MGF Ltd
Hyndburn WTW
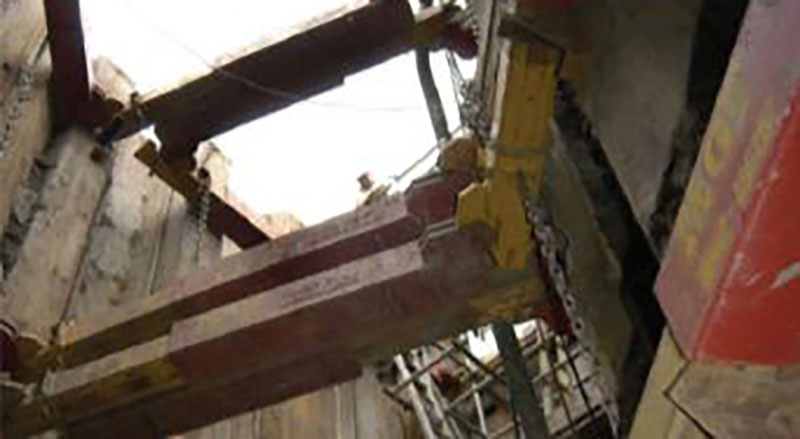
Hyndburn WTW
In 2003 the HMB Alliance were upgrading Hyndburn WTW at Great Harwood, as part of a £10 million water treatment project. This required a 14.0m long, 3.0m wide, 10.0m deep trench to carry large pipe runs from the main settlement tank.
Aside from the high loadings generated by the fairly poor ground conditions (granular fill with a mid-level water table) and the huge depth, the excavation had another problem – it took a turn through 45° at the centre.
The solution
HMB Alliance had come up with a sheet pile design utilising Larssen piles and had intended to design and install bespoke welded steel frames to accommodate the bend in the trench. However, the cost implications and anticipated difficulty of installation of a welded frame – particularly on such a short time scale – urged HMB to seek a better option.
MGF used HMB’s frame loads to design ‘back to back’ bays of hydraulic Heavy Duty Tank Brace. The pinned joints at the corners meant that the usual internal angle of 90° for rectangular frames could be articulated and increased to 112.5° thus accommodating the overall bend of 45°. As the frame loads at lower levels were very high, the lower frames were twinned up, but there was no need for any additional cross strutting and the customer had almost 7.5m of clear working room in the pit.
The sheet piles were pre-driven to full depth by a specialist piling contractor. Excavation commenced to the underside of the top frame, approximately 1.0m below commencing level.
The first ‘back to back’ frames were installed at approximately 0.7m below commencing level. Excavation continued further to the next level, where the middle ‘twin’ frame was installed.
The same sequence was repeated for the bottom ‘twin frame’. Excavation was complete at 10.0m deep and the pipework commenced.
Once all pipework was complete and satisfactory, the excavation was backfilled, gradually removing the frames one at a time, from the bottom upwards.
The verdict
The equipment was easy to install and, due to its available adjustment, it allowed for slight deviations in actual on site dimensions compared with those designed. The solution was much safer and more cost effective than a welded frame option and also greatly reduced the risk and magnitude of any deflections or ground movement. Working space was kept to a maximum, with the only obstructions being the return legs of Heavy Duty Tank Brace cutting across the bend.
For more information: MGF Ltd | +44 (0)1942 402700 | www.mgf.co.uk
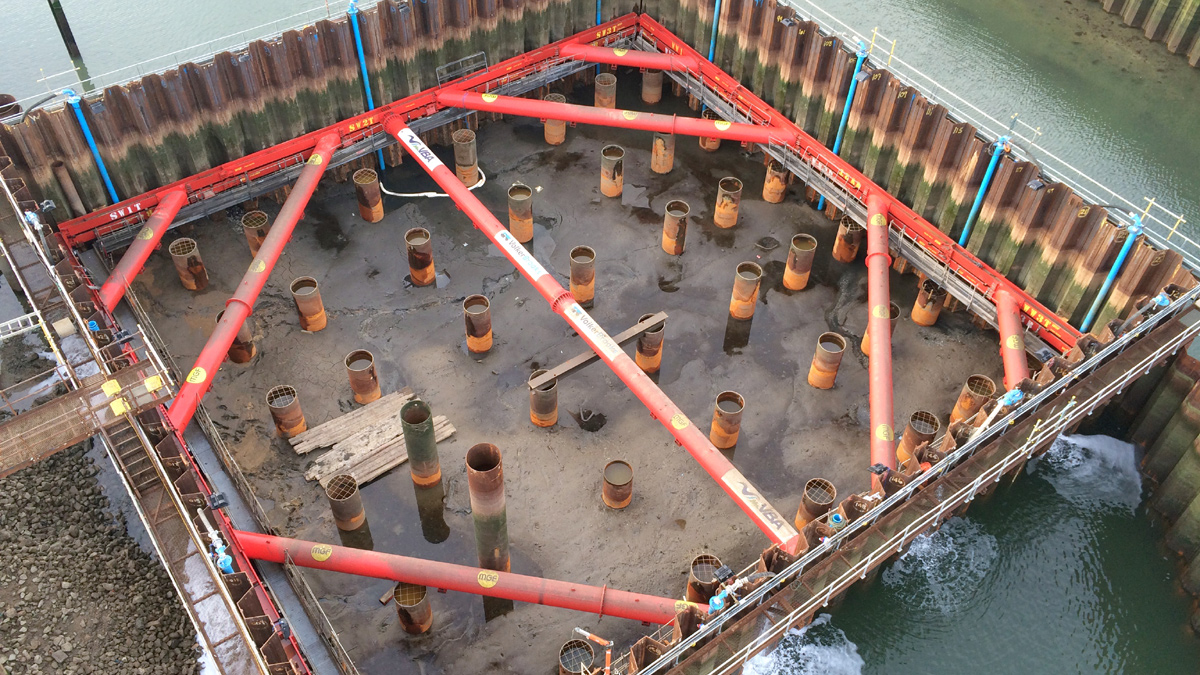
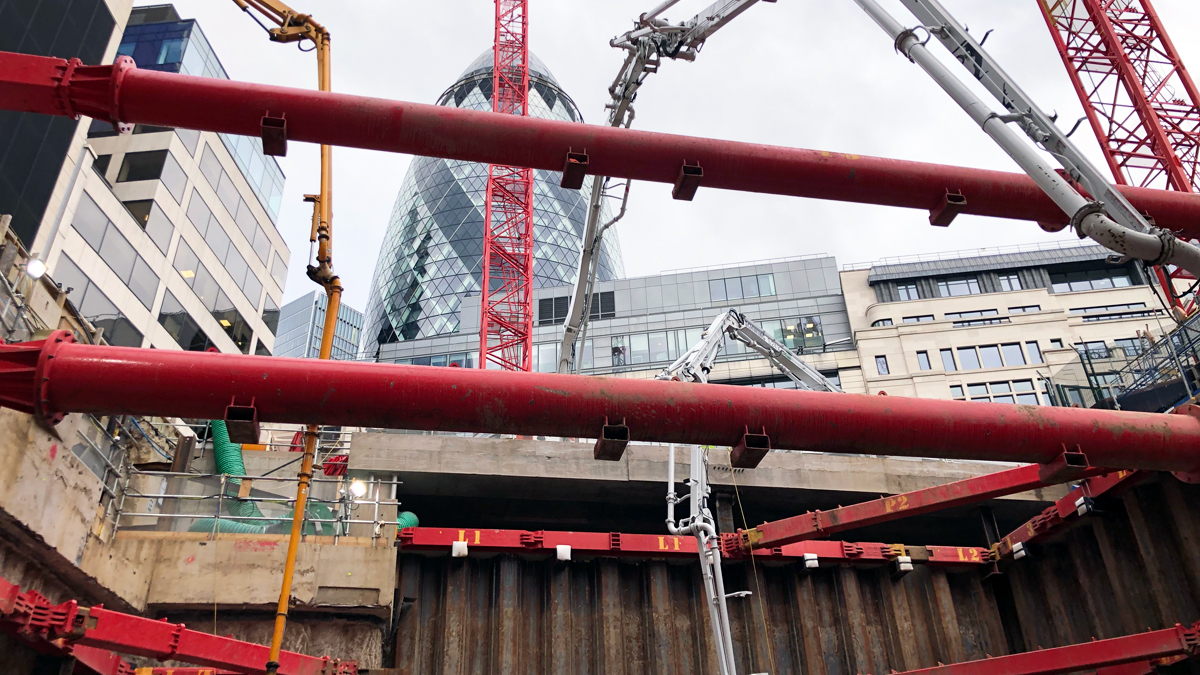
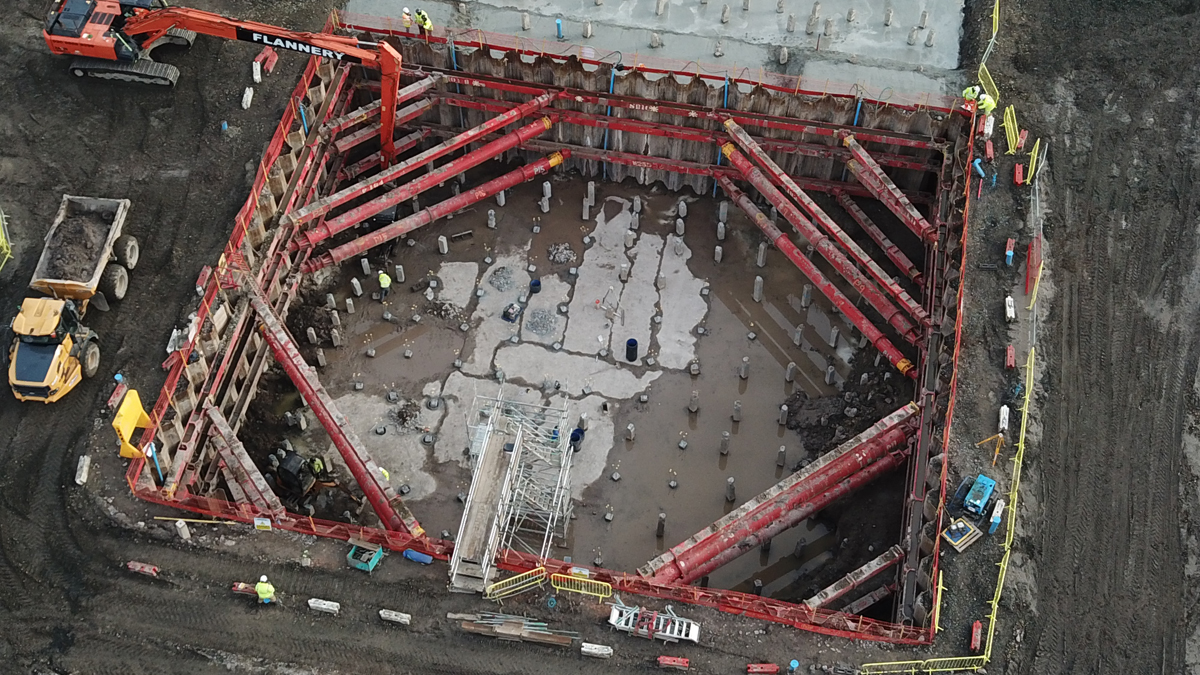
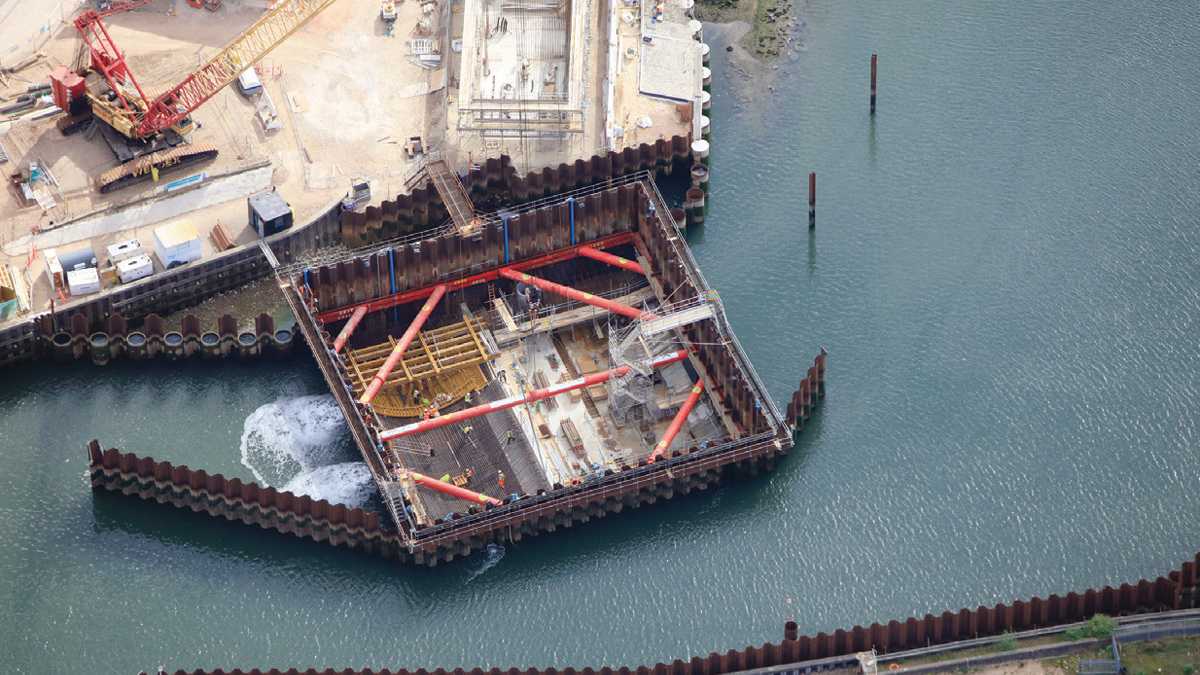
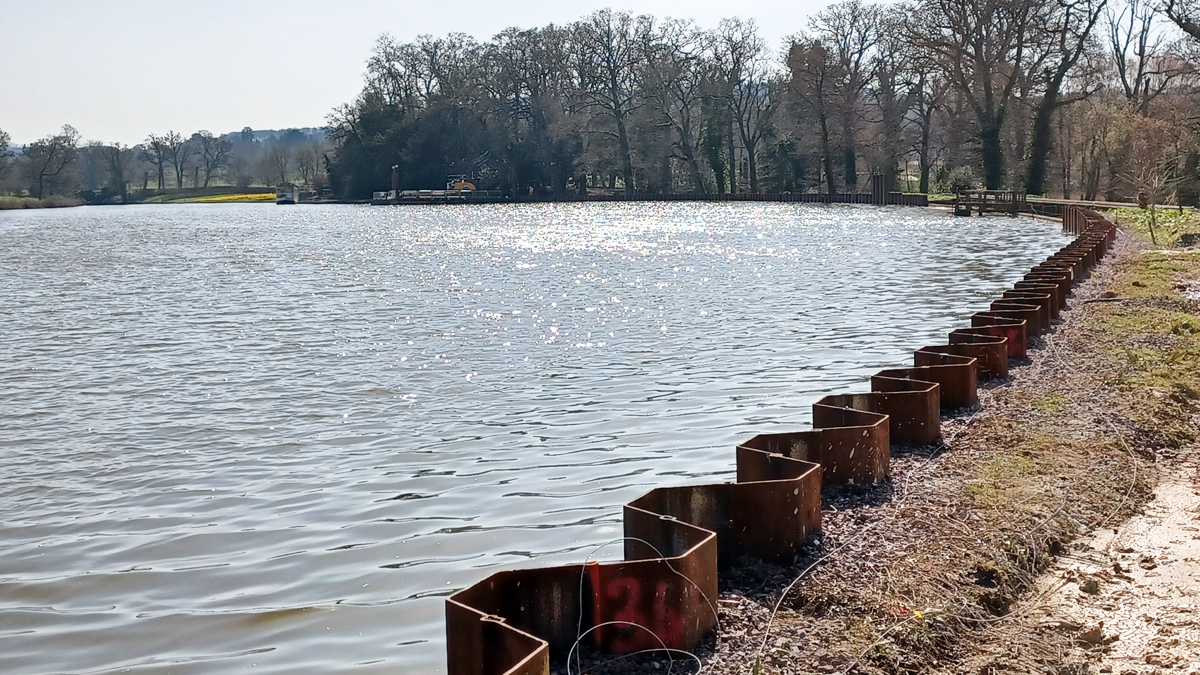
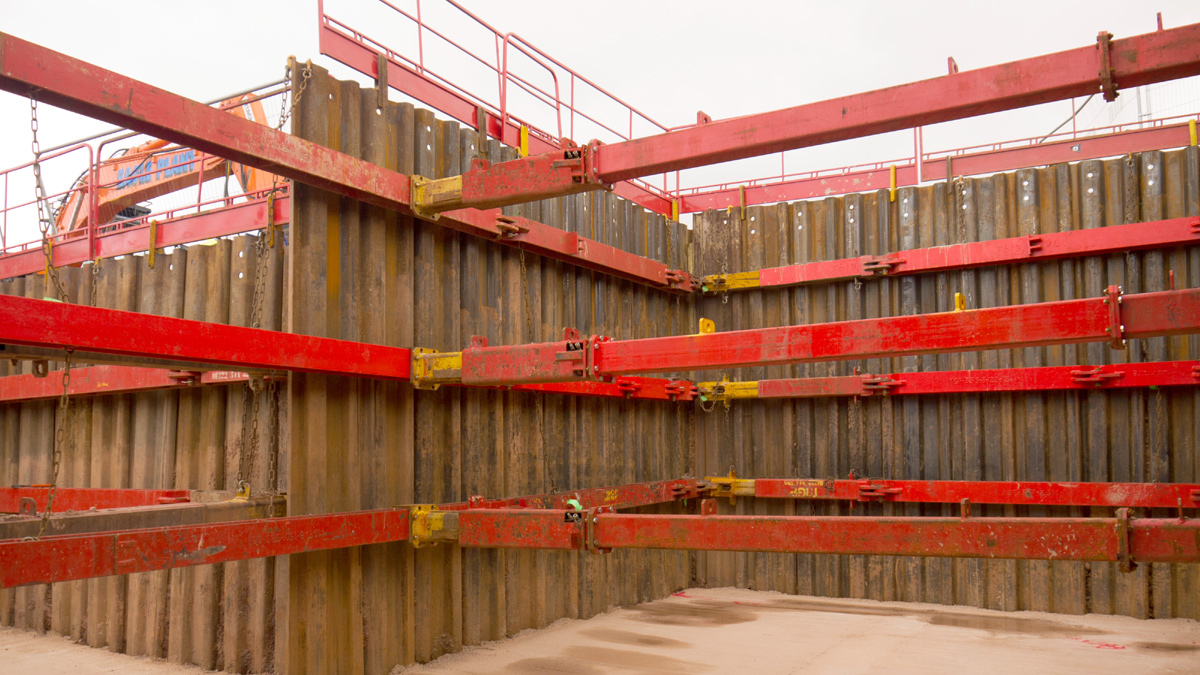
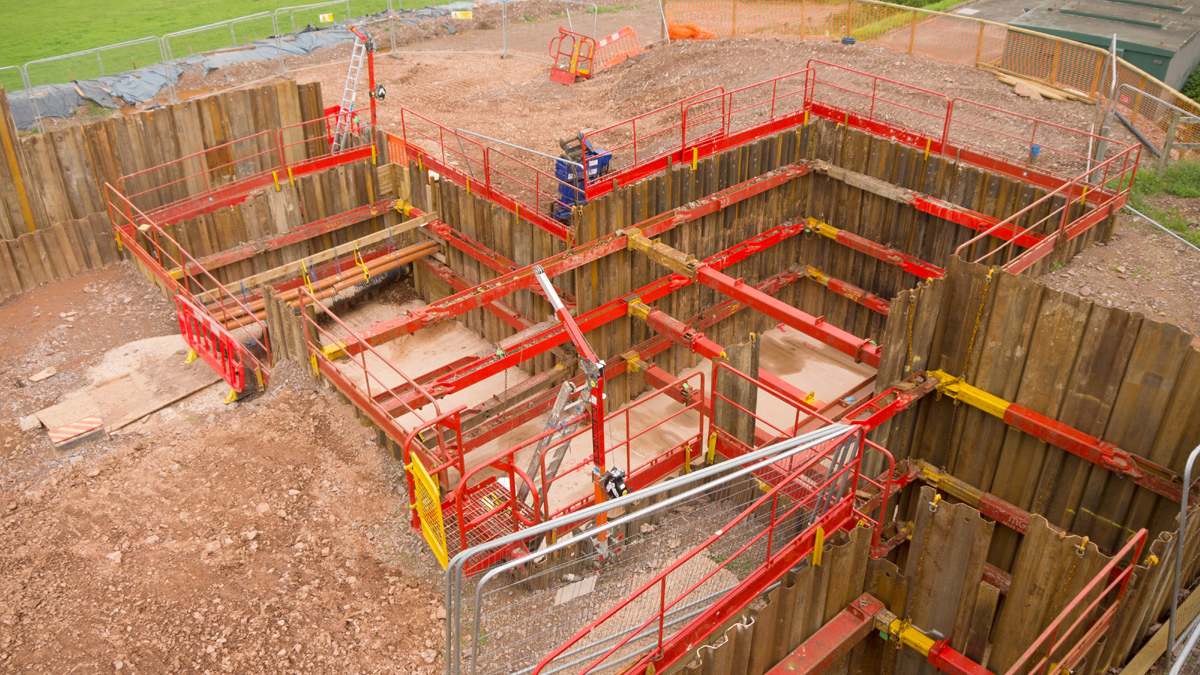
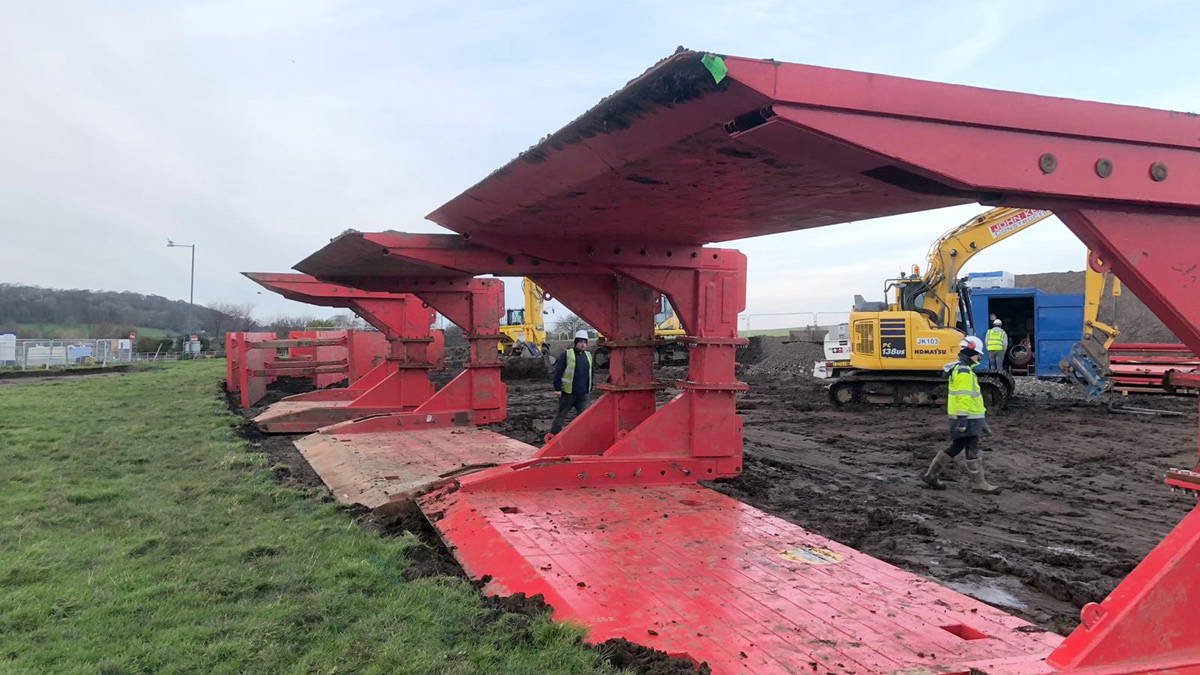
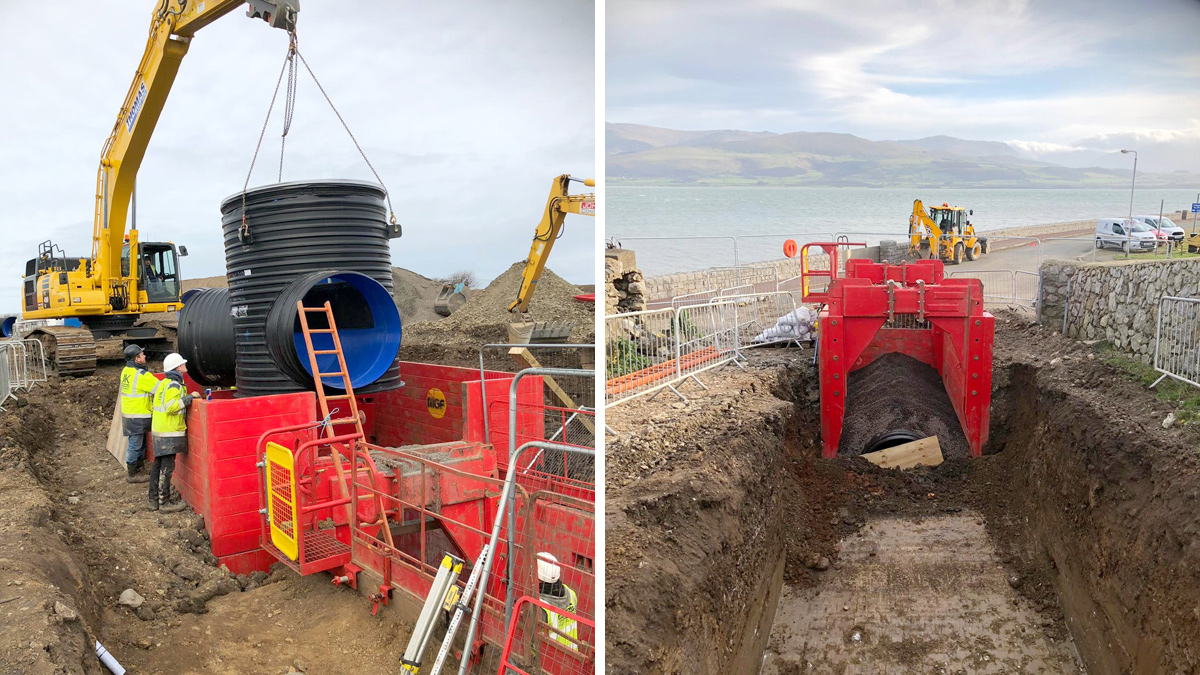
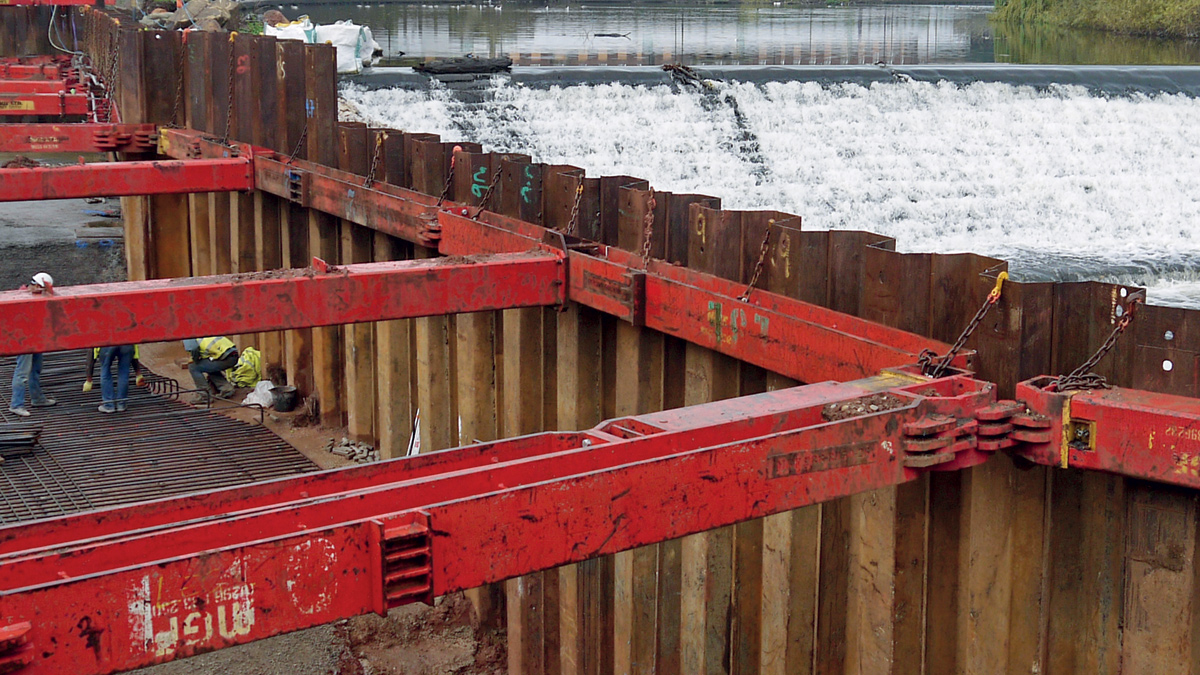
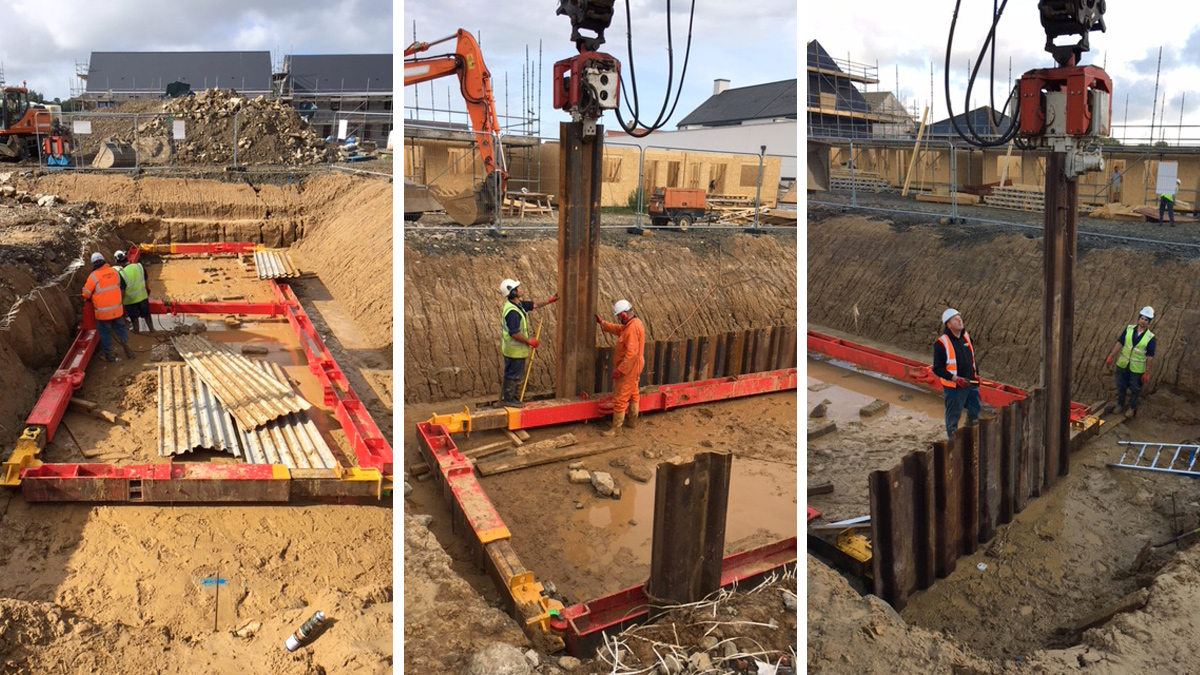
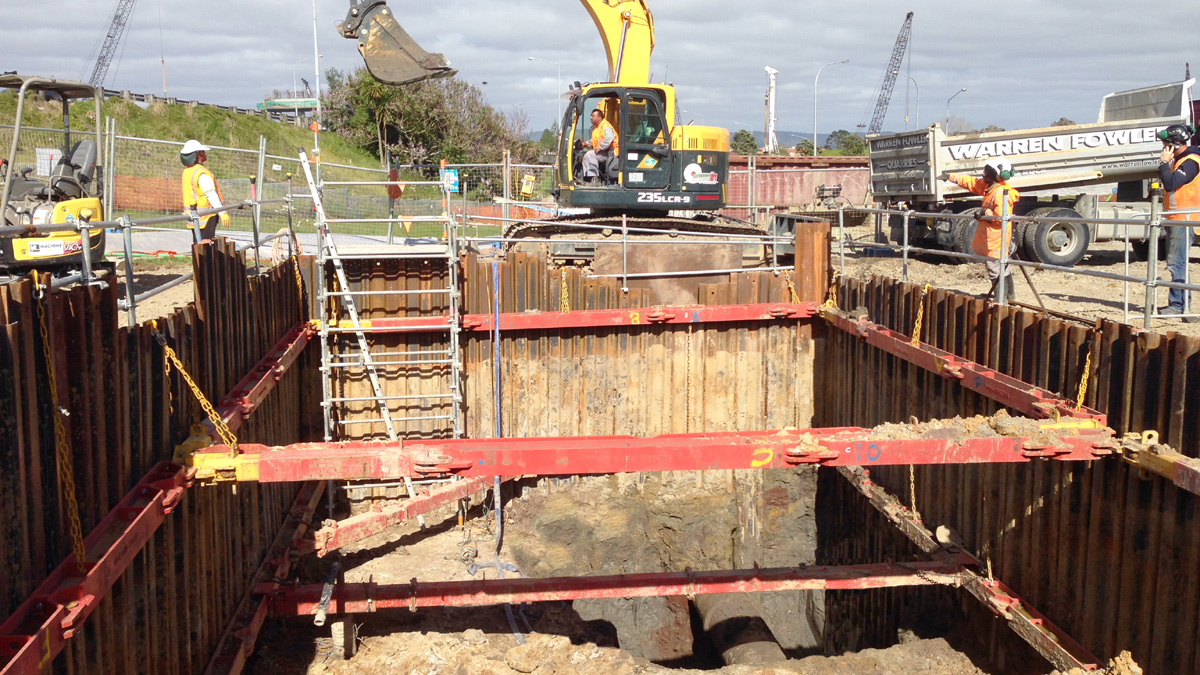
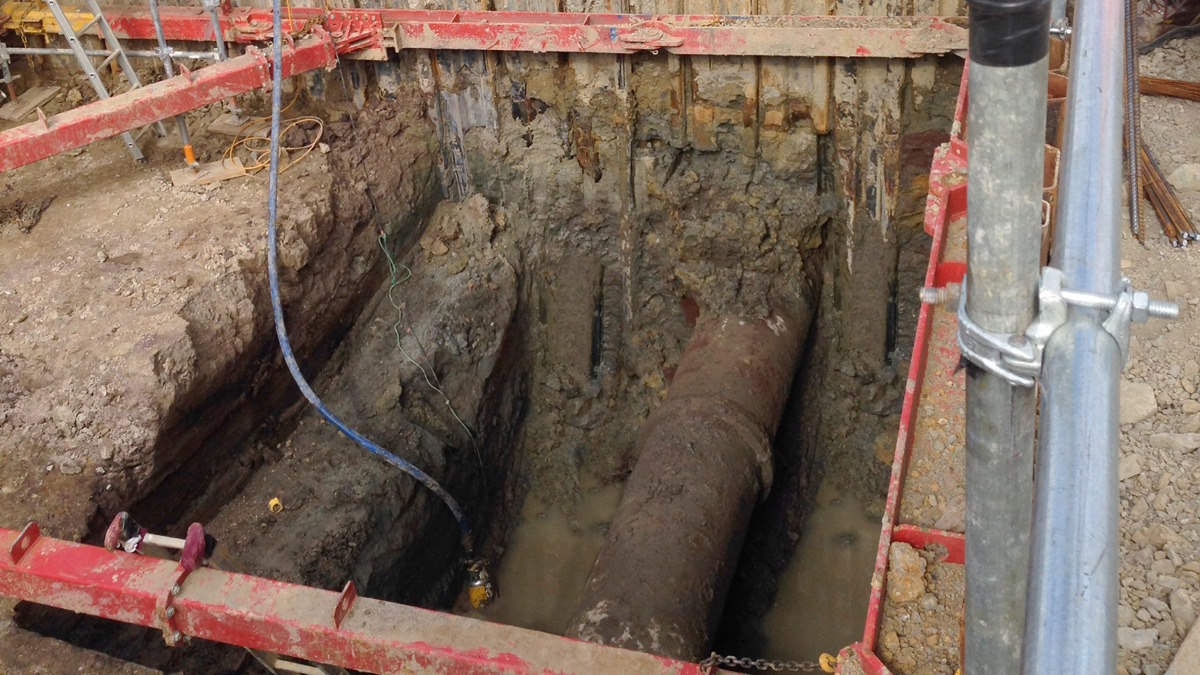
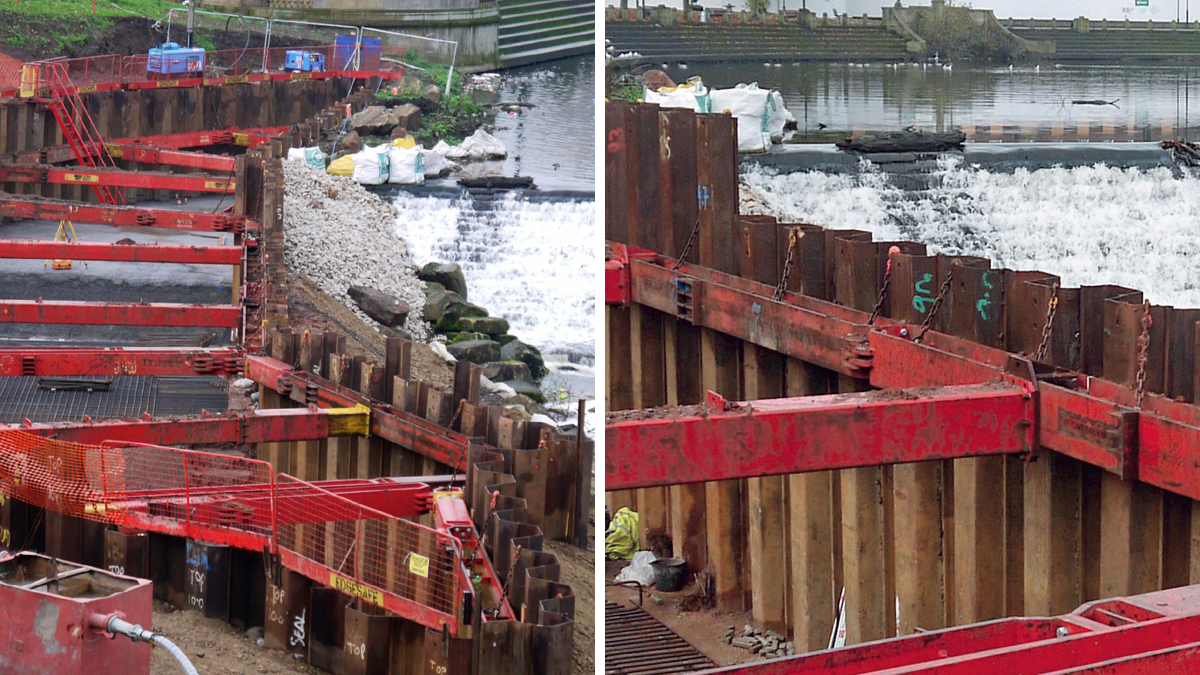
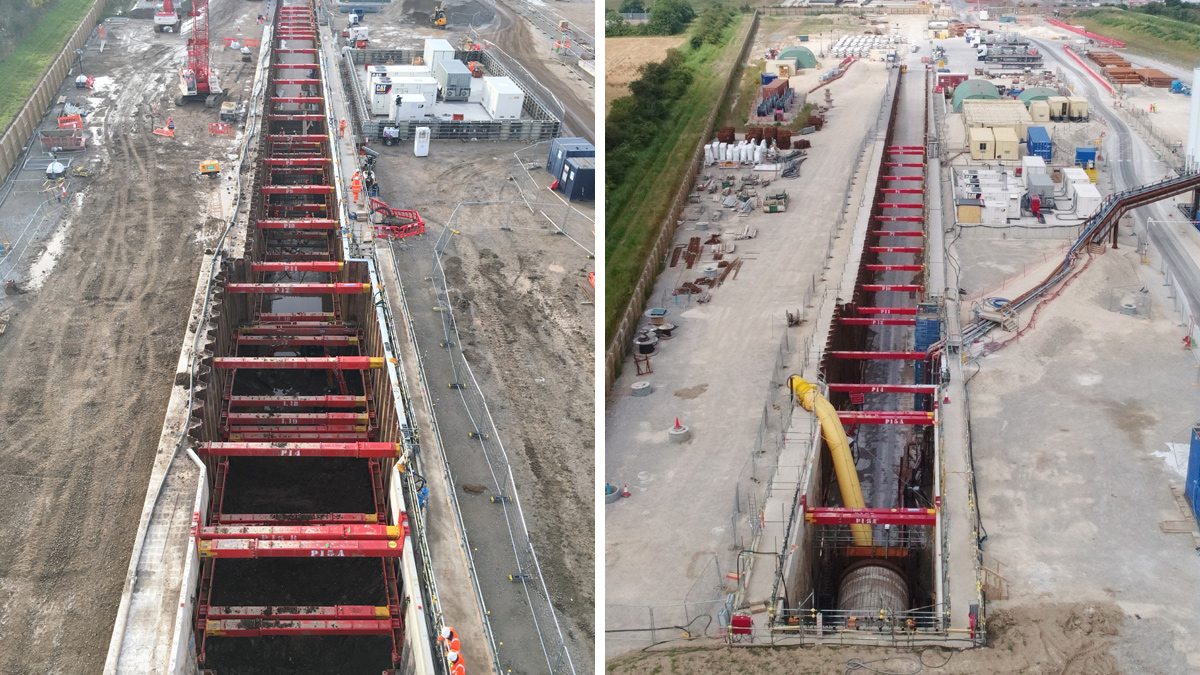
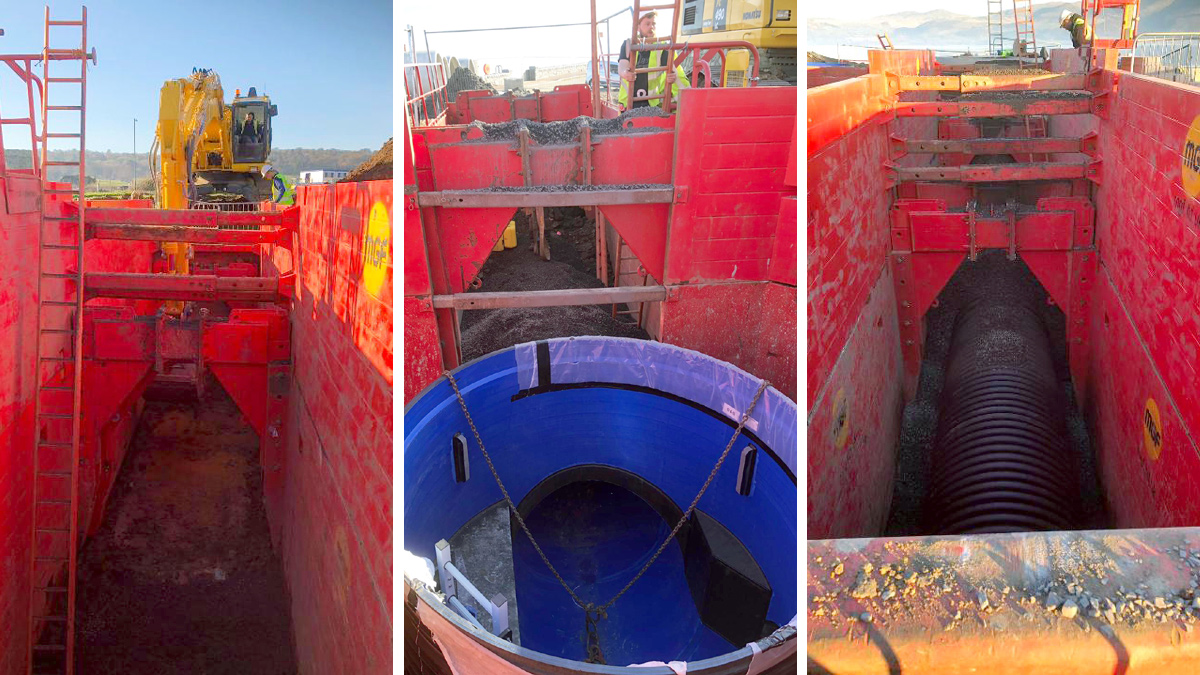
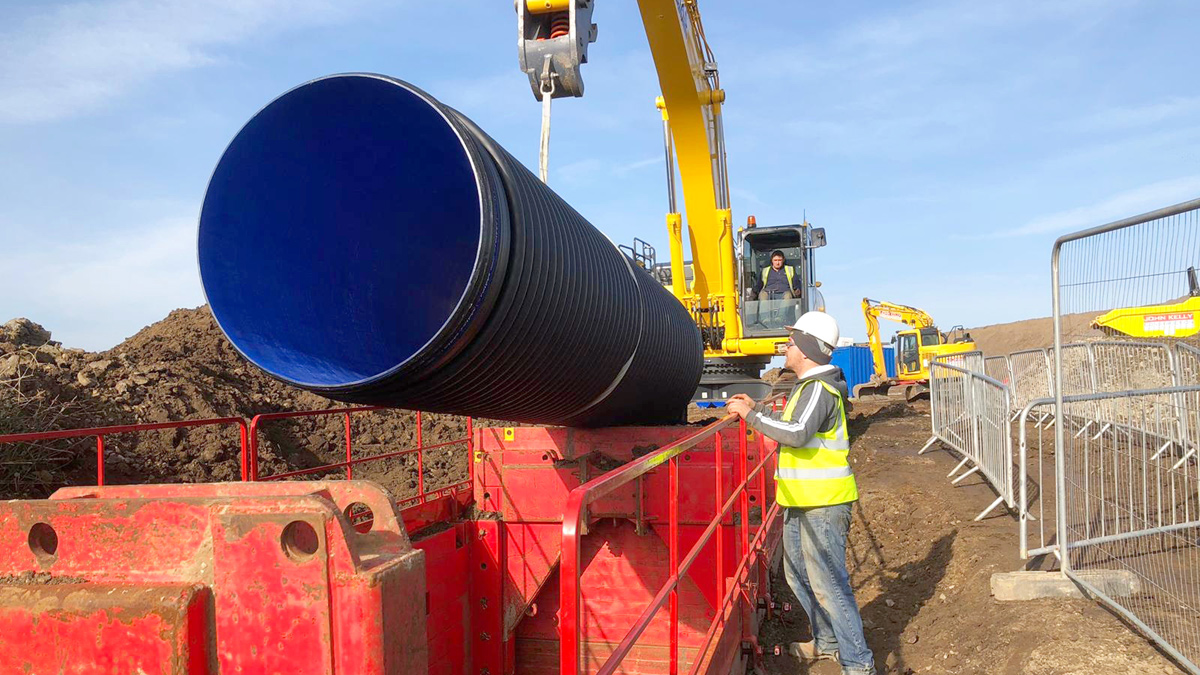