, 365 days a year by a team of operators, lock managers and engineers.
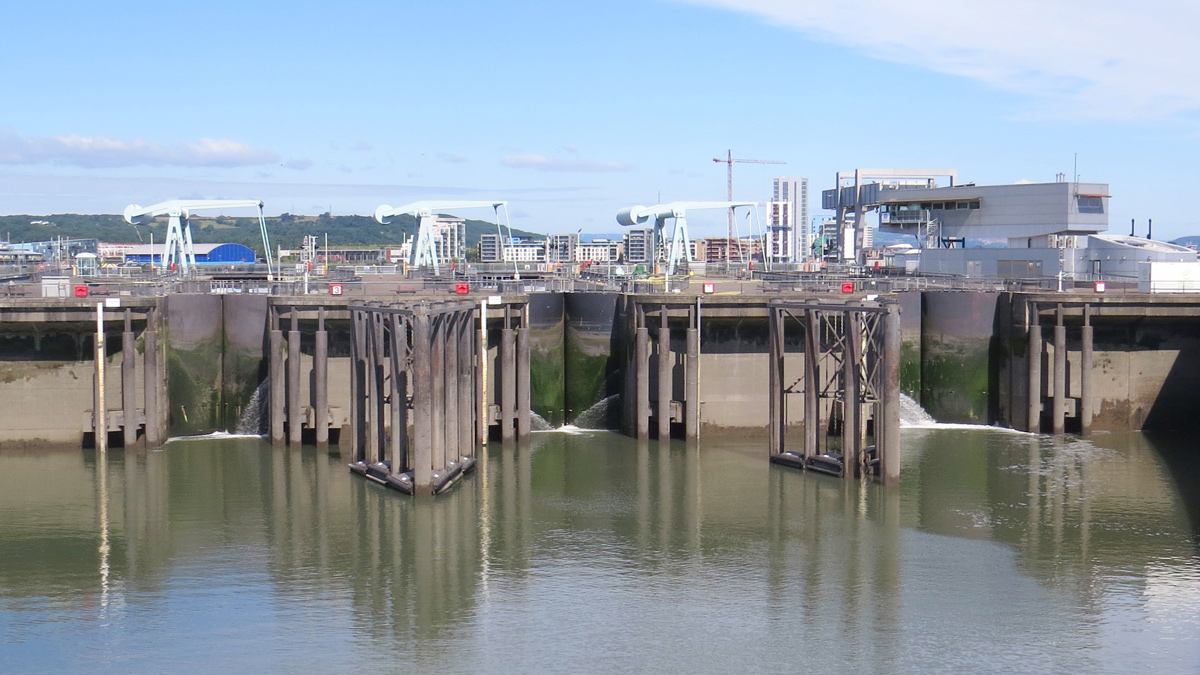
View of the three locks and bascule bridges where Technocover’s special emergency hatches provide 2-way access to the below plant gallery
Three locks, each measuring 40m long, allow boats to navigate between the Severn Estuary and Cardiff Bay. They can accommodate up to 10 average sized vessels at any one time, with passage through the locks taking between 5 and 20 minutes, depending on the tide. Each lock has a bascule bridge weighing approximately 88 tonnes. The lock gates are up to 16m high to enable boats to pass through at all stages of the expansive 14m tidal range. When the locks are closed, they allow passage over the barrage structure for pedestrians, cyclists and vehicles.
Five sluice gates control the level of water in the bay. These permit flows from the rivers Taff and Ely to exit into the Bristol Channel, or create a barrier to stop the high tide from entering the bay. Over a quarter of a million litres of water per second can flow through each gate, which measure 7.5m high and 9m wide.
Combined access and emergency escape hatches
Technocover was contracted to redesign the existing covers and manufacture four new flush-fitting emergency escape hatch access covers over shafts to the barrage operations gallery in areas close to the bascule bridges.
The four units were required to provide safe exit routes for personnel carrying out inspection and maintenance within the barrage’s internal gallery shafts, even if closed and locked from above.
Technocover’s knowledgeable designers set about the challenge of creating these special emergency escape hatches to meet the specific operational needs of the Cardiff Bay Barrage application.
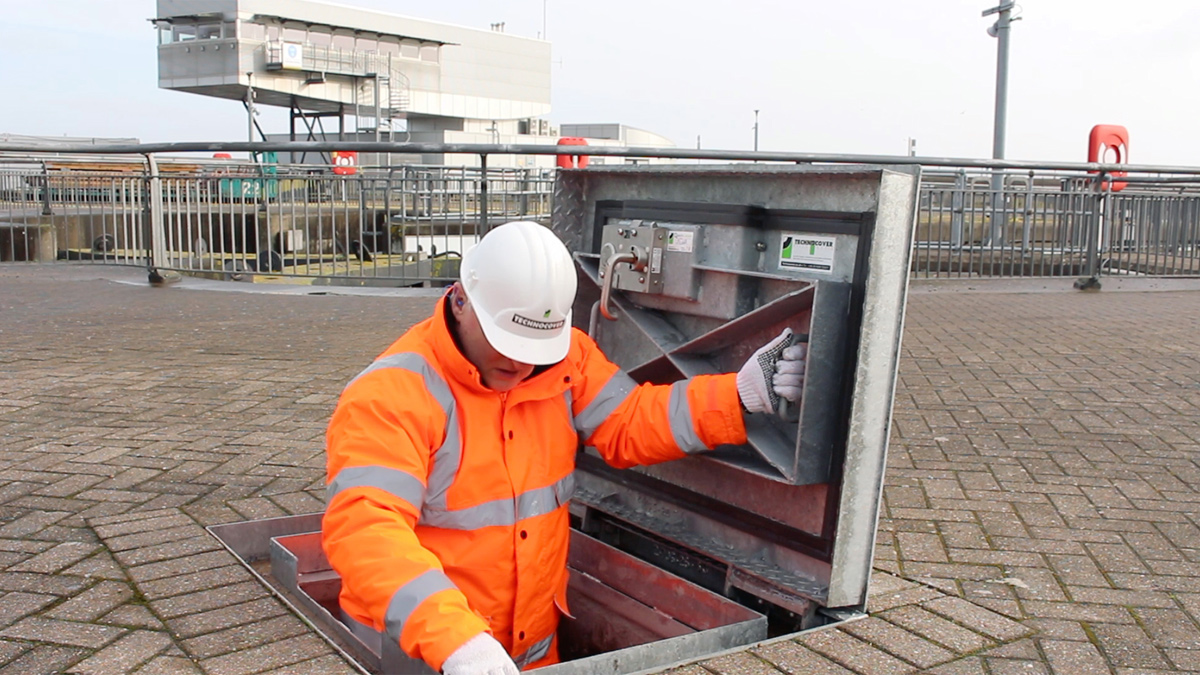
The emergency escape hatches allow quick exit from the shaft via a quick-release handle that overrides locking above. Note the substantial cross-bracing reinforcement under the lid to withstand C250 loading from plant and emergency vehicles
By incorporating an external locking system compatible with internal emergency escape hardware, access from above is controlled and facilitated via a turn-catch hasp and staple padlocking entry system. From below, this can be overridden by a single lever handle, providing efficient exit from inside the shafts, especially in an emergency situation.
Each cover also has a shrouded and hinged anti-trip padlock housing, designed to accept a LPCB approved security padlock. This is operable from above (once the padlock has been removed), and also from below by using a release handle on the slam-shut locking facility. An additional grab handle on the underside of the cover lid further assists exit from the chamber.
Surface water
Management of surface water – to prevent ingress into the shaft – was another important aspect of the design.
The frame design was adapted to incorporate a moated drainage channel with twin drainage pipes and hose connection points. This allows any water build-up from inside the frame to drain through a top connection pipe and drain tube into a sump at the bottom of the shaft.
In addition, sealing was provided to help prevent the ingress of water. This was fitted to the underside of each cover lid as standard, to safeguard it from damage when the cover is in the open position.
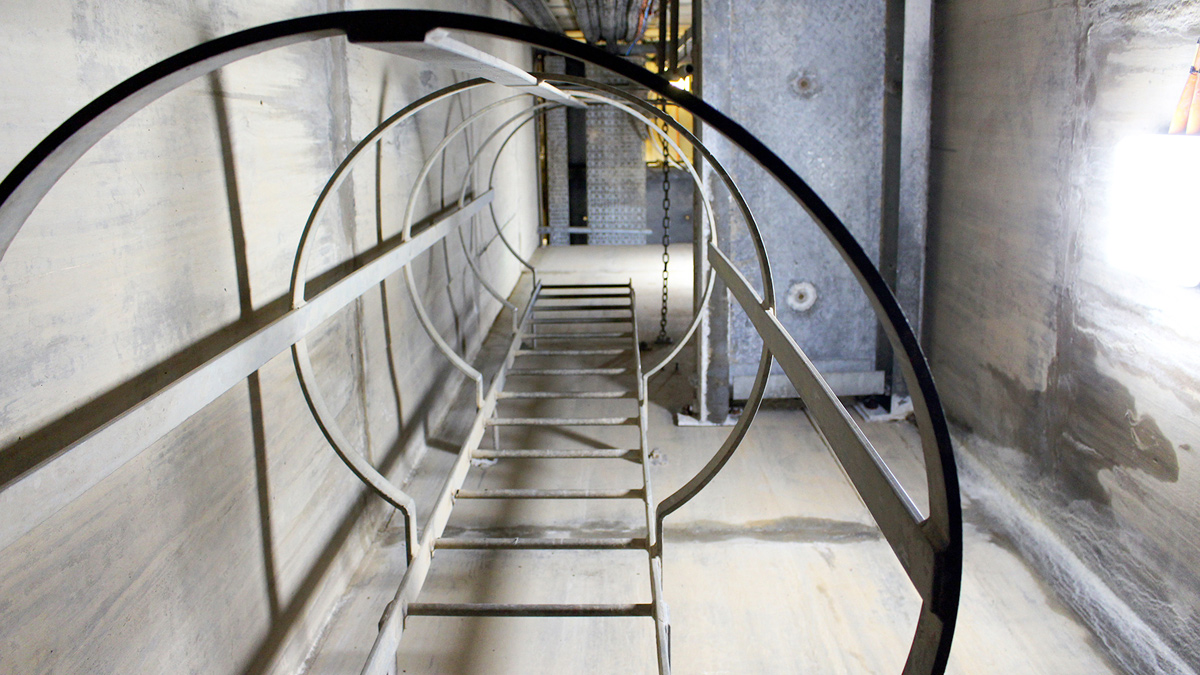
The 18m descent from the emergency escape cover at bascule bridge level to the internal barrage gallery
Three of the covers are located within block paved pedestrian areas, requiring appropriate underbracing to meet a C250 load requirement for occasional trafficking by utility plant. The fourth needed no additional strengthening, being sited within a tarmac area enclosed by protection rails.
In addition to these special adaptations, Technocover’s hinged, flush fit access cover offered the following standard features and benefits:
- Concealed holding down anchor points to maintain secure anchoring of frame within paved area.
- Single, sealed lifting keyhole (BSI conformant) in left-hand side of cover.
- Recessed padlock with hinged and anti-trip locked-down cover plate, complete with loading identification, to safeguard against tampering and ensure stable surface underfoot.
- Stainless steel, torsion-sprung lid providing operation by a single person in compliance with the Health and Safety Executive directive for manual handling.
- Concealed hinges to protect against damage from vehicle overrun and ingress of grit and other potentially damaging debris.
- Cover lid opens to 95 degrees to give convenient, safe and unobstructed access to chamber shaft.
- Hand operated, automatic safety stay that firmly holds hatch lid in open position during entry/exit.
- Wide sealing strip to underside of cover lid, preventing damage to seal when cover is open.
- Structural underbracing to underside of hatch cover, designed to withstand the required C250 loads.
- All mild steel hot dip galvanised after manufacture to BS EN ISO 1461 for long life weather-resistance and durability.
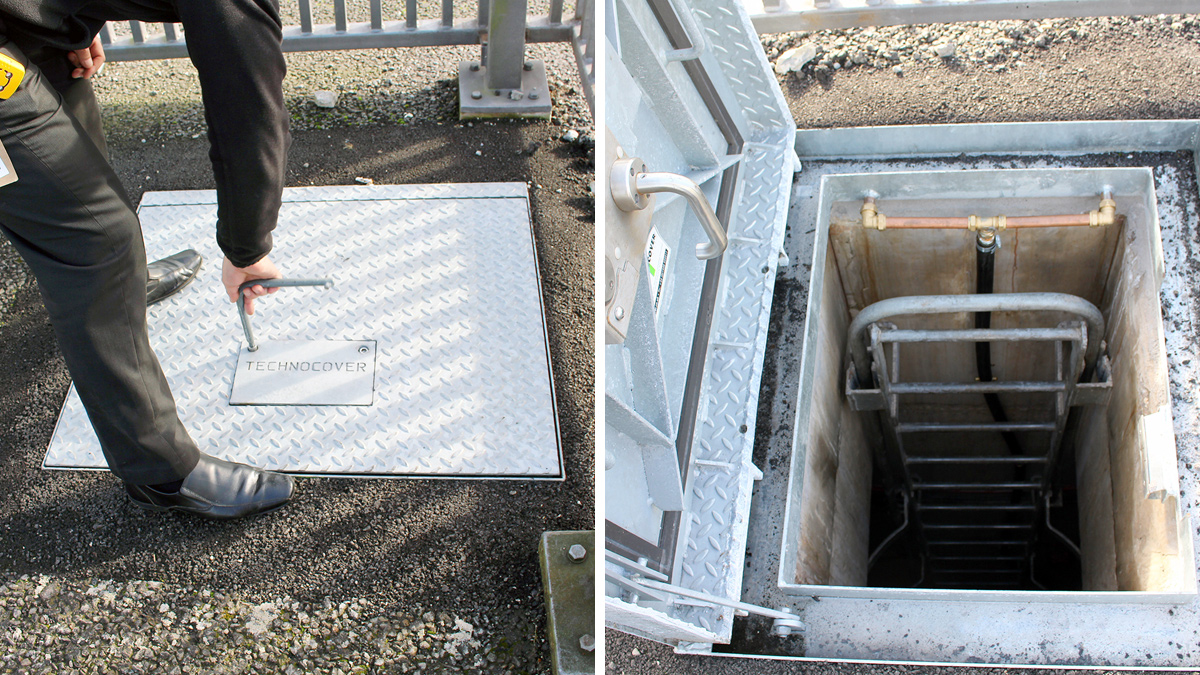
(left) Access cover within tarmac zone with protection rails around it. Note the custom locking key required by the client and the concealed padlock housing, as well as the shrouded hinges at far edge maintaining flush anti-trip finish and (right) Interior showing copper pipe from frame drainage connection points and the central single black hose that carries water 18+ metres down to the sump in gallery base
Design attention
Careful design attention was needed to ensure that the hidden hinges and concealed padlock were achieved while maintaining a flush, hazard-free finish and discrete look to minimise visual disruption of the surrounding block paved aesthetics.
Simple routine maintenance is carried out to ensure the covers continue to function efficiently. This involves opening the covers periodically to vent the chambers, and to check that the internal drainage connections and hoses are kept clear of any obstructions. If water is present, it can be drained away from the side frames and down the 18 plus metres shaft to the barrage gallery sumps.
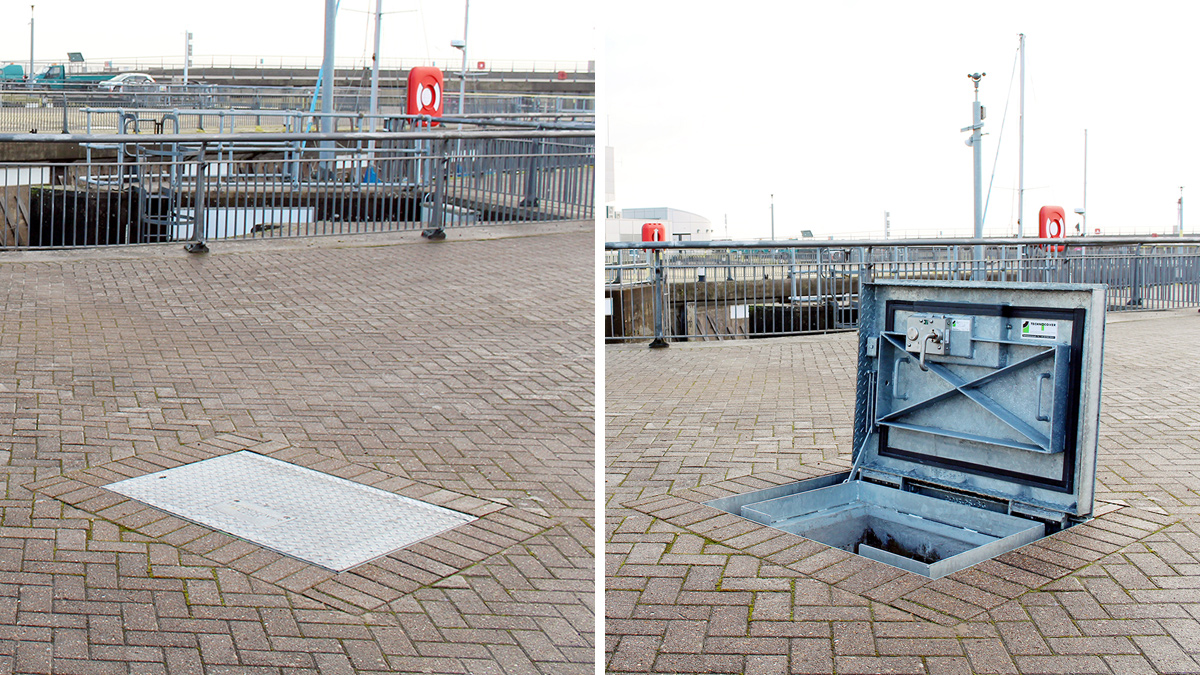
Chequer plate flush fitting emergency escape hatch cover shown in closed and open position. Please note that barriers are installed around open unit during normal operations
Twenty years on from completion of the barrage, Technocover’s access solutions continue to reflect the development’s ethos to achieve excellence and innovation in the field of urban regeneration and meet the highest standards of design and quality. Their structural integrity, water-resistant design and long life post-galvanised zinc finish will also ensure system weather-proofing and durability for the next twenty years and beyond.
For water supply and process sites – such as reservoirs, water treatment installations, boreholes and pumping stations – upstand versions of these emergency escape hatch covers are also available.