MGF Ltd
We have a vast experience in delivering shoring solutions to the water and utilities sectors including a wide range of shoring and safety equipment, trench sheets and sheet piles as well as providing bankside retention solutions on UK canals, riverbanks, and marinas.
Our bespoke waler and tie back system is a versatile solution that can be used in a range of configurations to suit different ground conditions, we also hold an extensive range of overlapping and interlocking trench sheets and sheet piles with galvanised or sealant options.
Headquartered in Ashton in Makerfield, near Wigan, we are committed to providing our customers with complete engineered solutions and promoting current best practice for all types of excavation works.
The company now employs over 400 people with a proud record of sponsoring and employing local engineering graduates and has 14 different depots around the UK from Dartford to West Lothian, Scotland. We also have an in-house transport fleet of over 60 vehicles giving us the flexibility to meet our customers needs.
With a vast product range from UniShore® systems to gantries and lifting beams, the hire and sale of our products is fully supported by our team of qualified engineers, experienced representatives, hire desk and operational staff. Providing national coverage, our depots hold extensive fleet stock, modern handling equipment and dedicated transport ensuring operational efficiency.
The hire and sale of our products is fully supported by our team of qualified engineers, experienced representatives, hire desk and operational staff.
Our values of commitment, innovation, and sustainability have guided us well in the last 35 years and will take us in to the future along with our mission which is to be the most trusted supplier of excavation safety solutions.
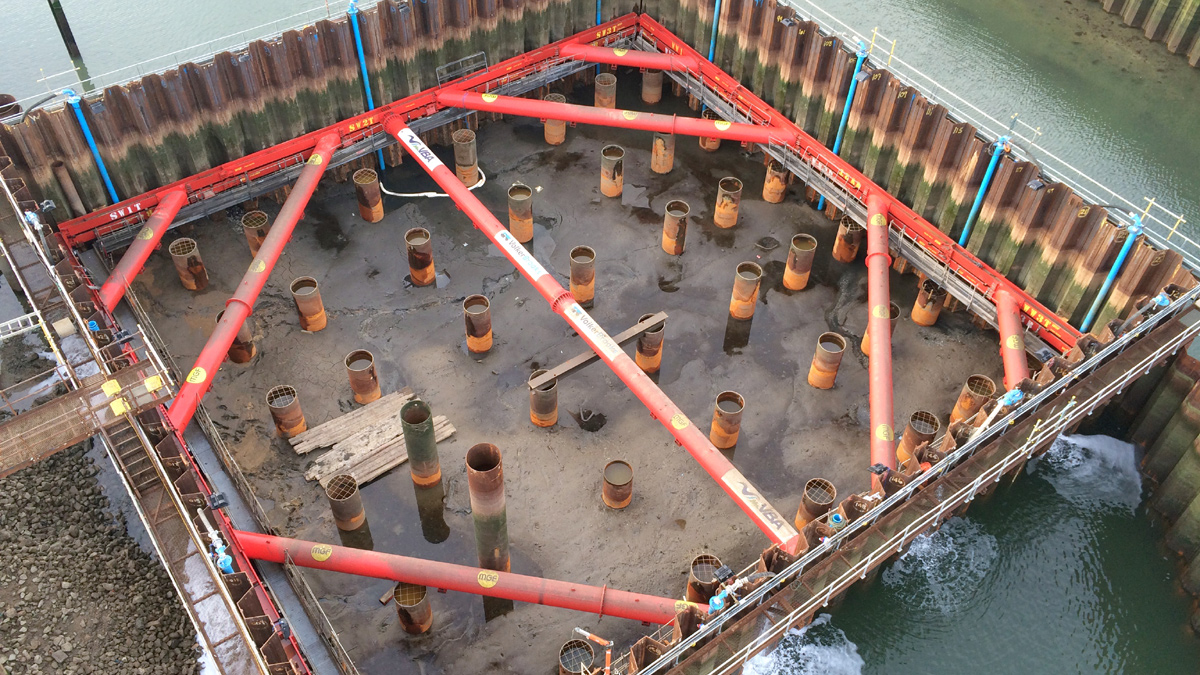
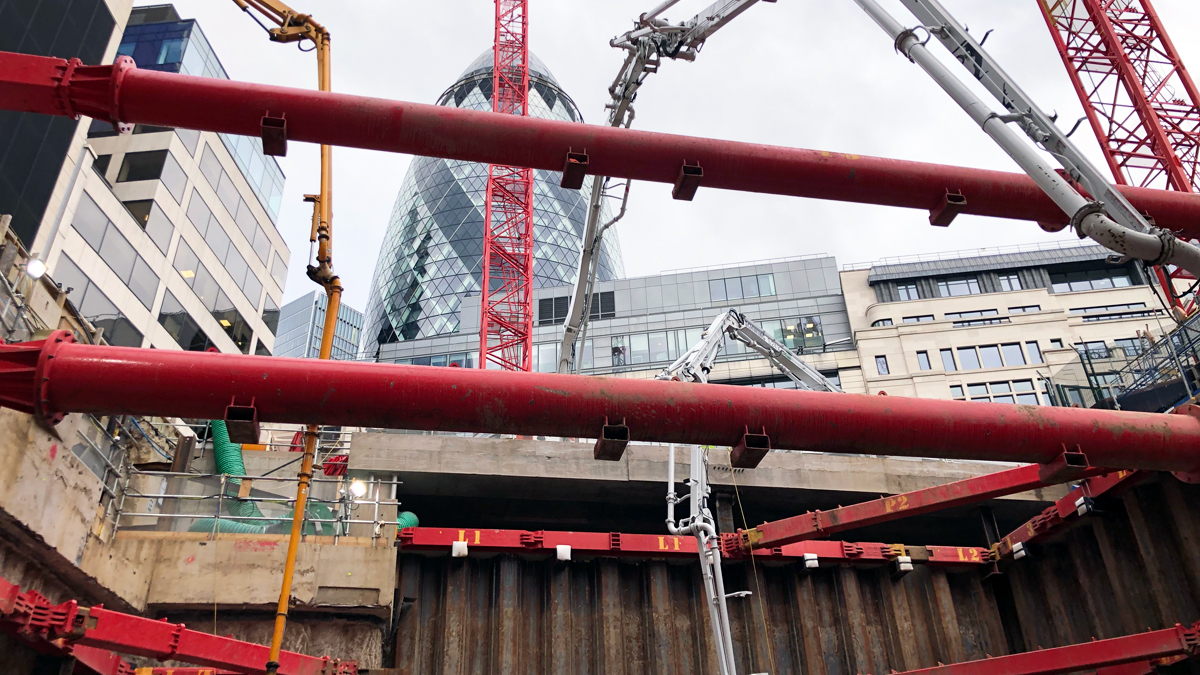
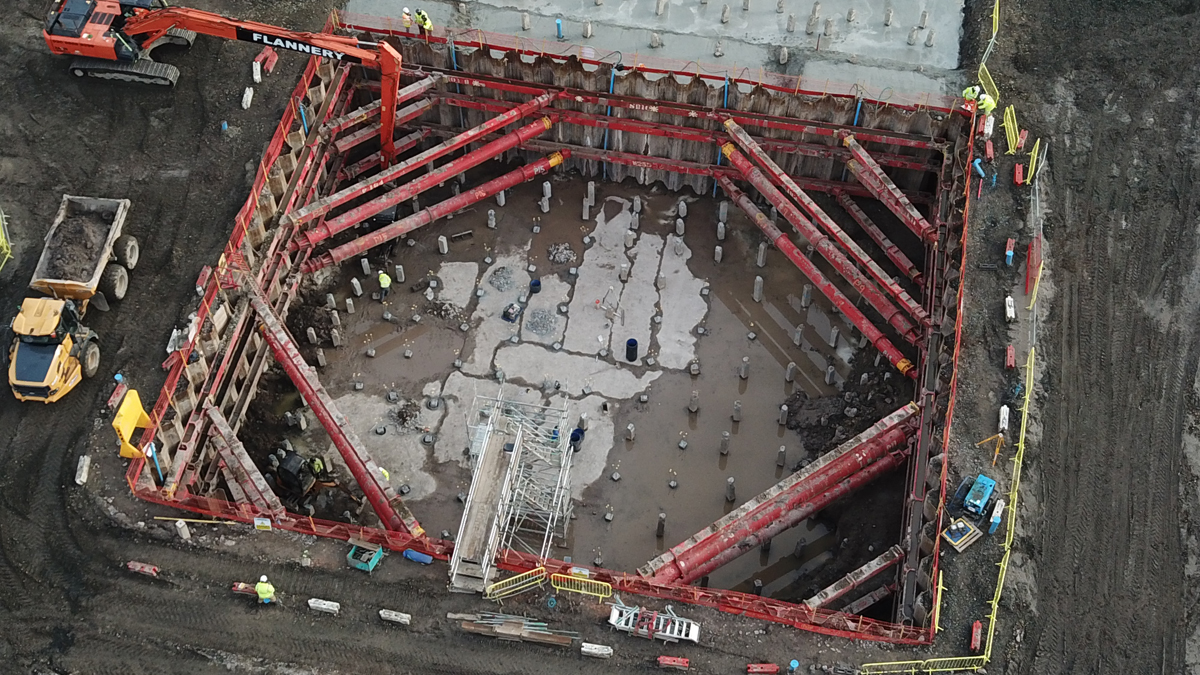
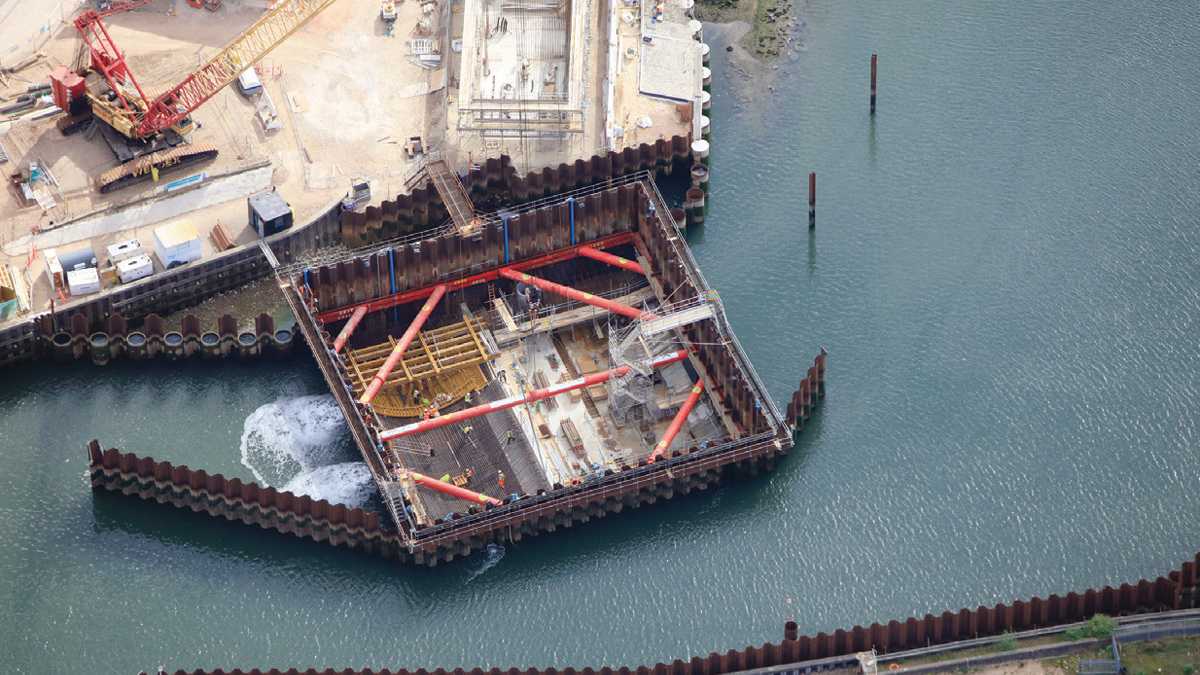
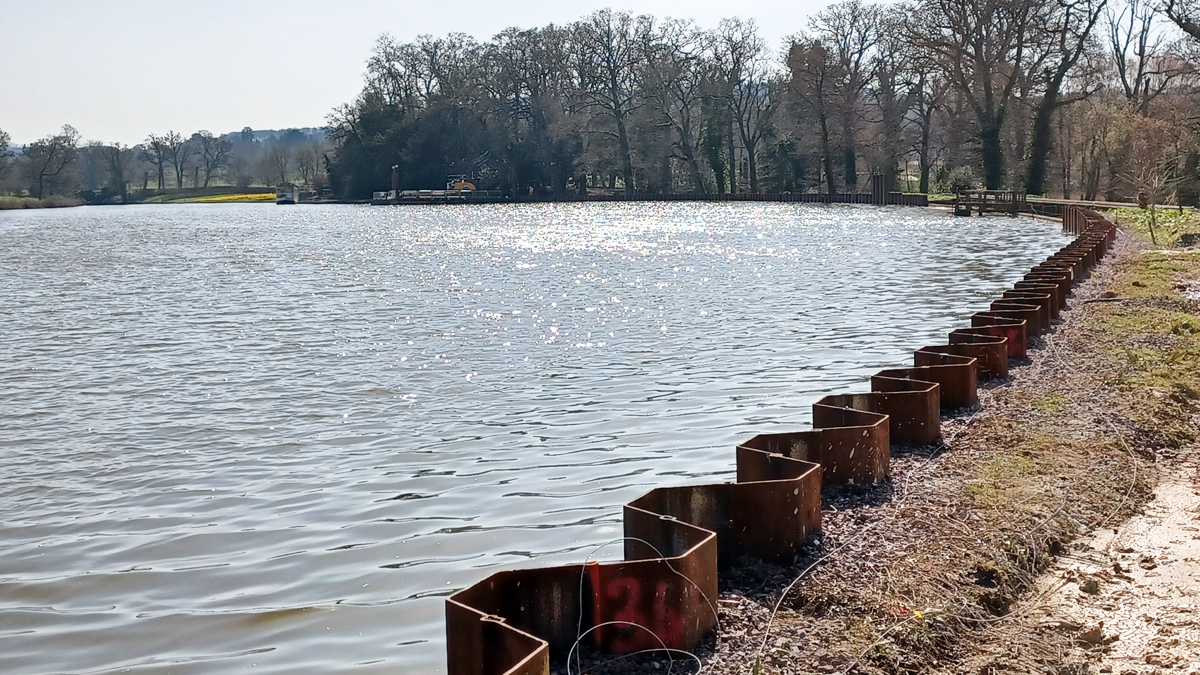
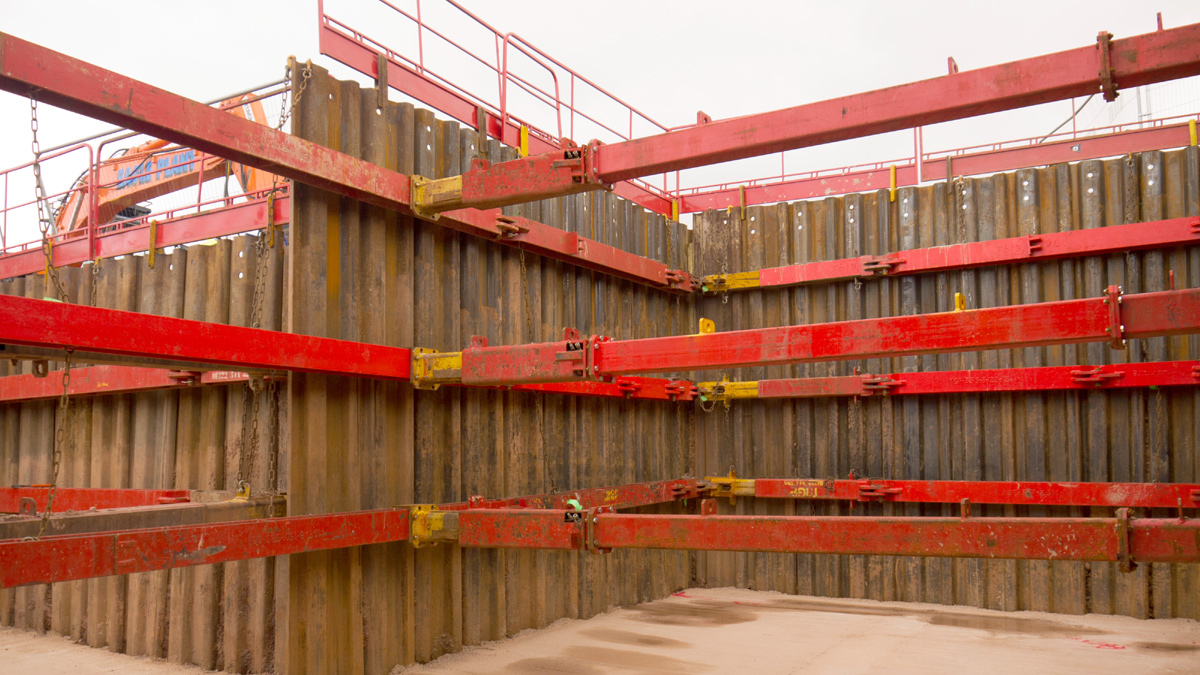
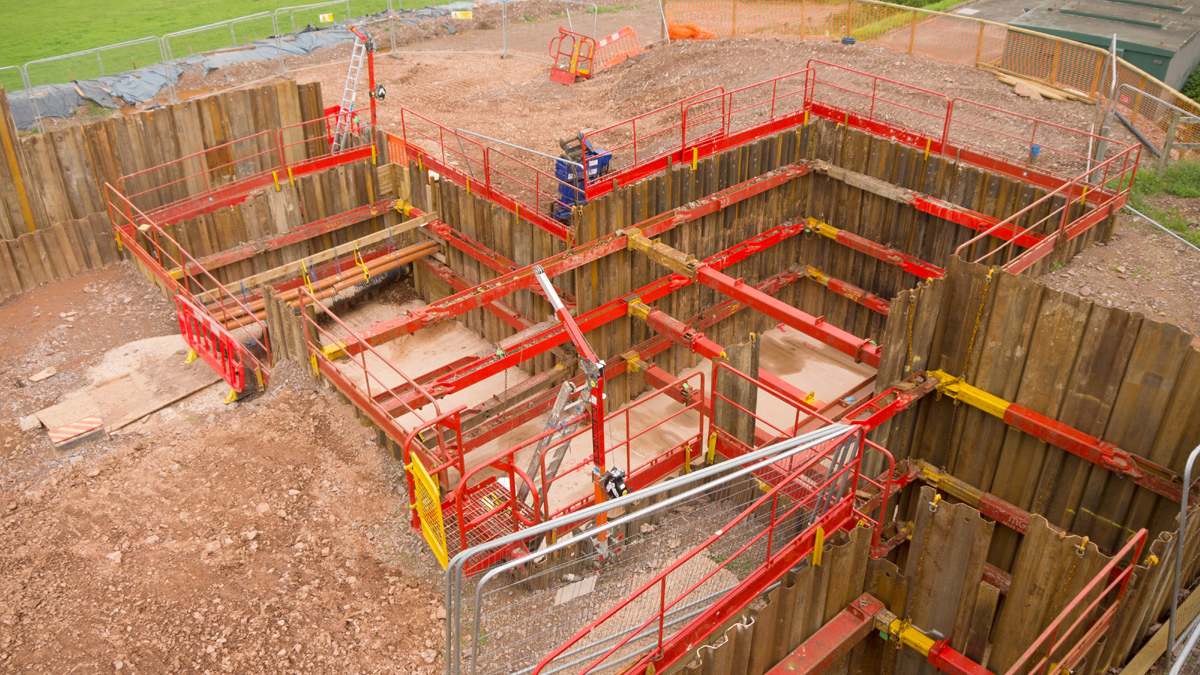
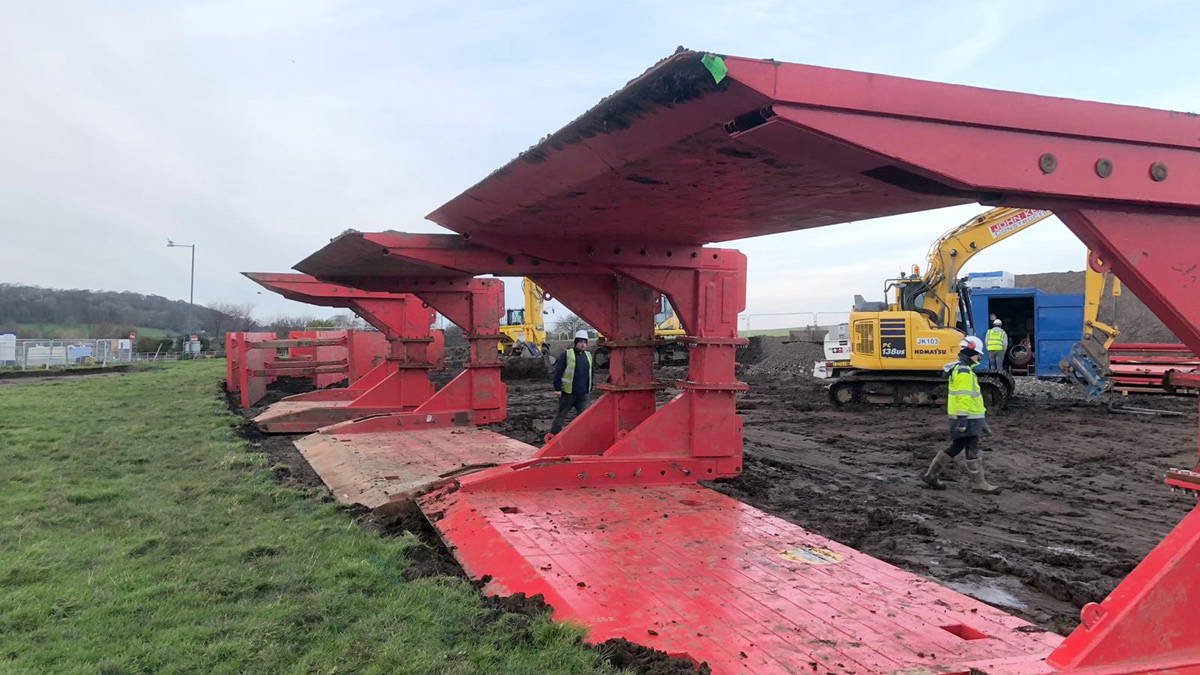
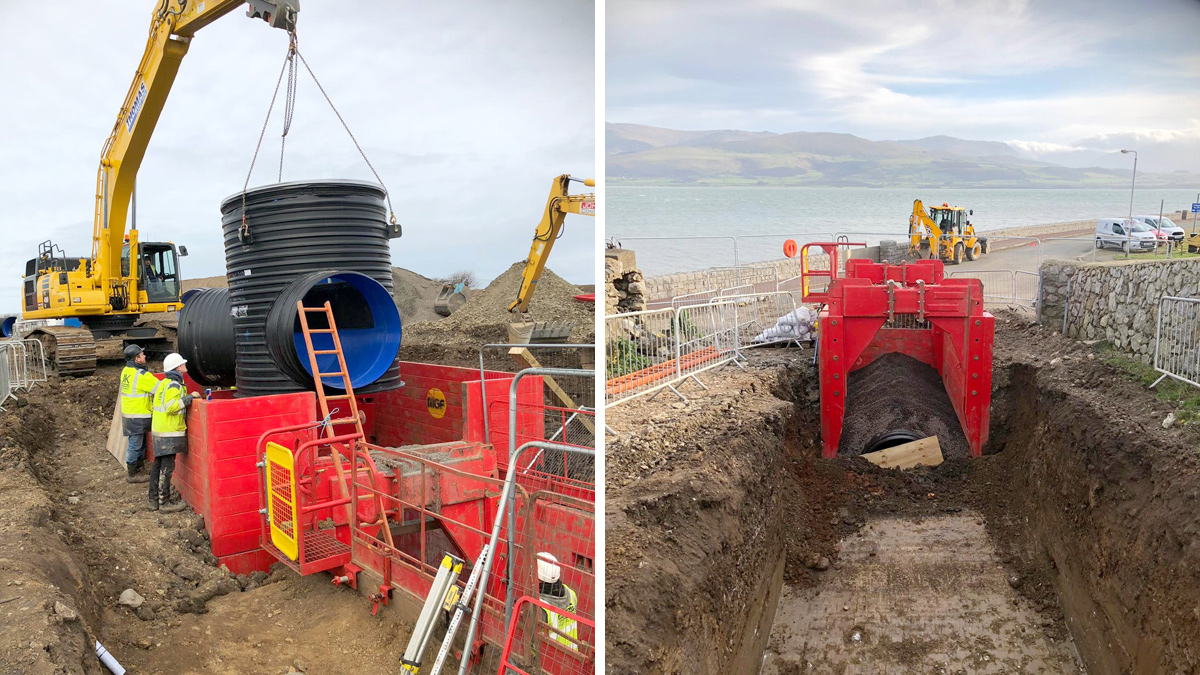
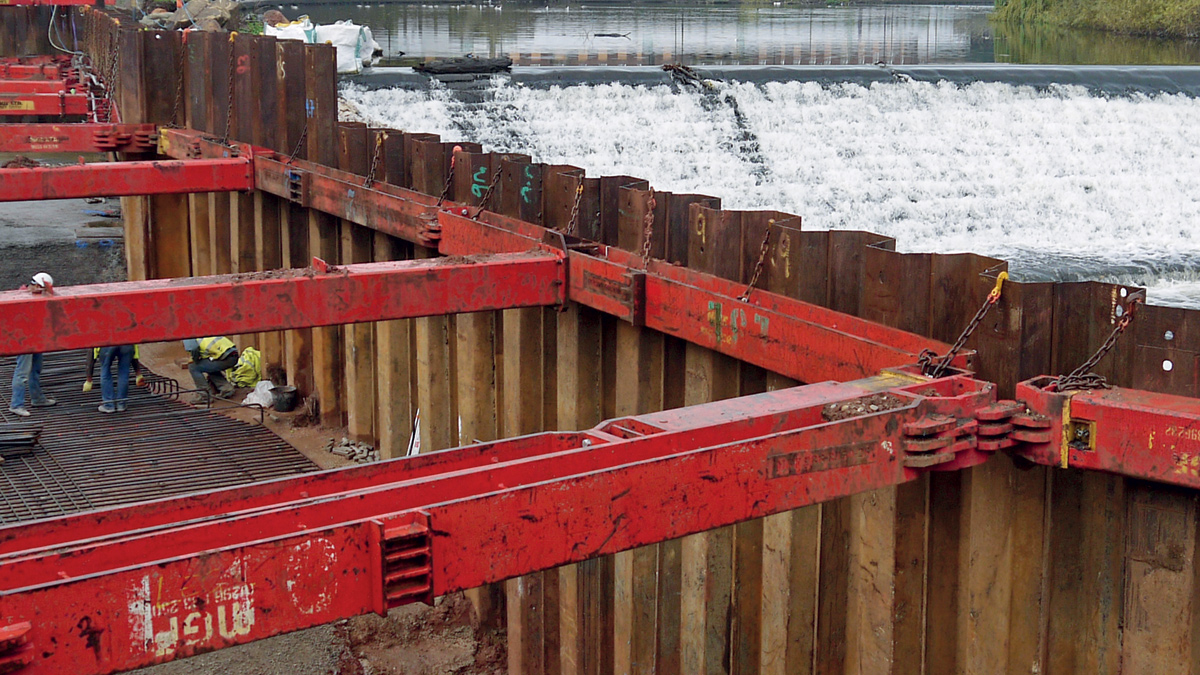
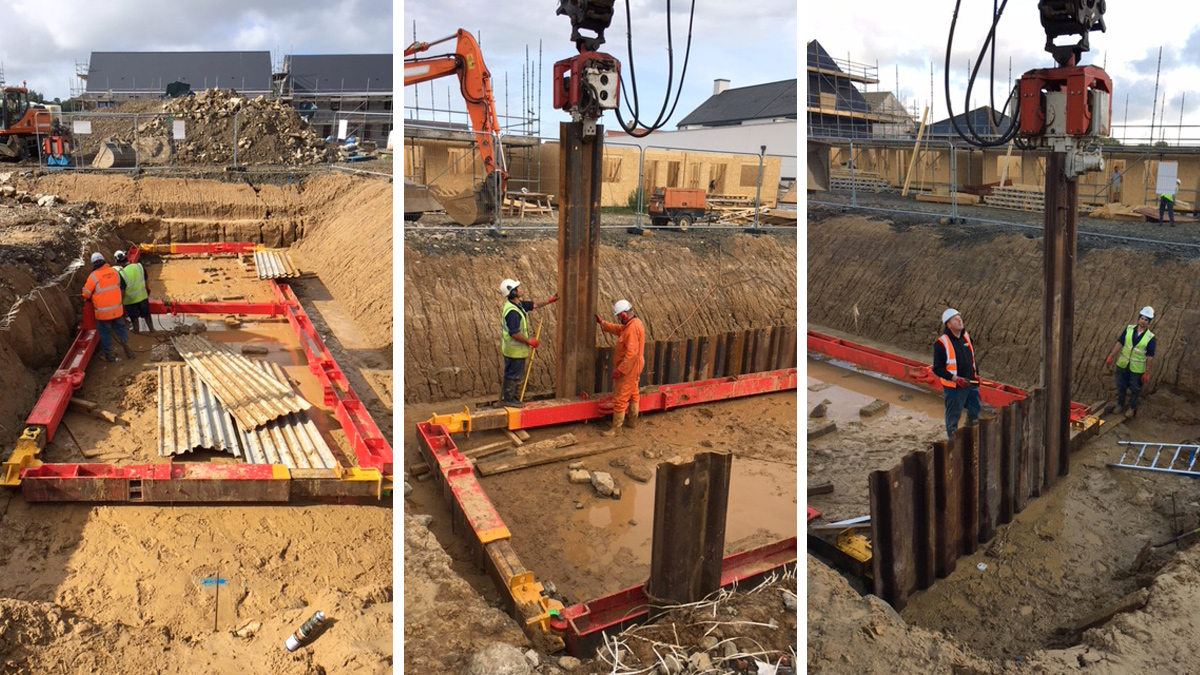
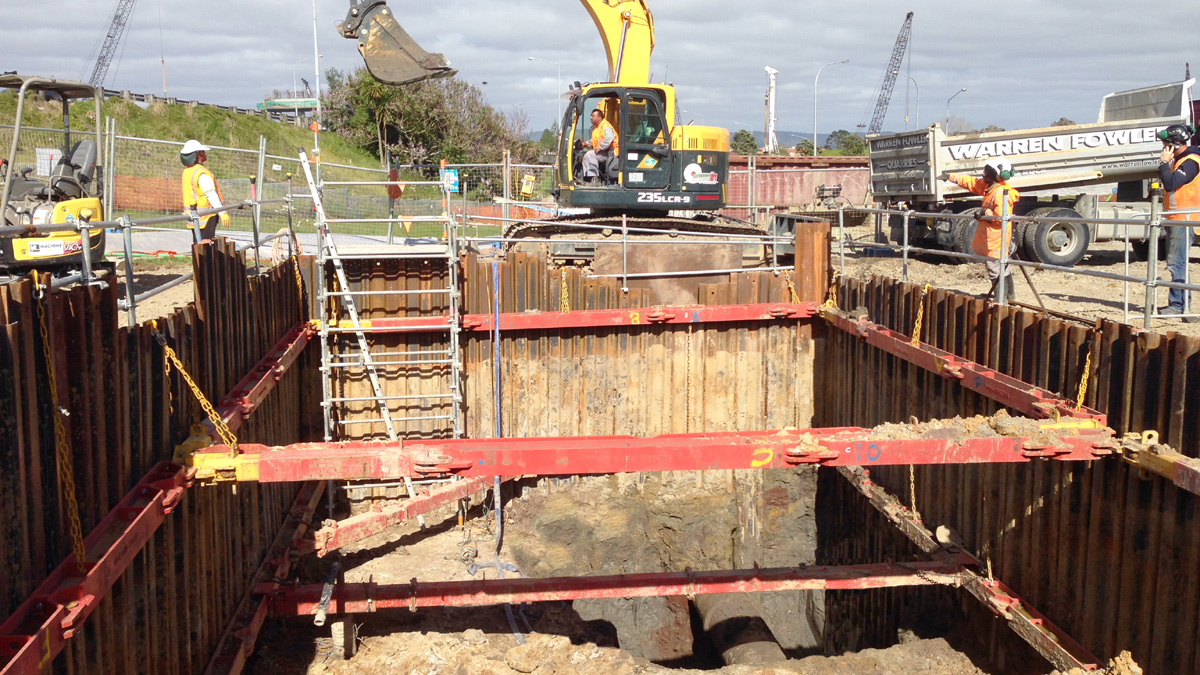
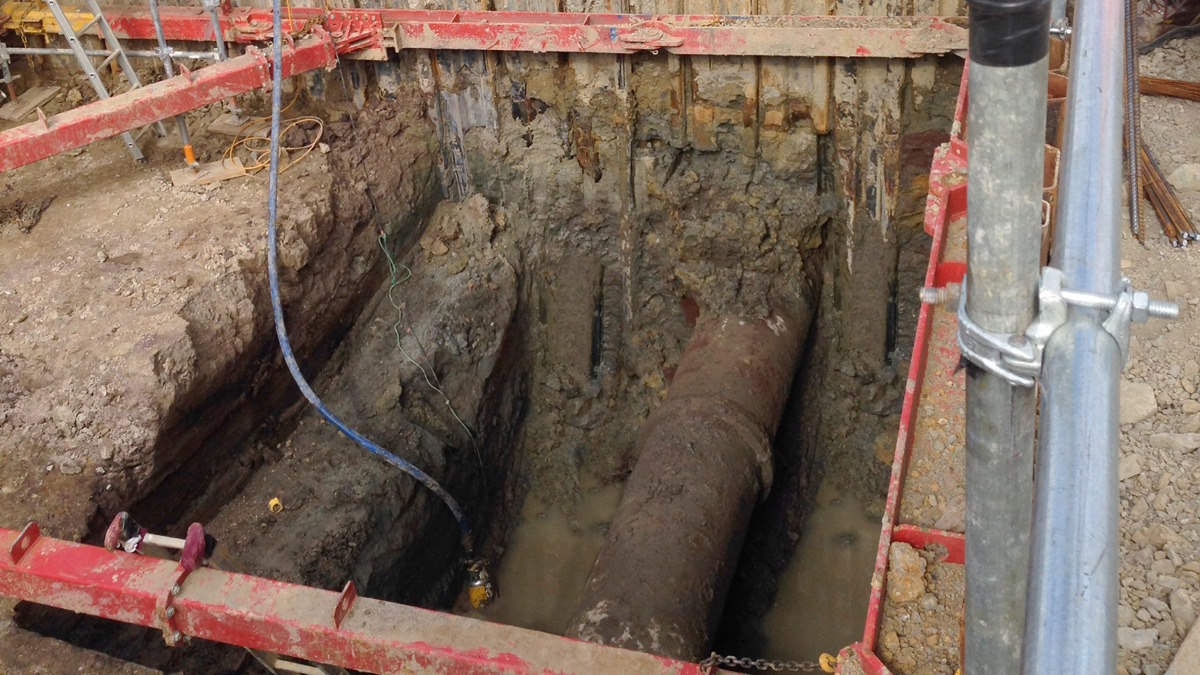
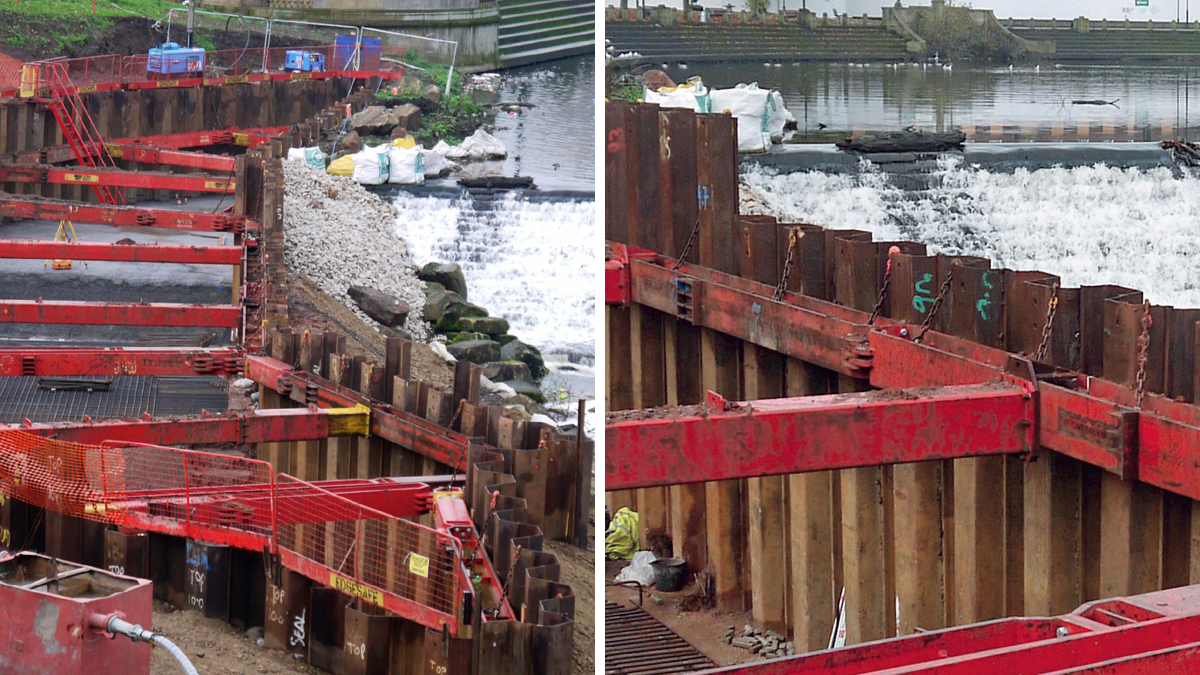
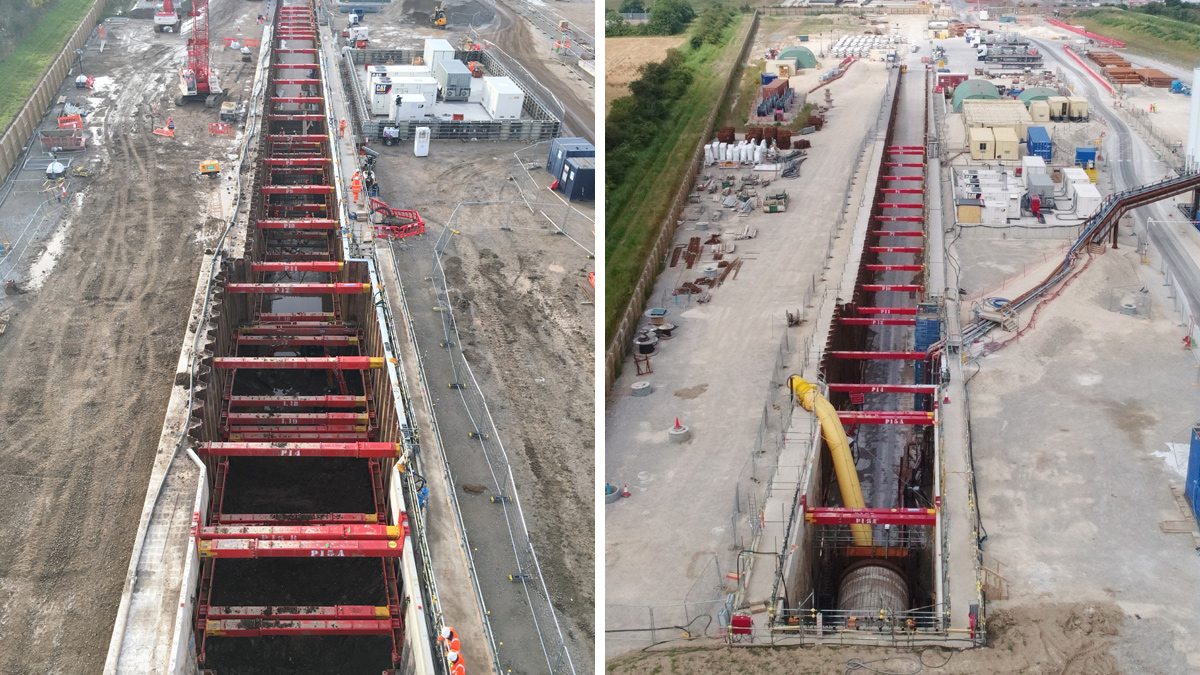
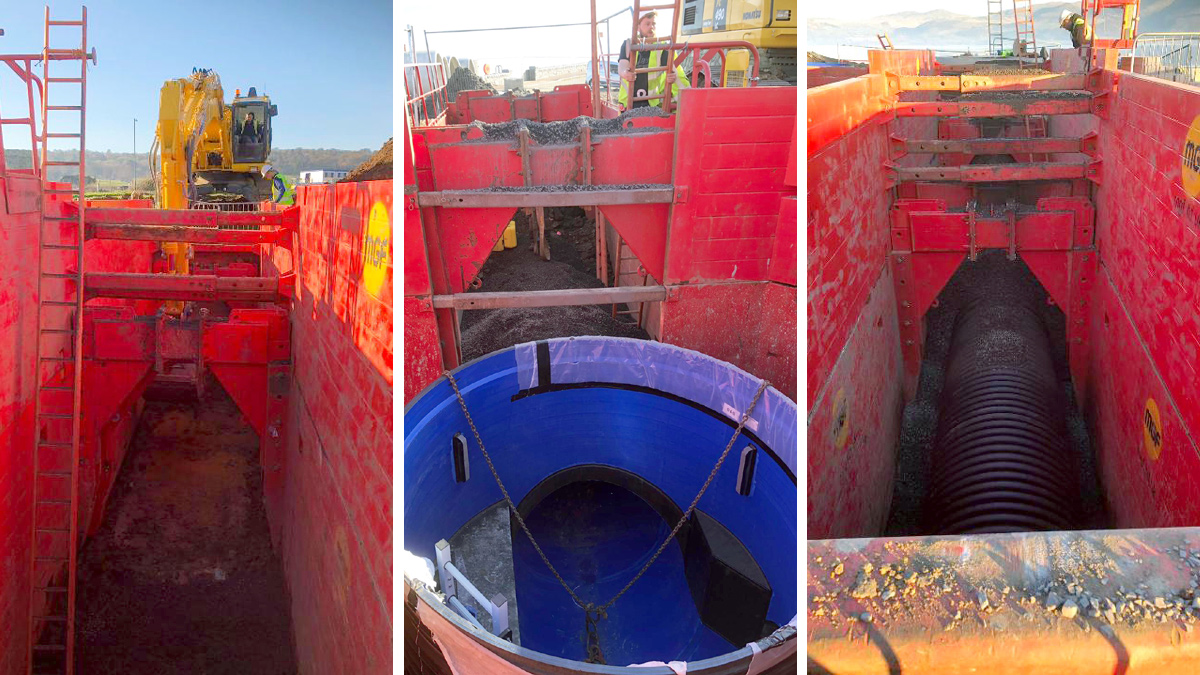
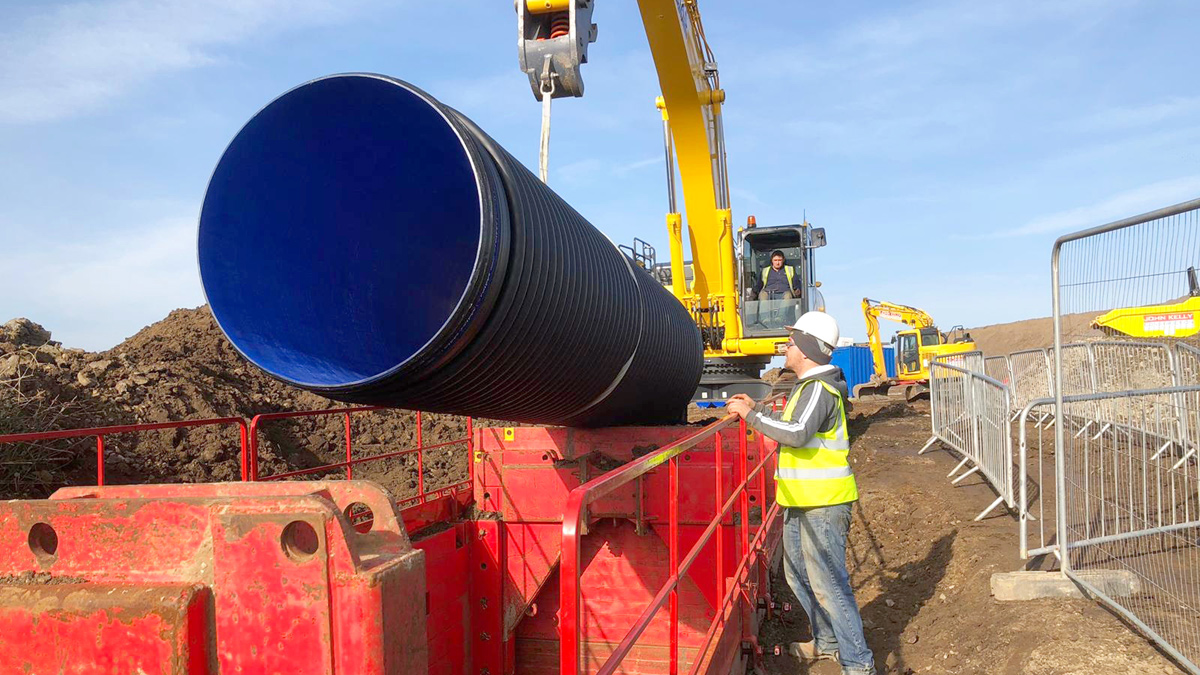
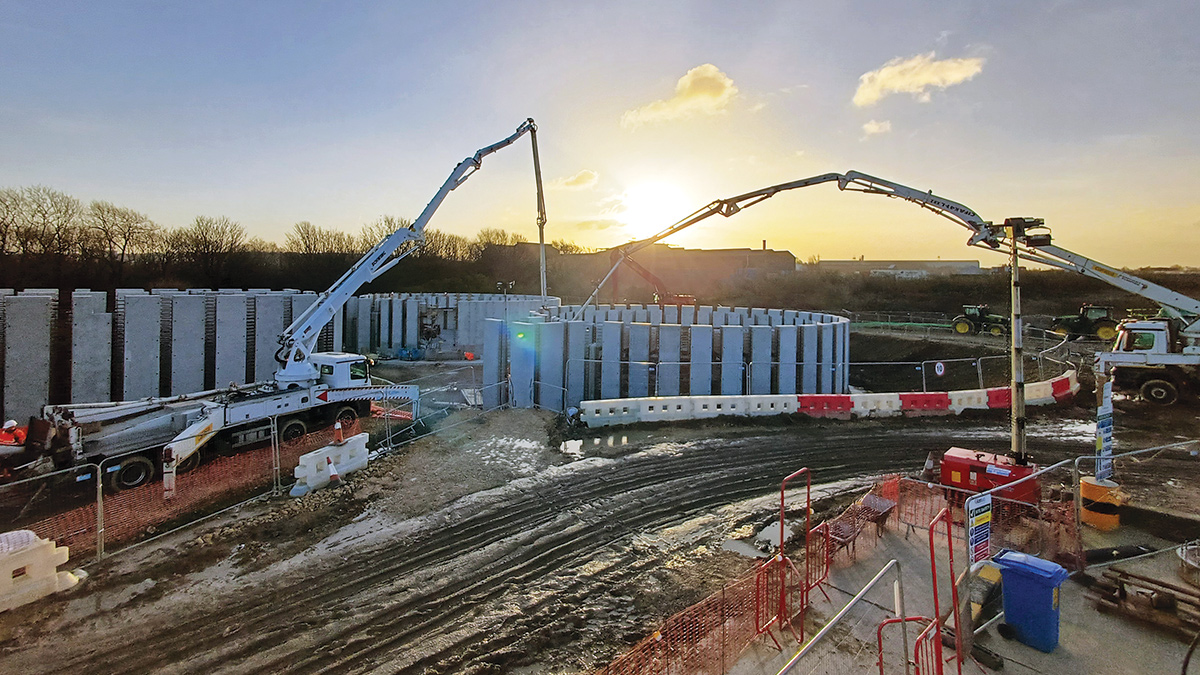
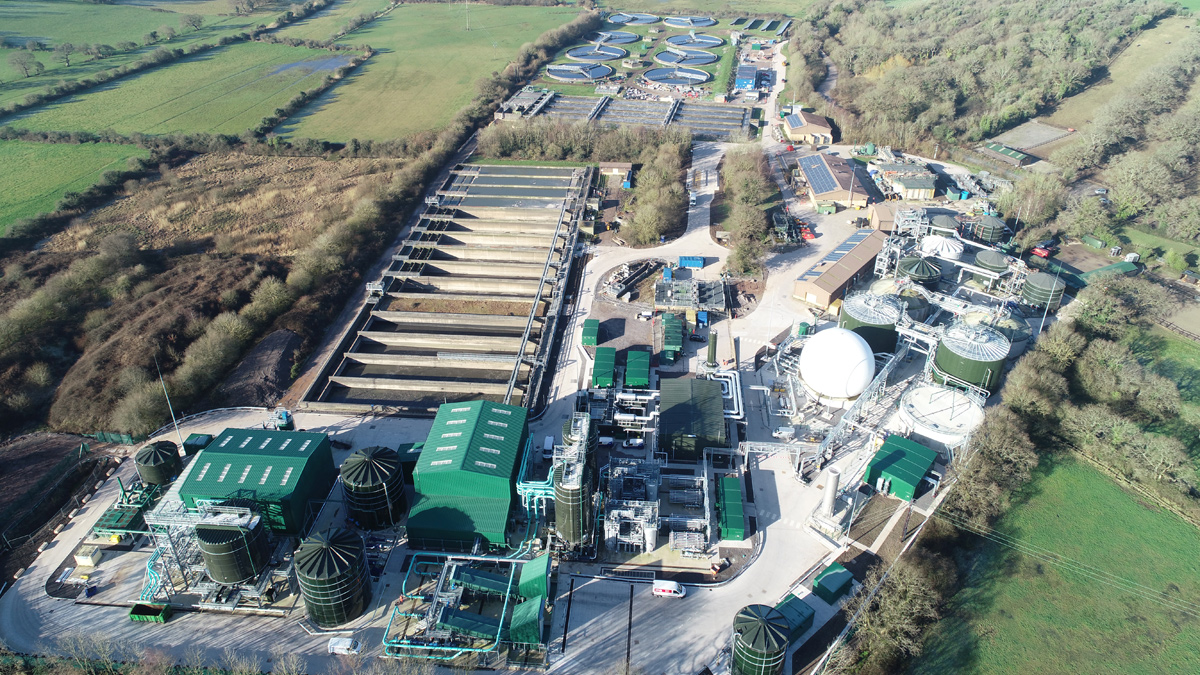
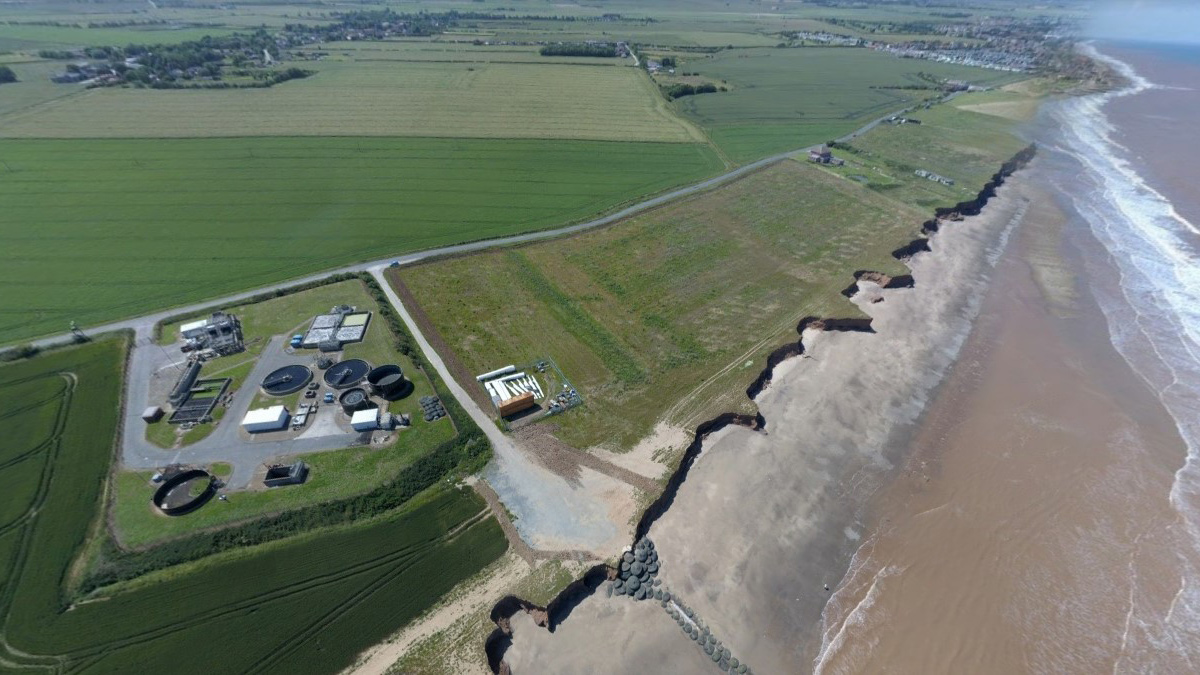
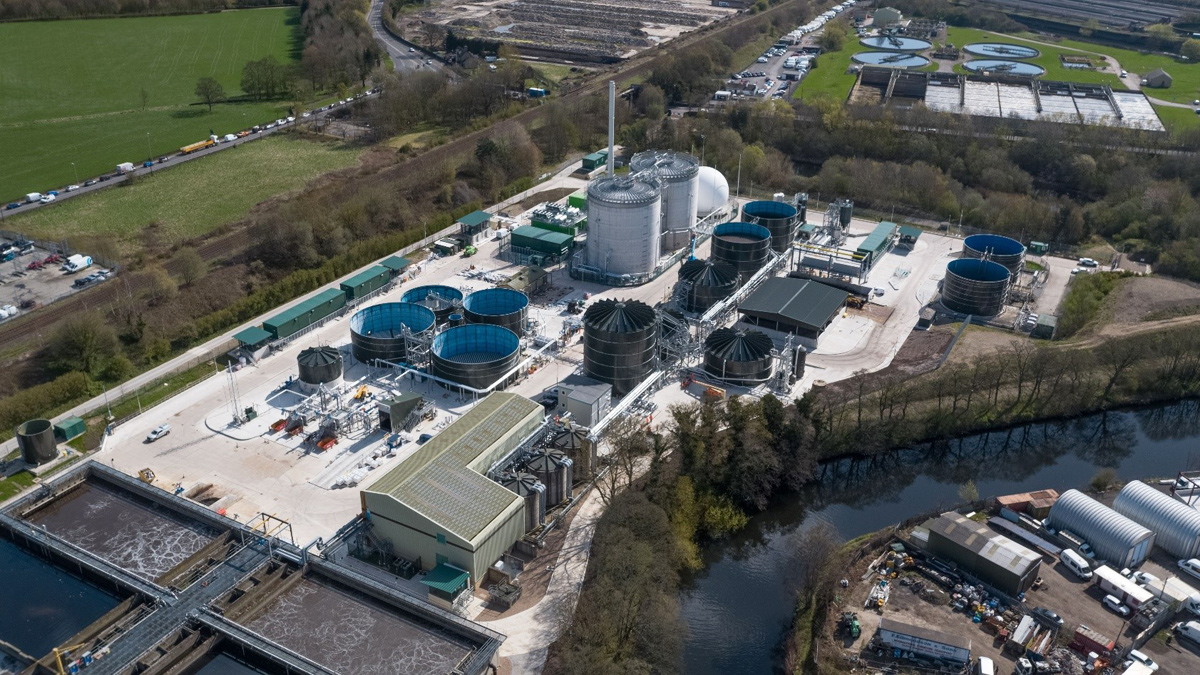
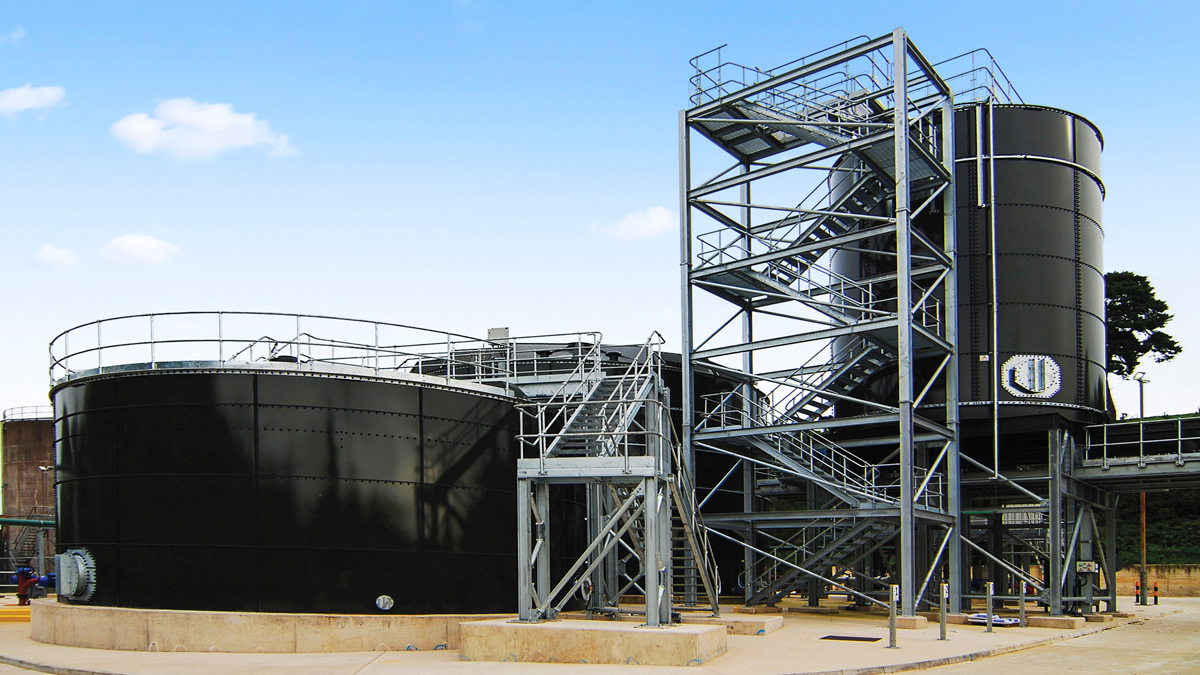
