Technocover Ltd
Physical Protection of Assets (2018)
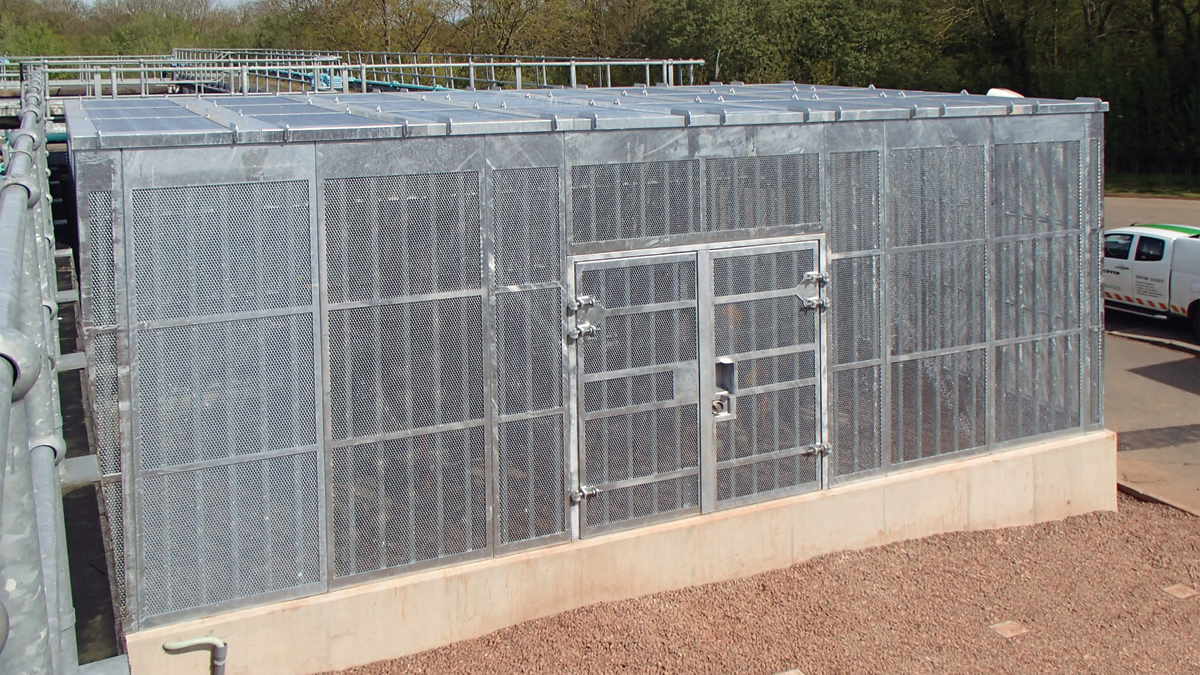
UltraSecure Level 4 LPCB approved high security five-sided Technocover cage system complete with padlock entry SR4 twin leaf hinged mesh panel doors
The security landscape within the UK’s water industry has evolved beyond recognition since the advent of dedicated legislation twenty years ago. From the upgrade of service reservoir protection that rolled out from the late 1990s, to the mature and sophisticated levels of security that ramify through today’s network, UK water sets a world-class standard in its approach to water asset hardening. It has seen nothing less than a revolution in the water security product market dominated by LPCB certificated equipment, from upstand covers and security louvres, to large security kiosks – built off-site and craned into place. Today, security hardware is being seamlessly integrated with today’s digital technology including electronic access control, wireless alarm networks and CCTV. As the industry gears up for AMP7 with talk of asset optimisation, operational efficiency and a hefty focus on ‘value’ rather than ‘cost’, security company Technocover believes its founding principle of ‘Total Service’ is more relevant than ever before.
Delivering best value through ‘Total Service’
With the introduction of reservoir security legislation in 1997, Technocover was one of the first to market with a double-skin upstand access cover tested and approved to the Loss Prevention Certification Board’s (LPCB) exacting LPS 1175 standard for security performance.
While LPCB has been critical to Technocover’s success, the company has maintained its lead by also focusing on project and customer support through ‘Total Service’. This includes site surveys, risk assessment advice, design with value management input, specialised logistics and delivery, installation, maintenance, even removal and recycling at end of service.
‘Total Service’ takes a holistic view of the product’s ‘journey’, from concept to decommission, to ensure it provides the best value, whole life solution focused on customer needs and cost efficiency.
While maximising customer satisfaction, it tailors UltraSecure solutions to the long-term outcomes, operational efficiency and ‘optimised asset intervention’ which have become the imperative of AMP6 and AMP7.
The emphasis is on close cooperation, listening to needs, and dovetailing products and site services to make life as easy as possible for clients and their delivery team, as well as avoiding under- or over-specification.
Closer collaboration
The current asset management plan (AMP) focus on transformative innovation and operational and cost efficiency is relying heavily on improving supply chain interaction, including closer collaboration between water company delivery parties.
Early involvement is a crucial part of this approach. Through close partnership and early engagement with the water company and their chosen tier 1 or tier 2 contractor, Technocover as a technology supplier is better able to support the delivery of high quality, timely and cost-effective solutions compliant with security needs.
Close collaboration with the client and project team at early planning stage allows the screening of every aspect of the product solution – its design, installation and operation – to identify opportunities for efficiency gains and cost savings, and achieve on-time, on-budget construction.
With this level of technical and service input, operational issues can typically be identified and resolved in the design that might otherwise lead to delays or difficulties in completing routine inspection and maintenance tasks, or even emergency procedures.
Case study – Early involvement: getting it right first time
The importance of early consultation with suppliers is highlighted by a recent upgrade project. The client placed an order for a twin-leaf LPCB SR 4 upstand access cover to harden the security of a borehole chamber.
As shown in Figure 1 (below), the cover was fitted on a high plinth which was accessed from the road via steps. To unlock the cover, the operative would need to climb a further 950mm using a ladder to gain access to the borehole. Due to the chamber height from the ground, it was not possible for an operative to open the cover leaves standing at ground level. More hazardous still, it meant using a ladder at the side of the chamber introducing the added danger of a fall from height.
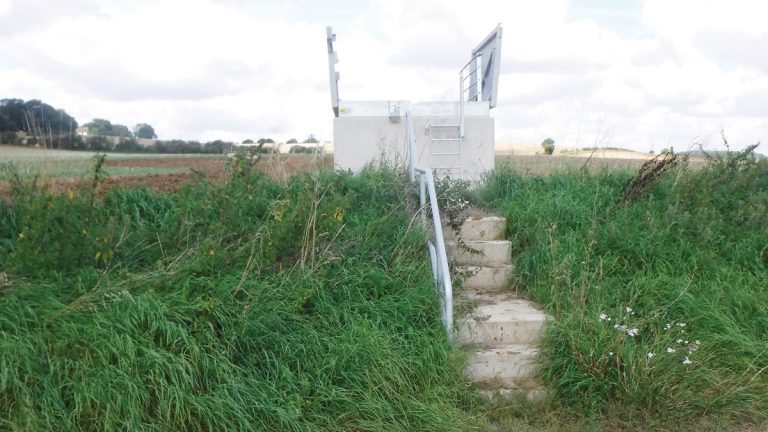
Figure 1: Early consultation with the supplier could have identified the need for a more appropriate access solution to secure the borehole and protect operatives
Under normal circumstances, the cover would have been entirely fit-for-purpose if installed on a conventional upstand at typical ground level. However, in this case the client did not stipulate when ordering that the cover needed to be raised almost a metre above ground height.
To overcome this initial oversight, Technocover proposed a new physical security access solution (Figure 2 below).
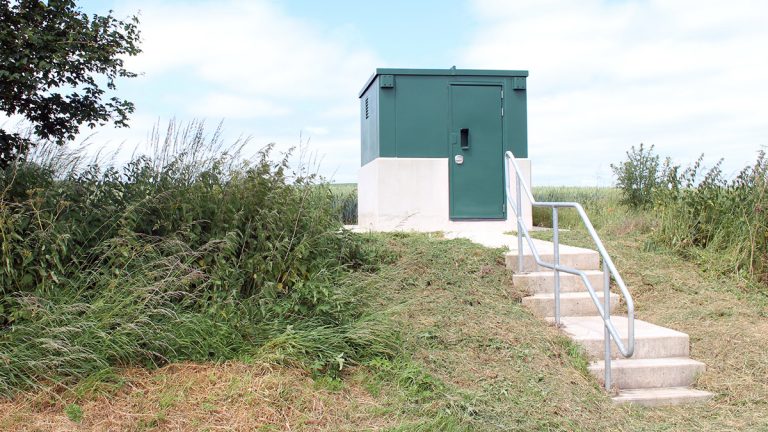
Figure 2: Technocover devised a half-height kiosk to fully secure the borehole while providing personnel with safe access to the chamber via a full height door
The twin hinged cover was removed and replaced by a 1335mm high, half height UltraSecure modular kiosk. Measuring 2300mm x 2300mm on plan, it features a single piece, removable roof sited in place of the upstand cover unit. The refit was done by one of Technocover’s installation teams within a morning. This included the cutting of a new 940mm x 900mm opening through the existing 200mm thick wall for integration of the SR 4 security door where the ladder had previously been.
The new assembly was hot dip galvanised after manufacture to BS EN ISO 1461 and then painted with a forest green finish.
This enclosure also has high and low louvre vents with internal insect mesh, the SR 4 door has rim lock with external ‘T’ handle entry and shrouded hasp and staple locking to suit LPCB approved padlock.
Clearly, early engagement could have avoided the additional costs of remediation.
Cost-efficiency through collaboration
Fully resourced project support, like Technocover’s Total Service, will become increasingly important to an industry tasked with working in more efficient and collaborative ways in AMP 7 and future spending programmes.
Early planning and supplier involvement can have a significant impact, in both the short and long-term, on the cost and other important outcomes of security procurement. It allows delivery partners to work proactively and be innovative, combining their individual expertise to anticipate issues and problem-solve, from design to installation to in-service operation.
As well as avoiding specification errors, early collaboration helps to ‘design out’ risks associated with health and safety and asset failure. There is also scope to ‘build in’ maximum functionality and necessary contingencies so that reactive maintenance, unplanned interventions and service disruption are minimised.
After 25 years, Technocover offers leading capability in harnessing value engineering and operational efficiency in the increasingly innovative security solutions demanded by the industry while maintaining LPCB compliance.
With the opportunity to add value and optimise performance, early planning of physical security work enables greater transparency and control/forecast of cost throughout the asset life-cycle. Its role should not be underestimated as the water industry strives for better outcomes within the supply chain and customer service.
This article was prepared by Technocover Ltd(T) 01938 555511 (W) www.technocover.co.uk